pengenalan
Machining large parts presents unique challenges and requires specialized techniques and equipment. As industries continue to demand high-precision and high-quality large components, manufacturers must adapt to meet these evolving needs. In this article, we’ll explore the challenges faced in machining large parts, the tools and techniques used to overcome them, and best practices for ensuring efficiency and quality. Whether you’re involved in manufacturing, machining, or working with large-scale projects, understanding these challenges and solutions can provide significant advantages. Let’s dive in and see how the right approach can make all the difference.
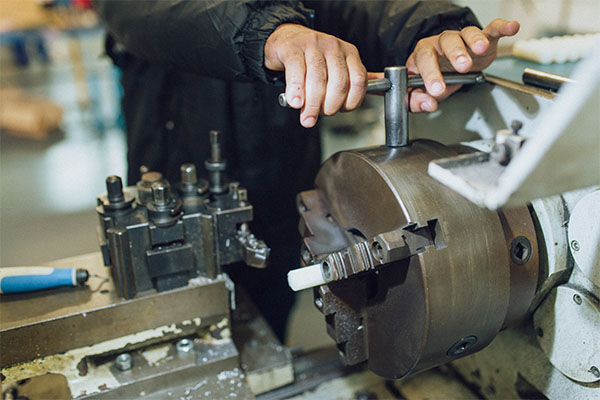
1. What Are the Key Challenges in Machining Large Parts?
When it comes to machining large parts, the challenges are multi-faceted. The first major hurdle is the sheer size and weight of the components. Larger parts often require machines with greater capabilities, and managing the increased forces during machining can lead to complications.
But here’s the kicker: achieving high precision in large parts is no easy feat. With larger workpieces, even slight deviations in measurement can result in significant errors. One of the key issues with large part machining is ensuring that the entire part remains aligned during the process. A shift in positioning can lead to costly mistakes, which is why proper fixturing and clamping are critical.
Another challenge is the tool wear. Larger parts require extended machining times, which leads to greater tool wear. The durability of cutting tools becomes even more important in these situations. Plus, the process requires managing increased thermal expansion and thermal deformation due to the heat generated during the cutting process.
One more thing: the handling and transportation of large parts can be just as complex as the machining itself. Moving large parts between different machines, stages of the process, or even to final inspection stations can pose logistical challenges that can affect workflow and timing.
To overcome these challenges, manufacturers often rely on high-precision CNC machines and expert operators. However, careful planning and precision are essential to ensuring that large parts are machined correctly.
Table 1: Key Challenges in Machining Large Parts
Challenge | Impact | Solution |
---|---|---|
Size and weight | Increased forces during machining | Use heavy-duty machines and fixtures |
Achieving precision | Potential for misalignment and errors | Use advanced CNC and measurement systems |
Tool wear | Reduced tool life due to longer machining | Select durable tools and manage tool wear |
Thermal expansion and deformation | Impact on machining accuracy | Implement effective cooling techniques |
Handling and transportation | Risk of delays or damage during moves | Use specialized lifting equipment and workflow optimization |
2. How Do You Choose the Right Tools for Machining Large Parts?
Choosing the right tools for machining large parts is critical for efficiency and accuracy. It’s not just about picking any tool; it’s about selecting the correct type of cutting tool for the material and the task at hand.
What’s the real story? The key to success lies in understanding the unique demands of large part machining. The tool selection process starts with the material you’re working with. Harder materials like titanium or tool steel require more robust tools with higher cutting power. On the other hand, softer materials like aluminum may allow for faster cutting speeds and less wear on the tools.
Tool strength is a critical factor, especially when dealing with heavy, large workpieces. Tools must be durable enough to withstand the high cutting forces involved in the machining of large parts. Alongside durability, the geometry of the cutting tool also plays a significant role. A tool with improper geometry can lead to excessive wear, increased temperatures, and poor finishes.
Ready for the good part? Selecting the right cutting speeds and feeds is just as important. When machining large parts, it’s essential to adjust cutting speeds and feeds to balance performance with tool life. Using too high a speed can cause excessive heat buildup, while too low a speed can lead to inefficiency and extended machining times.
Another consideration is the use of multi-tool systems, which can improve productivity by allowing operators to quickly switch between different tools for different operations. Additionally, ensuring that the tool can accommodate the dimensions of the workpiece is crucial, as some tools may not be able to reach all areas of large parts.
Table 2: Factors in Tool Selection for Large Part Machining
Factor | Impact | Consideration |
---|---|---|
Material type | Affects tool strength and cutting power | Choose appropriate tool material |
Tool strength | Affects durability and performance | Select robust tools for heavy-duty use |
Tool geometry | Influences cutting efficiency and tool life | Optimize geometry for specific tasks |
Cutting speeds and feeds | Affects machining time and tool life | Balance cutting speed with tool durability |
Tool compatibility | Determines ability to reach all part areas | Use adjustable or multi-tool systems |
3. What Are the Best Practices for Setting Up Large Parts in CNC Machines?
Setting up large parts in CNC machines requires careful planning and execution. The process starts with securing the workpiece on the machine bed. But here’s the kicker: if the workpiece isn’t properly secured, even the smallest movements during machining can cause major deviations, leading to defects or scrap. Proper clamping and fixturing are absolutely critical when machining large parts.
The first step in the setup process is determining the appropriate clamping system. For large parts, manufacturers often rely on heavy-duty clamping systems that can provide even pressure across the entire workpiece. These systems help maintain the workpiece’s position during machining, preventing any movement that could affect precision.
Once the part is securely clamped, the next task is alignment. Ensuring the workpiece is perfectly aligned with the machine’s cutting tools is crucial for achieving accurate results. Any misalignment can lead to dimensional inaccuracies, which can compound as the machining process progresses.
What’s the real story here? The setup time for large parts can often be quite extensive. But taking the time to ensure that everything is perfectly aligned and secure from the beginning will ultimately save time and money by preventing errors during machining. Additionally, it is essential to calibrate the CNC machine before starting any machining operations to ensure that it is running at optimal performance.
Another best practice is to regularly check for wear and tear on both the machine and the tooling throughout the machining process. Regular inspection of tools and parts will ensure that the machining process remains efficient and that any issues are identified before they become major problems.
Table 3: Best Practices for CNC Setup of Large Parts
Practice | Benefit | Best Practice Tips |
---|---|---|
Secure clamping | Prevents movement and ensures precision | Use heavy-duty, evenly distributed clamping systems |
Proper alignment | Ensures accuracy during machining | Use precision alignment tools and methods |
CNC machine calibration | Ensures machine operates at optimal settings | Calibrate regularly for best results |
Tool and part inspection | Prevents errors and ensures quality | Conduct regular checks on tools and parts |
4. How Do You Achieve Precision in Large Part Machining?
Achieving precision in large part machining is one of the most significant challenges faced by manufacturers. The larger the part, the harder it is to maintain precise measurements and tolerances throughout the machining process.
Ready for the good part? One of the most effective ways to ensure precision is through the use of advanced CNC machines that incorporate high-precision measurement systems. These systems continuously monitor the part’s dimensions during machining, providing real-time feedback to the operator. If any deviations from the desired dimensions are detected, the system can make adjustments on the fly, ensuring that the final product meets the required specifications.
Another technique for achieving precision in large parts is the use of high-quality tooling. The sharper the tool, the more accurate the cuts. Over time, tools wear down, which can lead to inaccuracies in the finished part. Using tools with longer lifespans, and regularly checking tool conditions, is essential for maintaining the quality and precision of large parts.
Furthermore, temperature control plays a key role in maintaining precision. When machining large parts, the process generates a significant amount of heat, which can lead to thermal deformation. This is especially problematic with large parts, as even small amounts of thermal distortion can cause significant changes in the part’s dimensions. Effective cooling systems are a must for keeping the workpiece temperature stable and reducing the risk of thermal expansion.
Another consideration for maintaining precision is proper programming. CNC programs for large parts should be thoroughly tested and optimized to ensure that all cutting paths are accurate. Even a slight error in the program can lead to significant defects in the final product.
Table 4: Techniques for Achieving Precision in Large Part Machining
Technique | Impact | Consideration |
---|---|---|
CNC measurement systems | Provides real-time feedback for precision | Invest in high-precision systems |
High-quality tooling | Improves accuracy and cutting efficiency | Use durable, sharp tools for longer life |
Temperature control | Prevents thermal distortion | Use effective cooling systems |
Optimized CNC programming | Ensures accurate cutting paths | Thoroughly test programs before use |
5. What Materials Are Commonly Used in Large Part Machining?
When machining large parts, the material selection plays a crucial role in determining both the difficulty and the effectiveness of the process. Not all materials are suitable for large-scale machining, and selecting the right one can make or break the success of the project.
What’s the real story? The most commonly used materials for large part machining include various metals such as steel, aluminum, and titanium. Steel, being one of the most widely used materials in manufacturing, is known for its strength and durability. However, it can also be challenging to machine, especially in large parts, due to its hardness and tendency to generate heat during machining.
Aluminum, on the other hand, is much easier to machine and is commonly used in industries like aerospace and automotive for large components. It’s lightweight, which makes it ideal for large parts that require mobility, but it is not as strong as steel or titanium. Nonetheless, its lower cost and ease of machining make it a popular choice for many applications.
Titanium, though more expensive, is often used for applications that require high strength-to-weight ratios, like in aerospace. However, machining titanium presents its own set of challenges, including higher cutting forces and tool wear. Specialized tools and cutting techniques are often required to work with titanium successfully.
Finally, some large parts may require the use of composite materials or plastics, depending on the application. These materials are often lighter and less expensive, but they may not offer the same level of durability as metals.
Table 5: Common Materials for Large Part Machining
Material | Characteristics | Aplikasi |
---|---|---|
Keluli | Strong, durable, harder to machine | Construction, automotive |
aluminium | Lightweight, easier to machine, cost-effective | Aerospace, automotive |
titanium | High strength-to-weight ratio, expensive | Aerospace, medical devices |
Composite materials and plastics | Lightweight, lower durability | Consumer products, automotive |
Kesimpulan
In conclusion, machining large parts comes with its set of challenges, but understanding these obstacles and implementing the right strategies can lead to successful outcomes. The key to overcoming these challenges lies in selecting the right tools, managing precision, choosing appropriate materials, and adhering to best practices in setup and operation. By addressing these factors, manufacturers can reduce errors, increase efficiency, and ensure high-quality results in their large part machining projects. The right approach, combined with the latest technology and techniques, can help overcome these challenges and improve machining operations across industries.
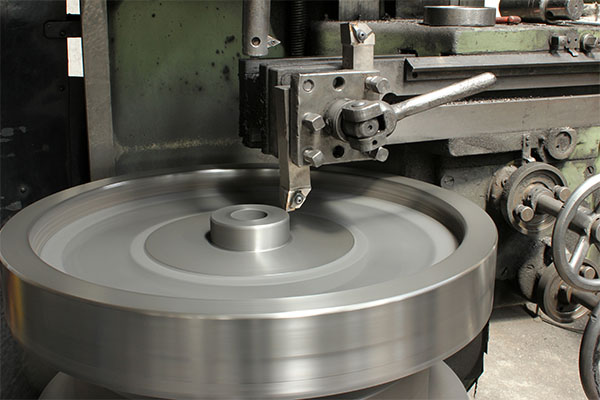
6. How Do You Control Heat and Minimize Thermal Deformation?
Controlling heat and minimizing thermal deformation during large part machining is a crucial factor in achieving precision and maintaining part quality. The process of machining large parts generates significant heat due to the cutting action, friction, and material removal. If this heat is not properly managed, it can lead to thermal expansion or deformation, affecting the final part dimensions.
What’s the real story? The most effective way to control heat is through proper cooling techniques. Coolants are used to absorb heat generated during machining and dissipate it, preventing excessive temperature buildup. There are several types of coolants, such as oils, water-based solutions, and air cooling, each suitable for different applications. The type of coolant you choose depends on the material you’re machining, the speed of the cut, and the machine being used.
Another key factor in controlling heat is selecting the right cutting parameters. Cutting speeds that are too high can lead to excessive heat generation, while too slow cutting speeds can lead to inefficient material removal. By finding the optimal cutting speed for the material and part size, manufacturers can reduce the risk of heat-related deformation.
But here’s the kicker: Tool material selection is another critical factor. Some tools are designed to withstand higher temperatures, which reduces the chances of thermal deformation during machining. For example, carbide tools can handle higher temperatures than high-speed steel, making them ideal for high-heat machining operations.
Thermal deformation can also be minimized through machine control. Modern CNC machines come equipped with advanced cooling systems and temperature sensors that monitor the temperature during machining and adjust as necessary to maintain consistent performance. Some machines are even equipped with temperature compensation features that allow them to make real-time adjustments to the machining process, ensuring that thermal effects are minimized.
Table 6: Cooling Techniques for Managing Heat in Large Part Machining
Cooling Method | Effectiveness | Consideration |
---|---|---|
Oil-based coolants | Effective at high cutting speeds | Requires proper disposal management |
Water-based coolants | Commonly used for precision cuts | Can corrode if not maintained properly |
Air cooling | Ideal for light cuts and small components | Less effective for large parts or high-speed cutting |
Integrated machine cooling systems | Provides real-time cooling during operation | Ensures consistent temperature management |
7. What Are the Key Considerations for Large Part Machining Surface Finishes?
Achieving the desired surface finish on large parts is one of the most important aspects of machining. The surface finish is critical for both the functionality and aesthetics of the part. It directly impacts factors like friction, wear resistance, and how the part interacts with other components in its assembly.
What’s the real story? The surface finish you achieve depends on various factors, including the cutting tool used, the machining process, and the material being worked with. For example, when working with softer materials like aluminum, you may achieve a smoother finish with higher cutting speeds, whereas harder materials like steel may require slower cutting speeds and finer tooling to achieve the desired finish.
One of the most effective ways to control the surface finish is through the choice of tooling. Tools with sharp edges and fine geometry can help produce a smoother surface by reducing vibrations and cutting forces during machining. Additionally, selecting the right coating for your tools, such as carbide or ceramic coatings, can reduce friction and improve the finish quality.
Ready for the good part? Another key factor in achieving a quality surface finish is controlling vibration during machining. Large parts are more susceptible to vibration due to their size and weight, and even small vibrations can cause imperfections on the surface. To minimize vibration, manufacturers use techniques such as machine dampening systems or special fixturing to secure the part more effectively.
Finally, post-machining processes like grinding, polishing, or honing can further improve the surface finish of large parts. These finishing processes are typically used for parts that require ultra-smooth finishes, such as those used in aerospace or automotive applications.
Table 7: Surface Finish Techniques for Large Part Machining
Technique | Effectiveness | Consideration |
---|---|---|
Sharp tooling and geometry | Reduces vibration and improves surface smoothness | Requires precision tool sharpening |
Tool coatings (e.g., carbide) | Reduces friction and wear | Coating choice depends on material |
Machine dampening systems | Prevents surface imperfections due to vibration | Requires proper machine setup |
Post-machining processes (grinding, honing) | Improves finish quality for high-precision applications | Time-consuming and adds cost |
8. How Does the Size of the Workpiece Affect the Machining Process?
The size of the workpiece significantly impacts nearly every aspect of the machining process, from the type of equipment used to the time required to complete the job. Larger parts require more advanced machinery, longer machining times, and more careful handling to maintain precision.
What’s the real story? One of the first things that changes when machining large parts is the type of machinery used. Standard CNC machines may not be capable of handling larger parts, so manufacturers often need to invest in specialized equipment like gantry machines, large vertical mills, or horizontal boring mills. These machines are designed to accommodate larger workpieces and provide the necessary stability to handle the increased cutting forces.
Another factor is the time required for machining. Larger parts generally take longer to machine due to their size and the increased number of operations needed to complete the part. Longer machining times increase the risk of tool wear, which can affect precision and quality. Additionally, large parts require more cooling and lubrication to manage heat buildup during the machining process.
But here’s the kicker: The handling of large parts is just as critical as the machining process itself. Large parts can be cumbersome and difficult to transport between different machines or stages of production. Specialized lifting equipment and fixtures are often necessary to ensure that the parts are moved safely without causing damage.
Finally, the size of the part can also affect the precision of machining. Larger parts are more susceptible to vibrations, thermal expansion, and deflections during machining, which can lead to inaccuracies. It’s important to use the right setup, tooling, and machine calibration to ensure that the part meets the required specifications.
Table 8: Impact of Workpiece Size on Machining
Factor | Impact | Consideration |
---|---|---|
Equipment size | Determines the type of machine used | Requires large-capacity machines |
Machining time | Longer machining times and tool wear | Increases operational costs |
Handling and transportation | Increased difficulty in moving large parts | Use specialized lifting and handling equipment |
Ketepatan | Larger parts more susceptible to vibrations and thermal effects | Implement vibration control and precise setup |
9. What Are the Cost Implications of Machining Large Parts?
Machining large parts can be significantly more expensive than machining smaller components due to various factors, including the cost of materials, tooling, labor, and machine time. Understanding the cost implications is critical for manufacturers to optimize their operations and maximize profitability.
What’s the real story? One of the primary cost drivers in large part machining is the price of materials. Large parts require more raw material, which increases the overall material costs. Additionally, the complexity of machining large parts can lead to higher labor costs. Skilled labor is required to set up, monitor, and operate machines that can handle large parts, and this expertise comes at a premium.
Tooling costs also increase with the size of the part. Larger parts require more robust tools that can withstand the increased cutting forces, which can be more expensive. The longer machining time associated with large parts also drives up the overall cost. Longer machining times lead to higher energy consumption, increased wear on machines, and greater consumption of cooling fluids and lubricants.
Ready for the good part? One way to reduce costs in large part machining is to optimize the machining process. By carefully selecting the right tools, materials, and machining parameters, manufacturers can reduce waste, minimize tool wear, and shorten machining times. Automation is another potential cost-saving measure. Using robots or automated systems for handling large parts can reduce labor costs and improve efficiency.
Finally, manufacturers should also consider the potential for scrap and rework. Large parts are more expensive to scrap, and any rework needed after machining can significantly increase the cost of the final product. Maintaining strict quality control throughout the process can help mitigate these costs.
Table 9: Cost Factors in Large Part Machining
Factor | Impact | Consideration |
---|---|---|
Material costs | Higher material usage for large parts | Requires efficient material planning |
Labor costs | Skilled labor needed for larger parts | Invest in training or automation |
Tooling costs | More robust tools needed for larger parts | Choose tools that provide the best value |
Machining time | Longer machining times increase costs | Optimize cutting parameters and machine time |
Scrap and rework | Increased costs if parts are scrapped or reworked | Implement quality control to minimize errors |
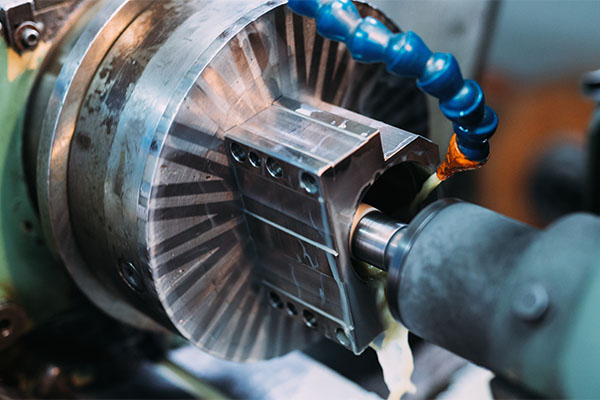
10. What Are the Latest Technological Advances in Large Part Machining?
Advancements in technology continue to transform the field of large part machining. New innovations in machinery, automation, and materials science are allowing manufacturers to achieve greater precision, efficiency, and cost-effectiveness when working with large parts.
What’s the real story? One of the most significant advancements in recent years is the development of multi-axis CNC machines. These machines allow for more complex cuts and greater precision in large part machining. By utilizing multiple axes of movement, manufacturers can machine more intricate features on large parts without having to reposition the workpiece.
Another innovation is the increased use of robotics and automation in large part machining. Robots can be used for tasks such as material handling, tool changing, and inspection, reducing the need for manual labor and improving efficiency. Automation also helps reduce the risk of human error, ensuring that the machining process remains consistent and precise.
Ready for the good part? AI and machine learning are beginning to play a more significant role in large part machining. These technologies can be used to optimize machining parameters in real-time, ensuring that the cutting process remains efficient and precise throughout. AI can also predict tool wear, allowing manufacturers to schedule maintenance before issues arise, reducing downtime and improving overall efficiency.
Additionally, new materials and coatings are being developed to improve the performance of cutting tools. These innovations help reduce friction, increase tool life, and improve the overall quality of the machined parts. Advances in additive manufacturing are also providing new ways to create large parts, offering potential cost savings and reducing material waste.
Table 10: Technological Advances in Large Part Machining
Teknologi | Impact | Consideration |
---|---|---|
Multi-axis CNC machines | Increased precision and complexity | Requires advanced machine setup and training |
Robotics and automation | Reduces manual labor and improves efficiency | Invest in robotic systems for material handling and tool changes |
AI and machine learning | Optimizes cutting parameters and predicts tool wear | Implement AI systems for real-time process optimization |
New materials and coatings | Reduces friction and improves tool life | Invest in high-performance coatings |
Pembuatan aditif | Reduces material waste and cost | Ideal for prototypes or low-volume production |
11. How Do You Ensure Quality Control in Large Part Machining?
Ensuring quality control in large part machining is essential for producing parts that meet the required specifications and function properly in their intended applications. Quality control is not just about checking dimensions; it involves a holistic approach that includes monitoring the entire machining process.
Ready for the good part? One of the key tools in ensuring quality is the use of precision measurement systems. These systems can be integrated into CNC machines or used as standalone tools to verify part dimensions in real-time. This ensures that any deviations from the desired specifications are caught early in the process, reducing the likelihood of defects in the final part.
Another critical aspect of quality control is using advanced inspection techniques. Coordinate Measuring Machines (CMM) are commonly used for large part inspection, as they can measure the exact dimensions of a part with high accuracy. CMMs use probes to touch various points on the part’s surface and create a 3D model of the part that can be compared to the original design.
But here’s the kicker: continuous monitoring of the machining process is essential for maintaining quality. Many CNC machines today are equipped with sensors that track various factors such as temperature, vibration, and cutting forces during machining. This real-time data allows operators to make adjustments to the process as needed to ensure that the part remains within tolerance.
Finally, regular audits and checks are vital. Even with the best equipment, human error can still occur. Regular inspections of tools, machines, and the final part are necessary to ensure that all aspects of the process are up to standard.
Table 11: Quality Control Methods in Large Part Machining
Method | Impact | Consideration |
---|---|---|
Precision measurement systems | Ensures accurate dimensions during machining | Integrate with CNC machines for real-time checks |
Coordinate Measuring Machines (CMM) | Provides detailed inspection of large parts | Requires skilled operators to interpret results |
Real-time monitoring systems | Tracks process data and ensures consistency | Use sensors for temperature, vibration, and cutting forces |
Regular audits and inspections | Ensures adherence to quality standards | Schedule frequent checks throughout the process |
12. How Does Large Part Machining Differ from Standard Machining?
Machining large parts involves several differences compared to machining smaller, more standard components. While the basic principles of machining remain the same, the unique challenges and requirements of large part machining set it apart.
What’s the real story here? One of the biggest differences is the size of the equipment involved. Large parts require much larger CNC machines, which can handle the size, weight, and complexity of the components. These machines must be able to withstand the forces generated during the machining process, which often leads to more complex machine designs and a higher initial investment.
In terms of the machining process itself, large parts often require more steps, longer machining times, and more frequent tool changes. As mentioned earlier, this is due to the increased wear on tools, the need for longer cutting times, and the challenges associated with keeping the workpiece aligned.
Another major difference is the precision required. While small parts often require high precision, large parts require even more care and attention to maintain the necessary tolerances. The slightest deviation in a large part can lead to significant issues, especially in industries like aerospace, automotive, and defense.
Ready for the good part? Large parts also require specialized handling and logistics. Moving large parts between machining centers or to the inspection stations requires specialized equipment and can introduce additional risks for damage or delays.
Table 12: Key Differences Between Large and Standard Part Machining
Factor | Large Part Machining | Standard Part Machining |
---|---|---|
Equipment size | Requires large CNC machines | Uses smaller, more standard machines |
Machining time | Longer machining times and more operations | Faster machining times and fewer operations |
Ketepatan | Higher precision required | Standard precision is often sufficient |
Handling and logistics | Requires specialized lifting and moving equipment | Easier to handle and move |
Tool wear | More tool wear due to longer machining times | Lower tool wear in smaller parts |
13. What Are the Most Common Types of CNC Machines for Machining Large Parts?
When machining large parts, manufacturers must use specialized CNC machines designed to handle larger workpieces. These machines provide the necessary precision and stability for machining large components and ensuring that they meet the required specifications.
What’s the real story? The most common type of CNC machine used for large part machining is the gantry machine. Gantry machines are designed with a large, rigid structure that can support large parts. They are ideal for machining large, flat components like automotive parts, aircraft fuselages, and heavy machinery components. These machines have multiple axes of movement, which allow for complex cutting operations on large parts.
Another commonly used CNC machine is the horizontal boring mill. These machines are used for machining large, heavy parts that require precise drilling and boring. Horizontal boring mills can handle parts that are too large for vertical machines, and they can be used to drill large holes, mill flat surfaces, and even complete full machining operations on massive components.
Ready for the good part? Vertical milling machines are also used in large part machining, particularly for large parts that require precise surface finishes. These machines can be equipped with rotary tables and other attachments to accommodate larger workpieces.
Other specialized machines include turning centers dan lathe machines that can handle large cylindrical parts, as well as Mesin CNC 5 paksi that provide unparalleled flexibility in machining large, complex parts.
Table 13: Common CNC Machines for Large Part Machining
Machine Type | Keupayaan | Aplikasi |
---|---|---|
Gantry machines | Large, rigid structure for complex cuts | Aerospace, automotive, heavy machinery |
Horizontal boring mills | Drilling and boring large, heavy parts | Automotive, construction, power generation |
Vertical milling machines | Precision milling for large parts | Aerospace, automotive, defense |
Turning centers and lathes | Machining of large cylindrical parts | Oil and gas, aerospace, automotive |
Mesin CNC 5 paksi | High flexibility for complex parts | Aerospace, medical devices, automotive |
14. What Safety Protocols Should Be Followed When Machining Large Parts?
Safety is paramount in large part machining due to the size and weight of the components, as well as the complexity of the machinery used. There are several safety protocols that manufacturers must adhere to in order to protect both workers and the equipment.
What’s the real story? The first step in ensuring safety is proper machine setup. Before starting any machining operation, operators should verify that all components are properly secured and that the machine is functioning as expected. Machine calibration is crucial to ensure that the cutting tools are aligned correctly and that there is no risk of machine malfunction.
But here’s the kicker: operators must also be aware of the physical risks associated with machining large parts. These parts are heavy and can be difficult to handle, requiring special lifting equipment and support to prevent injury. Using appropriate lifting tools and machinery to move large parts can significantly reduce the risk of accidents.
Another key safety consideration is personal protective equipment (PPE). Operators should wear the necessary PPE, including safety glasses, hearing protection, and gloves, to protect themselves from flying debris, high noise levels, and sharp edges. Additionally, ensuring that the work area is clean and free of obstructions is essential for maintaining safety during machining operations.
Ready for the good part? Regular maintenance of both the machines and the workplace environment is vital to ensuring ongoing safety. Machines should be serviced regularly to avoid breakdowns, and the work area should be kept organized to prevent accidents from occurring.
Table 14: Key Safety Protocols in Large Part Machining
Protocol | Importance | Consideration |
---|---|---|
Machine setup and calibration | Ensures machine accuracy and safety | Always calibrate before use |
Lifting and handling equipment | Reduces risk of injury from heavy parts | Use proper lifting tools |
Personal protective equipment (PPE) | Prevents injuries during machining | Ensure workers wear appropriate gear |
Clean and organized work area | Minimizes risks and accidents | Regularly clean and organize the workspace |
Regular machine maintenance | Prevents breakdowns and accidents | Implement a routine maintenance schedule |
15. How Do You Choose a Machining Service for Large Parts?
Memilih yang betul machining service for large parts is a critical decision that can affect the overall success of a project. The right service provider should have the experience, equipment, and expertise to handle large parts with precision and efficiency.
Ready for the good part? The first factor to consider when selecting a machining service is their experience with large parts. Experienced manufacturers will have the necessary expertise to handle the unique challenges of machining large components. They should be able to demonstrate their capability through past projects and client testimonials.
Another key factor is the equipment the service provider uses. The machining service should have access to high-quality, specialized equipment capable of handling large parts. This includes CNC machines, milling machines, and other tools that are essential for achieving the required precision in large part machining.
What’s the real story? Communication is just as important. A machining service that is responsive and willing to work closely with you to understand your needs and project requirements can ensure a smoother process from start to finish. Clear communication also ensures that any issues or concerns are addressed promptly, minimizing delays and errors.
Finally, pricing and lead times should also be considered. While cost shouldn’t be the only deciding factor, it is important to find a service provider that offers competitive pricing without compromising on quality. Make sure the lead times are reasonable and that the service provider can meet your deadlines.
Table 15: Key Factors in Choosing a Machining Service for Large Parts
Factor | Importance | Consideration |
---|---|---|
Experience with large parts | Ensures expertise in handling large components | Look for proven track record |
Equipment and capabilities | Determines the quality and precision of work | Verify equipment specifications |
Communication | Ensures smooth project execution | Choose a provider with responsive communication |
Pricing and lead times | Affects budget and delivery timelines | Compare quotes and delivery schedules |
Reputation and reviews | Indicates reliability and service quality | Check references and customer feedback |

Soalan Lazim
S1: What is large part machining?
Large part machining refers to the process of machining large components or parts that require specialized equipment and techniques to produce with high precision.
S2: How does CNC machining work for large parts?
CNC machining uses computer-controlled machines to precisely cut, shape, and finish large parts by following specific designs and measurements.
S3: What materials are best for large part machining?
Common materials for large part machining include metals like steel, aluminum, and titanium, as well as specialized non-metals based on the project requirements.
S4: What are the challenges in machining large parts?
The challenges include handling the size and weight of large parts, achieving precision, managing heat generation, and using specialized tools and machinery.
S5: How can I reduce costs in large part machining?
To reduce costs, focus on efficient tool usage, minimize material waste, optimize machine time, and carefully plan machining operations to reduce downtime.