Wstęp
CNC machining is a critical process in the manufacturing of steel parts, offering precision and efficiency. However, achieving optimal results can be tricky. In this article, we’ll walk through the essential strategies, tools, and techniques for perfecting CNC machining specifically for steel parts. From selecting the right materials and tools to troubleshooting common issues, every step plays a crucial role in ensuring the highest quality products. Whether you’re working with carbon steel, stainless steel, or alloy steel, mastering CNC machining will elevate your manufacturing process, reduce costs, and enhance productivity. Oto umowa, mastering these steps will make a significant difference in your operations.
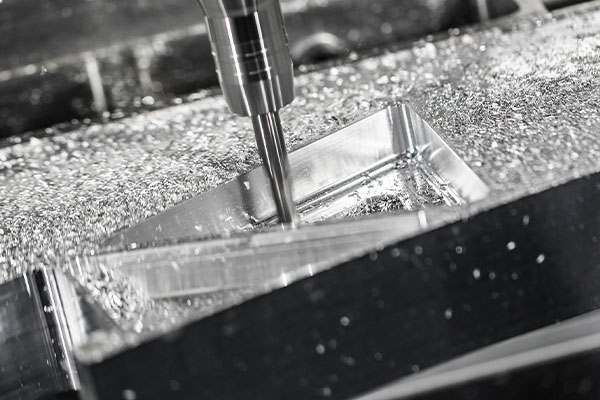
1. Understanding Steel and Its Types for CNC Machining
When it comes to CNC machining, steel is one of the most popular materials due to its strength, durability, and versatility. However, the type of steel used plays a significant role in how well it can be machined. Steel is generally categorized into different types, such as carbon steel, alloy steel, stainless steel, and tool steel. Each has its own unique characteristics that can affect the machining process.
Types of Steel and Their Machining Characteristics
- Carbon Steel: Known for its hardness, carbon steel is commonly used for manufacturing industrial parts. It has good machinability, but it can become brittle when hardened, so careful attention is needed when using this material.
- Alloy Steel: Alloy steel has added elements such as chromium, nickel, and molybdenum. These elements improve hardness and strength, making alloy steel suitable for demanding applications. However, alloy steel can be more challenging to machine, requiring specialized tools and techniques.
- Stal nierdzewna: While stainless steel is corrosion-resistant and durable, it is also more difficult to machine due to its high hardness and tendency to work-harden. The right cutting tools and speeds are essential to avoid excessive tool wear and maintain precision.
- Tool Steel: Known for its ability to maintain strength at high temperatures, tool steel is primarily used for creating cutting tools, dies, and molds. Machining tool steel requires high-performance machines and tools due to its toughness.
Each of these types of steel comes with its own machining challenges, but here’s the deal, understanding these materials and their properties is key to choosing the right cutting techniques and equipment for optimal results.
2. Key Challenges in CNC Machining for Steel
CNC machining steel parts presents several challenges that machinists must overcome. These issues can affect both the efficiency of the process and the quality of the final product. Whether you’re working with alloy steels or stainless steel, being aware of these common challenges is crucial for successful machining.
Heat Generation During Cutting
One of the primary challenges in CNC machining for steel is managing heat. The cutting process generates a significant amount of heat, which can lead to thermal expansion and part distortion. This is especially true for high-carbon steels and stainless steels, which can become brittle if overheated. The right coolant and lubrication can help minimize heat buildup, but effective machine settings and cutting parameters are essential to manage heat effectively.
Tool Wear and Durability
Steel is tough, which means tools wear down faster when machining steel parts. Cutting tools made of carbide or high-speed steel (HSS) tend to degrade quickly when exposed to high temperatures and the abrasiveness of steel. Overcoming this requires precise tool selection and proper tool maintenance. The key here is to choose the best cutting tools for steel, adjust speeds and feeds properly, and regularly check for tool wear to maintain the highest precision.
Surface Finish Quality
Achieving a smooth surface finish is another challenge in steel machining. Steel tends to leave rough, inconsistent surfaces that require secondary operations like polishing or grinding. To prevent this, adjusting the feed rate and cutting parameters is important. Tool choice also plays a crucial role in achieving high-quality finishes, as tools with proper geometry and coating can reduce surface defects.
3. Selecting the Right CNC Machine for Steel Machining
Choosing the right CNC machine is essential for achieving precision and efficiency when machining steel parts. Different CNC machines have varying capabilities depending on the complexity of the part and the type of steel being machined.
CNC Machine Type: Milling vs. Turning
- Milling Machines: CNC milling machines are commonly used for steel parts with complex geometries. These machines are capable of handling large cuts and fine details, making them suitable for both rough and finish machining.
- Turning Machines: CNC turning is ideal for parts with circular geometries, such as shafts or discs. A lathe machine provides high precision and is often used for producing parts with tight tolerances.
Machine Size and Power
The size and power of the CNC machine will affect the speed and precision with which it can handle steel parts. Larger machines are required for heavy-duty machining and large parts, while smaller machines are better suited for precision work. The machine’s horsepower and spindle speed are crucial factors when selecting equipment for steel machining.
4. Choosing the Best Cutting Tools for Steel
The choice of cutting tools is one of the most critical decisions in CNC machining, particularly when working with tough materials like steel. The correct tool selection can extend tool life, improve surface finishes, and reduce machining times.
Tool Material and Coatings
- Carbide Tools: Carbide cutting tools are the preferred choice for machining steel due to their durability and heat resistance. They can handle high cutting speeds, making them ideal for mass production.
- High-Speed Steel (HSS): While not as durable as carbide, HSS tools are commonly used for lighter operations or for machining softer steels.
- Tool Coatings: Applying coatings like titanium nitride (TiN) or titanium aluminum nitride (TiAlN) to the cutting tools can significantly improve their performance. These coatings reduce friction and increase tool life, which is crucial when machining steel.
Tool Geometry and Design
The geometry of the cutting tool plays a crucial role in determining the quality of the finished part. A tool with a proper cutting edge angle ensures efficient cutting and minimizes vibration. The design of the tool, including the number of flutes, also influences chip removal and heat dissipation, both of which are important when machining steel.
5. Optimizing CNC Machine Settings for Steel
Proper machine settings are essential for achieving optimal results when machining steel parts. Adjusting parameters such as cutting speed, feed rate, and depth of cut can drastically affect both the efficiency and quality of the process.
Speed and Feed Rate
- Cutting Speed: The cutting speed refers to the rate at which the cutting tool engages with the steel. Higher speeds result in faster production times but can cause excessive heat generation if not controlled.
- Feed Rate: The feed rate determines how fast the tool moves through the steel. A higher feed rate can lead to faster cutting but may reduce the surface finish quality. Properly balancing these parameters is essential for achieving the best results.
Depth of Cut and Step-over
The depth of cut refers to how deep the tool penetrates into the material with each pass. Too deep a cut can cause excessive strain on the tool and machine, while too shallow a cut can increase machining time. Step-over is the lateral movement of the tool as it cuts, and this must be optimized to achieve both efficient material removal and a smooth finish.
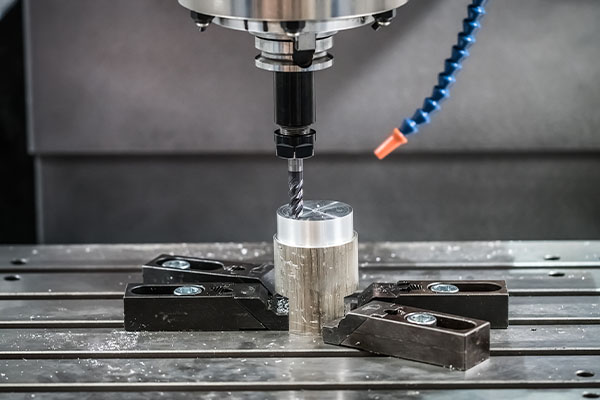
6. Coolants and Lubricants: Minimizing Heat and Tool Wear
Coolants and lubricants are vital when CNC machining steel. They reduce heat buildup, extend tool life, and improve part quality.
Coolants and Their Role in Steel Machining
The primary function of coolants is to reduce the temperature of both the cutting tool and the steel part. This prevents thermal expansion, tool wear, and surface finish defects. Water-based coolants are popular due to their cost-effectiveness, but oil-based coolants offer better lubrication.
Lubricants for Steel
Lubricants serve to reduce friction between the tool and the steel, improving cutting performance. Dry machining is also an option for specific steel grades, though it generally results in higher tool wear. Using a suitable lubricant is essential for achieving a balance between cutting speed, tool life, and surface finish.
7. Preventing Heat Distortion and Warping
Heat buildup is one of the most common causes of distortion and warping when machining steel. As the cutting tool interacts with the steel, excessive heat can cause expansion, resulting in a change in the dimensions of the part. Effective heat management strategies are essential for preventing such issues.
Thermal Expansion and Control
Steel expands when heated, and this can affect the dimensional accuracy of machined parts. Controlling heat is achieved through a combination of coolant use, machine settings, and cutting techniques. Cooling systems that apply coolant directly to the cutting area help maintain a consistent temperature, while maintaining optimal cutting speeds reduces excessive heat generation.
Best Practices to Minimize Warping
Proper fixturing and workholding techniques also help to minimize part distortion. By securing the steel part firmly during machining, vibrations and thermal deformations are reduced, ensuring that the part maintains its intended shape.
8. Achieving Precision in CNC Machining for Steel Parts
Precision is one of the main reasons CNC machining is preferred for steel parts. Whether you’re machining a simple component or a complex part, accuracy is crucial.
Tolerance Requirements
Steel parts often require tight tolerances, especially in industries such as aerospace and automotive. CNC machines are equipped with high-precision controls to ensure that parts are machined within these tight specifications. Maintaining consistent tool offsets I regular calibration of the CNC machine are key factors in achieving this level of precision.
On-machine Probes and Measurement Tools
Using on-machine probes to measure parts during machining is a key strategy for ensuring precyzja. These probes provide real-time feedback, allowing the machinist to adjust the process on the fly, which is particularly useful when working with large production runs.
9. CNC Machining Strategies for Complex Steel Parts
CNC machining is well-suited for producing complex steel parts that traditional machining methods might struggle with. When dealing with intricate geometries, using multi-axis CNC machines offers significant advantages.
Techniques for Complex Geometries
Parts with undercuts, deep pockets, and other challenging features require advanced machining strategies. Multi-axis machines allow the tool to approach the workpiece from multiple angles, significantly improving machining accuracy and reducing the need for re-fixturing.
Multi-axis Machining and Fixture Design
Using multi-axis machines can increase part complexity, but it also allows for more precise cutting and finishing. Proper fixture design ensures that the part is held securely throughout the machining process, minimizing errors caused by part movement.
10. Troubleshooting Common CNC Machining Problems for Steel Parts
Despite following best practices, issues may still arise during CNC machining for steel. Identifying and resolving common problems promptly can save time and resources.
Vibrations and Chatter
Chatter is one of the most common issues in CNC machining. This phenomenon occurs when the cutting tool vibrates during the cutting process, which can negatively impact the surface finish and dimensional accuracy. Adjusting feed rates, using stiffer tooling, or employing damping systems can help eliminate vibrations.
Tool Deflection
Tool deflection is caused when the cutting tool bends or shifts under pressure. This leads to inaccuracies and poor finishes. To reduce tool deflection, use tools with stronger materials, and adjust cutting parameters to reduce pressure on the tool.
11. Advanced Techniques for Perfecting CNC Machining for Steel
As technology advances, there are increasingly sophisticated methods available to further improve CNC machining for steel. These advanced techniques help overcome limitations and optimize both the speed and quality of production.
High-Speed Machining (HSM)
High-speed machining (HSM) is a method that focuses on increasing cutting speeds while maintaining precision. By using high-performance machines and cutting tools, HSM can significantly reduce machining times and enhance the surface finish. However, it requires specialized equipment and the right materials to handle the increased cutting forces and speeds. Oto umowa, adopting HSM can lead to substantial cost savings and productivity gains, particularly for high-volume production runs of steel parts.
Hard Milling and Hard Turning
Hard milling and hard turning are specialized techniques used for machining hardened steel. Traditional methods like grinding are often employed to finish hardened steel parts, but hard milling and turning allow for efficient removal of material without compromising part integrity. Hard milling uses a milling cutter to cut through materials that have been heat-treated to higher hardness levels, while hard turning uses CNC lathes to achieve similar results. These methods allow for quicker, more accurate machining of steel parts, reducing overall lead times.
CNC Grinding
CNC grinding is often used as a complementary process to milling and turning. It offers superior precision when machining steel parts that require extremely tight tolerances and fine surface finishes. Using specialized grinding wheels, CNC grinding machines can smooth out surfaces that may have been left rough after milling or turning, achieving finishes as fine as 0.0001 inches. Incorporating grinding into the manufacturing process allows for a higher degree of precision and finish quality, especially for parts with intricate details.
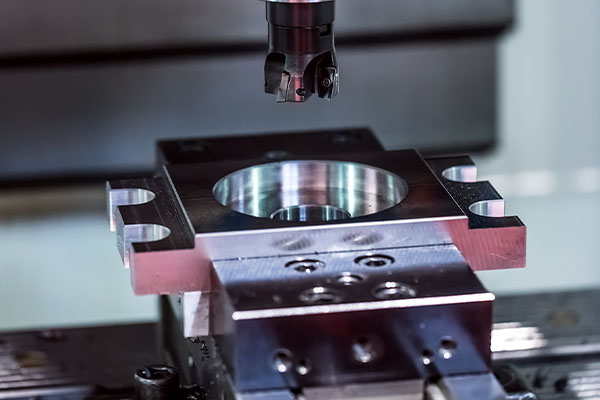
12. Quality Control and Inspection for CNC Machined Steel Parts
Maintaining high-quality standards is a critical aspect of CNC machining. Regular inspection and quality control are necessary to ensure that parts meet the required specifications and tolerances.
Visual Inspections
A visual inspection is often the first step in quality control. Look for surface defects, such as scratches, dents, or tool marks, that may have occurred during the machining process. A visual inspection can also identify any signs of overheating, which can cause discoloration or warping of the steel part. Oto umowa, while a visual inspection can catch obvious defects, it’s just the beginning of ensuring that a steel part meets the desired specifications.
Dimensional Inspection
For more precise checks, dimensional inspection is necessary. Tools like calipers, micrometers, and CMMs (Coordinate Measuring Machines) are used to measure critical dimensions of the part. These inspections ensure that the tolerances required for the part are met and that the part fits within the parameters set by the design.
Non-Destructive Testing (NDT)
For critical applications, non-destructive testing (NDT) is used to detect hidden defects without damaging the part. Methods such as ultrasonic testing, X-ray inspection, I dye penetrant testing are used to check the integrity of the part. NDT ensures that steel parts are free of internal flaws, which could compromise their performance in real-world applications.
13. Sustainability in CNC Machining for Steel Parts
The environmental impact of CNC machining is a growing concern in the manufacturing industry. As the demand for sustainable practices increases, manufacturers are adopting new methods to reduce waste, conserve energy, and minimize the use of harmful chemicals.
Reducing Waste
Efficient machining techniques are essential for minimizing scrap material. By optimizing cutting parameters such as speed and feed rates, manufacturers can significantly reduce material waste. Oto umowa, using high-quality, durable tools and maximizing tool life also helps reduce scrap material, resulting in more sustainable production processes.
Efektywność energetyczna
CNC machining uses a considerable amount of energy, especially when machining tough materials like steel. Manufacturers are adopting more energy-efficient CNC machines, which reduce electricity consumption while maintaining high performance. Additionally, using cutting techniques like high-speed machining helps minimize machining time and, consequently, energy use.
Eco-friendly Cutting Fluids
Traditional cutting fluids are often petroleum-based and can be harmful to the environment. However, there are now eco-friendly cutting fluids available that are biodegradable and non-toxic. These fluids reduce the environmental impact of the machining process while still providing the necessary cooling and lubrication for effective steel machining.
14. The Future of CNC Machining for Steel Parts
The CNC machining industry continues to evolve with the development of new technologies and materials. The future promises even more advanced solutions for machining steel parts, improving efficiency, precision, and sustainability.
Automation and AI in CNC Machining
Automation is changing the landscape of CNC machining for steel. AI and robotics are increasingly being used to optimize machining processes, monitor tool wear, and make real-time adjustments to cutting parameters. Automation helps reduce human error, improve precision, and streamline the production process, leading to lower costs and faster turnaround times.
Advances in CNC Machine Technology
New CNC machines are being developed with improved capabilities, such as higher spindle speeds, increased automation, and enhanced precision. These advances will help manufacturers meet the growing demand for complex, high-quality steel parts. Oto umowa, keeping up with these advancements allows manufacturers to stay competitive and maintain high standards in steel machining.
Emerging Materials
New steel alloys and materials are constantly being developed. These materials offer unique benefits, such as increased strength, resistance to corrosion, and improved machinability. As these new materials become more widespread, CNC machining will need to evolve to accommodate them, requiring new tools and techniques to achieve the best results.
15. Conclusion
In conclusion, perfecting CNC machining for steel parts is a multi-faceted process that requires attention to detail and a thorough understanding of materials, tools, and techniques. From choosing the right cutting tools and machine settings to ensuring proper quality control and incorporating sustainability practices, every step plays a critical role in producing high-quality steel parts. By following the strategies outlined in this guide, manufacturers can improve their CNC machining processes, reduce costs, and deliver precise, durable products. Whether you’re machining carbon steel, stainless steel, or alloy steel, the key to success lies in mastering the right techniques for the job.
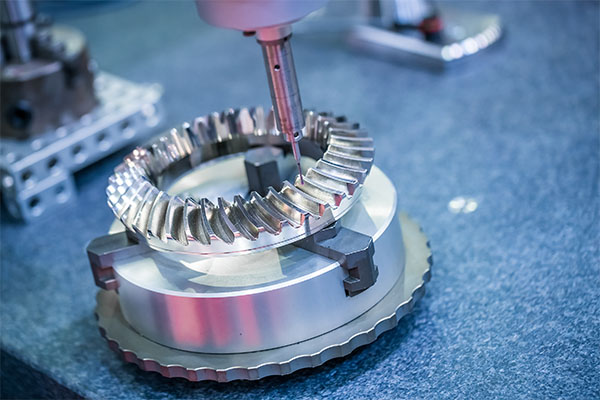
Sekcja FAQ
- What is the most common type of steel used in CNC machining?
- Carbon steel is often the most commonly used material in CNC machining due to its versatility, strength, and relatively low cost. Alloy steel and stainless steel are also used for specialized applications that require more specific properties, such as corrosion resistance or high strength.
- How can I reduce tool wear when machining steel?
- To reduce tool wear, it’s essential to use the correct cutting speeds, feeds, and cooling techniques. Choosing high-quality cutting tools, applying proper tool coatings, and regularly maintaining your machines will also help extend tool life.
- What are the best practices for achieving a smooth surface finish in steel parts?
- Use the appropriate cutting tools with sharp edges and correct geometry, maintain optimal cutting speeds and feeds, and ensure proper cooling during the machining process. Post-machining techniques like grinding or polishing may also be needed for very fine finishes.
- How do I handle thermal expansion when machining steel?
- Thermal expansion can be managed by using effective cooling systems to keep the steel part at a consistent temperature. Also, adjusting cutting parameters to minimize heat generation and using fixturing techniques that reduce the part’s movement can help control thermal distortion.
- What should I do if my CNC machine is causing vibrations during steel machining?
- Vibrations can be reduced by adjusting the feed rate and cutting speed, using stiffer tooling, and ensuring that the machine is properly calibrated. Damping systems or additional support for the machine can also help eliminate vibrations and improve the surface finish and accuracy.