Wstęp
Choosing the right CNC machining material is crucial for achieving the desired results in your manufacturing projects. Whether you’re working with metals, plastics, or composites, each material has its own unique properties that can affect the final product. In this article, we will explore the factors that go into selecting the best material for CNC machining, focusing on performance, cost, and precision. If you’ve ever been uncertain about which material is right for your project, you’re in the right place!
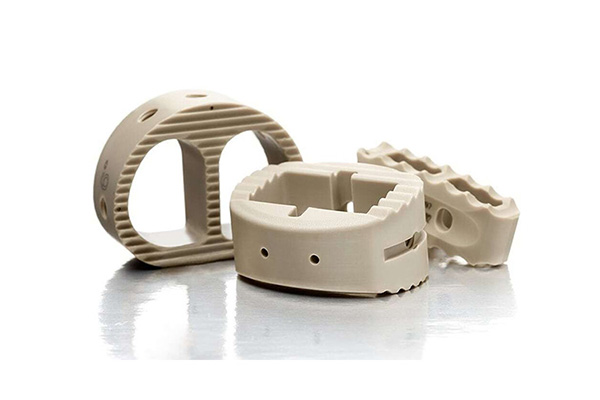
1. Why is selecting the right CNC machining material important?
The right material choice can make or break the success of your project. So, what makes material selection so crucial? Well, the material you choose impacts everything from the strength and durability of the part to its machinability and cost-efficiency.
What’s the real story? Choosing the wrong material can lead to increased production costs, longer machining times, and potentially, an inferior final product. For instance, selecting a material with low machinability might slow down the process, leading to higher labor costs and more wear on tools.
At the same time, selecting a material that is too expensive for the project could mean an unnecessary increase in costs, cutting into your profit margins. That’s why understanding the unique properties of materials is key to balancing these factors effectively.
Let’s look at an example. When machining a part that will experience high mechanical stress, selecting a material like titanium might be ideal due to its high strength-to-weight ratio. However, its cost could be prohibitive for some applications. In such cases, a material like steel could offer the right balance of performance and cost.
Table 1: Comparing Material Properties for Different CNC Applications
Tworzywo | Strength | Durability | Koszt | Machinability |
---|---|---|---|---|
Tytan | Wysoki | Wysoki | Wysoki | Niski |
Aluminium | Medium | Medium | Medium | Wysoki |
Steel | Wysoki | Wysoki | Medium | Medium |
Mosiądz | Niski | Niski | Medium | Wysoki |
2. What are the most common CNC machining materials?
CNC machining materials vary greatly depending on the type of part being produced. But here’s the kicker: understanding which materials are most commonly used for CNC machining is essential for making informed decisions. The most common materials include metals, plastics, and composites.
Metals are a popular choice for CNC machining due to their strength and durability. Aluminum, for example, is lightweight, corrosion-resistant, and highly machinable, making it ideal for a wide range of applications. Steel, on the other hand, offers superior strength and durability, making it perfect for more heavy-duty projects. Titanium is often used for high-performance applications, particularly in aerospace and medical devices.
Plastics like ABS and PEEK are also widely used, especially for parts that don’t require the strength of metals but still need durability and precision. PEEK, in particular, is known for its chemical resistance and ability to withstand high temperatures.
Composites, such as carbon fiber and fiberglass, are used when weight reduction is critical without sacrificing strength. These materials are commonly found in aerospace, automotive, and sporting goods industries.
Table 2: Overview of Common CNC Machining Materials
Tworzywo | Type | Key Use Case | Korzyści | Limitations |
---|---|---|---|---|
Aluminium | Metal | Aerospace, Automotive | Lightweight, corrosion-resistant | Lower strength than steel |
Steel | Metal | Heavy machinery, automotive | Strong, durable | Prone to corrosion |
ABS | Plastic | Prototypes, automotive | Easy to machine, low cost | Less durable than metals |
Carbon Fiber | Composite | Aerospace, automotive | High strength-to-weight ratio | Expensive, brittle |
3. How do you choose the right material for CNC machining?
Choosing the right material for CNC machining involves understanding a few key factors. Let’s dive into the specifics. So, what’s the deal? First, you need to think about the mechanical properties required for the project. This includes strength, hardness, and wear resistance. For example, parts that will be exposed to high temperatures or pressure, such as engine components, may require a material with high heat resistance and strength.
The next consideration is the material’s machinability. Some materials are more difficult to machine than others, and this can significantly affect the overall production time and cost. Materials like aluminum are relatively easy to machine, while others, like titanium, may require specialized tools and techniques.
Finally, the material’s cost is an important factor. You might be tempted to use the strongest or most durable material, but that could drive up the price. Sometimes, a more affordable material with the right balance of properties might be the better choice.
Table 3: Key Factors to Consider When Choosing CNC Machining Materials
Czynnik | Namysł |
---|---|
Mechanical Properties | Strength, hardness, and wear resistance |
Machinability | Ease of machining, tool wear, and cutting speed |
Koszt | Material cost, tooling costs, and labor costs |
4. What factors affect material selection for CNC machining?
There are several factors to consider when selecting a material for CNC machining, and it’s not just about the material itself. What’s the real story here? For instance, material strength is a crucial factor. Strong materials like steel or titanium are ideal for heavy-duty parts, but they may require more sophisticated equipment to machine.
Next, you need to think about thermal properties. Some materials expand or contract significantly under heat, which can lead to dimensional issues in the final part. Materials like aluminum are less prone to thermal expansion, making them ideal for applications that involve heat.
Wear resistance is another key factor. In industries where parts are exposed to constant friction, materials with high wear resistance, such as certain steels or ceramics, are preferred. Corrosion resistance is equally important, especially for parts used in harsh environments like marine or chemical industries.
Table 4: Material Properties for Specific CNC Machining Applications
Aplikacja | Tworzywo | Required Properties |
---|---|---|
Engine Components | Tytan | High strength, heat resistance |
Gear Parts | Steel | Wear resistance, strength |
Outdoor Parts | Stal nierdzewna | Corrosion resistance |
5. How does material cost impact CNC machining projects?
Material cost can have a significant impact on CNC machining projects. So, what’s the catch? While selecting a high-performance material like titanium may seem ideal for certain applications, it could dramatically increase the project cost, making it impractical for smaller-scale production.
For large-volume projects, the cost of material becomes even more critical. Bulk purchasing can sometimes help reduce costs, but it’s important to balance cost savings with the quality and properties needed for the part. Materials like aluminum or certain plastics might be more cost-effective choices without sacrificing too much in terms of strength and durability.
Let’s not forget about machining costs, which are directly impacted by the material choice. Harder materials tend to wear down tools faster, which can lead to more frequent tool changes and higher labor costs.
Table 5: Material Cost Comparison for CNC Machining Projects
Tworzywo | Cost per Unit | Machining Cost | Total Project Cost (Estimate) |
---|---|---|---|
Tytan | Wysoki | Wysoki | Very High |
Aluminium | Medium | Niski | Moderate |
Steel | Medium | Medium | Moderate |
Plastic | Niski | Niski | Niski |
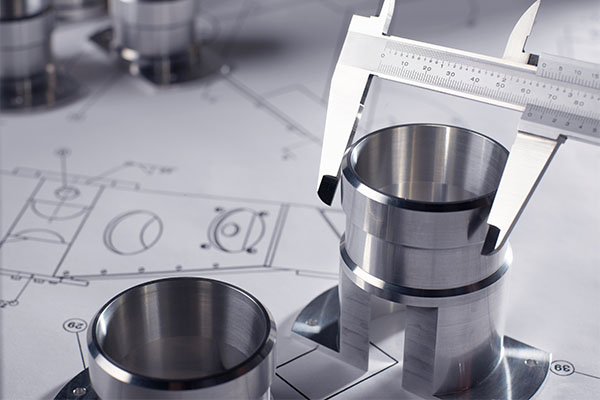
6. What is the importance of material availability in CNC machining?
Material availability is a critical aspect of selecting the right material for CNC machining. This is where it gets interesting. Imagine you’ve chosen the perfect material for your project, but there’s a problem: the material is on backorder. This can lead to significant delays and even project failure if you’re on a tight timeline.
In addition, sourcing materials from suppliers across different countries can lead to increased lead times due to shipping or regulatory issues. Working with suppliers who have a stable stock of materials or a short lead time for delivery can be the difference between meeting deadlines and not.
Let’s take a look at the aerospace industry, where precise materials are crucial. Aircraft manufacturers depend on the availability of materials like aluminum and titanium to meet their tight production schedules. Delays in material supply can disrupt production lines and cost millions in lost revenue.
7. How do machining processes affect material selection?
CNC machining processes can significantly influence the choice of material, and it’s essential to align the process with the material’s properties. So, what’s the deal? Each machining process has its own requirements, and some materials perform better with certain techniques than others.
For instance, when performing CNC turning, a material like aluminum is often preferred due to its ease of machining. It’s lightweight, soft, and has excellent machinability, which allows it to be cut quickly and precisely with minimal tool wear. On the other hand, CNC milling might require harder materials like steel or titanium, as these materials can better withstand the forces generated by the rotating tools during the milling process.
When it comes to surface finishing, the process also matters. For example, materials like stainless steel and aluminum are well-suited for processes like polishing or anodizing, which can enhance their surface appearance and corrosion resistance. Meanwhile, materials like plastic may not provide the same quality finish when subjected to these processes but can be easily painted or coated.
Another factor to consider is material removal rate (MRR). Harder materials like steel may require slower feed rates and more robust tooling to ensure proper material removal. This impacts the overall machining time and costs. On the other hand, materials that are easier to machine, like aluminum, tend to have a faster MRR and can be processed more efficiently.
Table 6: CNC Machining Process Compatibility with Materials
Machining Process | Best Material | Reason for Compatibility |
---|---|---|
Toczenie CNC | Aluminum, Brass | High machinability, lightweight |
Frezowanie CNC | Steel, Titanium | Stronger materials for rigidity |
Wykończenie powierzchni | Stainless Steel, Aluminum | Great for polishing, anodizing |
CNC Drilling | Plastics, Aluminum | Easier to drill through |
8. What are the best CNC machining materials for high-precision parts?
When it comes to high-precision parts, material selection is crucial. But here’s the kicker: CNC machining of precision parts requires materials that offer both strength and stability under extreme conditions. So, what makes materials suitable for precision applications?
The most common materials used in high-precision CNC machining are stainless steel, titanium alloys, and high-performance plastics like PEEK. These materials are favored for their high dimensional stability, which is essential for maintaining tight tolerances throughout the machining process. Titanium alloys, for example, provide excellent strength and corrosion resistance, making them ideal for aerospace and medical applications.
Stainless steel is another go-to material for precision parts. It offers high strength and durability, combined with corrosion resistance. It is commonly used in applications where both high strength and a polished finish are required, such as in the medical and automotive industries. For non-metallic high-precision parts, materials like PEEK and PTFE (Teflon) are often used, particularly in industries like electronics and food processing. These materials offer excellent chemical resistance and low friction, which is critical for applications that require tight fits and minimal wear.
When machining these materials, high-quality tools and advanced CNC techniques are often required to achieve the desired results. For instance, achieving tight tolerances on titanium parts may require slower feed rates and more advanced cutting tools to prevent tool wear.
Table 7: Best CNC Materials for High-Precision Machining
Tworzywo | Key Features | Best Use Case |
---|---|---|
Tytan | High strength, corrosion-resistant | Aerospace, medical implants |
Stal nierdzewna | Strong, durable, corrosion-resistant | Medical devices, automotive parts |
PEEK | High chemical resistance, low friction | Electronics, food processing parts |
PTFE (teflon) | Chemical resistance, non-stick | Pharmaceutical, food processing |
9. How do material properties influence CNC machining speed and efficiency?
Material properties play a pivotal role in CNC machining speed and efficiency. Ready for the good part? The hardness and density of a material directly influence the cutting speed and feed rate during the machining process. Harder materials generally take longer to machine due to increased tool wear and slower cutting speeds.
Take, for example, titanium alloys. These materials are tough to machine, requiring slower feed rates and special tooling to achieve the desired results. This can slow down the overall machining process and increase tooling costs. On the other hand, materials like aluminum are much softer, allowing for faster machining speeds, which increases efficiency and reduces overall production time.
Similarly, the material’s thermal conductivity impacts machining efficiency. Materials like aluminum, which have high thermal conductivity, can dissipate heat more efficiently, leading to cooler machining conditions. This results in less thermal distortion and increased tool life, which ultimately improves the efficiency of the machining process. In contrast, materials like steel or titanium tend to retain heat, leading to higher temperatures during machining, which can increase the risk of thermal distortion and reduced tool life.
By selecting materials with the appropriate properties for the machining process, manufacturers can significantly improve speed and efficiency, reduce tool wear, and lower overall production costs.
Table 8: Material Properties and Their Impact on CNC Machining Speed
Tworzywo | Hardness | Thermal Conductivity | Impact on Machining Speed |
---|---|---|---|
Tytan | Wysoki | Niski | Slower machining, higher wear |
Aluminium | Niski | Wysoki | Faster machining, lower wear |
Steel | Medium | Medium | Moderate machining speed |
Mosiądz | Niski | Wysoki | Fast machining, minimal wear |
10. What are the best CNC machining materials for durability?
Durability is key in CNC machining, especially when parts are subjected to harsh conditions. But what makes a material durable? Durable materials must withstand wear, corrosion, and mechanical stress over time without degrading. Let’s dive into the materials that offer the best durability for CNC machining.
Steel, especially stainless steel, is one of the best options for durability. Stainless steel is highly resistant to corrosion, making it perfect for industries like food processing and pharmaceuticals, where parts are exposed to moisture and chemicals. In addition, steel has high tensile strength, which makes it ideal for parts that need to withstand mechanical stress.
Another highly durable material is titanium. It has a remarkable combination of strength, light weight, and resistance to corrosion and high temperatures. These properties make it a popular choice in aerospace and military applications, where parts must endure extreme conditions.
For applications where high strength and impact resistance are crucial, materials like tungsten carbide and ceramics are often used. These materials are incredibly hard and can withstand high levels of wear and tear, making them suitable for cutting tools and high-performance industrial components.
Table 9: Durable Materials for CNC Machining
Tworzywo | Strength | Corrosion Resistance | Best Use Case |
---|---|---|---|
Stal nierdzewna | Wysoki | Excellent | Food processing, medical devices |
Tytan | Very High | Excellent | Aerospace, automotive |
Tungsten Carbide | Extremely High | Poor | Cutting tools, mining tools |
Ceramics | Very High | Excellent | High-performance industrial parts |
11. How do environmental factors affect material selection for CNC machining?
Environmental factors can significantly influence material selection, and it’s crucial to consider how these elements may affect performance. What’s the catch? Materials that perform well in controlled environments may not necessarily do so in harsh outdoor or industrial settings.
For example, materials used in outdoor applications must withstand exposure to moisture, temperature fluctuations, and ultraviolet radiation. Stainless steel and certain polymers, like UV-resistant plastics, are ideal choices for such conditions because they offer strong resistance to environmental degradation.
High temperatures are another environmental factor to consider. Materials like titanium and certain ceramics are excellent for high-heat applications, as they can withstand extreme temperatures without compromising their mechanical properties. On the other hand, materials like aluminum may not perform well in high-heat environments due to their relatively low melting point.
Chemical resistance is equally important, especially in industries like pharmaceuticals, food processing, and chemical engineering. Materials such as PTFE and PEEK offer excellent chemical resistance and can maintain their integrity when exposed to corrosive substances.
Table 10: Material Selection for Environmental Factors
Environmental Factor | Best Material | Reason for Selection |
---|---|---|
High temperatures | Titanium, Ceramics | High heat resistance |
Corrosive environments | Stainless Steel, PTFE | Excellent corrosion resistance |
UV exposure | UV-resistant Plastics | Resists degradation from UV rays |
Chemical exposure | PEEK, PTFE | Exceptional chemical resistance |
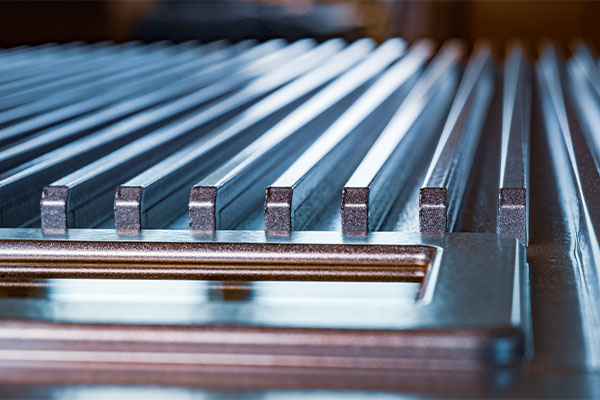
12. What are some advanced materials used in CNC machining?
Advanced materials are often used in CNC machining for high-performance applications where standard materials don’t meet the required specifications. But here’s the kicker: these advanced materials offer superior performance but often come at a higher cost and require specialized machining techniques.
For instance, carbon fiber composites are becoming increasingly popular in industries like aerospace and automotive. These materials offer an excellent strength-to-weight ratio and are ideal for applications where weight reduction is crucial. However, carbon fiber can be difficult to machine due to its brittle nature, requiring special tools and techniques.
Another advanced material is Inconel, a high-performance nickel-chromium alloy that can withstand extreme heat and pressure. It’s widely used in aerospace and energy sectors, particularly in turbine blades and other high-temperature applications. Machining Inconel can be challenging due to its hardness and tendency to work-harden, but it offers unmatched durability in extreme environments.
Ceramics are another advanced material used for their high-temperature resistance and hardness. They are often used in industries like medical device manufacturing and high-performance tooling. While ceramics are hard and wear-resistant, they are also brittle and require special handling during machining.
Table 11: Advanced CNC Materials for Specialized Applications
Tworzywo | Key Features | Best Use Case |
---|---|---|
Carbon Fiber | Lightweight, strong | Aerospace, automotive |
Inconel | High heat resistance, strong | Aerospace, energy sectors |
Ceramics | High hardness, heat resistance | Medical devices, tooling |
PEEK | High chemical resistance | Electronics, aerospace |
13. How does the finishing process affect material selection for CNC machining?
The finishing process is crucial in CNC machining, as it directly impacts the appearance and functionality of the final part. Ready for the good part? Depending on the material, different finishing processes can be applied to achieve a desired result.
Materials like aluminum and stainless steel are commonly polished to improve their surface finish and enhance corrosion resistance. On the other hand, materials like titanium may be anodized to create a durable oxide layer that improves wear resistance and provides an aesthetic color finish.
For plastics, coatings like painting or powder coating are often used to improve their durability and appearance. However, some materials may require more specialized treatments. For example, brass parts may be electroplated with gold or silver to enhance their corrosion resistance and aesthetic appeal.
Choosing the right material for finishing is essential because some materials may not respond well to certain treatments. For instance, high-strength materials like titanium can become brittle if over-treated during the anodizing process, so it’s important to carefully select both the material and the finishing process.
Table 12: Materials and Their Common Finishing Processes
Tworzywo | Common Finishing Process | Result |
---|---|---|
Aluminium | Polishing, anodizing | Corrosion resistance, aesthetic |
Stal nierdzewna | Polishing, passivation | Enhanced strength, appearance |
Tytan | Anodowanie | Corrosion resistance, color |
Mosiądz | Electroplating | Improved durability, aesthetics |
14. What are the common mistakes to avoid when selecting materials for CNC machining?
Selecting materials for CNC machining isn’t always straightforward. So, what should you avoid? Let’s explore some of the most common mistakes people make during material selection and how to prevent them.
One common mistake is overestimating the strength of a material. Just because a material is strong doesn’t mean it’s suitable for every application. For example, using titanium for a simple, non-load-bearing part can be unnecessarily expensive when other materials, like aluminum, would do just fine.
Another mistake is failing to consider material machinability. Some materials may seem ideal based on their strength or other properties, but they may be difficult to machine, resulting in longer production times, higher tool wear, and increased labor costs. Always ensure the material is compatible with the available machinery and tools.
Lastly, neglecting to factor in long-term performance can lead to premature failure of the part. For example, using a material that’s not resistant to corrosion or wear may lead to higher maintenance costs in the future.
Table 13: Common Mistakes in CNC Material Selection
Błąd | Konsekwencje | How to Avoid It |
---|---|---|
Overestimating material strength | Unnecessary high costs, weight | Assess the real performance needs |
Ignoring machinability | Increased production time and costs | Choose materials based on ease of machining |
Failing to consider long-term performance | Premature failure, higher maintenance costs | Select materials based on durability |
15. How can you optimize material selection for specific CNC machining needs?
Optimizing material selection is crucial for achieving the best results in CNC machining. But here’s the kicker: balancing performance, cost, and availability is key to making the best choice.
The first step is to evaluate the specific requirements of the project. What kind of stresses will the part face? Does it need to withstand high temperatures, corrosive environments, or heavy loads? Once these factors are understood, you can select the best material that offers the right balance of properties.
Next, consider material cost and availability. While high-performance materials may seem ideal, they can also be expensive and difficult to source. For large-volume projects, this can lead to significant cost increases. Therefore, it’s essential to find a material that meets performance requirements while staying within budget.
Finally, keep future maintenance and performance in mind. Some materials, like stainless steel, may cost more initially but will perform better and last longer, reducing the need for frequent replacements or repairs.
Table 14: Optimizing Material Selection for CNC Machining
Czynnik | Namysł |
---|---|
Performance | Match material properties to project requirements |
Koszt | Balance cost with material performance |
Availability | Ensure material is readily available |
Long-term Performance | Select durable materials to reduce future costs |
Sekcja FAQ
Pytanie 1: What is CNC machining material? CNC machining material refers to the raw material used in the CNC (Computer Numerical Control) process, which can be metals, plastics, or composites, depending on the project requirements.
Pytanie 2: How does material hardness affect CNC machining? Harder materials are more challenging to machine, which can increase wear on tools and affect machining speed. The correct material hardness is essential for balancing efficiency and part quality.
Pytanie 3: Why is material availability important for CNC machining? Material availability affects project timelines. Delays in sourcing specific materials can lead to missed deadlines and increased costs, so it’s crucial to consider material lead times when planning CNC machining projects.
Pytanie 4: What material is best for CNC machining aluminum parts? For aluminum parts, 6061 and 7075 alloys are commonly used due to their excellent machinability, strength, and versatility for various applications, from automotive to aerospace.
Pytanie 5: Can CNC machining handle all types of materials? While CNC machining can handle a wide range of materials, some high-strength or hard-to-machine materials, like certain ceramics or ultra-high-strength steels, may require specialized equipment or techniques.