pengenalan
Machining aluminum is a process that many industries rely on to create precise, durable, and lightweight parts. In this article, we will explore the best practices for machining aluminum efficiently, from choosing the right tools to managing heat buildup. Whether you are working with small, intricate components or larger parts, understanding how to optimize your machining processes can lead to significant improvements in both productivity and product quality.
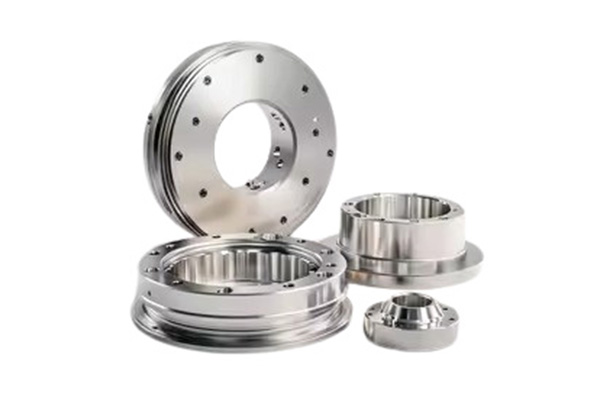
1. What are the benefits of machining Aluminum?
Aluminum is a widely used material in machining for a number of reasons. But here’s the kicker, it’s not just about its lightweight nature—aluminum offers a range of advantages in terms of durability, flexibility, and cost-effectiveness. One of the primary benefits is its excellent strength-to-weight ratio, which makes it ideal for industries such as aerospace and automotive. Its low density and high corrosion resistance also make it the preferred material in many environmental and structural applications.
Another major advantage of aluminum machining is its economic value. The material is relatively inexpensive compared to others like steel and titanium, making it a cost-effective choice for mass production. Plus, aluminum’s excellent machinability allows for high-speed cutting, which can lead to faster production times and reduced operational costs.
Aluminum’s popularity also lies in its versatility. Whether you are creating complex shapes or simple components, it can be used in a variety of applications. From thin-walled parts to high-performance aerospace components, aluminum machining is capable of delivering high precision while keeping material waste to a minimum.
Table 1: Benefits of Machining Aluminum
Benefit | Penerangan | Application |
---|---|---|
Lightweight | High strength-to-weight ratio | Aerospace, automotive, packaging |
Corrosion Resistance | Naturally resists rust and oxidation | Outdoor applications, marine industry |
Cost-Effective | Relatively inexpensive material | Mass production, low-cost manufacturing |
High Machinability | Easy to machine, allows high-speed cutting | Precision parts, intricate components |
2. How do you choose the right tools for machining Aluminum?
Choosing the right tools for machining aluminum is critical to ensuring efficiency and product quality. Ready for the good part? There are various tools available, each suited for different types of machining operations, such as cutting, drilling, and milling. The right tool depends on the specific requirements of the part you’re manufacturing.
The most commonly used tools for aluminum machining include high-speed steel (HSS) tools and carbide tools. HSS tools are more affordable and work well for softer aluminum alloys, while carbide tools are more durable and can handle harder grades of aluminum. Another important factor is the tool coating. Coatings like titanium nitride (TiN) are commonly used on tools for aluminum machining because they reduce wear and increase the lifespan of the tools.
In addition to material selection, the cutting geometry of the tool is crucial. Tools with sharp edges are essential for achieving a clean cut and reducing the risk of burr formation. Factors such as tool material, geometry, and coating all work together to ensure you get the best results while machining aluminum efficiently.
Table 2: Tools for Aluminum Machining
Tool Type | Material | Best For |
---|---|---|
High-Speed Steel (HSS) | Keluli | Softer aluminum alloys |
Carbide Tools | Carbide | Harder aluminum alloys |
Coated Tools | Titanium Nitride (TiN) | Durability, reducing wear |
3. What are the challenges of machining Aluminum?
Machining aluminum offers numerous benefits, but there are also some challenges that come with the process. This is where it gets interesting—while aluminum is relatively easy to machine, certain difficulties arise in ensuring quality and maintaining efficiency. One of the primary challenges is achieving a high-quality surface finish. Aluminum is highly prone to developing burrs, which can affect both the aesthetic and functional qualities of the part.
Deformation and warping are other common problems when machining aluminum, especially when cutting thick or large parts. The material’s soft and ductile nature means that it can easily bend or shift under machining forces. To combat this, it’s important to use proper fixturing techniques and maintain tight control over cutting parameters such as feed rates and speeds.
Heat generation is yet another hurdle to overcome. Aluminum has a low melting point, meaning it is particularly sensitive to heat buildup during machining. If excessive heat is not properly managed, it can cause the material to distort or even result in tool failure. To prevent this, effective cooling methods and tool selection must be carefully considered.
Table 3: Challenges in Machining Aluminum
Challenge | Impact | Solution |
---|---|---|
Surface Finish Issues | Formation of burrs and rough surfaces | Use sharp tools, adjust feed rates |
Deformation and Warping | Material bending under cutting forces | Proper fixturing, careful control of cutting parameters |
Heat Generation | Material distortion and tool failure | Cooling methods, proper tool materials |
4. How do you prevent material deformation during Aluminum machining?
Deformation during aluminum machining is a common challenge, but there are strategies to prevent it. What’s the real story? The key to reducing deformation lies in controlling the forces applied during cutting, particularly when working with thin or large parts. Proper fixturing is a fundamental technique. It ensures that the aluminum part is securely held in place, reducing any movement or flexing during machining. Without proper fixturing, even small forces can lead to significant warping.
Cooling and lubrication are essential to prevent deformation as well. Excessive heat can weaken aluminum, causing it to lose its shape and dimensional accuracy. Using the right cutting fluids helps to keep the material cool, reducing thermal expansion and maintaining precision. Coolants also act as lubricants, further improving the cutting process by reducing friction between the tool and material.
Lastly, controlling cutting speeds plays a crucial role in reducing deformation. If the cutting speeds are too high, it generates excess heat, while too low speeds can cause an inefficient cutting process. Finding the optimal speed for your material and tooling is key to maintaining both speed and quality during machining.
Table 4: Methods to Prevent Deformation
Method | Penerangan | Effectiveness |
---|---|---|
Proper Fixturing | Secure part to prevent flexing | High |
Cooling and Lubrication | Reduces heat buildup and friction | High |
Controlling Cutting Speeds | Adjust speeds to balance cutting efficiency and heat control | Moderate |
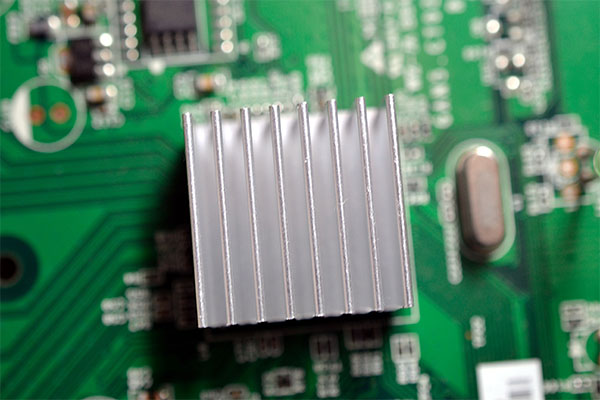
5. What cutting speeds are ideal for Aluminum machining?
Cutting speeds for aluminum are crucial to ensuring a smooth and efficient machining process. This is where it gets interesting—while aluminum is relatively soft, its cutting speeds need to be optimized to achieve the best results. The ideal feed rates and spindle speeds vary depending on the type of aluminum alloy and the machining operation. For example, when machining softer aluminum alloys, higher cutting speeds can be used without risking material damage. However, harder alloys require lower speeds to prevent heat buildup.
The aluminum alloy itself also influences the cutting speeds. Alloys with a higher percentage of copper or silicon are harder and require slower cutting speeds compared to those made primarily of aluminum. Moreover, cutting speeds must be adjusted based on tool wear. As tools wear down, they may not perform as efficiently, meaning the cutting speeds need to be reduced to avoid excessive wear and potential damage to the material.
Table 5: Cutting Speeds for Different Aluminum Alloys
Alloy Type | Recommended Cutting Speed (ft/min) | Tool Wear Adjustment |
---|---|---|
1000 Series (pure aluminum) | 500–1000 | Low wear |
2000 Series (copper alloy) | 300–700 | Moderate wear |
5000 Series (magnesium alloy) | 400–800 | Low to moderate wear |
7000 Series (zinc alloy) | 250–600 | High wear |
6. How does lubrication affect aluminum machining?
Lubrication plays a significant role in improving the efficiency of aluminum machining. Ready for the good part? Proper lubrication helps reduce friction between the cutting tool and the workpiece, leading to longer tool life and improved surface finish. It also serves to dissipate heat, reducing the chances of material deformation and tool wear.
There are several lubrication methods commonly used in aluminum machining. Flood coolant is the most traditional, providing a continuous stream of coolant to flush away chips and cool the cutting area. Another option is mist lubrication, which uses a fine spray of oil mixed with air to lubricate the cutting zone. Finally, dry machining, where no coolant is used, is sometimes employed in specific situations, although it can result in higher tool wear and heat buildup.
Choosing the best lubricant for aluminum depends on the specific machining process and tool material. For instance, when using high-speed steel tools, a water-soluble coolant is often the best choice. For carbide tools, a synthetic oil-based coolant might be more effective at reducing friction and improving cutting efficiency.
Table 6: Lubrication Methods for Aluminum Machining
Lubrication Method | Penerangan | Kelebihan |
---|---|---|
Flood Coolant | Continuous stream of coolant | Excellent cooling and chip removal |
Mist Lubrication | Fine spray of oil mixed with air | Reduced coolant use, effective cooling |
Dry Machining | No coolant used | Lower environmental impact |
7. What are the best machining methods for Aluminum?
When choosing a machining method for aluminum, it’s essential to understand the complexity of the part being produced. But here’s the kicker—while CNC machining is often the go-to method, there are several other techniques that might be better suited depending on the task. CNC machining offers unparalleled precision, making it ideal for complex parts with tight tolerances. It allows for automated production, reducing the risk of human error and improving repeatability.
On the other hand, manual machining may be more cost-effective for simpler components or one-off projects. Milling, turning, and drilling are common methods for machining aluminum, each suited for different tasks. Milling is often used for creating intricate shapes and flat surfaces, while turning is best for cylindrical parts. Drilling, of course, is essential for creating holes in aluminum components.
The right choice between CNC machining and manual machining depends on the part’s complexity and the production volume. For high-volume production, CNC machining is often the better choice due to its speed and efficiency. For low-volume or custom parts, manual machining may be more cost-effective and flexible.
Table 7: Comparison of Machining Methods for Aluminum
Method | Best For | Kelebihan |
---|---|---|
Pemesinan CNC | Complex, high-tolerance parts | Precision, repeatability, automation |
Manual Machining | Simple parts, low-volume production | Flexibility, lower setup costs |
Pengilangan | Flat surfaces, intricate shapes | Versatility, high-quality finishes |
8. How do you achieve the best surface finish when machining Aluminum?
Achieving the best surface finish when machining aluminum is key to ensuring the parts not only function correctly but also look professional. What’s the real story? It’s all about the right combination of tools, cutting parameters, and post-machining processes. The first step in achieving a smooth finish is selecting the right cutting tools. Tools with sharp edges and coatings such as TiN (Titanium Nitride) reduce friction and help minimize the formation of burrs and other imperfections.
Post-machining processes like polishing and anodizing can further enhance the surface finish. Polishing is especially important when the part will be visible or exposed to harsh environments, as it helps improve both aesthetics and corrosion resistance. Anodizing is a process that involves creating a protective oxide layer on the surface, improving the material’s resistance to wear and corrosion.
To make sure that the finish meets the necessary standards, you should also consider the impact of feed rates, speeds, and the amount of coolant being used. The right balance of these factors can help achieve a mirror-like surface finish and improve the overall quality of the part.
Table 8: Post-Machining Processes for Surface Finish
Proses | Purpose | Faedah |
---|---|---|
Menggilap | Improving aesthetics and surface smoothness | High-quality finish, corrosion resistance |
Anodizing | Adding a protective oxide layer | Enhanced durability, corrosion resistance |
Deburring | Removing sharp edges and burrs | Improved safety, aesthetics |
9. How do you handle heat buildup in Aluminum machining?
Heat buildup is a major concern when machining aluminum, particularly because of the material’s relatively low melting point. So, what’s the trick? Managing heat effectively is crucial to prevent deformation, tool wear, and poor surface finishes. Cooling techniques, including the use of flood coolant or mist lubrication, are commonly employed to control the temperature during machining.
Air cooling is another technique used to reduce heat buildup, especially in dry machining environments where no coolant is used. While air cooling doesn’t offer the same level of cooling as liquid-based methods, it can still help maintain a moderate temperature, especially for lighter machining operations. Tool material selection also plays a role in heat resistance. High-speed steel tools tend to be more heat-sensitive compared to carbide tools, which are better suited for high-heat machining operations.
By using the right combination of coolant, tool material, and cutting parameters, heat buildup during aluminum machining can be minimized, ensuring optimal tool life and part quality.
Table 9: Cooling Methods for Heat Management
Cooling Method | Penerangan | Best For |
---|---|---|
Flood Coolant | Continuous stream of coolant | High-volume, high-heat operations |
Air Cooling | Use of compressed air to reduce heat | Low-volume machining, dry machining |
Misting | Fine spray of coolant and air | Moderate heat reduction, light cutting |
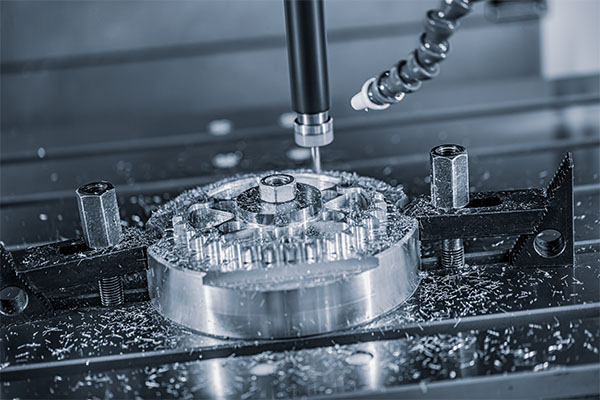
10. What are the environmental considerations when machining Aluminum?
Environmental concerns are becoming increasingly important in machining, especially with materials like aluminum, which is often recycled. But here’s the kicker—while aluminum is one of the most recyclable metals, it still generates waste and consumes energy during machining. One of the key considerations is minimizing waste and energy consumption during machining. Using energy-efficient machines and optimizing cutting parameters can help reduce the carbon footprint of the machining process.
Recycling aluminum scrap is another major environmental consideration. The recycling process not only conserves resources but also reduces the energy required to produce new aluminum from raw materials. Additionally, sustainable machining practices such as reducing coolant use, recycling cutting fluids, and utilizing green lubricants help lower the environmental impact.
By adopting sustainable practices, manufacturers can not only reduce their environmental footprint but also lower operational costs, making aluminum machining both eco-friendly and cost-effective.
Table 10: Sustainable Practices in Aluminum Machining
Practice | Penerangan | Faedah |
---|---|---|
Recycling Aluminum | Reusing aluminum scrap | Reduced resource consumption, energy savings |
Energy-Efficient Machines | Using machines that consume less energy | Lower operating costs, reduced carbon footprint |
Green Lubricants | Using eco-friendly lubricants | Lower environmental impact |
11. How does part complexity affect Aluminum machining?
The complexity of the part plays a significant role in determining the machining process used for aluminum. What’s the real story? Intricate designs with tight tolerances require more advanced machining methods to ensure precision. Complex geometries, such as those with deep pockets or thin walls, can present challenges in terms of tool access and material stability during machining.
Thin-walled parts are particularly prone to distortion during machining due to their low mass. To manage this, it’s important to control cutting forces and temperatures, as well as to use appropriate fixturing techniques. The more complex the design, the greater the need for specialized tools and equipment, such as multi-axis CNC machines, which can perform multiple operations without repositioning the workpiece.
Managing tight tolerances is also more difficult when dealing with complex parts. The smallest deviation can cause significant performance issues, especially in industries like aerospace or automotive. Proper quality control and precision measurement tools are required to ensure that the parts meet the necessary specifications.
Table 11: Impact of Part Complexity on Aluminum Machining
Complexity Level | Challenges | Penyelesaian |
---|---|---|
Simple | Easy to machine, fewer tool changes | Basic tools, lower machining time |
Complex | Difficult to fixture, tighter tolerances | Multi-axis CNC machines, precision fixtures |
Thin-Walled Parts | Susceptible to distortion and vibration | Careful tool selection, temperature control |
12. What role does Aluminum alloy play in machining?
The alloy composition of aluminum plays a major role in its machinability. Ready for the good part? Different alloys have unique characteristics that affect how they respond to machining processes. For example, 1000 series alloys are pure aluminum and are easy to machine, but they lack the strength needed for heavy-duty applications. On the other hand, 7000 series alloys, which contain zinc, are stronger but more difficult to machine due to their increased hardness.
The machining characteristics of aluminum alloys depend on several factors, including the alloy’s hardness, ductility, and strength. These factors dictate the choice of tools and machining parameters. For instance, high-strength alloys may require carbide tools or slower cutting speeds to prevent excessive wear or deformation. The alloy composition also impacts tool life, as harder alloys tend to wear tools out faster, requiring frequent maintenance or replacement.
Table 12: Machining Characteristics of Aluminum Alloys
Alloy Type | Hardness | Machinability | Tool Life Impact |
---|---|---|---|
1000 Series | Soft | Easy | Low |
2000 Series | Medium | Moderate | Moderate |
5000 Series | Medium | Moderate | Moderate |
7000 Series | Hard | Difficult | High |
13. What are common mistakes to avoid in Aluminum machining?
When machining aluminum, it’s crucial to avoid a few common mistakes that could compromise the quality of your finished product or even damage the equipment. One of the primary issues is overheating the material. Aluminum has a relatively low melting point, and excessive heat generated during machining can cause the material to soften, leading to issues such as dimensional inaccuracy or poor surface finish. It’s important to use proper cutting speeds and feeds, ensuring the material stays within the optimal temperature range.
Another mistake to watch out for is using incorrect tooling or feeds. Aluminum machining requires specific tools, and using the wrong ones can lead to inefficiencies, poor surface finishes, or even tool damage. For instance, using dull tools or improper feeds can cause excessive friction, overheating, and premature tool wear. Matching the right tool to the application is key to achieving optimal results.
Lastly, many operators overlook the significance of ignoring material properties. While aluminum is a versatile material, its properties can vary significantly depending on the alloy. Some aluminum alloys are more prone to work hardening, while others are more susceptible to corrosion. Understanding these properties and adjusting the machining process accordingly is essential to prevent issues such as tool breakage, surface imperfections, or inconsistent results.
What’s the real story? By avoiding these common mistakes, you can ensure your aluminum machining processes are smooth, efficient, and cost-effective. Let’s dive deeper into how to improve efficiency in the next section.
Table 13: Common Mistakes in Aluminum Machining
Mistake | Explanation | Consequences |
---|---|---|
Overheating the material | Excessive heat can soften the aluminum, leading to inaccuracies. | Dimensional issues, poor surface finish |
Using incorrect tooling | Using improper tools can lead to poor cutting performance. | Tool damage, inefficiency |
Ignoring material properties | Not understanding the material’s properties can cause errors. | Tool breakage, inconsistent results |
14. How do you improve efficiency in Aluminum machining?
Improving efficiency in aluminum machining requires a multifaceted approach that incorporates advanced technology and optimized workflows. Automation and advanced CNC machines are game-changers in this regard. These machines offer high precision and repeatability, reducing human error and increasing production speed. Additionally, automated processes help minimize downtime, ensuring that the machining process runs smoothly around the clock.
Optimizing tool paths and setups is another critical aspect of improving efficiency. By carefully planning the tool paths and ensuring they are as short and direct as possible, you can reduce unnecessary movement and speed up the machining process. Moreover, minimizing tool changes and retooling can save both time and money.
But here’s the kicker—implementing lean manufacturing principles can also significantly improve machining efficiency. Lean practices focus on eliminating waste, reducing cycle times, and ensuring that all resources are used effectively. By streamlining the production process, you can not only improve efficiency but also cut costs and enhance overall product quality.
Ready for the good part? These improvements can lead to faster turnaround times, better resource utilization, and ultimately, higher profits. Let’s explore the future trends in aluminum machining next.
Table 14: Strategies to Improve Aluminum Machining Efficiency
Strategy | Penerangan | Faedah |
---|---|---|
Automation and CNC machines | Using automated systems and CNC machines for precision machining. | Increased precision, reduced downtime |
Optimizing tool paths and setups | Planning efficient tool paths to minimize movement and retooling. | Faster cycle times, cost reduction |
Lean manufacturing principles | Eliminating waste and streamlining processes. | Improved efficiency, reduced costs |
15. What future trends are emerging in Aluminum machining?
As the aluminum machining industry continues to evolve, several emerging trends are shaping the future of the sector. Advances in machining technology are perhaps the most significant. New CNC machines and cutting-edge tools are enabling manufacturers to achieve higher precision, faster processing speeds, and more complex geometries. These advancements are opening up new possibilities in industries such as aerospace, automotive, and medical devices, where precision and efficiency are paramount.
The role of artificial intelligence in machining is another trend gaining momentum. AI is being used to optimize machining processes in real-time by predicting tool wear, adjusting cutting speeds, and ensuring optimal conditions. With AI’s ability to learn from data, it can offer insights that human operators might miss, leading to more efficient and precise machining.
But wait, there’s more—upcoming materials and alloys are also expected to influence the future of aluminum machining. Manufacturers are constantly developing new aluminum alloys with improved properties, such as greater strength, resistance to corrosion, and better machinability. These innovations will require new machining techniques and tools to handle the evolving materials.
What’s the real story? The future of aluminum machining looks incredibly exciting, with technology playing a pivotal role in improving efficiency, precision, and overall capabilities. Let’s move on to answer some frequently asked questions.
Table 15: Emerging Trends in Aluminum Machining
Trend | Penerangan | Impact |
---|---|---|
Advances in machining technology | New CNC machines and tools enable more complex machining. | Increased precision, speed, and capability |
AI in machining | Artificial intelligence optimizes the machining process in real-time. | Enhanced efficiency, predictive capabilities |
Upcoming materials and alloys | New aluminum alloys with improved properties are emerging. | Demand for new machining techniques and tools |
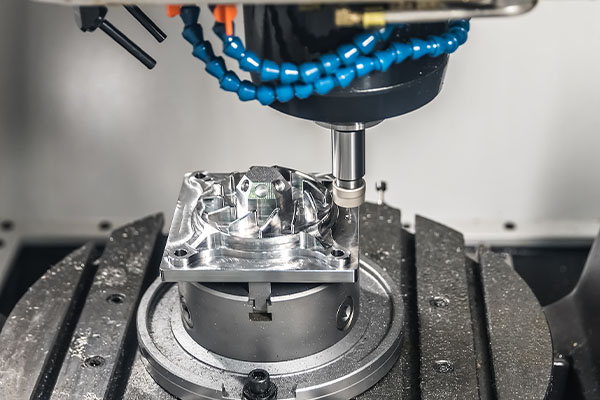
Bahagian Soalan Lazim
S1: What is Aluminum machining?
Aluminum machining is the process of cutting, shaping, and finishing aluminum materials using various tools and techniques like milling, turning, and drilling. It is widely used in industries such as aerospace, automotive, and manufacturing.
S2: How does CNC machining work for Aluminum?
CNC machining uses computer-controlled machines to precisely cut and shape aluminum. The process is highly accurate and efficient, making it ideal for complex parts that require tight tolerances.
S3: What are the best tools for machining Aluminum?
The best tools for machining aluminum include high-speed steel (HSS) tools, carbide tools, and tools with specific coatings like TiN to reduce wear and improve performance. Tool selection depends on the type of operation and aluminum alloy used.
S4: Why is Aluminum prone to deformation during machining?
Aluminum is relatively soft and can easily deform under pressure. Deformation can be caused by excessive cutting forces, high temperatures, and improper fixturing. Careful handling and the right machining parameters are essential to prevent this.
S5: How do you maintain tool life when machining Aluminum?
To maintain tool life, it’s important to use the correct cutting speeds, ensure proper lubrication, and regularly monitor tool wear. Using high-quality tools with coatings also helps reduce friction and prolongs tool life.