Odlewnictwo ciśnieniowe
Precision die casting helps your product from design to realization
Efficient and high-precision die casting process to meet the needs of multiple industries from prototype to mass production
High Quality Parts
ISO 9001:2015 certified, Vastion delivers precision die casting with rigorous quality inspections at every stage: pre-production, in-production, first article inspection, and pre-delivery.
Fast Lead Time
Vastion’s network of Chinese die-casting manufacturers guarantees high efficiency and quick production. Our advanced, automated facilities are equipped to handle complex custom projects with precision and speed.
Die Casting Specialist
Vastion specializes in custom die casting solutions, delivering enhanced product durability and cost efficiency. With advanced technology and precision machinery, we ensure every component meets high standards of quality, performance, and visual appeal.
Odlewnictwo ciśnieniowe
What is Die Casting
Precision Engineering for Durable and Cost-Effective Metal Components
Die casting is a manufacturing process where molten metal is injected into a mold under high pressure to create precise, durable, and complex metal parts. Known for its efficiency and accuracy, die casting produces components with excellent dimensional stability, smooth surfaces, and minimal post-processing needs. It is widely used in industries such as automotive, electronics, and construction for its cost-effectiveness and ability to produce high-volume, high-quality parts consistently.
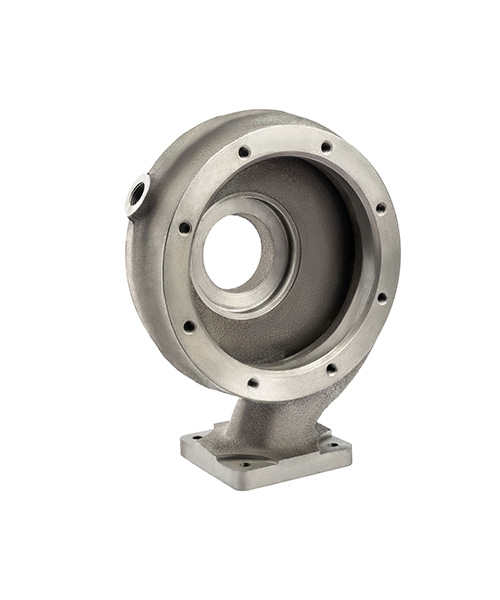
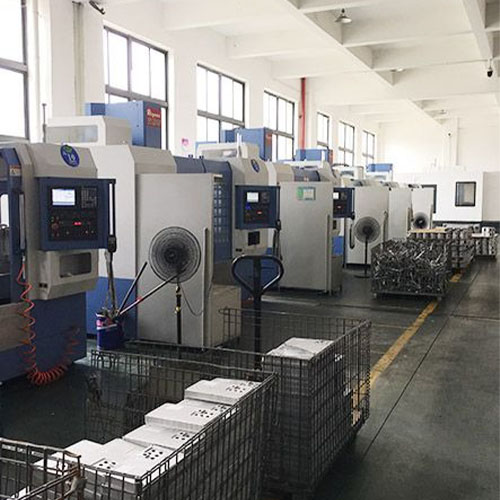
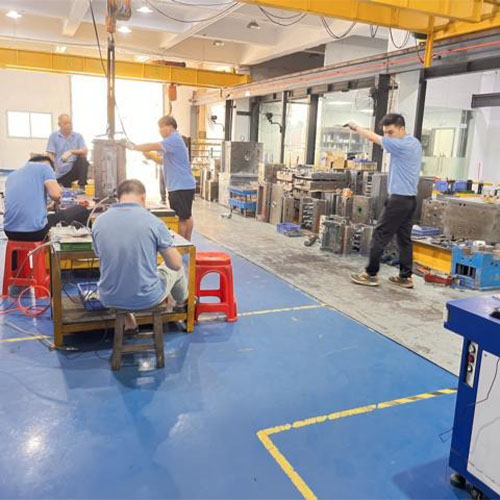
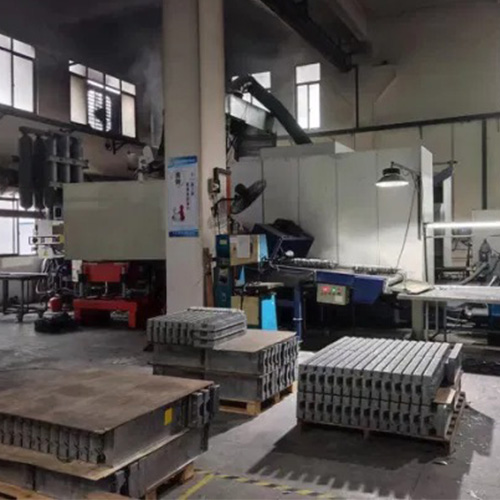
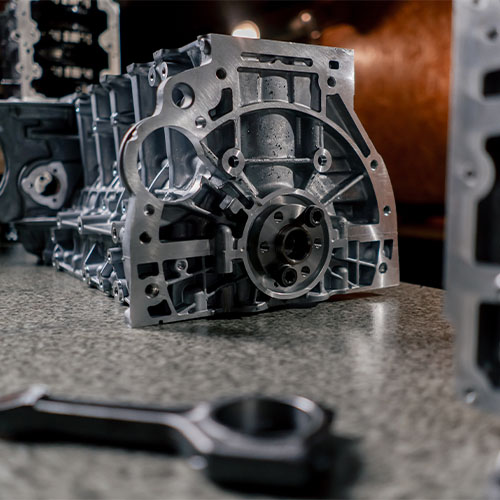
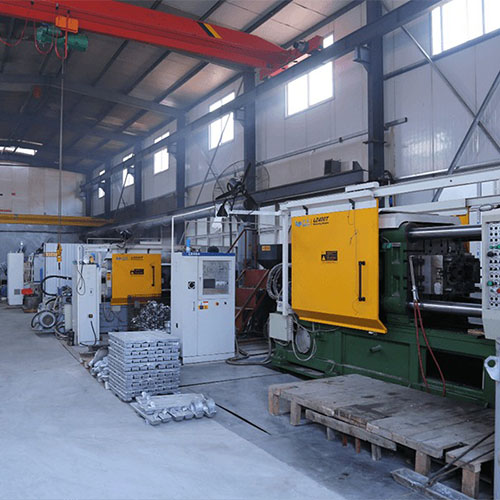
Die Casting Process
Precision Die Casting Solutions for Superior Performance
At Vastion, our die casting process combines advanced technology and precision engineering to produce high-quality, durable components. From mold design to final production, every step is optimized for efficiency, cost-effectiveness, and consistent quality. With our expertise, we deliver reliable solutions tailored to meet your specific requirements.
Every Step From RawMaterials to Finished Products
Step 1: Raw Material Melting
The die casting process begins with melting high-quality metal raw materials in a controlled environment. This step ensures uniform composition and eliminates impurities, resulting in consistent material quality. Temperature control is critical to maintain the metal’s optimal fluidity for injection.
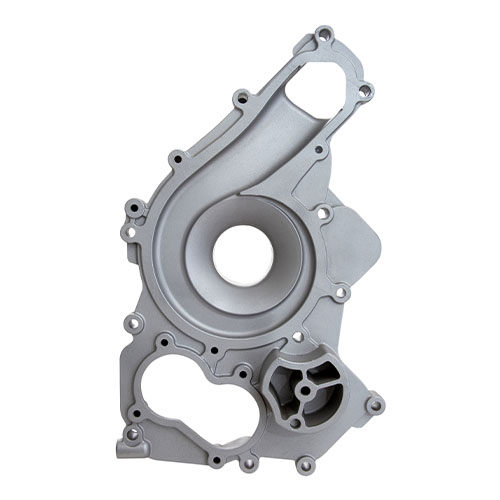
Step 2: High-Pressure Injection into Mold
Once the metal is fully molten, it is injected into precision-engineered molds using advanced automated equipment. The high-pressure injection ensures that the molten metal fills every cavity of the mold quickly and accurately, reducing the risk of defects and ensuring uniform part density.
Step 3: Cooling and Ejection
After the mold is filled, the molten metal rapidly cools and solidifies into the desired shape. The cooling process is carefully controlled to prevent warping or deformation. Once solidified, the product is ejected from the mold with precision, maintaining dimensional stability and structural integrity.
Step 4: Post-Processing and Finishing
The final step involves post-processing to enhance the product’s functionality and appearance. This includes precision machining, polishing, surface coating, and painting. Each component undergoes thorough quality inspections to ensure it meets the required standards for durability, performance, and aesthetics.
At Vastion, our streamlined die casting process guarantees efficiency, precision, and reliability, delivering products that meet the highest industry standards.
Przybory
Die Casting Materials
At Vastion, we offer a wide range of die casting materials, including aluminum, zinc, copper, I magnesium. Each material is selected to meet specific performance, durability, and design requirements.
Aluminum Die Casting
Lightweight and strong, aluminum is ideal for automotive and aerospace parts requiring durability and minimal weight.
Materials:Aluminum ADC12、ADC6、A360、A380
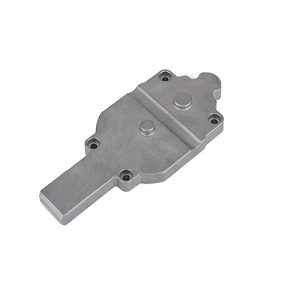
Zinc Die Casting
Strength and durability, excellent precision, and high-tolerance capabilities are ideal for complex designs.
Materials: Zinc Zamak 3, Zamak 5, Zamak 2, ZA8
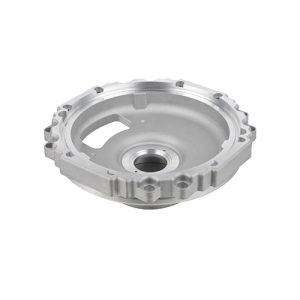
Magnesium Die Casting
The lightest structural metal, magnesium offers an excellent stiffness-to-weight ratio, ideal for weight-sensitive applications.
Materials: Magnesium AZ91D, AM60B
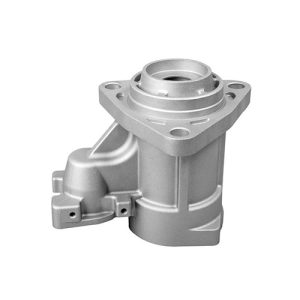
Copper Die Casting
Copper is excellent for parts such as heat sinks and electrical connectors because it conducts heat and electricity very effectively.
Materials: Copper ZQA19-2, ZQA19-4, ZQA19-7, ZQA19-10
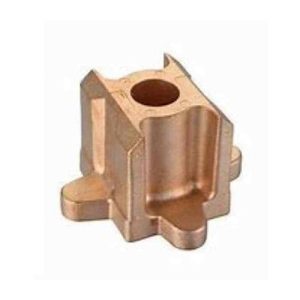
Die Casting Surface Finishing
Choose the Best Surface Treatment for Your Die Casting Parts
Vastion provides advanced surface finishing options, including polishing, sand blasting, plating, powder coating, and painting, brushed finish ensuring enhanced durability, corrosion resistance, and a premium appearance for every die-cast product.
Surface Finishing Advantages
Polishing: Enhances surface smoothness and shine, providing a clean and refined appearance.
Sand Blasting: Improves surface texture, removes impurities, and prepares the surface for further treatment or coating.
Plating: Adds a protective metallic layer, enhancing corrosion resistance and electrical conductivity.
Powder Coating: Delivers a durable, uniform finish with excellent resistance to scratches, chemicals, and fading.
Painting: Offers customizable colors and a protective layer, improving aesthetic appeal and surface durability.
Brushed Finish: Provides a distinctive texture with fine lines, combining an elegant appearance with improved scratch resistance.
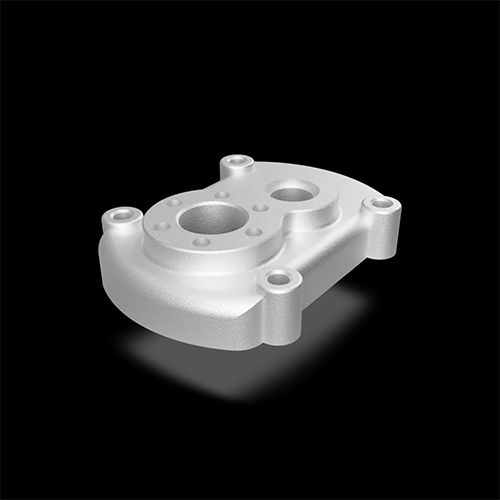
Need custom die casting product?
Capabilities
Our Die Casting Capabilities
Vastion specializes in custom die casting, offering precision-engineered solutions tailored to meet diverse requirements. From design to production, we ensure exceptional quality, efficiency, and reliability in every project.
Nazwa
Opis
Minimum Part Weight
0.017 kg
Maximum Part Weight
12 kg
Maximum Part Weight
12 kg
Minimum Part Size
∅17 mm × 4 mm
Maximum Part Size
300 mm × 650 mm
Minimum Wall Thickness
0.8 mm
Maximum Wall Thickness
12.7 mm
Kontrola jakości
ISO 9001 Certified
Minimum Possible Batch
1000 pcs
CTA
Unlock Precision and Durability with Our Die-Casting Solutions
Partner with us for high-quality die-cast parts that deliver precision, strength, and cost-efficiency. Contact us today for tailored solutions to meet your manufacturing needs!
Types
Types of Die Casting Processes
The choice between hot chamber and cold chamber die casting depends on the melting point and chemical properties of the material, as well as requirements for product precision, production efficiency, and cost. If you provide specific product requirements, I can offer a more tailored recommendation.
Hot Chamber Die Casting
- Process Characteristics: The molten metal is kept in a reservoir (hot chamber) attached to the machine and injected directly into the mold through a gooseneck mechanism.
- Materiały stosowane: Suitable for metals with low melting points that don’t chemically react with the equipment, such as zinc, magnesium, and some low-melting-point aluminum alloys.
- Advantages:
- High injection speed and production efficiency.
- Requires less space for equipment.
- Disadvantages:
- Not suitable for high-melting-point materials (e.g., standard aluminum or copper alloys), as high temperatures can damage the equipment.
Cold Chamber Die Casting
- Process Characteristics: Molten metal is heated in a separate furnace and then manually or mechanically transferred to the injection chamber (cold chamber), where it is injected into the mold.
- Materiały stosowane: Ideal for high-melting-point metals or metals that are corrosive to hot chamber equipment, such as aluminum, copper, and certain high-temperature alloys.
- Advantages:
- Capable of handling high-melting-point metals.
- Longer mold lifespan due to reduced thermal stress.
- Disadvantages:
- Slightly lower production efficiency because the molten metal needs to be transferred.
- More complex operation and equipment.
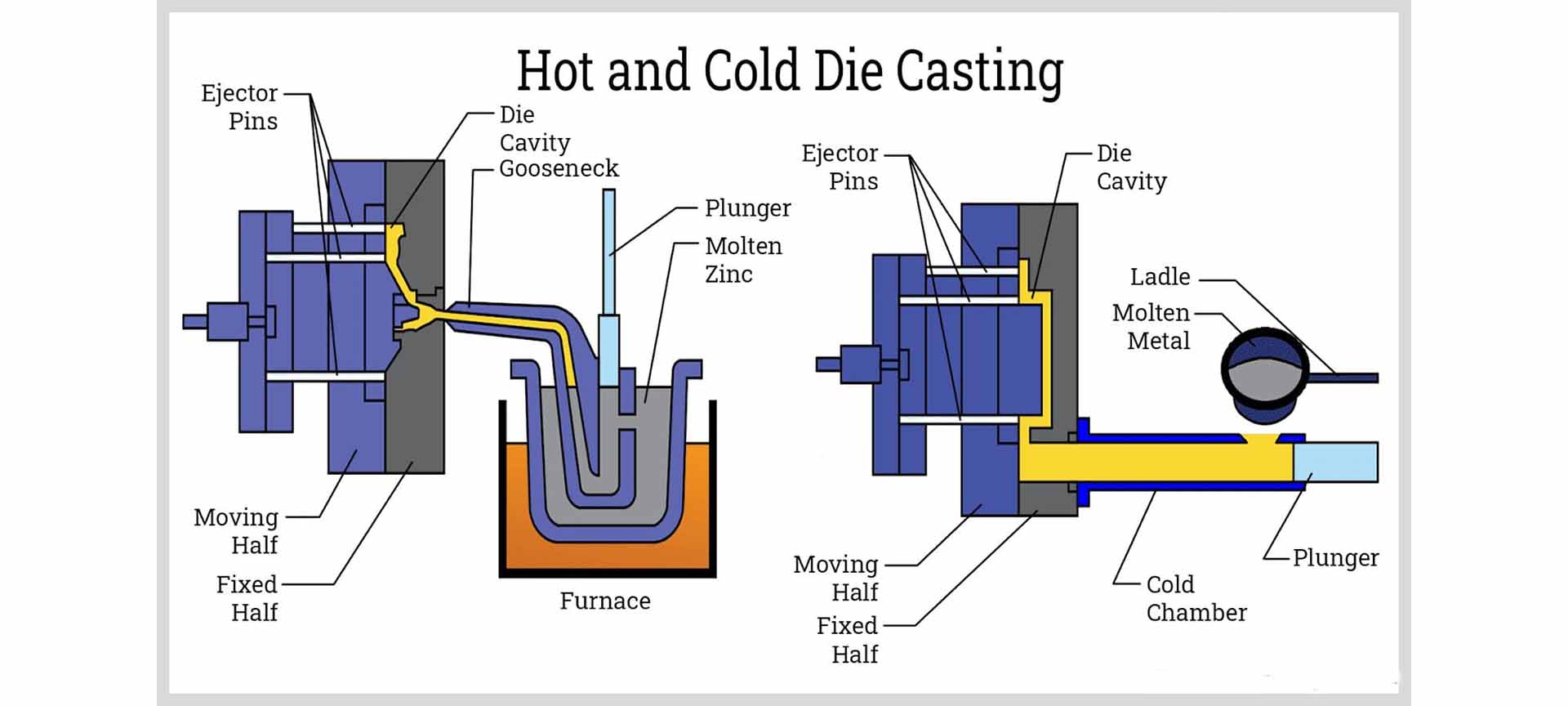
Pros and Cons
Die Casting Advantages and Disadvantages
Understand the strengths and challenges of die casting to make informed manufacturing decisions.
Die Casting Advantages
Die casting offers exceptional precision and consistency, producing complex shapes with tight tolerances and smooth surface finishes. It ensures high production efficiency, allowing mass production with minimal machining requirements. The process is cost-effective for large-scale manufacturing, reducing material waste and labor costs. Additionally, die-cast products are highly durable, offering excellent mechanical strength and resistance to wear and corrosion, making them suitable for demanding applications across various industries.
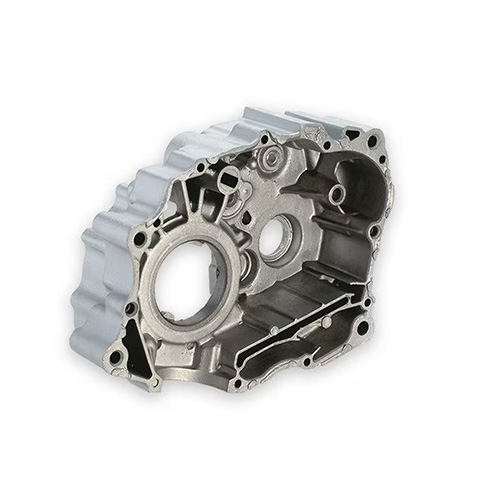
Die Casting Disadvantages
Despite its advantages, die casting has certain limitations. The initial tooling and mold costs are relatively high, making it less economical for low-volume production. The process is generally limited to non-ferrous metals such as aluminum, zinc, and magnesium. Complex internal designs can be challenging to achieve, and certain defects, such as porosity, may occur if not properly managed. Additionally, die-cast parts may require secondary processing for specific finishes or precision requirements, adding extra time and cost.
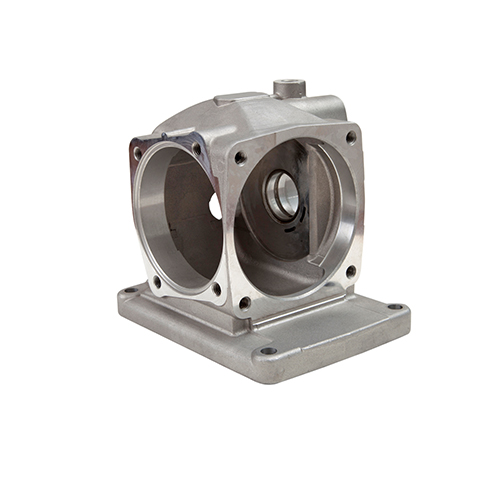
Wideo
Precision in Every Cast: Your Trusted Die Casting Partner
Discover our advanced alloy die casting I metal die casting expertise. From innovative die casting mold design to high-quality production, we deliver reliable solutions for your manufacturing needs.
Często zadawane pytania
Frequently Asked Questions About Die Casting
Explore key insights about die casting products, including their durability and precision. Learn how automotive die casting ensures high performance in vehicle components. Understand the importance of die casting tooling in achieving consistent quality and efficiency. Discover material options and customization possibilities to meet your manufacturing needs.
Die casting products offer excellent precision, strength, and durability, with smooth surface finishes and consistent quality, making them ideal for various industries.
Automotive die casting produces lightweight, high-strength components, such as engine parts and transmission housings, ensuring performance, efficiency, and reliability in vehicles.
Die casting tooling, including molds and dies, is essential for creating accurate and repeatable parts, ensuring efficiency, and reducing material waste during production.
Common materials include aluminum, zinc, and magnesium alloys, chosen for their strength, lightweight properties, and corrosion resistance.
Yes, die casting allows for highly customizable designs to meet unique specifications, ensuring optimal performance across diverse applications.
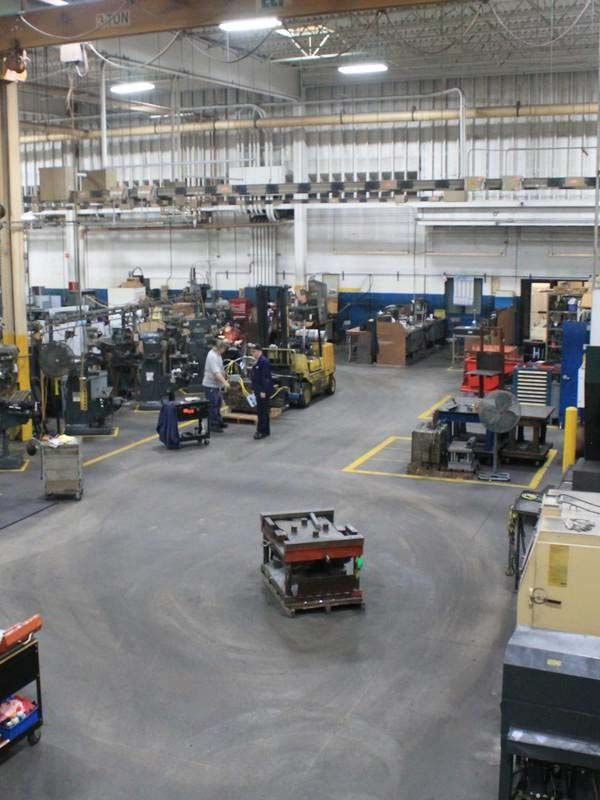
Any questions you want to ask?
Our team is ready to assist with any inquiries about die casting solutions. Contact us today for expert advice and tailored support!