Invoering
The world of CNC (Computer Numerical Control) machining has undergone remarkable transformations in recent years. These innovations have reshaped the manufacturing landscape, providing industries with cutting-edge solutions to improve precision, efficiency, and overall performance. In this article, we will explore some of the latest CNC innovations that are revolutionizing the machining process. We’ll take a deep dive into how these advancements are pushing the boundaries of what’s possible and why they matter to modern manufacturing.
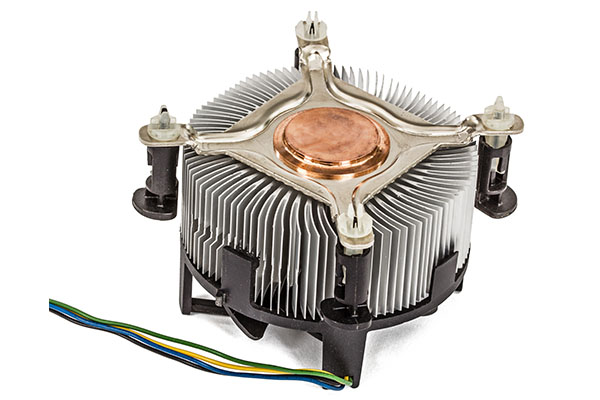
1. What Are the Latest CNC Innovations?
CNC machining has come a long way since its inception. What was once a manual and highly complex process has evolved into a streamlined, automated system with advanced features that make it more efficient, precise, and versatile. But here’s the kicker: the rate at which these innovations are being introduced is faster than ever.
Recent CNC innovations include AI-powered systems, IoT-enabled machines, and the integration of robotics to optimize the manufacturing process. For instance, CNC machines now come equipped with real-time data monitoring systems, allowing operators to track machine performance and anticipate maintenance needs before breakdowns occur. This predictive maintenance not only saves time but also ensures machines are running at their optimal capacity.
In addition, some new CNC machines now feature autonomous capabilities. These machines can perform tasks with little human intervention, which significantly reduces labor costs and the potential for human error. Manufacturers are also integrating 3D printing technology with CNC to enable the creation of more intricate parts and components that were once considered too complex or time-consuming to produce.
The key takeaway? New CNC innovations aren’t just about improving existing functions—they are creating entirely new possibilities for the machining industry.
Table 1: Comparison of Traditional vs. New CNC Innovations
Feature | Traditional CNC Machines | New CNC Innovations |
---|---|---|
Automatisering | Limited | High Automation |
Data Monitoring | Manual | Real-Time Monitoring |
Maintenance | Reactive | Predictive |
Machine Intervention | High | Low |
Integration with Robotics | Not Common | Common |
2. How Are New CNC Technologies Transforming Manufacturing?
New CNC technologies are not just improving the machines themselves; they are transforming the entire manufacturing process. Ready for the good part? These innovations are leading to faster production cycles, lower costs, and higher-quality products. Let’s explore how.
One of the biggest transformations is the integration of artificial intelligence (AI) into CNC machining. AI-driven algorithms can analyze machine performance and make adjustments on the fly, optimizing settings for speed, accuracy, and efficiency. This results in faster production times and a reduction in scrap materials. Manufacturers can now create highly intricate parts in less time, while also improving the overall quality.
What’s more, CNC machines equipped with IoT sensors provide a level of connectivity that enables real-time communication between the machine and the operator. This data can be used for immediate adjustments or predictive maintenance, helping to avoid costly downtime and repairs.
In the past, CNC machines were limited to one task at a time, but now, machines can perform multi-tasking operations, such as milling, turning, and drilling in a single setup. This reduces the need for multiple machines, saving both space and money in the long run.
Table 2: Key Benefits of New CNC Technologies
Voordeel | Beschrijving |
---|---|
Faster Production | AI and IoT integration improve efficiency and speed. |
Reduced Costs | Multi-tasking capabilities save space and reduce setup times. |
Higher Precision | Real-time adjustments ensure better accuracy and lower error rates. |
Lower Downtime | Predictive maintenance minimizes unexpected breakdowns. |
3. What Are the Key Features of the Latest CNC Machines?
New CNC machines come equipped with a variety of advanced features that were once considered futuristic. But here’s where it gets interesting: these features are now becoming standard.
Take the increased use of robotics, for example. With CNC machines now integrated with robotic arms, manufacturers can automate the loading and unloading of parts. This reduces human intervention, speeds up production, and minimizes the chances of contamination or mistakes during part handling.
Another significant feature is the incorporation of advanced materials. The latest CNC machines are capable of machining a broader range of materials, including harder metals and composites that were previously difficult to process. These materials allow manufacturers to create stronger, lighter, and more durable components, which is particularly important in industries like aerospace, automotive, and medical device manufacturing.
Moreover, the latest CNC machines often come with touch-screen interfaces and user-friendly controls. This allows for more intuitive programming, making the machines more accessible to operators who may not have a deep technical background.
Table 3: Top Features of the Latest CNC Machines
Feature | Beschrijving |
---|---|
Robotics Integration | Automates part handling for faster production cycles. |
Advanced Materials Support | Capable of machining hard metals and composites. |
Touch-Screen Interface | Provides a more intuitive and accessible user interface. |
Increased Automation | Reduces human error and enhances machine efficiency. |
4. How Do New CNC Innovations Improve Machining Accuracy?
Accuracy is the cornerstone of any CNC machine’s performance, and new innovations are pushing the boundaries of what’s possible. But here’s the kicker: these advancements are not only improving accuracy but also ensuring that errors are caught before they even happen.
One of the most notable developments is the use of laser and optical sensors for real-time measurement and adjustments. These sensors continuously monitor the part being produced and make automatic corrections to the machining process. This not only ensures that every part meets the specified dimensions but also significantly reduces the time spent on quality control checks.
Additionally, some of the latest CNC machines feature advanced software that can predict potential issues with machining accuracy based on real-time data. This predictive capability allows manufacturers to address problems before they impact the production process, ultimately saving time and money.
Finally, advancements in vibration-damping technology are also playing a role in improving accuracy. These systems reduce unwanted vibrations during machining, which can cause inaccuracies. By minimizing vibrations, these machines ensure that every cut is as precise as possible.
Table 4: Accuracy Improvement Features in New CNC Machines
Feature | Beschrijving |
---|---|
Laser and Optical Sensors | Continuously monitor and adjust for precision. |
Predictive Software | Prevents potential accuracy issues before they occur. |
Vibration-Damping Technology | Reduces vibrations to ensure precision during machining. |
5. What Role Does Artificial Intelligence Play in CNC Machines?
Artificial intelligence (AI) is making a significant impact on CNC machines. You might be wondering, how exactly does AI enhance CNC operations? Let’s break it down.
AI allows CNC machines to optimize their performance based on real-time data. For instance, AI can adjust machining parameters such as cutting speed and depth to maximize efficiency without compromising quality. This dynamic adjustment ensures that each job is completed as quickly as possible while maintaining the highest possible standards.
Additionally, AI-powered predictive maintenance is becoming increasingly common in modern CNC machines. By analyzing historical data and monitoring machine behavior, AI can predict when a part is likely to fail, allowing for preventive maintenance. This reduces the risk of unexpected downtime and helps businesses avoid costly repairs.
AI is also playing a key role in quality control. By analyzing data from various sensors and cameras, AI systems can detect defects in the production process that might be missed by human inspectors. This ensures that only parts meeting strict quality standards make it through the manufacturing process.
Table 5: AI Features in CNC Machines
Feature | Beschrijving |
---|---|
Dynamic Optimization | AI adjusts machining parameters for optimal efficiency. |
Predictive Maintenance | AI predicts failures before they occur, reducing downtime. |
Quality Control Automation | AI detects defects during production to ensure high quality. |
Conclusie
In conclusion, the latest CNC innovations are transforming the manufacturing industry in profound ways. From advanced materials and automation to the integration of artificial intelligence and robotics, these innovations are improving efficiency, precision, and cost-effectiveness. With the ability to produce complex parts faster and more accurately than ever before, CNC machines are opening new doors to what’s possible in manufacturing. As these technologies continue to evolve, the future of machining looks brighter than ever, offering manufacturers unprecedented opportunities to innovate and stay competitive in a rapidly changing market.
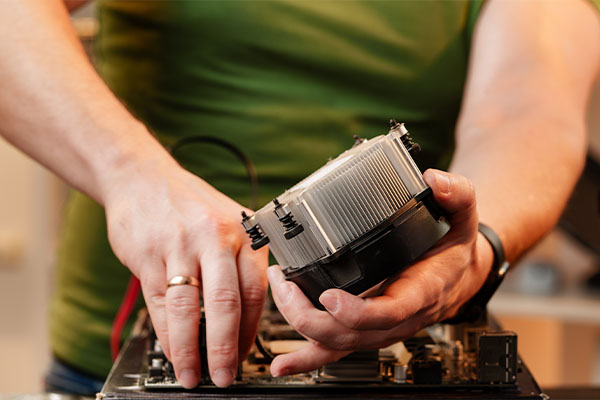
6. What Are the Benefits of CNC Machines with IoT Integration?
The Internet of Things (IoT) is revolutionizing the way CNC machines operate, providing manufacturers with the ability to monitor and manage their machines remotely. So, what’s the real story? IoT integration makes it possible to collect and analyze data in real-time, leading to better decision-making and improved performance.
One of the most significant advantages of IoT-enabled CNC machines is predictive maintenance. By continuously monitoring the machine’s condition and performance, IoT sensors can detect signs of wear and tear or malfunction before they cause a breakdown. This proactive approach reduces downtime and minimizes costly repairs, leading to a longer lifespan for the equipment.
Additionally, IoT integration allows operators to track performance data remotely, which means they can make adjustments to optimize the machining process without being physically present. This is particularly useful for manufacturers with large facilities or multiple production lines, as it reduces the need for constant on-site supervision.
IoT-enabled machines also offer enhanced efficiency. By tracking everything from cutting speed to material usage, manufacturers can identify areas for optimization and make data-driven decisions that improve overall productivity. Real-time feedback also allows operators to make adjustments on the fly, ensuring that production stays on schedule and that machines are running at peak performance.
Table 6: Benefits of IoT Integration in CNC Machines
Feature | Beschrijving |
---|---|
Predictive Maintenance | Identifies potential failures before they occur. |
Remote Monitoring | Enables off-site performance monitoring and adjustments. |
Increased Efficiency | Provides real-time data to optimize production parameters. |
Improved Machine Longevity | Reduces wear and tear by identifying maintenance needs early. |
7. How Do New CNC Innovations Impact CNC Machining Costs?
The initial cost of CNC machines can be high, but the long-term savings are where new innovations truly shine. But here’s where it gets interesting: while the upfront investment in the latest CNC machines may be steep, the long-term savings in operational costs can more than make up for it.
New CNC technologies, such as automation and AI, reduce the need for manual labor, cutting down on staffing costs. Machines that can operate autonomously or with minimal human supervision allow businesses to reallocate human resources to other areas, making the manufacturing process more cost-effective. For instance, AI-driven systems can optimize cutting speeds, tool changes, and other parameters to maximize machine uptime and minimize waste, which lowers the overall cost per unit produced.
In addition, predictive maintenance and IoT integration reduce unplanned downtime. In traditional systems, a machine breakdown could mean several hours or even days of halted production. With predictive maintenance, potential issues can be identified early, preventing unexpected failures and avoiding expensive repairs. This reduces the frequency and severity of breakdowns, ultimately saving manufacturers both time and money.
Moreover, by improving precision and reducing scrap rates, new CNC machines can help businesses use materials more efficiently. This reduces the amount of raw material wasted during production, further driving down costs.
Table 7: Cost Savings from New CNC Innovations
Cost Factor | Traditional CNC Machines | New CNC Innovations |
---|---|---|
Labor Costs | High | Reduced with automation |
Downtime | Frequent and costly | Minimized with predictive maintenance |
Material Waste | Higher | Reduced with improved precision |
Maintenance Costs | High and reactive | Lower with IoT and AI integration |
8. How Are CNC Innovations Improving Sustainability in Manufacturing?
Sustainability is more important than ever in today’s manufacturing environment, and new CNC technologies are playing a key role in reducing the environmental impact of machining operations. What’s the real story here? These innovations are helping manufacturers use resources more efficiently, reduce waste, and lower energy consumption.
One of the most significant sustainability benefits of new CNC machines is their ability to reduce material waste. Modern CNC machines are more precise than ever before, ensuring that less material is discarded during the machining process. This not only saves money on raw materials but also helps manufacturers meet sustainability goals by reducing their environmental footprint.
In addition, the energy efficiency of new CNC machines has greatly improved. Many of the latest models come equipped with energy-saving features, such as advanced motors, intelligent power management systems, and energy-efficient components. These machines consume less power, which reduces the overall energy costs and helps businesses contribute to a more sustainable manufacturing process.
Furthermore, the integration of additive manufacturing (3D printing) with CNC machining allows manufacturers to create parts with minimal waste. Unlike traditional machining methods, which remove material from a block, 3D printing adds material layer by layer, ensuring that only the necessary amount is used.
Table 8: Sustainability Benefits of New CNC Innovations
Feature | Beschrijving |
---|---|
Reduced Material Waste | High precision reduces waste during production. |
Energy Efficiency | New machines consume less energy with advanced technology. |
Additive Manufacturing | 3D printing enables parts to be made with minimal waste. |
Eco-Friendly Materials | New CNC machines work with sustainable materials, reducing environmental impact. |
9. What Are the Top CNC Innovations for Small and Medium Manufacturers?
It’s not just large manufacturers who benefit from CNC innovations. Small and medium-sized enterprises (SMEs) can also leverage new CNC technologies to stay competitive in the market. But here’s the kicker: many of these innovations are now accessible to businesses with limited budgets, making it easier for SMEs to adopt cutting-edge technology.
One key development is the availability of affordable, compact CNC machines designed specifically for smaller operations. These machines offer many of the same advanced features as larger models but at a fraction of the cost. For example, desktop CNC machines are now available with full functionality, making them ideal for smaller workshops or hobbyists looking to enter the CNC world.
Additionally, many CNC machines are now available as open-source systems. These systems allow SMEs to customize the machines and software to suit their specific needs, providing a level of flexibility and scalability that was previously unavailable to smaller manufacturers.
Moreover, cloud-based CNC software is making it easier for SMEs to manage their machines and operations remotely. This software allows businesses to monitor production, track performance, and manage maintenance schedules without needing to invest in expensive IT infrastructure.
Table 9: Top CNC Innovations for SMEs
Feature | Beschrijving |
---|---|
Compact Machines | Smaller, more affordable machines for smaller operations. |
Open-Source Systems | Customizable CNC machines and software for greater flexibility. |
Cloud-Based CNC Software | Remote monitoring and management of CNC machines. |
Affordable Automation | Automation options available for smaller budgets. |
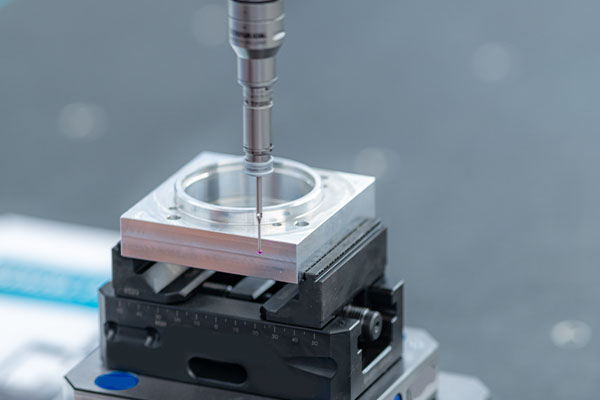
10. What Are the Challenges in Implementing New CNC Technologies?
While the benefits of new CNC innovations are clear, implementing these technologies does come with its challenges. So, what’s the catch? The adoption of new CNC technologies can be costly, time-consuming, and requires a significant amount of training.
First, there’s the cost of purchasing the latest equipment. New CNC machines are often more expensive than older models, and the costs don’t end there. Installation, training, and maintenance also come with additional expenses. This can be a significant hurdle for businesses with limited budgets.
Additionally, the learning curve for new technologies can be steep. Operators must undergo training to effectively use the advanced features of modern CNC machines. This requires both time and resources, which can be a burden for businesses looking to stay competitive while managing their workforce.
Finally, integrating new CNC technologies into existing workflows can be difficult. Older machines and processes may not be compatible with the latest innovations, requiring businesses to completely overhaul their operations to take full advantage of new technologies.
Table 10: Challenges of Implementing New CNC Technologies
Uitdaging | Beschrijving |
---|---|
High Initial Costs | New CNC machines and technology come with a high price tag. |
Training and Skill Development | Operators must be trained to use the new systems effectively. |
Integration with Existing Systems | New technologies may not be compatible with older equipment. |
Maintenance Costs | New machines may require specialized maintenance services. |
11. What Is the Future of CNC Innovations?
The future of CNC machining is bright, with advancements in artificial intelligence, robotics, and additive manufacturing paving the way for even more groundbreaking innovations. Ready for the good part? These technologies will not only improve the efficiency of CNC machining but will also lead to the creation of entirely new manufacturing possibilities.
One exciting development is the integration of AI and machine learning in CNC systems. These systems will be able to learn from past operations and continuously optimize machining parameters for even greater efficiency and accuracy. This self-optimization will allow CNC machines to adapt to different production environments without human intervention.
Robotics will also play a key role in the future of CNC machining. Robotic arms will be integrated with CNC machines to automate tasks such as material handling, assembly, and inspection. This will lead to even greater automation and reduced labor costs.
In addition, the continued growth of additive manufacturing (3D printing) will open up new possibilities for creating complex, customized parts that were previously difficult or impossible to produce with traditional CNC methods.
Table 11: Future Trends in CNC Innovation
Trend | Beschrijving |
---|---|
AI and Machine Learning | Systems that learn and optimize processes automatically. |
Robotics Integration | More automated tasks with robotic arms integrated into CNC systems. |
Additive Manufacturing Growth | 3D printing will enable more complex part designs. |
Self-Optimizing CNC Machines | Machines that adjust settings automatically for optimal performance. |
12. How Can Manufacturers Stay Competitive with New CNC Innovations?
Staying competitive in today’s rapidly changing manufacturing landscape requires embracing new CNC innovations. But here’s the kicker: it’s not just about adopting new technologies—it’s about strategically integrating them into your operations.
One of the best ways to stay competitive is by continuously evaluating your existing equipment and processes. Don’t wait until a competitor gains an advantage—actively seek out opportunities to improve your operations with the latest CNC technologies. By investing in new equipment, software, and training, you can increase your production capabilities and reduce costs.
Another key strategy is to collaborate with technology providers to gain insights into the latest trends. Networking with suppliers and industry experts will help you stay informed about new advancements and ensure that you’re always one step ahead of the competition.
Finally, it’s crucial to invest in workforce development. Ensure that your team is well-trained in using the latest CNC technologies, and foster a culture of continuous learning to keep your business on the cutting edge.
Table 12: Strategies to Stay Competitive with CNC Innovations
Strategy | Beschrijving |
---|---|
Regular Equipment Evaluation | Continuously assess and upgrade equipment to stay ahead. |
Collaboration with Technology Providers | Gain insights into emerging trends and innovations. |
Workforce Training | Invest in ongoing training to keep your team skilled in the latest CNC systems. |
Focus on Innovation | Foster a culture of innovation to adapt quickly to new CNC technologies. |
13. What Are the Best CNC Machines for High-Precision Work?
For manufacturers who require extreme precision, choosing the right CNC machine is crucial. Ready for the good part? Some of the latest CNC machines offer ultra-high precision and are capable of producing parts with tolerances measured in microns.
Machines with advanced thermal stability, vibration damping systems, and enhanced spindle performance are ideal for high-precision work. These systems are designed to minimize errors and ensure that each part is produced to exact specifications.
In addition, CNC machines with multi-axis capabilities allow for complex parts to be machined in one setup, which increases both speed and accuracy. Machines with direct drive spindles and high-frequency motors further improve precision by reducing backlash and increasing torque.
Some CNC machines also come with advanced software that supports complex geometry and allows for real-time adjustments during the machining process. These features, combined with precise hardware, make modern CNC machines the go-to solution for industries like aerospace, medical devices, and electronics.
Table 13: Best CNC Machines for High-Precision Work
Feature | Beschrijving |
---|---|
Thermal Stability | Ensures minimal temperature fluctuations for higher accuracy. |
Vibration Damping | Reduces vibrations to improve machining precision. |
Multi-Axis Capability | Allows for complex parts to be machined in one setup. |
Direct Drive Spindles | Enhances torque and minimizes backlash for better precision. |
14. How Does Automation in CNC Machines Enhance Production?
Automation in CNC machines is a game-changer. What’s the catch? CNC automation can drastically reduce production time, improve consistency, and lower labor costs.
Automated systems, like robotic arms, can handle tasks such as part loading and unloading, material handling, and even inspection. This reduces the need for human intervention, ensuring that production continues without delays or errors.
Automated CNC machines can also communicate with other systems within the production line, allowing for seamless integration and optimized workflow. For example, automated tools can be swapped in and out without human assistance, reducing downtime between operations.
Furthermore, automated systems can monitor the machining process in real-time, making adjustments to maintain optimal conditions. This ensures consistent quality across all parts, which is essential for industries that require high standards, like automotive or aerospace manufacturing.
Table 14: Benefits of Automation in CNC Machines
Voordeel | Beschrijving |
---|---|
Reduced Production Time | Automation speeds up machining processes. |
Improved Consistency | Machines operate with minimal human intervention, ensuring consistent quality. |
Lower Labor Costs | Reduces the need for human operators and manual tasks. |
Seamless Workflow Integration | Automated machines can communicate with other systems in the production line. |
15. How Can Businesses Maximize ROI with CNC Innovations?
Maximizing return on investment (ROI) with new CNC innovations involves strategic planning and effective implementation. But here’s where it gets interesting: even though these machines come with a hefty price tag, they can provide significant returns over time through increased efficiency, reduced waste, and improved product quality.
One of the most effective ways to maximize ROI is by focusing on regular machine maintenance. By keeping your CNC machines in peak condition, you can extend their lifespan and prevent costly breakdowns. Additionally, it’s essential to continually assess your machining processes to identify areas for improvement.
Another way to boost ROI is by investing in operator training. Skilled operators are more efficient and better able to troubleshoot issues, ensuring that your machines are always running at their best.
Lastly, leveraging data collected from IoT and AI systems can provide valuable insights into machine performance, production trends, and potential improvements, all of which can help businesses make smarter decisions and optimize their operations for maximum ROI.
Table 15: Maximizing ROI with CNC Innovations
Strategy | Beschrijving |
---|---|
Regular Machine Maintenance | Keeps machines in optimal condition to avoid breakdowns. |
Operator Training | Skilled operators increase efficiency and reduce errors. |
Data-Driven Decision Making | Use IoT and AI data to make informed decisions for optimization. |
Process Optimization | Continuously assess and refine production processes for greater efficiency. |
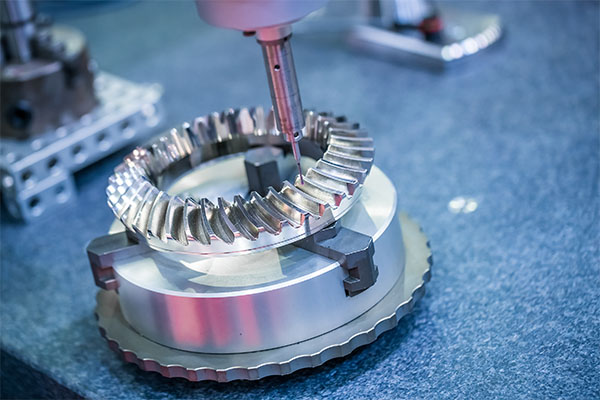
FAQ-sectie
Vraag 1: What is a CNC machine?
A CNC (Computer Numerical Control) machine is a machine tool that is controlled by a computer program. CNC machines can perform various tasks like milling, drilling, turning, and cutting to manufacture precise parts for a wide range of industries.
Vraag 2: How does CNC machining work?
CNC machining works by using computer software to control machine tools. A part design is created in a CAD (Computer-Aided Design) system, and the CNC machine follows the instructions to create the part by removing material from a solid block.
Vraag 3: What are the benefits of new CNC innovations?
New CNC innovations enhance machining precision, speed, and automation, leading to reduced production times and costs. They also improve safety and sustainability, making manufacturing processes more efficient and eco-friendly.
Vraag 4: How do artificial intelligence and CNC work together?
Artificial intelligence in CNC machines optimizes machining processes by predicting and preventing equipment failure, enhancing operational efficiency, and improving production planning through real-time data analysis and learning from past operations.
Vraag 5: What are the challenges in adopting new CNC technologies?
Challenges include the high initial cost of new machines, the learning curve for operators, and the need for regular maintenance. Additionally, businesses must ensure that their workforce is trained to handle the latest CNC technologies to fully leverage their capabilities.