Wstęp
CNC machining has revolutionized the way industries approach manufacturing, offering precise and efficient solutions for producing high-quality parts. But here’s the deal: the choice of material is one of the most critical decisions when setting up a CNC project. Whether you’re crafting parts for aerospace, automotive, or medical devices, the right material will determine the durability, cost, and overall performance of your product. In this guide, we will walk you through everything you need to know about CNC machining materials— from the different types of materials to how to choose the best one for your specific needs. By the end of this guide, you’ll be equipped to make informed decisions that lead to better results.
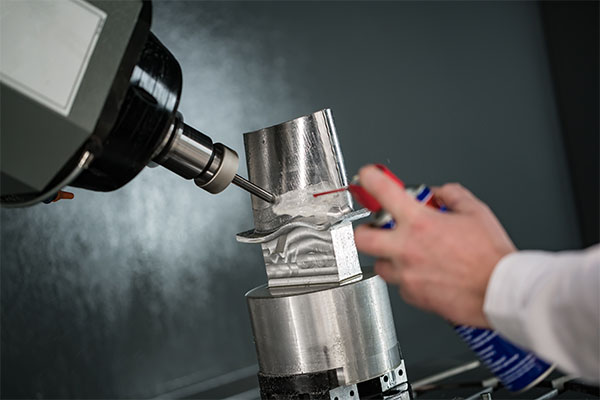
1. Types of CNC Machining Materials
When it comes to CNC machining, understanding the types of materials available is the first step in making an informed decision. There are several categories of materials commonly used in CNC operations, each offering unique properties that suit different applications. Let’s dive in and explore the most common material types.
Metale
Metals are the most widely used materials in CNC machining. They offer excellent strength, durability, and versatility. Some of the most popular metals used in CNC machining include:
- Steel: Steel, particularly carbon steel and stainless steel, is a go-to choice for applications requiring strength and durability. Carbon steel is often used for structural components, while stainless steel is favored for its corrosion resistance, making it ideal for medical or food-grade applications.
- Aluminium: Aluminum is a lightweight, corrosion-resistant metal, making it perfect for applications in aerospace, automotive, and electronics. Aluminum alloys, such as 6061, are particularly popular due to their strength-to-weight ratio and machinability.
- Tytan: Known for its superior strength and lightweight properties, titanium is commonly used in industries like aerospace and medical devices. However, titanium requires specialized tools due to its hardness, making it more difficult to machine than aluminum or steel.
- Mosiądz: Brass is commonly used for components that require electrical conductivity and corrosion resistance. It is softer than steel and aluminum, making it easier to machine, and is often used in the production of precision parts and fittings.
- Miedź: Copper alloys are used in applications that require high thermal conductivity, such as heat exchangers and electrical connectors.
Tworzywa sztuczne
Plastics offer advantages in applications where weight reduction and ease of machining are critical. They are more cost-effective than metals and offer good chemical resistance. Some of the most common plastics used in CNC machining include:
- ABS (Acrylonitrile Butadiene Styrene): ABS is a tough, impact-resistant plastic commonly used in automotive, consumer goods, and electronic housings.
- Poliwęglan: Polycarbonate is known for its transparency and high impact resistance. It is often used in applications where clear or tough plastic parts are needed, such as in the automotive and medical industries.
- Nylon: Nylon is a strong, durable, and lightweight plastic that is often used in applications requiring low friction, such as gears, bearings, and bushings.
Composites
Composite materials are often used in applications where high strength-to-weight ratios are required. These materials combine multiple components to achieve properties that are superior to those of individual materials.
- Carbon Fiber Reinforced Polymers (CFRP): CFRPs are used in aerospace, automotive, and sports equipment industries due to their exceptional strength-to-weight ratio.
- Glass Fiber Composites: Glass fiber composites are used in applications requiring high strength and heat resistance, such as automotive parts and electronics.
Others
- Drewno: Wood-based materials like plywood and MDF are commonly used for prototypes, furniture, and design products. They are easy to machine and can be customized to meet design specifications.
- Ceramics: Ceramic materials are used in highly specialized CNC machining applications, such as in the production of semiconductor components and medical devices, due to their durability and resistance to high temperatures.
2. Factors to Consider When Choosing CNC Machining Materials
Choosing the right CNC machining material isn’t just about picking the most popular or cheapest option. Instead, several factors must be carefully considered to ensure that the material meets the needs of your specific project. Let’s break it down.
Mechanical Properties
Mechanical properties like strength, toughness, and hardness are critical when choosing a material for CNC machining. Materials with high tensile strength can withstand heavy loads without deformation, making them suitable for applications that require durability, such as aerospace and automotive parts. Toughness is essential for materials used in impact-resistant parts, while hardness is important for materials that will undergo frequent wear, like tools or industrial equipment.
Thermal Properties
Thermal properties also play a significant role in material selection. Materials with high thermal resistance can withstand extreme temperatures without losing strength, which is vital in industries like aerospace and automotive. Thermal expansion should also be considered, as materials with high expansion rates may warp or deform when exposed to temperature fluctuations.
Workability
The ease of machining is an important factor to consider, especially if the material is difficult to work with. Soft materials, like aluminum and plastic, are generally easier to machine and cut, while harder materials, such as titanium and high-carbon steel, require specialized tooling and slower machining speeds to avoid tool wear.
Cost Considerations
Material costs can significantly impact the overall budget for a CNC machining project. Some materials, like aluminum, are relatively inexpensive compared to high-performance materials like titanium or carbon fiber composites. However, it’s important to balance cost with the specific needs of the project to ensure that you’re not compromising on quality or performance.
Aesthetic and Surface Finish Requirements
In some industries, the appearance of the final product is critical. Materials that can be polished or finished smoothly, like plastics and aluminum, are often chosen for aesthetic reasons. If surface finish is a priority, the material’s ability to achieve a high-quality finish should be considered.
3. Material Selection for Different CNC Machining Applications
Different industries and applications have specific material needs, and CNC machining is no different. Let’s explore the material requirements for various sectors to understand how to choose the right material based on the application.
Aerospace Industry
In the aerospace industry, strength, weight, and durability are the primary considerations when selecting CNC machining materials. Aluminum alloys such as 7075 and 6061 are commonly used because they are lightweight and strong. Tytan is also favored for its high strength-to-weight ratio and ability to withstand extreme temperatures and pressures. Carbon fiber composites are increasingly being used in aerospace applications due to their excellent strength-to-weight ratio.
Automotive Industry
The automotive industry requires CNC machining materials that are strong, durable, and capable of withstanding high temperatures and stresses. Steel alloys, including carbon steel and stainless steel, are commonly used for engine components and structural parts. Aluminium is often chosen for parts that require weight reduction, such as engine blocks and body panels. Plastic composites may also be used for lightweight components, such as dashboards and interior parts.
Medical Devices
Medical device manufacturing requires materials that are biocompatible, durable, and corrosion-resistant. Stainless steel is commonly used for surgical instruments, while plastics like polycarbonate and PEEK (Polyetheretherketone) are used for implants and other medical components. The material selection process also takes into account the need for materials that can be sterilized and are resistant to wear and tear in the body.
Elektronika użytkowa
In consumer electronics, precision and functionality are key. Tworzywa sztuczne like ABS and polycarbonate are widely used for housings and components due to their ease of machining, impact resistance, and ability to hold intricate designs. Aluminium is also commonly used for premium products, like laptop casings and smartphones, due to its lightweight and sleek finish.
Furniture and Design
Furniture manufacturing often involves materials that are easy to machine, aesthetically pleasing, and cost-effective. Wood and wood-based composites such as MDF and plywood are commonly used. Tworzywa sztuczne may also be used for functional or decorative parts, while metal may be chosen for legs, frames, and hardware.
4. Material Properties: How They Affect CNC Machining Performance
The properties of a material have a direct impact on how well it performs during CNC machining. Understanding these properties will help you make more informed decisions and optimize your machining processes.
Tensile Strength
Tensile strength refers to a material’s ability to resist breaking under tension. Materials with high tensile strength, like steel, titanium, I high-strength composites, are well-suited for applications where the part will be subjected to heavy loads. Materials with low tensile strength may not perform well in these situations, leading to deformation or breakage.
Hardness
Hardness is the measure of a material’s resistance to surface indentation or scratching. Harder materials, like tool steels, are necessary for applications where parts will be exposed to abrasive conditions. Softer materials, such as plastics and some aluminum alloys, are easier to machine but may not be suitable for high-wear environments.
Ductility
Ductility refers to a material’s ability to deform without breaking, which is important when working with parts that will undergo bending or stretching. Materials like steel I aluminum offer good ductility and are ideal for applications that require parts to withstand mechanical stress without cracking.
Corrosion Resistance
Corrosion resistance is an essential property for materials used in harsh environments, like those exposed to water or chemicals. Stainless steel I titanium offer excellent corrosion resistance, making them ideal for medical, marine, and chemical processing applications.
Weight and Density
The weight and density of a material can influence the performance of the final product. Lightweight materials like aluminum I plastics are preferred in industries like aerospace and automotive, where reducing weight is a priority. Heavier materials, like steel and titanium, are used where strength and durability outweigh the need for weight reduction.
5. CNC Machining Materials: Common Myths Debunked
There are many misconceptions surrounding CNC machining materials. Let’s debunk some common myths to clear up confusion and help you make better decisions.
Myth 1: All Metals Are the Same
Not true! Different metals have different properties, and understanding these differences is crucial when selecting the right material. For example, while aluminum is lightweight and easy to machine, steel is much stronger and more durable. Each metal type has its own unique properties, and these should align with your specific needs.
Myth 2: Plastics Are Not as Durable as Metals
While it’s true that metals are generally stronger than plastics, plastics like PEEK and nylon are highly durable and offer excellent resistance to wear and impact. They are often chosen for applications where weight reduction and chemical resistance are more important than sheer strength.
Myth 3: Composite Materials Are Too Expensive
Although composite materials like carbon fiber can have a high initial cost, they offer excellent performance in lightweight and high-strength applications. In the long run, their durability and performance may actually reduce costs, particularly in industries like aerospace where weight savings are critical.
6. How Material Selection Impacts Tooling and Equipment Choices
When selecting a CNC machining material, it’s essential to understand how the material will interact with your tools and equipment. Let’s break down how material selection affects tooling and equipment requirements.
Cutting Tools for Different Materials
Different materials require different cutting tools. Harder materials, such as steel and titanium, require cutting tools made from tougher materials like carbide Lub ceramic, which are more resistant to wear. Softer materials like aluminum and plastics can often be machined with high-speed steel tools. Tool coatings also play a significant role in extending tool life and improving performance.
Machine Settings for Material Types
The hardness and composition of the material will determine the settings for your CNC machine. For harder materials, slower speeds and lower feed rates are typically required to avoid damaging the tool. Softer materials can be machined at higher speeds, allowing for faster production times.
Material-Specific Workholding Solutions
Some materials require specialized workholding solutions to ensure accuracy and stability during machining. For example, softer materials like aluminum may need to be clamped securely to prevent deformation, while harder materials like titanium might require more robust fixtures to handle the forces during machining.
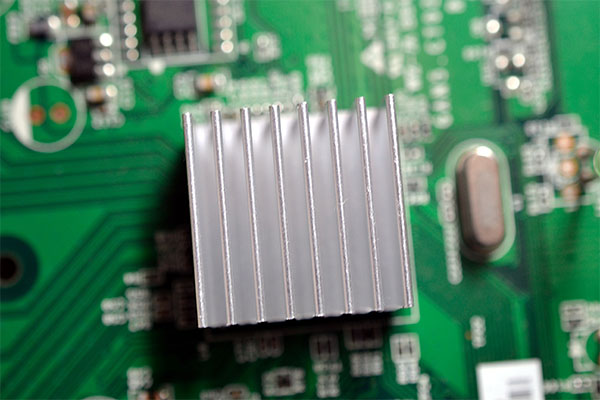
7. CNC Machining Materials: How to Read Material Specifications
When selecting CNC machining materials, understanding material specifications is key. These specifications outline the material’s properties, ensuring you choose the right one for your project. Let’s explore how to read material specifications.
Understanding Material Codes and Grades
Material codes and grades are used to identify materials according to specific standards set by organizations such as ASTM and ISO. These codes typically include information about the material’s composition, strength, and other important characteristics. For example, AISI 304 is a common grade of stainless steel, which is identified by its chemical composition.
Common Material Tests and Standards
Material testing ensures that a material meets specific standards for its intended use. Common tests include tensile strength tests, which measure a material’s resistance to breaking under tension, and hardness tests, which measure a material’s resistance to indentation. Standards like ASTM Lub ISO help guide manufacturers in selecting the right material for specific applications.
8. Best Practices for Machining Metals
Machining metals requires specific techniques to ensure that the material is cut, shaped, and finished properly. Here are some tips for machining different types of metals efficiently and effectively.
Machining Steel
Steel is one of the most common materials used in CNC machining, but it presents challenges due to its hardness. To machine steel, it’s important to use the right cutting tools and set the machine to slower speeds to prevent tool wear. Proper cooling is also critical to dissipate the heat generated during machining and to maintain tool life.
Machining Aluminum
Aluminum is easier to machine than steel, but it can still present challenges due to its softness and tendency to gum up cutting tools. To machine aluminum, use sharp tools, maintain high speeds, and ensure effective cooling to prevent the material from sticking to the tool.
Titanium Machining
Titanium is highly resistant to heat and corrosion, but it is also difficult to machine due to its hardness. To machine titanium, you’ll need high-performance tools and specialized techniques to ensure clean cuts and minimize tool wear. Slow speeds and light cuts are generally recommended.
Copper and Brass Machining
Copper and brass are easier to machine than steel and titanium, but they can be prone to galling (material buildup on the tool) if not properly lubricated. Proper cutting fluid should be used to ensure smooth machining.
9. Best Practices for Machining Plastics
Machining plastics presents unique challenges, primarily due to the material’s tendency to deform under heat. Let’s discuss some best practices to follow when machining plastics.
Choosing the Right Plastic for Your Project
Selecting the right plastic is critical for ensuring that the material performs well during machining. Plastics like ABS and polycarbonate are commonly used for parts that require high impact resistance, while Nylon is used for low-friction applications. PEEK is used in high-performance applications due to its strength and heat resistance.
Cutting Techniques for Plastics
Plastics are often easier to machine than metals, but they can melt or warp if not properly handled. To machine plastics, use sharp tools, slow speeds, and ensure that the material is properly clamped to avoid warping. Coolants and lubricants are often necessary to keep the material from overheating.
Common Challenges in CNC Machining Plastics
Warping and melting are two of the most common challenges when machining plastics. To avoid these issues, it’s crucial to manage cutting speeds and tool pressure carefully. Using the right cooling techniques can help reduce heat buildup and prevent plastic deformation.
10. How CNC Machining Materials Are Tested for Quality
Quality assurance is crucial in CNC machining, as even slight variations in material properties can impact the final product. Here’s a closer look at how materials are tested for quality before machining.
Visual Inspection and Surface Defects
Visual inspections are the first line of defense in identifying defects in materials, such as cracks, scratches, or discolored areas. These defects can compromise the quality of the final product if not addressed early on.
Mechanical Testing
Mechanical tests such as tensile strength tests, hardness tests, I impact tests help determine the material’s suitability for specific applications. These tests measure how the material will behave under stress, pressure, or temperature changes.
Non-Destructive Testing Methods
Non-destructive testing methods like X-ray, ultrasonic, and dye penetrant testing are used to identify internal defects without damaging the material. These tests are especially useful for high-performance materials used in critical applications like aerospace and medical devices.
11. Environmental and Sustainability Considerations in Material Selection
Sustainability is becoming a key concern in the manufacturing sector. Let’s look at how material selection can impact the environment.
Recyclability of CNC Machining Materials
Materials like aluminum are highly recyclable, making them an environmentally friendly option for CNC machining. Recycled aluminum is often used in automotive and aerospace applications, as it offers comparable strength and performance to virgin material.
Sustainable Material Sourcing
Sustainable sourcing of materials ensures that they are produced and harvested responsibly. Companies are increasingly seeking materials that meet environmental standards and certifications to ensure their products have a minimal environmental impact.
Reducing Waste and Improving Efficiency
Efforts to reduce waste include optimizing machining processes to minimize scrap material. Reducing waste not only lowers material costs but also contributes to sustainability by conserving resources and energy. Efficient machining can also improve the overall lifecycle of the material.
12. The Role of Material Certification in CNC Machining
Material certification plays a critical role in ensuring the quality and reliability of materials used in CNC machining. Let’s take a closer look at why certification matters.
Material Certification Processes
Materials used in CNC machining often require certification to verify that they meet specific industry standards. Certification processes like those from ASTM and ISO ensure that materials perform as expected and are suitable for their intended application.
Traceability and Certification for High-Precision Industries
For industries like aerospace and medical devices, material traceability is critical. Certified materials ensure that they meet the stringent requirements for precision and safety, and any potential defects can be traced back to the source.
13. How to Maintain CNC Machining Materials for Longevity and Performance
Maintaining both materials and machinery is essential for long-term success in CNC machining. Here’s how to ensure that both the material and your equipment continue to perform optimally.
Storage and Handling of Materials
Proper storage of materials helps prevent corrosion, contamination, or degradation. Metale should be stored in a dry, cool environment to avoid rusting, while plastics should be kept away from UV light and extreme temperatures to prevent degradation.
Regular Maintenance of CNC Machines
Routine machine maintenance is crucial for preventing wear and tear on both equipment and material. Regularly checking machine components, such as the spindle and cutting tools, helps maintain machining accuracy and performance.
Proper Lubrication and Cooling for Materials
Using the right coolants and lubricants during CNC machining helps extend tool life and maintain the quality of the material. Smarowanie also reduces friction, preventing overheating and material deformation.
14. Troubleshooting Common CNC Machining Material Issues
Even with the best practices in place, problems can arise during the machining process. Here’s how to troubleshoot some of the most common issues related to CNC machining materials.
Tool Wear and Material Choice
Hard materials like titanium and stainless steel can wear out tools quickly, requiring frequent tool changes and slower machining speeds. Choosing the right tool for the material type is critical to prolong tool life.
Surface Finish Problems
Surface finish issues are often caused by incorrect machining speeds, dull tools, or poor material quality. Regular inspection and fine-tuning of machine settings can help improve surface finish quality.
Warping and Deformation
Warping and deformation often occur when materials are not properly handled or when cutting speeds are too fast. To avoid this, make sure the material is securely clamped, and adjust cutting parameters based on the material’s properties.
15. Conclusion: Choosing the Right CNC Machining Material for Your Next Project
When it comes to CNC machining, material selection plays a crucial role in determining the quality and performance of the final product. By understanding the different types of materials available, their properties, and how they impact machining performance, you can make an informed decision that leads to better results. Remember, each material has its own advantages and challenges, so always consider your project requirements carefully. Don’t hesitate to consult with experts or conduct small-scale tests before committing to a specific material for large-scale production.
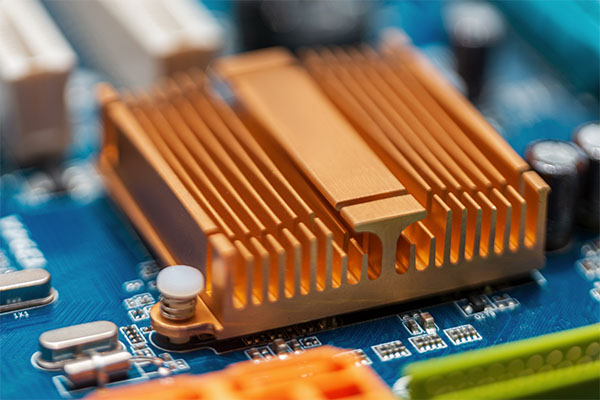
Sekcja FAQ
What’s the Best Material for CNC Machining?
Choosing the best material for CNC machining depends on the specific requirements of your project. Aluminium is often a go-to for applications requiring lightweight and corrosion-resistant materials. Steel is preferred for parts requiring high strength and durability. Tytan is ideal for high-performance applications, while plastics like ABS and polycarbonate are great for lightweight, cost-effective projects. Ultimately, the best material is one that aligns with your mechanical, thermal, and budgetary needs.
Can I Use the Same Tool for All CNC Machining Materials?
Not exactly. Different materials require different tools due to variations in hardness and machining behavior. For example, harder materials like titanium and steel require cutting tools made from carbide Lub ceramic, while softer materials like aluminum and plastics can be machined using high-speed steel tools. Tool coatings also play an important role in extending tool life, particularly when machining tough materials.
Why Are Some CNC Machining Materials More Expensive Than Others?
The cost of CNC machining materials can vary based on factors such as material availability, production methods, I material properties. High-performance materials like titanium I carbon fiber composites tend to be more expensive due to their superior strength, heat resistance, and lightweight properties. On the other hand, common materials like aluminum and steel are more affordable and widely available, making them more cost-effective for many applications.
How Does Material Thickness Affect CNC Machining?
Material thickness affects both the machining process and the type of tooling used. Thicker materials may require additional support during machining to prevent deformation or distortion. They also generally require slower feed rates and higher cutting forces. Thinner materials, however, can be cut at higher speeds but may be more prone to wypaczanie Lub distortion, requiring careful handling and machine adjustments.
Is There a Universal CNC Machining Material for All Applications?
No, there is no one-size-fits-all material for CNC machining. Each material has its own set of advantages and drawbacks based on the intended application. For instance, while steel is strong and durable, it might not be suitable for lightweight applications where aluminum Lub plastics would perform better. The ideal material is one that meets the specific mechanical, thermal, and budget requirements of the project while balancing cost and performance.
Can CNC Machining Materials Be Recycled?
Yes, many CNC machining materials are recyclable. For example, aluminum I steel can be easily recycled and reused, which helps reduce waste and lower production costs. Tworzywa sztuczne like ABS and polycarbonate are also recyclable, though the recycling process can be more complex. Recykling not only makes manufacturing more sustainable but also contributes to the overall cost-effectiveness of the project by reducing raw material expenses.
How Do I Ensure the Quality of CNC Machining Materials?
To ensure the quality of CNC machining materials, you should always choose certified materials that meet industry standards (e.g., ASTM, ISO). Conducting thorough visual inspections I mechanical tests such as tensile and hardness tests is also essential for verifying that the material meets your project requirements. Non-destructive testing methods like X-ray or ultrasonic testing can also be used to identify internal flaws without damaging the material.
How Can I Prevent Warping During CNC Machining?
Deformacja typically occurs when materials are heated unevenly during the machining process. To prevent warping, ensure that the material is securely clamped during machining. Use coolants to dissipate heat and avoid excessive cutting speeds, especially for thinner materials or those with high thermal expansion rates. Additionally, pre-heating materials before machining can help prevent drastic temperature changes that may lead to warping.
What Are the Most Common CNC Machining Materials for Prototypes?
For prototypes, materials that are easy to machine, cost-effective, and readily available are often preferred. Tworzywa sztuczne like ABS I Delrin are common choices because they offer great machinability and can be easily adjusted for design iterations. Aluminium is also a popular choice due to its balance of strength and ease of machining. For high-performance prototypes, stainless steel Lub aluminum alloys may be chosen for their durability.
How Do I Choose the Right CNC Machining Material for My Project?
Choosing the right CNC machining material depends on several factors, including the mechanical properties required (strength, hardness, etc.), thermal resistance, I workability of the material. Consider the cost constraints, the intended use of the part (e.g., aerospace, automotive, medical), and whether the material needs to meet any specific regulatory standards. Consulting with a machining expert or conducting small-scale tests can help ensure the material you choose meets your project’s requirements.