Wprowadzenie do tolerancji obróbki CNC
Obróbka CNC jest jedną z najdokładniejszych metod produkcji, umożliwiającą produkcję części o wysokiej dokładności i powtarzalności. Jednak kluczowym czynnikiem w obróbce CNC jest koncepcja tolerancji, która definiuje dopuszczalne odchylenia wymiarów części. Tolerancje są niezbędne, aby zapewnić, że części pasują i działają prawidłowo w końcowym montażu, szczególnie w przypadku zamówień niestandardowych. Zrozumienie różnych typów tolerancji i ich wpływu na proces obróbki jest kluczowe zarówno dla producentów, jak i klientów. W tym przewodniku przyjrzymy się kluczowym aspektom Tolerancje obróbki CNC, w tym ich rodzaje, czynniki na nie wpływające oraz sposoby ich optymalizacji pod kątem opłacalności i precyzji.
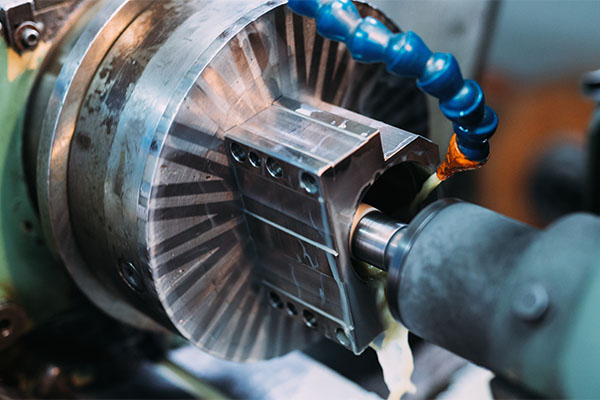
Czym są tolerancje obróbki CNC?
Definiowanie tolerancji w obróbce CNC
Tolerancje to dopuszczalne granice odchyleń wymiarów części. W obróbce CNC odnosi się to do tego, jak bardzo rzeczywiste wymiary danej części mogą różnić się od zamierzonych wymiarów projektowych, a jednocześnie być akceptowalne dla funkcji. Zasadniczo tolerancje definiują zakres, w którym część może się różnić, i zapewniają, że część nadal będzie mogła prawidłowo pasować do zamierzonego zespołu.
W obróbce CNC rozróżnia się dwa podstawowe typy tolerancji: tolerancje wymiarowe I tolerancje geometryczneTolerancje wymiarowe odnoszą się do dopuszczalnego odchylenia od określonego pomiaru (takiego jak długość, szerokość i wysokość), podczas gdy tolerancje geometryczne opisują dopuszczalne odchylenia kształtu lub formy części (takie jak prostoliniowość, płaskość lub okrągłość). Tolerancje te są kluczowe dla zapewnienia, że części działają prawidłowo i są kompatybilne z innymi komponentami.
Dlaczego tolerancje są kluczowe w obróbce CNC
Precyzja maszyny CNC jest w dużej mierze determinowana przez jej zdolność do utrzymywania ścisłych tolerancji. W takich branżach jak przemysł lotniczy, motoryzacyjny czy urządzenia medyczne, gdzie komponenty muszą idealnie do siebie pasować, tolerancje stają się jeszcze ważniejsze. Określając precyzyjne tolerancje, producenci mogą zapewnić, że części spełniają wymaganą funkcjonalność i są niezawodne w warunkach operacyjnych.
Natomiast jeśli tolerancje są zbyt luźne, ostateczna część może nie spełniać zamierzonych kryteriów wydajności, co prowadzi do kosztownych błędów lub awarii. Z drugiej strony, zbyt ciasne tolerancje mogą zwiększyć koszty produkcji i niepotrzebnie wydłużyć terminy realizacji. Znalezienie właściwej równowagi jest niezbędne do osiągnięcia zarówno jakości, jak i efektywności kosztowej.
Rodzaje tolerancji obróbki CNC, które powinieneś znać
Tolerancje wymiarowe
Tolerancje wymiarowe określają, jak bardzo wymiary części mogą się różnić od zamierzonego pomiaru. Są to najczęściej określane tolerancje w obróbce CNC. Na przykład wał może wymagać długości 100 mm z tolerancją ±0,1 mm. Oznacza to, że rzeczywista długość może wynosić od 99,9 mm do 100,1 mm i nadal być akceptowalna.
Tolerancje wymiarowe można stosować do pomiarów liniowych (takich jak długość, szerokość lub wysokość części) i pomiarów kątowych (takich jak kąty między cechami). Im węższa tolerancja, tym dokładniejszy musi być pomiar, co często wymaga zaawansowanych maszyn CNC i dłuższego czasu produkcji.
Tolerancje geometryczne
Tolerancje geometryczne służą do kontrolowania kształtu, orientacji i lokalizacji cech na części. Tolerancje te są kluczowe dla zapewnienia, że części pasują do siebie zgodnie z przeznaczeniem. Na przykład otwór może wymagać idealnie okrągłego kształtu lub umieszczenia w precyzyjnym miejscu względem innych cech na części. Tolerancje geometryczne obejmują:
- Prostota: Zapewnia, że element, taki jak krawędź lub oś, jest idealnie prosty.
- Płaskość: Zapewnia, że powierzchnia jest równa w określonym zakresie tolerancji.
- Okrągłość: Zapewnia, że otwór lub element cylindryczny jest idealnie okrągły.
- Pozycja:Określa dokładne położenie obiektu względem innych.
Dzięki określeniu tych tolerancji geometrycznych projektanci mogą mieć pewność, że części spełniają wymagane kryteria funkcjonalne.
Tolerancje wykończenia powierzchni
Tolerancje wykończenia powierzchni określają gładkość powierzchni części. W wielu zastosowaniach jakość powierzchni może mieć kluczowe znaczenie dla wydajności części, zwłaszcza w przypadku komponentów, które się poruszają lub stykają się z innymi częściami. Wykończenie powierzchni jest często określane za pomocą pomiarów chropowatości, takich jak Ra (średnia chropowatość), Rz (średnia maksymalna wysokość) i Ry (maksymalna wysokość profilu).
Dlaczego tolerancje mają znaczenie: wpływ na jakość i funkcjonalność części
Rola tolerancji w funkcjonalności części
Jeśli chodzi o funkcjonalność części, tolerancje stosowane podczas procesu obróbki mogą znacząco wpłynąć na to, czy część będzie pasować i działać zgodnie z przeznaczeniem. Na przykład w przypadku komponentów samochodowych lub lotniczych niewielkie odchylenia w wymiarach części mogą mieć wpływ na to, jak dobrze części współdziałają, co prowadzi do problemów, takich jak słabe dopasowanie, nieefektywność, a nawet awaria pod wpływem naprężeń.
W niektórych przypadkach niewielkie odchylenie rozmiaru lub kształtu może nie być kwestią krytyczną. Jednak w przypadku zastosowań o wysokiej wydajności, takich jak komponenty silników, urządzenia medyczne lub instrumenty o wysokiej precyzji, nawet najmniejsze naruszenia tolerancji mogą prowadzić do kosztownych błędów i awarii produktu. Dlatego zrozumienie, jak wybrać właściwą tolerancję dla każdej części, jest niezbędne.
Tolerancje i kontrola jakości części
Tolerancje mają bezpośredni wpływ na proces kontroli jakości. Ścisłe tolerancje wymagają bardziej zaawansowanego sprzętu i wyższych poziomów kontroli, co zapewnia, że części spełniają surowe standardy. Metody kontroli jakości, takie jak współrzędnościowe maszyny pomiarowe (CMM) lub optyczne systemy pomiarowe, są często stosowane w celu sprawdzenia, czy części mieszczą się w określonym zakresie tolerancji. Im wyższa tolerancja, tym bardziej rygorystyczny staje się proces kontroli.
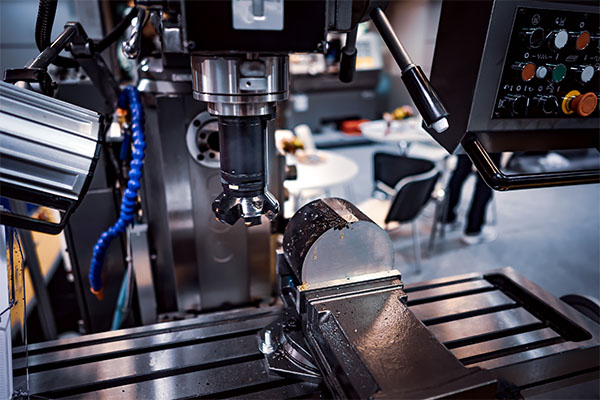
Czynniki wpływające na tolerancje obróbki CNC
Właściwości i tolerancje materiałów
Materiał wybrany do części ma znaczący wpływ na tolerancje, które można osiągnąć. Niektóre materiały, takie jak metale, mogą być bardziej stabilne i łatwiejsze do obróbki w ścisłych tolerancjach, podczas gdy inne, takie jak tworzywa sztuczne lub kompozyty, mogą podlegać większym odkształceniom podczas obróbki. Twardość materiału, rozszerzalność cieplna i wytrzymałość odgrywają rolę w tym, jak łatwo materiał może zachować ścisłe tolerancje.
Na przykład metale takie jak stal nierdzewna i aluminium są powszechnie używane do obróbki CNC, ponieważ zapewniają doskonałą stabilność wymiarową i mogą osiągnąć ścisłe tolerancje bez nadmiernego zużycia narzędzi. Jednak bardziej miękkie materiały, takie jak plastik lub guma, mogą wymagać specjalnych rozważań, aby zapewnić dokładną obróbkę.
Możliwości maszyn CNC
Rodzaj używanej maszyny CNC odgrywa również kluczową rolę w określaniu poziomu precyzji, jaki można osiągnąć. Maszyny CNC mają różne stopnie dokładności, a każda maszyna ma swoje własne ograniczenia, jeśli chodzi o utrzymanie ścisłych tolerancji. Maszyny o wysokiej precyzji, takie jak te stosowane w produkcji lotniczej, mogą utrzymywać tolerancje ±0,001 mm lub nawet mniejsze, podczas gdy maszyny ogólnego przeznaczenia mogą osiągać tolerancje tylko ±0,05 mm.
Wybierając maszynę, należy koniecznie dopasować jej możliwości do wymagań konkretnej produkowanej części. Zrozumienie ograniczeń sprzętu CNC pomoże w wyborze właściwej tolerancji dla części i uniknięciu niepotrzebnych regulacji, które mogłyby zwiększyć koszty.
Narzędzia i zużycie
Jakość narzędzi i ich zużycie w czasie mogą również wpływać na tolerancje osiągane w obróbce CNC. W miarę zużycia narzędzi mogą one powodować niewielkie odchylenia w wymiarach części. Regularna konserwacja i wymiana narzędzi są kluczowe dla utrzymania stałej precyzji.
Aby zmniejszyć wpływ zużycia narzędzi, wielu producentów stosuje zaawansowane powłoki lub narzędzia z węglików spiekanych, które są zaprojektowane tak, aby były trwalsze i zachowywały ostrość. Ponadto dostosowanie parametrów obróbki, takich jak prędkość, posuw i głębokość cięcia, może pomóc w poprawie precyzji gotowej części.
Typowe zakresy tolerancji obróbki CNC dla różnych materiałów
Tolerancje dla części metalowych
Części metalowe często muszą spełniać bardzo ścisłe tolerancje, szczególnie w takich branżach jak lotnictwo i motoryzacja. Na przykład części wykonane ze stali nierdzewnej mogą być obrabiane z tolerancją ±0,05 mm, podczas gdy części wykonane z aluminium mogą osiągać tolerancje tak ścisłe, jak ±0,025 mm. Tolerancje te zapewniają, że części metalowe pasują do siebie prawidłowo i dobrze działają w wymagających warunkach.
Tolerancje dla części plastikowych
Części plastikowe z kolei są na ogół trudniejsze do obróbki z takimi samymi ścisłymi tolerancjami jak metale. Tolerancja dla części plastikowych zwykle mieści się w zakresie od ±0,1 mm do ±0,5 mm, w zależności od rodzaju plastiku i złożoności części. Tworzywa sztuczne mogą być podatne na odkształcanie, kurczenie się lub rozszerzanie z powodu zmian temperatury, co może utrudniać utrzymanie stałych tolerancji.
W niektórych przypadkach do zastosowań krytycznych można stosować tworzywa sztuczne o wysokiej wydajności, takie jak PEEK lub PTFE. Materiały te mogą osiągnąć węższe tolerancje, ale wymagają bardziej zaawansowanych technik obróbki.
Tolerancje dla materiałów kompozytowych
Materiały kompozytowe, które są często stosowane w zastosowaniach lotniczych i motoryzacyjnych, stwarzają własne wyzwania, jeśli chodzi o obróbkę CNC. Materiały kompozytowe są często warstwowe i mogą mieć różne właściwości w zależności od kierunku włókien, co może powodować zmiany w wytrzymałości i stabilności wymiarowej części. Tolerancje dla części kompozytowych zwykle wahają się od ±0,1 mm do ±0,3 mm, w zależności od konkretnego materiału i geometrii części.
Wybór właściwych tolerancji dla niestandardowych obrabianych części
Określanie wymagań dotyczących tolerancji
Wybór właściwych tolerancji dla Twoich niestandardowych obrabianych części zaczyna się od zrozumienia konkretnej funkcji części. Na przykład części, które muszą do siebie pasować lub oddziaływać z innymi komponentami, wymagają węższych tolerancji, aby zapewnić właściwe wyrównanie i funkcjonalność. Z drugiej strony części, które nie wymagają precyzyjnego dopasowania, mogą być zaprojektowane z luźniejszymi tolerancjami, aby obniżyć koszty produkcji.
Aby określić optymalną tolerancję dla części, konieczne jest rozważenie zarówno wymagań projektowych, jak i możliwości procesu produkcyjnego. Zbyt ciasne tolerancje mogą wydłużyć czas produkcji, koszty narzędzi i prawdopodobieństwo błędów, podczas gdy zbyt luźna tolerancja może zagrozić funkcji lub jakości części.
Równoważenie precyzji i kosztów
Choć kuszące może być określenie możliwie najściślejszych tolerancji, aby zapewnić najwyższy poziom precyzji, często wiąże się to z wyższymi kosztami. Osiągnięcie ciaśniejszych tolerancji zazwyczaj wymaga bardziej zaawansowanych maszyn, dłuższego czasu obróbki i wyższych kosztów inspekcji. W przypadku wielu części bardziej opłacalne jest określenie tolerancji, które są odpowiednie dla zamierzonej funkcji części, bez przesady w kwestii precyzji.
Znalezienie właściwej równowagi pomiędzy tolerancją i kosztami jest kluczem do osiągnięcia zarówno jakości, jak i wydajności w obróbce niestandardowej.
Jak tolerancje wpływają na koszty obróbki CNC
Związek między tolerancjami a kosztami produkcji
W obróbce CNC istnieje bezpośrednia korelacja między ścisłością tolerancji a całkowitym kosztem produkcji. Węższe tolerancje zazwyczaj wymagają bardziej zaawansowanej technologii, większej precyzji i więcej czasu, aby upewnić się, że część jest zgodna ze specyfikacją. W rezultacie koszty produkcji mają tendencję do wzrostu wraz z potrzebą ściślejszych tolerancji. Dzieje się tak, ponieważ na każdym etapie procesu, od początkowego projektu do końcowej kontroli, wymagana jest większa uwaga na szczegóły.
Na przykład podczas obróbki części z tolerancją ±0,1 mm maszyna może potrzebować wykonać więcej przejść lub użyć specjalistycznych narzędzi, aby zapewnić osiągnięcie pożądanych wymiarów. Może to wydłużyć czas obróbki i zużycie materiału, co przyczynia się do wyższych kosztów. Z drugiej strony, część z tolerancją ±0,5 mm może nie wymagać tak dużo czasu lub specjalistycznego sprzętu do wytworzenia, co obniża koszty produkcji.
Ponadto części o mniejszych tolerancjach często wymagają bardziej rygorystycznej kontroli jakości i inspekcji. W zależności od zastosowania może to obejmować użycie zaawansowanych narzędzi, takich jak współrzędnościowe maszyny pomiarowe (CMM), skanowanie laserowe lub inne urządzenia pomiarowe o wysokiej precyzji. Koszt tych narzędzi, wraz z czasem spędzonym na inspekcji każdej części, może szybko wzrosnąć podczas produkcji komponentów o bardzo małych tolerancjach.
Jak tolerancje wpływają na czas realizacji
Tolerancje wpływają również na czas realizacji projektów obróbki CNC. Części o mniejszych tolerancjach wymagają bardziej starannego planowania i dodatkowego czasu na proces obróbki. Na przykład obróbka części wymagającej tolerancji ±0,01 mm może zająć kilka godzin dłużej niż obróbka podobnej części o tolerancji ±0,5 mm.
Dodatkowy czas potrzebny do spełnienia węższych tolerancji może również opóźnić ogólny harmonogram produkcji, szczególnie w projektach z wieloma częściami lub złożonymi geometriami. Ponadto, jeśli w trakcie procesu wystąpią błędy obróbki, mogą one wymagać korekty, co doprowadzi do dodatkowych przeróbek i dalszego wydłużenia czasu realizacji.
Aby zminimalizować wpływ ścisłych tolerancji na czas realizacji, producenci często muszą starannie planować i optymalizować proces obróbki. Może to obejmować wybór odpowiednich maszyn, dostosowanie parametrów cięcia i użycie najbardziej wydajnych ścieżek narzędzi, aby zapewnić ukończenie części zgodnie z harmonogramem.
Zrozumienie ograniczeń Twojego sprzętu i narzędzi CNC
Precyzja maszyn CNC i jej wpływ na tolerancje
Możliwości używanego sprzętu CNC są kluczowym czynnikiem w określaniu poziomu precyzji, jaki można osiągnąć podczas procesu obróbki. Różne typy maszyn CNC mają różne stopnie dokładności i ważne jest zrozumienie ograniczeń używanych maszyn, aby uniknąć ustalania nierealistycznych oczekiwań dotyczących tolerancji.
Na przykład, wysokiej klasy frezarki lub tokarki CNC używane w przemyśle lotniczym lub medycznym mogą osiągnąć tolerancje tak ścisłe jak ±0,001 mm. Maszyny te wykorzystują zaawansowane technologie, takie jak frezowanie wieloosiowe, kalibracja laserowa i systemy sprzężenia zwrotnego w czasie rzeczywistym, aby zachować ekstremalną precyzję.
Z drugiej strony, uniwersalne maszyny CNC mogą nie być w stanie utrzymać tak ścisłych tolerancji, a osiągalna dokładność może wynosić tylko ±0,05 mm lub ±0,1 mm. Niezbędne jest dopasowanie wymaganych tolerancji części do możliwości dostępnego sprzętu CNC, aby zapewnić, że produkcja jest zarówno wykonalna, jak i opłacalna.
Wybór właściwej maszyny CNC do danego zadania
Wybór odpowiedniej maszyny CNC do danego zadania jest kluczowy dla uzyskania pożądanej tolerancji. Na przykład, jeśli wymagana tolerancja jest wąska, a część ma złożoną geometrię, może być konieczna inwestycja w maszyny o wysokiej precyzji, takie jak szwajcarskie tokarki CNC lub frezarki 5-osiowe. Maszyny te oferują możliwość obróbki złożonych części z minimalnym błędem, ale wiążą się z wyższymi kosztami początkowymi i dłuższym czasem produkcji.
Jednak w przypadku prostszych części o luźniejszych tolerancjach może wystarczyć standardowa frezarka CNC. Wybór odpowiedniej maszyny na podstawie wymaganych tolerancji może pomóc usprawnić produkcję, obniżyć koszty i zapewnić, że część spełnia standardy jakości.
Narzędzia i zużycie narzędzi
Jakość i stan narzędzi używanych w obróbce CNC również odgrywają znaczącą rolę w dokładności produktu końcowego. Z czasem narzędzia mogą się zużywać, co powoduje zmiany wymiarów i odchylenia od określonych tolerancji. Dlatego regularna konserwacja i terminowa wymiana narzędzi są krytyczne dla utrzymania spójnych wyników, szczególnie podczas obróbki części z zachowaniem ścisłych tolerancji.
Ponadto materiał i powłoka narzędzia mogą mieć wpływ na jego trwałość i precyzję. Na przykład narzędzia węglikowe mają tendencję do utrzymywania ostrości i stabilności wymiarowej w czasie, co czyni je preferowanym wyborem do precyzyjnej obróbki CNC. Powlekane narzędzia, takie jak te z powłokami z azotku tytanu (TiN) lub węglem diamentopodobnym (DLC), mogą również pomóc zmniejszyć zużycie i wydłużyć żywotność narzędzia, co jest szczególnie ważne podczas obróbki trudnych materiałów lub produkcji części o ciasnych tolerancjach.
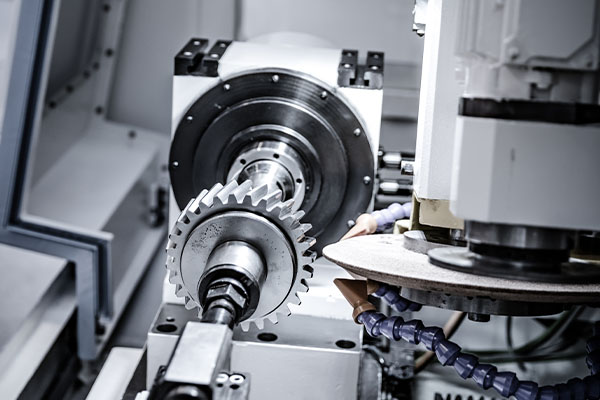
Optymalizacja tolerancji w celu skrócenia czasu realizacji i obniżenia kosztów
Równoważenie precyzji i wydajności
Podczas gdy ścisłe tolerancje są konieczne w przypadku niektórych zastosowań, mogą one prowadzić do dłuższych terminów realizacji i wyższych kosztów produkcji. Dlatego jednym z kluczowych wyzwań w obróbce CNC jest znalezienie właściwej równowagi między precyzją a wydajnością. Osiągnięcie wymaganych tolerancji przy jednoczesnym utrzymaniu niskich kosztów produkcji i utrzymaniu szybkiego czasu realizacji jest niezbędne do spełnienia wymagań klientów i utrzymania konkurencyjności na rynku.
Jednym ze sposobów optymalizacji tolerancji przy zachowaniu wydajności jest skupienie się na krytycznych wymiarach części. Nie wszystkie cechy części muszą spełniać najściślejsze tolerancje. Poprzez określenie, które wymiary są najważniejsze dla funkcjonalności części i stosowanie ściślejszych tolerancji tylko tam, gdzie jest to konieczne, producenci mogą skrócić czas obróbki i obniżyć koszty bez uszczerbku dla wydajności części.
Usprawnienie procesu obróbki
Aby zoptymalizować czas obróbki i obniżyć koszty, producenci powinni również rozważyć usprawnienie procesu obróbki. Można to osiągnąć, wybierając odpowiednie strategie obróbki, takie jak używanie najbardziej odpowiednich narzędzi skrawających, dostosowywanie prędkości posuwu i optymalizowanie ścieżek narzędzi. Maszyny CNC wyposażone w zaawansowane możliwości automatyzacji, takie jak zmieniacze narzędzi lub zautomatyzowane systemy ładowania, mogą również pomóc w skróceniu czasu poświęcanego na zadania nieproduktywne, co jeszcze bardziej przyspieszy proces.
Innym skutecznym sposobem optymalizacji tolerancji jest wykorzystanie zaawansowanych technik produkcyjnych, takich jak produkcja addytywna lub obróbka hybrydowa. Metody te często pozwalają osiągnąć ten sam poziom precyzji, co tradycyjna obróbka CNC, jednocześnie redukując marnotrawstwo materiału, zużycie narzędzi i czas produkcji.
Przykłady wyzwań i rozwiązań tolerancji w świecie rzeczywistym
Studium przypadku 1: Komponent lotniczy o wąskich tolerancjach
W produkcji lotniczej części takie jak komponenty silnika i elementy konstrukcyjne muszą spełniać niezwykle ścisłe tolerancje, aby zapewnić bezpieczeństwo i wydajność. Jeden z przykładów z prawdziwego świata dotyczył specjalnie obrabianego wspornika aluminiowego używanego w systemie podwozia samolotu. Tolerancja wymagana dla tej części wynosiła ±0,01 mm, co stanowiło wyzwanie ze względu na potencjał materiału do rozszerzalności cieplnej i skomplikowaną geometrię projektu.
Aby spełnić wymagania dotyczące ścisłych tolerancji, producent użył precyzyjnej 5-osiowej maszyny CNC z kalibracją laserową. Ponadto wdrożyli wieloetapowy proces obróbki, który obejmował precyzyjne operacje zgrubne, półwykańczające i wykańczające. Część została również poddana kilku rundom kontroli jakości przy użyciu współrzędnościowej maszyny pomiarowej (CMM), aby upewnić się, że spełnia ona wymagane specyfikacje.
Studium przypadku 2: Komponent urządzenia medycznego o złożonej geometrii
W branży urządzeń medycznych komponenty takie jak narzędzia chirurgiczne i implanty wymagają wysokiej precyzji, aby zapewnić ich prawidłowe i bezpieczne działanie. Jednym z przykładów była obróbka tytanowego implantu kolana, która wymagała złożonych tolerancji geometrycznych, w tym precyzyjnej okrągłości i tolerancji położenia dla otworów, w których miałyby być osadzone śruby.
Aby osiągnąć te tolerancje, producent użył szwajcarskiej tokarki CNC z możliwością obsługi narzędzi. Pozwoliło im to na obróbkę części w jednym ustawieniu, zmniejszając ryzyko błędów spowodowanych przez zmianę położenia. Następnie część została sprawdzona za pomocą wysoce precyzyjnego optycznego systemu pomiarowego, aby upewnić się, że wszystkie tolerancje geometryczne zostały spełnione.
Kontrola jakości: zapewnienie dokładności i spójności obróbki CNC
Znaczenie rygorystycznej kontroli
Kontrola jakości odgrywa kluczową rolę w zapewnieniu, że części mieszczą się w określonych tolerancjach i spełniają wymagane standardy. W obróbce CNC kontrola rozpoczyna się w trakcie procesu konfiguracji i trwa przez cały cykl produkcyjny. Wielu producentów używa współrzędnościowych maszyn pomiarowych (CMM) i systemów skanowania laserowego do dokładnego pomiaru części i wykrywania wszelkich odchyleń od pożądanych specyfikacji.
Kontrola może również obejmować kontrole wizualne, oceny wykończenia powierzchni i testy funkcjonalne, w zależności od zamierzonego zastosowania części. W przypadku części o szczególnie ciasnych tolerancjach mogą być wymagane dodatkowe kroki kontroli, aby upewnić się, że podczas procesu obróbki nie wystąpią żadne odchylenia.
Rola zautomatyzowanych systemów inspekcji
Wraz z rozwojem technologii wielu producentów polega obecnie na zautomatyzowanych systemach inspekcji, aby monitorować precyzję części obrabianych CNC. Systemy te wykorzystują lasery, kamery lub inne czujniki do ciągłego sprawdzania wymiarów części w trakcie ich produkcji. Zautomatyzowana inspekcja nie tylko zwiększa dokładność, ale także przyspiesza proces kontroli jakości, umożliwiając producentom wczesne wykrywanie błędów i zapobieganie kosztownym pomyłkom.
Ciągłe doskonalenie i pętle sprzężenia zwrotnego
Oprócz formalnych inspekcji producenci powinni wdrażać programy ciągłego doskonalenia, aby monitorować wydajność obróbki w czasie. Poprzez śledzenie kluczowych wskaźników, takich jak zużycie narzędzi, wydajność maszyny i dokładność produkcji, producenci mogą identyfikować obszary wymagające poprawy i wprowadzać niezbędne zmiany, aby stale utrzymywać ścisłe tolerancje.
Rola tolerancji w zamówieniach obróbki niestandardowej
Specyfikacje obróbki niestandardowej i tolerancji
Składając zamówienia na obróbkę skrawaniem, klienci powinni jasno komunikować swoje wymagania dotyczące tolerancji, aby uniknąć nieporozumień lub kosztownych błędów. Dostarczenie szczegółowych rysunków określających pożądane tolerancje dla każdej cechy części pomoże zapewnić, że proces obróbki będzie przebiegał sprawnie. Klienci powinni również współpracować ze swoimi partnerami produkcyjnymi, aby ustalić, czy określone tolerancje są możliwe do osiągnięcia w ramach danego czasu i budżetu.
Współpraca z dostawcami obróbki CNC
Współpraca między klientem a dostawcą jest kluczowa, aby zapewnić, że tolerancje są jasno zrozumiane i spełnione. Może to obejmować omówienie wyboru materiałów, przegląd możliwości sprzętu CNC i zapewnienie, że projekt części jest zoptymalizowany zarówno pod kątem możliwości produkcji, jak i wymagań dotyczących tolerancji.
Dostawcy często mogą dostarczyć cennych informacji na temat tego, jak dostosować projekty części, aby były łatwiejsze do obróbki, a jednocześnie spełniały specyfikacje tolerancji. Współpracując, producenci i klienci mogą osiągnąć najlepszą możliwą równowagę między precyzją, kosztami i czasem realizacji.

Często zadawane pytania
Jakie są najczęstsze tolerancje obróbki CNC?
Najczęstsze tolerancje dla obróbki CNC wahają się od ±0,05 mm do ±0,5 mm, w zależności od złożoności i materiału części. Węższe tolerancje, takie jak ±0,01 mm, są zazwyczaj wymagane w przypadku zastosowań o wysokiej precyzji, takich jak przemysł lotniczy i urządzenia medyczne.
Jak tolerancje wpływają na koszty obróbki CNC?
Węższe tolerancje zazwyczaj zwiększają koszty obróbki CNC, ponieważ wymagają bardziej zaawansowanego sprzętu, dłuższego czasu obróbki i bardziej rygorystycznej kontroli. Luźniejsze tolerancje mogą pomóc obniżyć koszty i czas produkcji.
Czy obróbka CNC pozwala na uzyskanie ścisłych tolerancji dla wszystkich materiałów?
Podczas gdy wiele materiałów, takich jak metale, może osiągnąć ścisłe tolerancje dzięki obróbce CNC, niektóre materiały, takie jak tworzywa sztuczne i kompozyty, są trudniejsze do obróbki z wysoką precyzją ze względu na ich wrodzone właściwości. Ważne jest, aby wybrać odpowiedni materiał dla wymaganej tolerancji.
Jak mogę obniżyć koszty obróbki części o małych tolerancjach?
Aby obniżyć koszty, skup się na optymalizacji projektu pod kątem możliwości produkcji. Określ tolerancje tylko tam, gdzie są one niezbędne do funkcji części, i wybierz odpowiedni proces obróbki i sprzęt do danego zadania. Współpraca z producentem może również pomóc zidentyfikować obszary, w których można obniżyć koszty bez poświęcania jakości.
Jakie narzędzia najlepiej sprawdzają się w osiąganiu ścisłych tolerancji w obróbce CNC?
Narzędzia węglikowe i narzędzia powlekane, takie jak te z powłokami z azotku tytanu (TiN), są idealne do uzyskania ścisłych tolerancji. Narzędzia te dłużej zachowują ostrość, zmniejszając ryzyko zużycia narzędzia i zmian wymiarowych.