pengenalan
When looking into CNC machining, one of the first questions businesses often ask is, “How much does CNC machining cost per hour?” This question is vital for anyone considering this precise and efficient manufacturing method. Understanding the various factors that influence the cost will help you make informed decisions when planning your project. Whether you’re working on a one-off prototype or a large-scale production run, knowing what contributes to the pricing can save you time, money, and frustration. In this article, we will explore what drives the cost of CNC machining and how you can optimize your project to stay within budget.

Apakah Pemesinan CNC?
CNC machining, or Computer Numerical Control machining, refers to a process where pre-programmed computer software controls the movement of tools and machinery. Unlike traditional manual methods, CNC machining is highly precise and can produce parts with complex geometries. The main types of CNC machining include milling, turning, and grinding, each serving different purposes depending on the specific needs of the project.
Milling involves removing material from a workpiece using rotating cutters, making it ideal for producing flat or curved surfaces. Turning, on the other hand, is used to shape materials into cylindrical forms, while grinding involves finishing processes for smoother surfaces. CNC machines are crucial in industries ranging from aerospace and automotive to medical devices and electronics, providing high-quality and consistent parts with minimal human intervention.
The key advantage of CNC machining lies in its precision and ability to repeat tasks consistently. However, you might be wondering how all of these factors impact the price per hour of using CNC machines. The costs associated with CNC machining depend on several factors, such as machine complexity, material choice, and job size. By understanding these variables, you can get a clearer picture of what to expect in terms of pricing.
What Affects CNC Machining Costs?
Several factors contribute to the overall cost of CNC machining. The complexity of the project, the type of machine used, and the materials involved can all play a significant role in determining the hourly rate. Here’s a deeper look at each of these factors:
Machine Type and Complexity
The type of CNC machine you use plays a significant role in determining machining costs. For example, a 5-axis CNC machine, which can work on multiple sides of a part simultaneously, is more expensive to operate than a simple 3-axis machine. This is because more advanced machines require greater precision, specialized tooling, and a higher level of operator skill.
Material Costs
Materials are a major factor in CNC machining costs. While materials like aluminum and plastic are relatively affordable, others, such as titanium or specialty alloys, can be more expensive. Choosing the right material can significantly impact the overall cost of your machining project. Not only does the material affect the raw material price, but it also influences the tool wear and machine time.
Part Size and Complexity
Larger parts or those with intricate designs may take longer to machine, leading to higher costs. Parts that require additional operations, such as drilling or threading, also increase the cost since the machine will be running for a longer period and may require special tooling.
Tolerances and Finishing
The tighter the tolerances needed for your project, the more precise and time-consuming the machining process will be. High-tolerance parts often require additional setup time and specialized tools, which increase costs. Furthermore, post-processing services like polishing or coating may add extra expenses.
Hourly Rates for CNC Machining: What’s the Average?
CNC machining hourly rates can vary greatly depending on the machine type, material, and complexity of the job. On average, the cost can range from $40 to $150 per hour, but you might be wondering why this wide range exists.
The type of machine significantly affects the rate. A standard CNC mill may cost around $50 per hour, while more advanced machines, like 5-axis mills, can run as high as $150 per hour due to the additional capabilities and skilled labor required. It’s important to keep in mind that your project’s needs will directly impact the machine selection and, therefore, the cost.
Additionally, location plays a role in determining CNC machining costs. Manufacturing in developed countries like the U.S. or Germany tends to be more expensive than in countries like China, where labor and overhead costs are lower.
How to Calculate CNC Machining Costs Per Hour
Understanding how to calculate CNC machining costs is essential for businesses working on custom projects. It’s not just about the hourly rate – several components go into the overall pricing.
Breakdown of Hourly Rates
Typically, the hourly rate for CNC machining is a sum of labor costs, machine usage, material costs, and overhead. Labor costs include the salary of the operator and any additional technical support needed during the process.
Cost Per Minute Calculations
If you’re looking at smaller jobs, it may be helpful to break down the hourly rate into minute-based calculations. For example, a $100 per hour rate equates to about $1.67 per minute of machine time. This allows for a more granular understanding of how costs accumulate during the machining process.
Cost Estimators and Online Tools
Several cost estimators and online tools can help you calculate your CNC machining costs more accurately. These tools take into account factors like the machine type, material, and complexity of the design to give you a more precise quote.
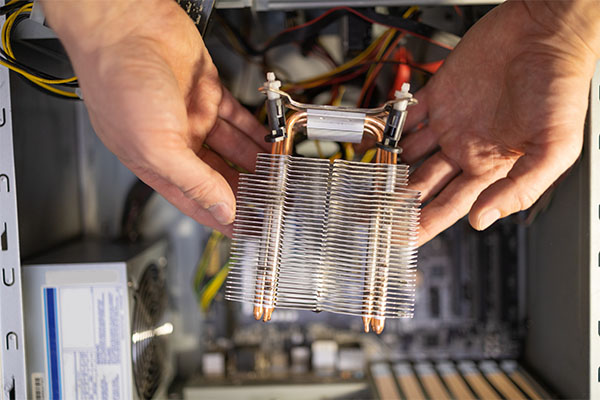
CNC Machining Cost Factors: Labor vs. Machine Time
Both labor and machine time contribute significantly to CNC machining costs. Understanding the relationship between these two can help you determine the true cost of a project.
Labor Cost Impact
Labor costs can vary based on the complexity of the task and the skill of the operator. Highly skilled operators may command higher wages, especially for projects that require intricate machining. However, more experienced operators can also complete tasks more quickly, which may help to reduce overall costs in the long run.
Machine Time Breakdown
Machine time is typically the largest portion of the CNC machining cost. This includes both the setup time and the actual running time of the machine. You can reduce machine time by optimizing your part designs or using more efficient machines.
The Relationship Between Machine and Labor Costs
While machine time accounts for the largest portion of costs, labor costs should not be underestimated. A more efficient machine may reduce the need for labor, but highly skilled operators are still essential for ensuring precision.
Material Costs in CNC Machining
Material selection plays a critical role in the overall cost of CNC machining. The type of material you choose will determine the base cost of the project and can influence other factors such as machine wear and part complexity.
Cost of Common Materials
Common CNC machining materials include metals such as aluminum, steel, and titanium, as well as plastics like nylon and PVC. The cost of materials varies depending on market trends and material availability. Metals like titanium tend to be more expensive than aluminum, and plastic parts may require less tool wear, making them more cost-effective.
Impact of Material Waste
CNC machining involves material removal, meaning there will be waste material. For highly detailed parts, this waste can add up, making the material costs more expensive. Using efficient cutting tools and techniques can help minimize material waste and reduce overall project costs.
Choosing the Right Material for Cost-Efficiency
While opting for cheaper materials might seem like a good way to save money, it’s important to consider the material’s suitability for your part’s requirements. Choosing a more durable material can prevent additional costs down the line due to failures or defects.
CNC Machining Costs: Location Matters
The cost of CNC machining can also vary depending on your location and the location of your CNC provider. You might be wondering why this matters so much, but the answer lies in the cost of labor and overhead in different regions.
How Geography Affects Pricing
In regions with high labor costs, like the U.S. and Europe, CNC machining can be significantly more expensive than in countries with lower labor costs, such as China or India. This makes outsourcing to offshore manufacturers a popular choice for cost-conscious businesses.
Local vs. International Manufacturing
While international manufacturing may offer cheaper rates, there are risks involved, such as communication barriers, longer lead times, and shipping costs. Local CNC machining providers offer more control over quality and timing, which may justify the higher price.
Understanding CNC Machining Setup Fees
Setup fees are an important part of CNC machining pricing. These fees are charged to cover the initial preparation required to begin machining, including tool changes, programming, and machine calibration.
What’s Included in Setup Fees
Setup fees typically include time spent preparing the machine, loading materials, and fine-tuning the program. These fees can range from a small fixed cost to a significant portion of the overall price, depending on the complexity of the job.
How Setup Costs Vary by Project
For small, low-quantity runs or prototypes, setup fees can be a larger portion of the cost. However, for larger production runs, setup costs are spread out over more parts, reducing the cost per part.
Reducing Setup Costs
By improving part designs and reducing the number of tool changes, you can minimize setup time and lower setup fees. Additionally, working with a skilled operator who can quickly adjust the machine settings will help reduce these costs.
Quantity and Volume Discounts in CNC Machining
Quantity plays a key role in CNC machining pricing. Larger orders often come with volume discounts, which can reduce the cost per part and lower the overall machining cost per hour.
How Order Size Impacts Pricing
When you increase the order quantity, the cost per part typically decreases due to economies of scale. Machining more parts per hour means less time spent setting up the machine, leading to lower costs overall.
Cost Reduction Strategies for Larger Orders
For large-scale projects, it’s essential to plan ahead to optimize machine time and reduce waste. By working with a CNC provider that understands how to streamline production, you can further reduce per-unit costs.
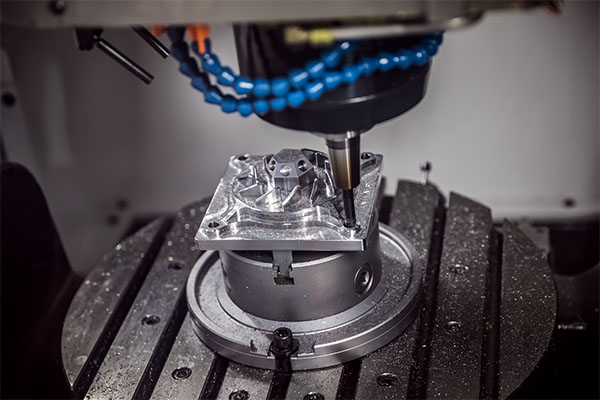
Hidden Costs in CNC Machining
While it’s easy to focus on the visible costs like machine time and material prices, there are hidden costs that can creep in if you’re not careful. These hidden costs can significantly affect the final price of your project.
Additional Fees That Might Surprise You
Hidden costs may include shipping, quality control inspections, or even packaging fees. To avoid these unexpected costs, always ensure that the provider offers a transparent quote and discusses potential extra fees upfront.
Preventing Hidden Costs
The best way to avoid hidden fees is to get a detailed, itemized quote from your CNC provider. This should include everything from material costs to post-processing charges. Be sure to ask questions about any potential additional fees to ensure you’re not caught off guard.
CNC Machining Pricing for Prototypes vs. Production Runs
CNC machining for prototypes is often more expensive than for large production runs. This is due to the fact that prototypes require additional setup, testing, and adjustments.
Prototype Pricing
Prototypes are typically priced higher because of the time spent on refining and adjusting the part’s design. However, prototyping is essential for ensuring that the final product meets your expectations.
Production Run Pricing
Once you move to a production run, the costs become more efficient. With larger quantities, the setup costs are amortized across the parts, reducing the overall cost per part.
Speed and Efficiency Considerations
Faster production rates can reduce the per-hour cost of CNC machining. By improving efficiencies, you can lower the cost per part, which is especially important for production runs.
How Do CNC Machining Providers Set Their Pricing?
CNC machining providers consider a number of factors when setting their pricing. Understanding these factors can help you get a better idea of what to expect when requesting a quote.
Factors Affecting Provider Pricing
Providers will consider machine costs, labor rates, overhead, and material costs when determining their rates. Additionally, factors like the complexity of the part, the volume of the order, and the timeline all play a role in pricing.
Negotiating Pricing with CNC Providers
It’s important to ask your CNC provider for a detailed quote and inquire about discounts for large orders or long-term contracts. Negotiating with providers who understand your needs can lead to cost savings.
Why CNC Machining Is Cost-Effective for High-Precision Parts
CNC machining is often seen as a more expensive option for low-volume manufacturing. However, when it comes to high-precision parts, CNC machining can actually be more cost-effective in the long run.
Long-Term Cost Savings
The precision and efficiency of CNC machining result in fewer defects and rework costs. For industries requiring strict tolerances, like aerospace or medical devices, CNC machining is the best choice despite its higher initial cost.
How It Compares to Traditional Manufacturing Methods
Compared to traditional manufacturing methods, CNC machining offers better quality and consistency at lower overall costs. While initial pricing might be higher, the savings on quality control and material waste make it a more cost-effective solution.
Common Misconceptions About CNC Machining Costs
There are several misconceptions about CNC machining pricing. Some believe CNC machining is only for large manufacturers or that it’s too expensive for small businesses.
Debunking Myths
CNC machining is accessible for businesses of all sizes. While it may seem like a large investment upfront, the accuracy and efficiency of the process make it a cost-effective solution in the long term.
When CNC Machining Isn’t the Most Cost-Effective Choice
For very simple parts or low quantities, CNC machining might not be the best choice. Traditional manufacturing methods may offer more cost-efficient alternatives for specific needs.
Kesimpulan
In summary, understanding CNC machining costs requires careful consideration of several factors, including machine type, material, part complexity, and order volume. By keeping these factors in mind, you can better plan your projects and avoid unexpected costs. Whether you’re creating a prototype or a production run, CNC machining offers unparalleled precision and efficiency, making it a reliable solution for businesses in various industries. Always seek transparent quotes and communicate your needs clearly to ensure you get the best pricing possible.
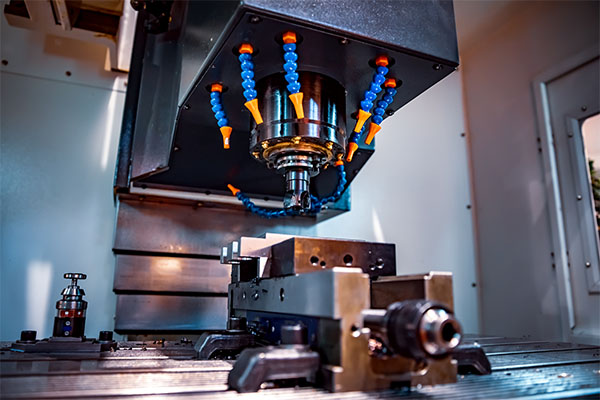
Bahagian Soalan Lazim
- What’s the average hourly rate for CNC machining?
The average hourly rate for CNC machining ranges from $40 to $150 per hour, depending on the type of machine, material, and complexity. - Why are setup fees included in the price?
Setup fees cover the time and effort required to configure the machine, load materials, and prepare the system for production. - How can I reduce the cost of my CNC machining project?
To reduce costs, choose cost-effective materials, optimize part designs for efficiency, and increase order volume to take advantage of bulk discounts. - What are the hidden costs of CNC machining?
Hidden costs can include shipping, packaging, quality assurance, and post-processing services. Always request an itemized quote. - Is CNC machining more expensive for prototypes?
Yes, prototyping typically costs more due to the additional setup, design adjustments, and testing involved. - How do I compare CNC machining providers effectively?
Compare quotes, machine capabilities, and experience. Ask for transparent pricing and inquire about potential additional fees. - What materials are most cost-effective for CNC machining?
Aluminum, plastics, and basic steel alloys are among the most cost-effective materials for CNC machining. - What factors can impact the overall cost of my CNC machining project?
Factors include material selection, part complexity, machine type, labor costs, and the size of the order.