Invoering
Nylon CNC machining is an essential process for many industries that require precise, durable, and lightweight parts. In this article, we’ll cover everything you need to know about nylon CNC machining, including its benefits, challenges, and how to optimize the process. Whether you’re a manufacturer, engineer, or just curious about the machining world, this guide will provide you with the knowledge to understand and utilize this technology effectively. Let’s dive in!
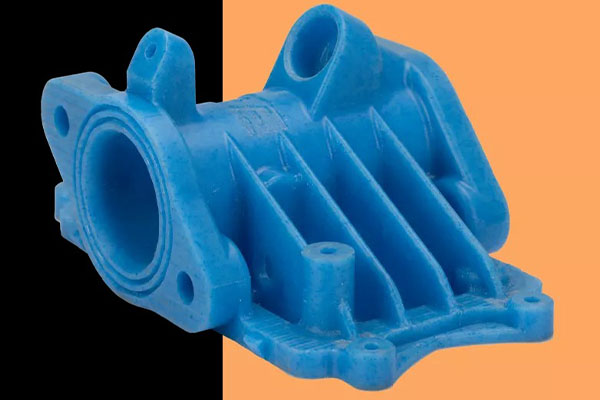
1. What is Nylon CNC Machining?
When it comes to CNC machining, nylon is a highly popular material due to its versatility, strength, and durability. What exactly is nylon CNC machining? Well, it’s the process of using Computer Numerical Control (CNC) machines to cut, shape, and finish parts made from nylon. This material is widely used in various applications, from automotive components to medical devices, thanks to its strength-to-weight ratio and resistance to wear.
But here’s the kicker—nylon is not just any plastic. It’s a synthetic polymer that has the ability to absorb impact, making it perfect for parts that need to withstand stress. As a machining material, nylon offers several advantages: it’s easy to machine, affordable, and can be customized to fit specific needs. It’s also resistant to chemicals, moisture, and certain environmental factors. These properties make it ideal for CNC machining in industries like aerospace, automotive, and medical manufacturing.
If you’re thinking about machining nylon parts for your next project, keep in mind that there are various types of nylon, such as nylon 6, nylon 66, and others. Each type has different characteristics, making some more suitable for certain applications than others.
Let’s break it down a bit further to understand how this process works.
2. Why is Nylon Used in CNC Machining?
You might be wondering, why is nylon so popular in CNC machining? The answer lies in its exceptional properties. Nylon is known for its strength, flexibility, and resistance to wear and tear, making it perfect for parts that need to endure high stress. Plus, it’s lightweight, which is crucial in industries like automotive and aerospace, where weight savings can lead to better performance and fuel efficiency.
Now, let’s talk specifics. When it comes to CNC machining, nylon stands out due to its ability to be easily molded and shaped without losing its strength or durability. This is important in industries that require high-precision parts, such as medical devices, where even the smallest mistake can lead to catastrophic results.
One of the key benefits of using nylon in CNC machining is its high chemical resistance. For parts that need to withstand exposure to oils, solvents, or other harsh chemicals, nylon provides an excellent solution. Whether you’re manufacturing gears, bearings, or any other component that needs to operate in tough environments, nylon ensures longevity and reliability.
But here’s the real story: nylon also has great impact resistance. This makes it a popular choice for industries that require parts that will endure repetitive stresses, like the automotive industry, where components like gears and bushings are constantly in motion. So, when you need a material that can take a hit and keep performing, nylon is often the go-to choice.
3. How Does Nylon CNC Machining Work?
So, you’re probably asking yourself, how does the actual process of machining nylon work? Well, it’s quite similar to other types of CNC machining. The primary difference lies in how nylon behaves under cutting conditions. It’s important to set the machine up properly to prevent any deformation during the process.
Here’s how it works: first, the nylon material is placed into a CNC machine, which is controlled by a computer to ensure precision. The machine uses various cutting tools—like end mills, drills, and lathes—to remove material from the nylon block to create the desired shape. It’s a highly accurate process, capable of producing parts with very tight tolerances.
Klaar voor het goede gedeelte? Nylon can be machined in several ways. For instance, drilling and milling are common techniques used to shape the material, depending on the type of part being produced. The CNC machine uses precise commands to ensure each cut is accurate and that the final product meets exact specifications. But since nylon is a relatively soft material, it requires specialized tools and settings to avoid issues like warping or overheating. These are things you need to consider when setting up your machine.
If you’ve been thinking about using nylon for your next CNC machining project, understanding these steps is crucial. This is where it gets interesting: choosing the right cutting tools and settings can make or break the quality of your parts. Now, let’s look at how you can ensure quality in the process.
4. What are the Benefits of Nylon CNC Machining?
You may be asking, what are the key benefits of choosing nylon for CNC machining? Let’s dive into the details. One of the most significant advantages of nylon CNC machining is its sterkte-gewichtsverhouding. Nylon parts are both strong and lightweight, which is ideal for applications where reducing weight is essential, such as in aerospace or automotive industries. This allows for greater fuel efficiency, improved performance, and less strain on other components.
But here’s the kicker—nylon is also incredibly resistant to wear and tear. Over time, parts made from nylon will maintain their shape and function, even under harsh conditions. For example, gears and bushings made from nylon can last significantly longer than those made from metals or other materials that may wear down quicker. This is why nylon is often the material of choice for moving parts in machinery.
Another benefit of nylon CNC machining is its chemical resistance. Parts made from nylon are able to withstand exposure to oils, solvents, and other chemicals without degrading. This makes it an ideal material for manufacturing parts that will be used in environments where exposure to harsh chemicals is common, such as in the oil and gas industry.
What’s the real story? In short, nylon CNC machining provides durability, strength, and versatility, making it a valuable option for a wide range of applications. Whether you need lightweight parts or durable components for heavy-duty use, nylon is an excellent choice. But it’s not without its challenges, which brings us to the next section.
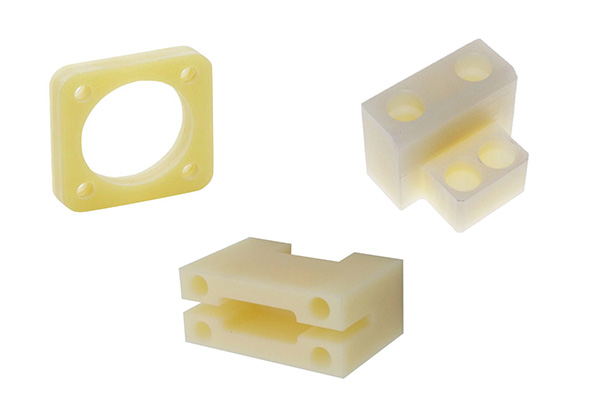
5. What are the Challenges of Nylon CNC Machining?
Despite its many benefits, nylon CNC machining isn’t without its challenges. You might be wondering, what are the main obstacles when machining nylon? Well, there are a few things you should keep in mind to ensure optimal results.
First, nylon can be prone to warping when it’s heated during machining. This can be problematic, especially when you’re working with intricate designs or when tight tolerances are required. To avoid this issue, it’s essential to manage the temperature carefully during the process. Using tools that can minimize friction and heat build-up, like carbide cutting tools, can also help prevent warping.
Een andere uitdaging is gereedschapsslijtage. While nylon is relatively easy to machine, it can be abrasive on the cutting tools over time. This means that frequent tool changes might be necessary to maintain precision and quality. Choosing the right tools and cutting parameters can significantly reduce this issue.
Now, here’s the real kicker—finding the right balance between speed and precision can be tricky. If the cutting speed is too high, it could cause the material to melt or deform. On the other hand, too slow a speed could lead to inefficient machining, which can drive up production costs. Properly balancing these factors is essential for a successful nylon CNC machining project.
6. How to Choose the Right CNC Machine for Nylon?
So, how do you choose the best CNC machine for machining nylon? The right CNC machine is critical for producing high-quality nylon parts, and there are several factors you need to consider.
First, you’ll want to look for a machine with precise control. Since nylon machining often requires tight tolerances, having a CNC machine that can offer fine adjustments is essential. Machines with advanced software and control systems are ideal for ensuring accuracy in the machining process.
But here’s where it gets interesting—machine type matters! For instance, if you’re producing complex parts, you may need a multi-axis CNC machine. These machines can move the cutting tools in multiple directions, allowing for more intricate designs and shapes. On the other hand, if you’re working on simpler parts, a 3-axis machine might be sufficient.
Klaar voor het goede gedeelte? You should also consider the power of the machine and its cutting capacity. Some CNC machines may not be powerful enough to handle thicker or tougher nylon grades, so it’s important to match the machine’s specifications to the type of nylon you plan to use. By carefully selecting a machine that meets these requirements, you can ensure that your machining process is smooth and efficient.
7. How to Optimize Nylon CNC Machining for Efficiency?
When it comes to CNC machining, efficiency is key. So, how can you optimize the process when machining nylon? There are several strategies that can help you increase productivity and reduce costs.
One of the best ways to optimize nylon CNC machining is by choosing the right cutting tools. High-quality, sharp tools will reduce friction, prevent overheating, and ensure that you get precise cuts every time. Another key factor is the cutting speed—setting the optimal speed for nylon can help avoid problems like melting or warping, while also speeding up the machining process.
What’s the real story? Efficient tool management is also essential. Regular tool maintenance, such as cleaning and sharpening, ensures consistent performance and longer tool life. By keeping tools in top condition, you reduce the chances of errors and delays during the machining process.
To further boost efficiency, it’s essential to minimize material waste. With nylon, you can optimize the cutting path and nesting patterns to make sure you’re getting the most out of your material. Using CAD/CAM software to plan cuts is an excellent way to reduce waste and improve production times.
8. What are the Types of Nylon Used in CNC Machining?
When it comes to choosing nylon for CNC machining, you may be wondering: What types of nylon are best suited for machining? Nylon comes in various types, each with its own unique properties. Let’s break down some of the most common types used in CNC machining.
The two most common types are nylon 6 En nylon 66. Nylon 6 is known for its high flexibility and ease of processing, making it ideal for applications like bushings, gears, and bearings. Nylon 66, on the other hand, offers superior strength and heat resistance, making it ideal for parts that will be exposed to high temperatures or heavy stress.
But here’s the kicker—there are also specialized nylons, like glass-filled nylon, which is reinforced with glass fibers to provide increased strength and rigidity. This type of nylon is used in applications where higher performance is required, such as in automotive and aerospace components.
Understanding the differences between these types of nylon will help you choose the best material for your specific CNC machining needs. Whether you need flexibility, strength, or heat resistance, there’s a type of nylon suited for every application.
9. What Industries Use Nylon CNC Machining?
Nylon CNC machining is widely used across various industries, and each sector benefits from its unique properties. Which industries rely on nylon CNC machining the most? Let’s take a closer look.
First, the automotive industry uses nylon for components like gears, bushings, and engine parts due to its strength, heat resistance, and lightweight properties. Nylon parts help improve fuel efficiency and performance while reducing overall vehicle weight.
In the aerospace industry, nylon is used for components that require both strength and weight reduction, such as gears and bearings. Nylon CNC machining allows for the production of highly durable parts that can withstand extreme conditions without adding unnecessary weight.
The medical industry also makes use of nylon for CNC machining, particularly in applications where precision and strength are crucial. Parts like prosthetics, medical devices, and surgical tools benefit from nylon’s durability and biocompatibility.
What’s the real story? Nylon CNC machining plays a pivotal role in ensuring that components across various industries are durable, lightweight, and functional. Each sector can take advantage of nylon’s versatility to meet their unique requirements.
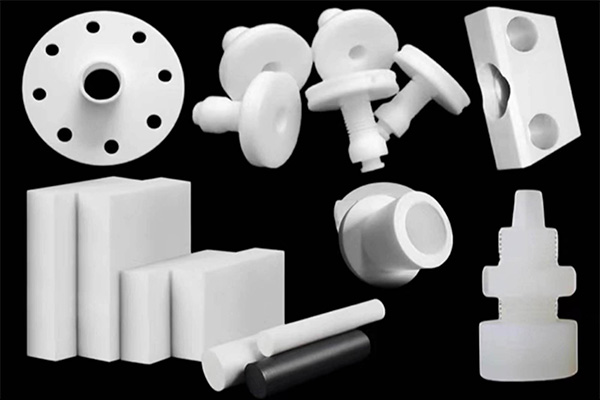
10. How to Care for and Maintain Nylon CNC Machined Parts?
Maintaining the quality of your nylon CNC machined parts is essential to ensure longevity and optimal performance. So, how do you care for these parts? First, it’s important to clean nylon parts regularly to prevent the buildup of dirt, dust, or other contaminants. Cleaning with a mild detergent and warm water will suffice—just be sure to dry the parts thoroughly afterward.
Here’s where it gets interesting—proper storage is just as important. Keep your nylon parts in a cool, dry place to prevent them from absorbing moisture, which could affect their strength and performance. Additionally, you should inspect parts regularly for wear and tear, especially if they are used in high-stress environments.
Lastly, protect your nylon parts from extreme temperatures. Excessive heat or cold can weaken the material, so it’s important to ensure that parts are stored and used within the recommended temperature range for nylon.
11. Can Nylon CNC Machining Be Used for Prototyping?
Absolutely! Nylon CNC machining is an excellent choice for prototyping. Why? Because it allows manufacturers to produce durable, functional parts quickly and affordably. What’s the real story? Prototyping with nylon gives designers the flexibility to test and iterate on their designs before moving to mass production. Plus, the rapid turnaround time means faster product development and reduced time to market.
Nylon is ideal for prototypes because it offers a good balance of strength, durability, and cost-effectiveness. In fact, many industries, including automotive and medical device manufacturing, use nylon for prototypes to ensure the part will perform well before committing to the final production process.
12. What Are the Environmental Considerations for Nylon CNC Machining?
In today’s world, environmental sustainability is a priority for many manufacturers. So, what are the environmental considerations when machining nylon? Nylon is a non-biodegradable material, meaning it can have a long-term impact if not disposed of properly. However, the good news is that nylon can be recycled, and many manufacturers have adopted more sustainable practices, such as recycling scrap nylon and reusing it in production.
But here’s where it gets interesting— the impact of machining on the environment can be minimized through the use of cleaner machining processes. For example, using less harmful cutting fluids and energy-efficient CNC machines can help reduce the carbon footprint of nylon CNC machining.
13. What Are the Costs Involved in Nylon CNC Machining?
How much does it cost to machine nylon? The cost of nylon CNC machining depends on several factors, including the type of nylon being used, the complexity of the part, and the volume of production. But here’s the kicker— generally speaking, nylon is an affordable material to machine, especially compared to metals like aluminum or steel. This is one of the reasons why nylon is so popular in CNC machining.
To get a more accurate cost estimate, you’ll need to factor in other costs, such as labor, machine operation, and raw material prices. High-volume production can lower the cost per part, making it more affordable overall. In addition, optimizing your machining process can help save costs by reducing waste and increasing efficiency.
14. How Do You Ensure Quality Control in Nylon CNC Machining?
Quality control is essential in CNC machining, and nylon parts are no exception. So, how do you ensure that your nylon parts meet high standards? First, it’s crucial to inspect parts during and after the machining process. This can be done through visual inspections, as well as using measuring tools like calipers or coordinate measuring machines (CMM) to verify dimensions.
What’s the real story? Ensuring quality in nylon CNC machining also involves maintaining strict tolerances and using the proper cutting tools and machine settings. By paying attention to these details, you can produce parts that meet your quality standards and reduce the risk of defects.
15. What is the Future of Nylon CNC Machining?
So, what does the future hold for nylon CNC machining? As technology continues to evolve, so does the ability to machine nylon more efficiently and precisely. Klaar voor het goede gedeelte? The development of advanced CNC machines and cutting tools means that nylon machining will only become more cost-effective and capable of producing more complex parts.
The future of nylon CNC machining looks bright, with innovations in materials and processes that will improve performance and sustainability. Here’s where it gets interesting— we can expect to see even more widespread use of nylon in industries like aerospace, automotive, and medical manufacturing, as the demand for lightweight, durable parts continues to grow.
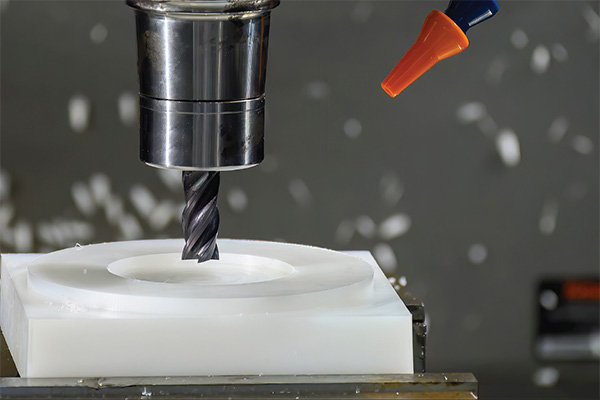
FAQ-sectie
Q1: What is Nylon CNC Machining?
Nylon CNC machining is a process where computer-controlled machines are used to cut and shape parts made from nylon, a durable, lightweight material. This technique is used in various industries for creating high-precision parts.
Q2: How does Nylon CNC Machining work?
The process involves feeding a block of nylon into a CNC machine, which uses a cutting tool to remove material and create the desired shape. The machine follows precise, pre-programmed instructions to ensure accuracy and efficiency.
Q3: Why is nylon a popular material for CNC machining?
Nylon is popular because of its strength, flexibility, and resistance to wear and chemicals. It’s also lightweight and affordable, making it suitable for a wide range of applications.
Q4: What are the main challenges when machining nylon?
Challenges include managing heat to prevent warping, tool wear, and finding the right balance between speed and precision. Proper machine setup and tool selection are essential for success.
Q5: Can nylon parts be used for prototyping?
Yes, nylon is an excellent choice for prototyping due to its durability, ease of machining, and cost-effectiveness. It allows manufacturers to test and refine designs before moving to full-scale production.