1. Introduction to CNC Milling
Computer Numerical Control (CNC) milling has revolutionized the manufacturing industry by introducing unparalleled precision and automation to the machining process. At its core, CNC-frezen is a subtractive manufacturing technique where material is removed from a workpiece using rotating cutting tools, guided by computer-generated code. This method allows for the creation of complex and intricate parts that would be challenging, if not impossible, to produce manually. The evolution from manual milling to CNC technology has not only increased production efficiency but also enhanced the consistency and quality of manufactured components. By automating the control of machining tools through computer software, CNC milling minimizes human error and ensures that each part adheres to exact specifications. This precision is crucial in industries where even the slightest deviation can lead to significant issues, such as aerospace, medical device manufacturing, and automotive sectors. Moreover, the adaptability of CNC milling machines to work with a wide range of materials—including metals, plastics, and composites—further underscores their significance in modern manufacturing. As we delve deeper into the intricacies of CNC milling, we will explore its operational mechanisms, the various types of machines utilized, and the diverse applications that benefit from this advanced technology.
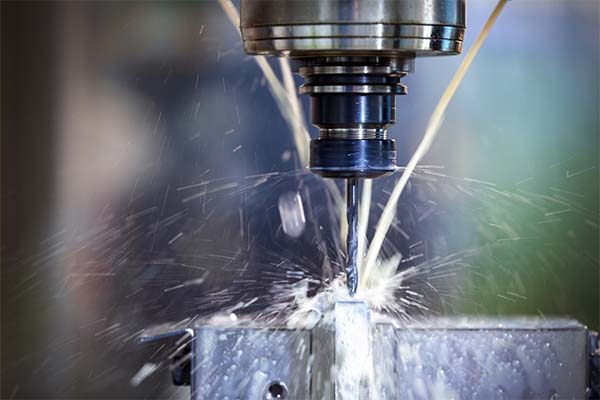
2. How CNC Milling Works
The CNC milling process is a harmonious blend of software precision and mechanical execution. It begins with the creation of a detailed 3D model of the desired part using Computer-Aided Design (CAD) software. This digital model serves as the blueprint, encapsulating all the geometric features and dimensions required. Once the design is finalized, it is imported into Computer-Aided Manufacturing (CAM) software, which translates the model into a series of precise instructions known as G-code. This code dictates the movements of the milling machine, specifying parameters such as tool paths, spindle speeds, feed rates, and depth of cuts. The CNC milling machine, equipped with a variety of cutting tools, then executes these instructions. The workpiece is securely fixed onto the machine’s worktable, and the cutting tool, mounted on a spindle, rotates at high speeds to remove material in a controlled manner. The machine’s ability to move the tool and/or the workpiece along multiple axes—commonly three (X, Y, and Z), but sometimes more in advanced machines—enables the creation of complex geometries and intricate features. Throughout the process, feedback systems monitor the machine’s operations, ensuring adherence to the programmed parameters and allowing for real-time adjustments to maintain accuracy. This closed-loop system is fundamental to achieving the high precision and repeatability that CNC milling is renowned for. By automating the machining process, CNC milling not only enhances efficiency but also significantly reduces the likelihood of human error, leading to consistent production of high-quality parts.
3. Types of CNC Milling Machines
CNC milling machines are diverse, each designed to cater to specific manufacturing needs. The primary classification is based on the orientation of the spindle and the number of axes of movement. Vertical milling machines feature a vertically oriented spindle, allowing for easy access to the workpiece and making them suitable for tasks like face milling and drilling. Horizontal milling machines, with a horizontally oriented spindle, are ideal for cutting deep grooves and slots, as well as for heavy material removal. Beyond these, there are universal milling machines that combine features of both vertical and horizontal machines, offering greater flexibility. The number of axes also plays a crucial role in defining a machine’s capabilities. Three-axis machines move the tool along the X, Y, and Z axes, suitable for most simple milling tasks. Four-axis machines add rotation around the X-axis, allowing for more complex operations like engraving curved surfaces. Five-axis machines, which can rotate around both the X and Y axes, enable the creation of intricate parts with complex geometries, reducing the need for multiple setups and increasing precision. Selecting the appropriate type of CNC milling machine depends on factors such as the complexity of the part design, material properties, production volume, and specific tolerances required. Understanding these machine types and their applications is essential for optimizing manufacturing processes and achieving desired outcomes.
4. Key Components of CNC Milling Machines
A CNC milling machine comprises several critical components that work in unison to execute precise machining tasks. The spindle, often considered the heart of the machine, holds and rotates the cutting tool at varying speeds, dictated by the material and specific operation. The worktable provides a stable platform to secure the workpiece, with some tables offering movement along different axes to facilitate complex machining. Linear guides and ball screws ensure smooth and accurate movement of the machine components, translating the programmed instructions into precise physical motions. The control panel serves as the user interface, allowing operators to input commands, monitor operations, and make necessary adjustments. Modern CNC machines are also equipped with automatic tool changers, enabling swift transitions between different cutting tools, thereby enhancing efficiency and reducing downtime. Additionally, feedback systems, such as encoders and sensors, continuously monitor the machine’s performance, ensuring that deviations from the desired parameters are promptly corrected. Understanding these components and their functions is vital for effective machine operation, maintenance, and troubleshooting, ultimately contributing to the production of high-quality machined parts.
5. Materials Suitable for CNC Milling
CNC milling is versatile, accommodating a wide range of materials to meet diverse manufacturing requirements. Metals such as aluminum, known for its machinability and strength-to-weight ratio, are commonly milled to produce components for the aerospace and automotive industries. Steel, including its various alloys, is favored for parts requiring high strength and durability, while brass and copper are selected for their excellent electrical conductivity and corrosion resistance. Plastics like ABS, polycarbonate, and nylon are also frequently machined, offering lightweight solutions with good chemical resistance for applications in consumer electronics and medical devices. Advanced composites and engineered materials are increasingly being milled to leverage their unique properties for specialized applications. The choice of material impacts not only the functionality of the final product but also influences machining parameters such as cutting speed, feed rate, and tool selection. Therefore, a thorough understanding of material properties is essential to optimize the CNC milling process, ensuring efficiency and the production of parts that meet stringent quality standards.
6. Advantages of CNC Milling
CNC milling offers numerous advantages that have solidified its position as a cornerstone in modern manufacturing. One of the most significant benefits is its unparalleled precision and accuracy. By utilizing computer-controlled movements, CNC milling machines can produce components with extremely tight tolerances, ensuring consistency across large production runs. This level of precision is particularly crucial in industries such as aerospace and medical devices, where even minor deviations can have serious implications.
Another notable advantage is the efficiency and speed of CNC milling. Traditional manual milling requires significant time and labor, with each part demanding individual attention. In contrast, CNC milling can operate continuously, producing parts at a much faster rate without compromising quality. The automation of the process reduces the likelihood of human error, leading to higher productivity and lower rejection rates.
Flexibility is also a key strength of CNC milling. With the ability to quickly reprogram machines for different tasks, manufacturers can easily switch between producing various components. This adaptability is essential in today’s market, where customization and rapid prototyping are in high demand. Moreover, CNC milling machines can work with a wide range of materials, including metals, plastics, and composites, broadening their application scope.
Cost-effectiveness is another critical advantage. While the initial investment in CNC machinery can be substantial, the long-term savings are significant. The reduction in manual labor, decreased material waste due to precise machining, and lower error rates contribute to overall cost reductions. Additionally, the scalability of CNC milling allows manufacturers to meet varying production demands without incurring excessive costs.
In summary, the precision, efficiency, flexibility, and cost-effectiveness of CNC milling make it an indispensable tool in the manufacturing industry, enabling the production of high-quality components that meet stringent standards.
7. Common Applications of CNC Milling
CNC milling’s versatility has led to its widespread adoption across various industries, each leveraging its capabilities to meet specific needs. In the aerospace sector, CNC milling is employed to manufacture complex components such as turbine blades, structural parts, and intricate housings. The high precision and ability to work with advanced materials ensure that the stringent safety and performance standards of the aerospace industry are met.
The automotive industry also benefits significantly from CNC milling. Engine components, transmission parts, and custom prototypes are efficiently produced using CNC machines. The technology allows for rapid production cycles and the flexibility to adapt to design changes, which is essential in the fast-paced automotive market.
In the medical field, CNC milling is crucial for creating precision instruments, implants, and prosthetics. The ability to produce parts with complex geometries and fine details ensures that medical devices meet the necessary standards for functionality and biocompatibility. Moreover, the repeatability of CNC milling processes guarantees consistency in mass-produced medical components.
The electronics industry utilizes CNC milling to fabricate components like heat sinks, enclosures, and connectors. The precision machining capabilities allow for the production of parts with tight tolerances, essential for the proper functioning of electronic devices. Additionally, the adaptability of CNC milling machines enables manufacturers to keep up with the rapid advancements in electronic product designs.
Beyond these industries, CNC milling is employed in the production of custom parts, molds, and tooling for various manufacturing processes. Its ability to handle diverse materials and produce complex shapes makes it a valuable asset in both mass production and specialized, low-volume manufacturing scenarios.
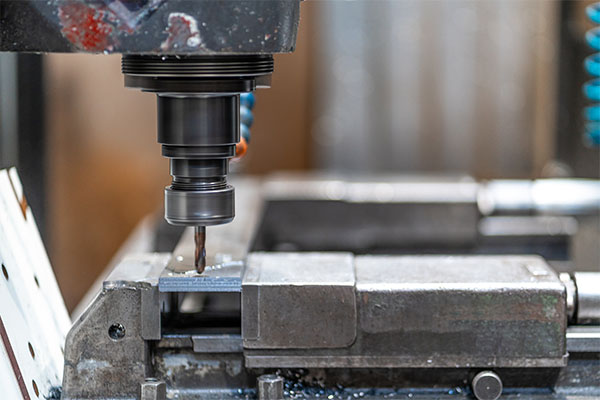
8. Challenges and Considerations in CNC Milling
Despite its numerous advantages, CNC milling presents certain challenges that manufacturers must address to optimize operations. One primary consideration is the initial capital investment required for CNC machinery. High-quality CNC machines can be expensive, and the costs extend beyond the purchase price to include expenses related to setup, maintenance, and necessary software. For small and medium-sized enterprises, this financial barrier can be significant.
Another challenge is the need for skilled personnel to operate and maintain CNC machines. While CNC technology automates many aspects of the machining process, knowledgeable operators are essential for programming, troubleshooting, and ensuring optimal performance. The shortage of skilled labor in the manufacturing sector can make it difficult to find qualified individuals, necessitating investment in training and development programs.
Material-specific challenges also arise in CNC milling. Different materials exhibit varying properties, such as hardness, tensile strength, and thermal conductivity, which can affect machinability. Selecting appropriate cutting tools, speeds, and feeds for each material is crucial to prevent issues like tool wear, poor surface finish, or dimensional inaccuracies. Manufacturers must thoroughly understand material characteristics to optimize machining parameters effectively.
Design considerations play a role in the effectiveness of CNC-frezen. Complex geometries or features with difficult-to-reach areas may require specialized tooling or machine configurations, potentially increasing production time and costs. Collaborative efforts between designers and machinists during the design phase can help identify potential issues and implement design for manufacturability (DFM) principles to streamline production.
In conclusion, while CNC milling offers substantial benefits, addressing these challenges through strategic planning, investment in technology and human resources, and effective collaboration can enhance the efficiency and effectiveness of CNC milling operations.
9. Future Trends in CNC Milling
The landscape of CNC milling is undergoing significant transformations, driven by technological advancements and evolving industry demands. One prominent trend is the integration of Artificial Intelligence (AI) and Machine Learning (ML) into CNC systems. AI-driven CNC systems are becoming more common, enabling real-time decision-making and predictive maintenance. These advancements reduce downtime, optimize tool life, and enhance machining precision by learning and adapting to production environments.
Another significant development is the rise of hybrid manufacturing, which combines additive and subtractive processes within a single machine. This integration allows for greater design flexibility, material efficiency, and the ability to produce complex geometries that were previously challenging or impossible to achieve. Hybrid machines can add material through additive manufacturing techniques and then refine the part with subtractive processes, streamlining production workflows.
Automation and robotics are also playing a crucial role in the evolution of CNC milling. The integration of automation and robotics is set to transform CNC machining significantly. Automated systems are becoming standard in many facilities, enabling machines to operate 24/7 without constant human oversight. This shift not only increases production capacity but also reduces labor costs and minimizes human error.
The focus on duurzaamheid is influencing CNC milling practices as well. Manufacturers are adopting eco-friendly approaches, such as using energy-efficient machines, recycling coolants, and minimizing material waste. These practices not only reduce environmental impact but also align with global sustainability goals and can lead to cost savings in the long run.
In summary, the future of CNC milling is being shaped by advancements in AI and machine learning, the adoption of hybrid manufacturing, increased automation, and a commitment to sustainability. These trends are set to enhance the efficiency, precision, and adaptability of CNC milling operations in the coming years.
10. Conclusion
CNC milling has firmly established itself as a cornerstone of modern manufacturing, offering unparalleled precision, efficiency, and versatility. From its fundamental principles to the latest technological advancements, CNC milling continues to evolve, meeting the diverse needs of industries worldwide. The integration of AI, automation, and sustainable practices signifies a promising future, where CNC milling will play an even more critical role in driving innovation and productivity. As manufacturers embrace these emerging trends, the potential for CNC milling to contribute to complex, high-quality, and cost-effective production processes is boundless. Staying informed and adaptable to these changes will be key to leveraging the full capabilities of CNC milling in the years to come.
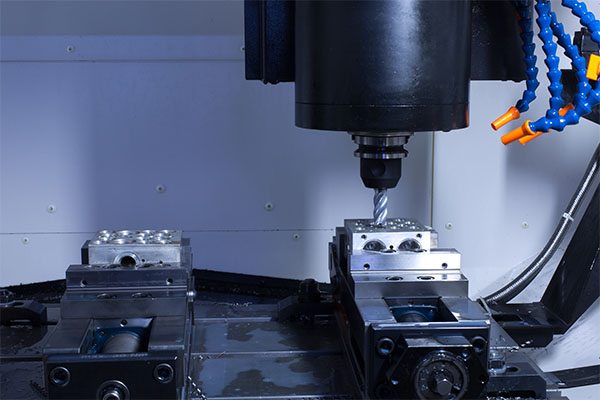
(FAQs) about CNC milling
1. What is CNC Milling?
CNC (Computer Numerical Control) milling is a subtractive manufacturing process that utilizes computer-controlled machines to remove material from a workpiece, shaping it into a desired form. The process involves a rotating cutting tool mounted on a spindle, which moves along multiple axes to carve out the specified geometry from materials such as metals, plastics, or composites. The precision and automation of CNC milling make it ideal for producing complex parts with high accuracy and repeatability.
2. How Does CNC Milling Differ from CNC Turning?
While both CNC-frezen and CNC turning are machining processes controlled by computer numerical inputs, they differ in operation and applications. In CNC milling, the cutting tool rotates and moves along multiple axes, while the workpiece remains stationary or moves in a controlled manner. Conversely, CNC turning involves rotating the workpiece on its axis while a stationary cutting tool shapes it. Milling is typically used for creating complex shapes and features, whereas turning is ideal for producing cylindrical parts.
3. What Materials Can Be Processed Using CNC Milling?
CNC milling is versatile and can process a wide range of materials, including:
- Metals: Aluminum, steel, brass, copper, titanium, and various alloys.
- Plastics: ABS, polycarbonate, nylon, PEEK, and others.
- Composites: Fiberglass, carbon fiber-reinforced polymers, and more.
The selection of material depends on the specific requirements of the part, such as mechanical properties, surface finish, and application environment.
4. What Are the Common Types of CNC Milling Machines?
CNC milling machines are categorized based on their configuration and the number of axes they operate along:
- Vertical Milling Machines: Feature a vertically oriented spindle, suitable for operations like face milling and end milling.
- Horizontal Milling Machines: Have a horizontally oriented spindle, ideal for cutting slots and grooves.
- 3-Axis Machines: Move the cutting tool along the X, Y, and Z axes.
- 4-Axis Machines: Add rotation around the X-axis, allowing for more complex geometries.
- 5-Axis Machines: Include rotation around both the X and Y axes, enabling the creation of intricate parts without repositioning the workpiece.
The choice of machine depends on the complexity of the part and the specific machining requirements.
5. What Are the Advantages of CNC Milling?
CNC milling offers several benefits, including:
- High Precision and Accuracy: Computer control ensures consistent production of parts within tight tolerances.
- Repeatability: Once a program is set, identical parts can be produced with minimal variation.
- Flexibility: Easy reprogramming allows for quick changes in design and production of different parts.
- Efficiency: Automation reduces manual intervention, increasing production speed and reducing errors.
- Complex Geometry: Capable of producing intricate designs that would be challenging with manual machining.
These advantages make CNC milling a preferred choice in industries requiring high-quality and precise components.
6. What Are Common Applications of CNC Milling?
CNC milling is utilized across various industries for applications such as:
- Aerospace: Manufacturing of structural components and engine parts.
- Automotive: Production of engine blocks, transmission housings, and custom parts.
- Medical Devices: Creation of surgical instruments, implants, and prosthetics.
- Electronics: Fabrication of enclosures, heat sinks, and connectors.
- Industrial Equipment: Machining of gears, brackets, and machinery components.
The versatility of CNC milling allows it to meet the diverse needs of these sectors.
7. What Factors Influence the Quality of CNC Milled Parts?
Several factors affect the quality of parts produced through CNC milling:
- Tool Selection: Choosing the appropriate cutting tool material and geometry for the material being machined.
- Cutting Parameters: Optimizing spindle speed, feed rate, and depth of cut to suit the material and desired finish.
- Machine Condition: Regular maintenance to ensure accuracy and prevent mechanical issues.
- Workpiece Fixturing: Securely holding the workpiece to prevent movement during machining.
- Programming Accuracy: Precise programming of tool paths to avoid errors and ensure dimensional accuracy.
Attention to these factors is essential for achieving high-quality CNC milled parts.
8. How Does CNC Milling Compare to Additive Manufacturing?
CNC milling and additive manufacturing (AM) are both methods of creating parts but differ fundamentally:
- Process: CNC milling is subtractive, removing material to form the part, while AM is additive, building the part layer by layer.
- Material Waste: Milling generates more waste due to material removal; AM is more material-efficient.
- Surface Finish: CNC milling typically achieves better surface finishes without additional processing.
- Material Options: Milling can handle a wider range of materials, including metals and plastics, with established properties.
- Complexity: AM excels at producing complex geometries with internal features difficult to achieve with milling.
The choice between the two depends on factors like design complexity, material requirements, production volume, and cost considerations.
These FAQs provide a comprehensive understanding of CNC milling, covering its principles, advantages, applications, and considerations.