Wstęp
Manufacturing errors are a common challenge in the production industry, affecting product quality, cost efficiency, and customer satisfaction. Tolerances play a crucial role in the manufacturing process, determining the acceptable limits for a product’s dimensions and ensuring that parts fit and function correctly. In this article, we will explore how to reduce manufacturing errors and control tolerances effectively, keeping the production process smooth and efficient.
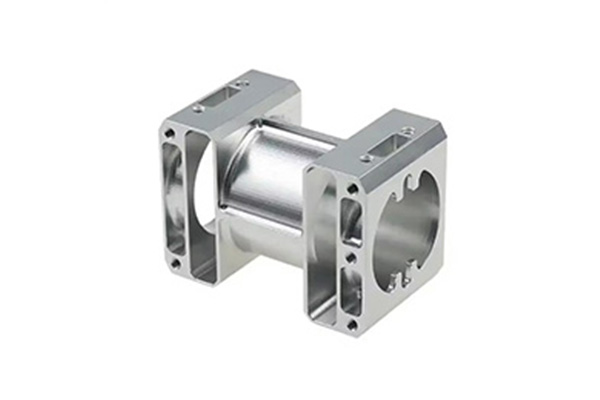
1. What Are Manufacturing Errors?
Manufacturing errors are discrepancies that occur during the production process, resulting in parts that don’t meet the specified design or functional requirements. These errors can be caused by various factors, including human mistakes, machine malfunctions, or environmental conditions. But here’s the kicker: even the smallest errors can lead to significant consequences, such as defective products, increased costs, and production delays.
There are several types of manufacturing errors, including dimensional errors, material defects, and process-related issues. Dimensional errors refer to deviations in size, shape, or geometry, often caused by inaccurate measurements or machine calibration issues. Material defects, on the other hand, occur when raw materials don’t meet the required standards, leading to weak or faulty products. Process-related errors involve problems with the production process itself, such as incorrect settings, misalignment, or inadequate training.
In manufacturing, reducing these errors is essential to maintaining quality and efficiency. For example, using high-precision machinery, investing in quality control systems, and conducting regular equipment maintenance can help mitigate dimensional errors. Additionally, working with reliable suppliers who provide quality materials and implementing stringent quality assurance processes can minimize material defects.
Manufacturing errors not only affect product quality but can also have financial implications. Inaccurate parts or defective products often result in rework, scrap, or returns, all of which contribute to higher production costs and decreased profitability. Addressing these issues is crucial for improving operational efficiency and customer satisfaction.
Manufacturing Errors | Causes | Konsekwencje |
---|---|---|
Dimensional errors | Inaccurate measurements, machine malfunctions | Reduced product quality, increased rework |
Material defects | Subpar raw materials, poor quality control | Weak products, increased returns |
Process-related errors | Incorrect settings, misalignment, lack of training | Increased costs, production delays |
2. Why Are Manufacturing Errors a Concern in the Industry?
Manufacturing errors can have a significant impact on the overall production process. But here’s the real story: they don’t just affect the product itself; they can disrupt the entire supply chain, increase costs, and damage the company’s reputation. The implications of manufacturing errors extend beyond production, affecting customer satisfaction and long-term business success.
One of the primary concerns with manufacturing errors is their impact on product quality and safety. If an error occurs during production, it can lead to defects that make the product unsafe to use or fail to meet quality standards. For example, if a car part is manufactured incorrectly, it can jeopardize the vehicle’s performance and safety. This could lead to costly recalls, legal consequences, and damage to the brand’s reputation.
Another concern is the effect on production costs and profitability. Errors in manufacturing often result in waste, rework, or the need to scrap parts. These additional costs can quickly add up, eroding profit margins. In a highly competitive industry, the ability to minimize manufacturing errors is crucial for maintaining cost-effectiveness and staying competitive.
What’s the real story here? Manufacturing errors can also damage customer trust. When customers receive defective products or experience delays due to production errors, they may lose confidence in the brand and take their business elsewhere. Consistent product quality is key to retaining loyal customers and maintaining a positive reputation in the market.
Manufacturing Error Impact | Product Quality | Production Costs | Customer Trust |
---|---|---|---|
Dimensional errors | Decreased functionality, potential safety hazards | Increased rework, scrap | Loss of customer confidence |
Material defects | Weak, unsafe products | Increased returns, replacements | Negative reviews, reputation damage |
Process-related errors | Delays, production stoppages | Increased labor costs, downtime | Lost business, customer dissatisfaction |
3. How Do Manufacturing Errors Affect Tolerance Control?
Tolerance control is an essential aspect of the manufacturing process, as it ensures that parts and components fit and function as intended. But here’s the thing: manufacturing errors can directly affect tolerance control, leading to parts that do not meet the required specifications. This can result in parts that are too loose or too tight, affecting their ability to perform correctly in the final product.
Tolerance refers to the allowable deviation from a specified dimension or feature. In manufacturing, maintaining tight tolerances is critical for ensuring that parts fit together correctly and function as expected. For example, in aerospace manufacturing, where precision is crucial, a slight variation in tolerance can cause parts to fail or malfunction. Manufacturing errors, such as dimensional inaccuracies or misalignment, can compromise tolerance control and lead to parts that don’t meet quality standards.
What’s the kicker here? When manufacturing errors impact tolerance control, they often require additional inspection, adjustment, or rework. This not only increases production time but also adds to the cost. In some cases, the errors may be so significant that the parts need to be scrapped entirely, resulting in wasted materials and resources.
To prevent manufacturing errors from affecting tolerance control, manufacturers must implement strict quality control measures and use advanced tools for precise measurement and inspection. Utilizing automated machinery with built-in sensors and real-time monitoring can help ensure that tolerances are maintained throughout the production process.
Tolerance Control Challenges | Przyczyna | Rozwiązanie |
---|---|---|
Dimensional inaccuracies | Machine malfunctions, poor calibration | Regular machine maintenance, precise calibration |
Misalignment | Improper assembly, machine settings | Use of alignment tools, automated systems |
Material defects | Variations in material properties | Working with trusted suppliers, material testing |
4. What Are the Key Types of Tolerances in Manufacturing?
There are several types of tolerances used in manufacturing to define the acceptable limits of variation in a part’s dimensions or features. But here’s the thing: understanding these types of tolerances is essential for ensuring that parts meet the required specifications and function as intended. Let’s break it down.
The most common types of tolerances in manufacturing are dimensional tolerances, geometric tolerances, and surface finish tolerances. Dimensional tolerances specify the allowable variation in the size of a part. For example, a part may be specified to be 50 mm ± 0.1 mm, meaning that it can vary by 0.1 mm in either direction. Geometric tolerances define the acceptable variation in the shape, orientation, and location of features on a part. Surface finish tolerances, on the other hand, specify the acceptable roughness or smoothness of a surface.
What’s the real story? Tolerances are critical in ensuring that parts fit together properly during assembly. For instance, in the automotive industry, where components must be assembled precisely to ensure proper function, dimensional and geometric tolerances are especially important. Even a small deviation in tolerance can result in parts that don’t fit, causing functionality issues or assembly difficulties.
To manage tolerances effectively, manufacturers use tools like computer-aided design (CAD) software and precision measurement instruments. CAD software helps designers create detailed models with specific tolerance requirements, while precision measurement tools like micrometers and calipers ensure that parts meet these specifications.
Type of Tolerance | Definition | Example | Aplikacja |
---|---|---|---|
Dimensional tolerance | Variation in part size | 50 mm ± 0.1 mm | Ensures correct part fit |
Geometric tolerance | Variation in shape, orientation, or location | Flatness, parallelism | Used in precision assembly |
Surface finish tolerance | Roughness or smoothness of surface | Ra 0.8 µm | Ensures proper function and appearance |
5. How Can You Measure and Assess Manufacturing Errors?
Accurate measurement is key to detecting and assessing manufacturing errors. But here’s the kicker: without the right tools and methods, it can be difficult to pinpoint exactly where the errors are occurring in the production process. To ensure that parts meet quality standards, manufacturers must use precise measurement instruments and assessment techniques.
Common tools for measuring manufacturing errors include calipers, micrometers, and coordinate measuring machines (CMM). Calipers are used to measure the external dimensions of a part, while micrometers provide more precise measurements for smaller dimensions. CMMs, on the other hand, are highly accurate machines that can measure the dimensions of parts in three-dimensional space, detecting deviations from the desired specifications.
Another important aspect of error assessment is statistical analysis. By collecting data on the dimensions of parts throughout the production process, manufacturers can identify trends and patterns that indicate potential errors. This data can then be used to make adjustments and improve the process to prevent further errors.
What’s the real story here? Effective error measurement and assessment require a combination of advanced tools, skilled operators, and a solid understanding of the manufacturing process. Manufacturers who invest in high-quality measurement tools and continuous monitoring systems can significantly reduce the likelihood of errors and improve overall production quality.
Measurement Tools | Zamiar | Accuracy | Aplikacja |
---|---|---|---|
Calipers | Measure external dimensions | ±0.02 mm | Used for general measurements |
Micrometers | Measure small dimensions | ±0.001 mm | Used for high-precision measurements |
CMM (Coordinate Measuring Machine) | 3D measurement of parts | ±0.002 mm | Used for complex geometries |
6. What Role Does GD\&T Play in Reducing Manufacturing Errors?
Geometric Dimensioning and Tolerancing (GD\&T) is a powerful tool for ensuring that parts are manufactured with the right dimensions and functional characteristics. But here’s the thing: without GD\&T, manufacturing errors can slip through the cracks, leading to parts that don’t fit or function properly.
GD\&T provides a standardized system for defining the allowable tolerances of geometric features on a part. It uses symbols to define parameters such as size, location, orientation, and form, allowing manufacturers to specify exactly how parts should be produced. By using GD\&T, manufacturers can reduce the likelihood of errors by ensuring that everyone involved in the production process understands the tolerance requirements clearly.
What’s the kicker here? GD\&T also helps manufacturers identify the most critical features of a part that must meet strict tolerance requirements. For example, in aerospace manufacturing, where precision is paramount, GD\&T ensures that parts meet the required specifications for performance and safety. GD\&T also helps manufacturers minimize the risk of costly rework or scrap by providing clear and precise instructions for production.
By incorporating GD\&T into the design and manufacturing process, companies can improve communication, reduce errors, and increase efficiency. Using GD\&T not only helps to reduce manufacturing errors but also enhances the overall quality and consistency of the products.
GD\&T Feature | Zamiar | Example |
---|---|---|
Size tolerance | Specifies allowable variation in size | 50 mm ± 0.1 mm |
Location tolerance | Specifies allowable variation in location | Position of a hole relative to a feature |
Form tolerance | Specifies allowable variation in shape | Flatness, roundness |
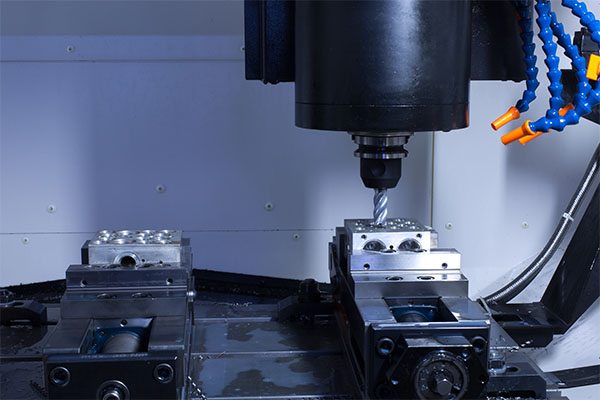
7. How Can You Implement Statistical Process Control (SPC) to Reduce Errors?
Statistical Process Control (SPC) is a method used to monitor and control a process through statistical methods. But here’s the kicker: SPC helps manufacturers keep track of their production process in real-time, identifying when things go wrong before they become significant issues. It’s a powerful tool for reducing manufacturing errors and ensuring that products meet quality standards.
SPC involves the use of control charts, process capability analysis, and various statistical tools to monitor the consistency of a manufacturing process. The goal is to detect any variation in the process that could lead to errors, allowing for corrective actions to be taken before defects occur. For instance, a control chart can show when a production line starts to deviate from the desired parameters, signaling that an issue might arise. This early warning system is essential in preventing significant manufacturing errors.
One of the most effective ways SPC reduces errors is by providing continuous data on the performance of machines and processes. With real-time data, operators can identify issues before they lead to defective parts. For example, if a machine starts producing parts that fall outside of tolerance limits, SPC can alert the operator to adjust the machine settings immediately. This proactive approach helps minimize the chances of errors going unnoticed and reduces waste.
What’s the real story? By integrating SPC into the manufacturing process, companies can ensure that their production lines remain stable, consistent, and within acceptable limits. Over time, this reduces the variability of products, lowers scrap rates, and enhances overall product quality.
SPC Tool | Zamiar | Korzyści | Example |
---|---|---|---|
Control charts | Monitor process variation | Detect deviations early | Control chart tracking part dimensions |
Process capability analysis | Measure process performance | Identify areas for improvement | Evaluating machine tolerance capabilities |
Statistical analysis | Identify patterns in data | Reduce errors, improve efficiency | Analyzing data for trends in defects |
8. What Are the Best Practices for Quality Assurance in Manufacturing?
Quality assurance (QA) is the backbone of any manufacturing process. It ensures that products are consistently produced according to specified standards and free from defects. But here’s the thing: establishing effective quality assurance practices isn’t just about checking for defects at the end of the production line; it’s about building quality into every step of the manufacturing process.
Best practices for quality assurance include clear documentation of processes, frequent inspections, and employee training. When you document every step of the production process, it becomes easier to identify where errors might occur. Regular inspections are also crucial for catching defects early, rather than waiting until the end of production. Training employees on quality control procedures helps ensure that they understand their role in maintaining high standards, reducing the likelihood of errors due to oversight or lack of knowledge.
What’s the kicker? Integrating automated quality checks during production can also help reduce errors. Automated inspection systems, such as machine vision and laser scanning, can quickly detect discrepancies in parts, reducing the chance of defective products making it to the next stage of production. These systems are often faster and more accurate than human inspection, ensuring a higher level of quality control.
The key to successful QA is consistency. By maintaining standardized procedures, training employees, and using technology to assist in inspections, manufacturers can significantly reduce errors and improve the overall quality of their products.
QA Best Practice | Zamiar | Korzyści | Example |
---|---|---|---|
Process documentation | Record production steps | Standardize operations | Standard operating procedures (SOPs) |
Regular inspections | Identify defects early | Minimize defects, improve quality | Visual inspections, in-line testing |
Employee training | Educate workers on quality standards | Reduce errors, improve efficiency | Hands-on training for quality checks |
9. How Do You Handle and Correct Manufacturing Errors Once Detected?
It’s one thing to detect manufacturing errors; it’s another to address them effectively. But here’s the deal: handling and correcting manufacturing errors requires a structured approach to identify the root cause, implement corrective actions, and prevent future occurrences. This is where root cause analysis (RCA) and corrective and preventive actions (CAPA) come into play.
Root cause analysis involves investigating an error to determine the underlying cause. Rather than simply fixing the immediate problem, RCA helps manufacturers understand why the error occurred in the first place. This could involve reviewing machine settings, materials used, or even the process itself. Once the root cause is identified, corrective actions are taken to eliminate the error, followed by preventive measures to ensure it doesn’t happen again.
What’s the kicker here? Corrective and preventive actions (CAPA) are critical for continuous improvement. After identifying the root cause, manufacturers should implement CAPA procedures that focus on correcting the issue immediately and preventing its recurrence in the future. This might include changes in machine settings, retooling the production process, or updating training for operators.
By effectively handling and correcting errors, manufacturers can prevent costly rework, reduce waste, and improve the overall quality of their products. This structured approach is essential for building a more efficient and error-free production process.
Krok | Zamiar | Example | Tools Used |
---|---|---|---|
Root cause analysis | Identify the source of errors | Investigating machine malfunction | Fishbone diagram, 5 Whys |
Corrective actions | Fix the immediate error | Adjusting machine settings | Corrective action plan |
Preventive actions | Prevent future errors | Updating training procedures | Preventive maintenance schedule |
10. How Can Lean Manufacturing Help Reduce Errors?
Lean manufacturing is a methodology focused on improving efficiency by eliminating waste and optimizing processes. But here’s the thing: lean principles can also be incredibly effective in reducing manufacturing errors by streamlining workflows, improving process control, and fostering a culture of continuous improvement.
Lean manufacturing focuses on several key principles, including 5S, Kaizen, and Just-In-Time (JIT). 5S is a system that helps organize the workspace, ensuring that tools and materials are easily accessible and that the environment is conducive to efficient production. Kaizen is a continuous improvement philosophy that encourages workers to identify and address inefficiencies in their work. JIT minimizes inventory levels by producing only what is needed, when it is needed, reducing the chances of defects caused by overproduction or excess stock.
What’s the kicker here? By implementing lean principles, manufacturers can improve both product quality and overall efficiency. For example, JIT minimizes the chances of defects due to outdated inventory, while 5S ensures that workspaces are organized, reducing the likelihood of errors caused by misplaced tools or materials.
Lean manufacturing not only reduces errors but also enhances the overall production process by making it more efficient and responsive to customer needs. By focusing on continuous improvement, lean principles help companies identify and correct errors before they affect the final product.
Lean Principle | Zamiar | Korzyści | Example |
---|---|---|---|
5S | Organize workspace | Reduce clutter, improve efficiency | Labeling tools, creating workstations |
Kaizen | Continuous improvement | Eliminate inefficiencies, improve quality | Regular team meetings to suggest improvements |
JIT | Minimize inventory | Reduce waste, improve product flow | Producing parts based on customer demand |
11. How Do You Ensure Consistency in Product Quality?
Consistency in product quality is essential for maintaining customer satisfaction and meeting regulatory standards. But here’s the thing: achieving consistency requires a combination of standardized processes, continuous monitoring, and employee training. Without these elements, quality can fluctuate, leading to defective products and customer dissatisfaction.
To ensure consistency, manufacturers must first establish clear standards for product quality. These standards should cover all aspects of the product, from design specifications to material requirements and production methods. Regular monitoring is crucial to ensuring that production stays within these standards. This can be done through in-line testing, inspections, and audits. Additionally, using automated systems for quality checks can provide real-time data and prevent errors from slipping through unnoticed.
What’s the kicker here? Employee involvement is key to maintaining consistency. When workers are properly trained and engaged in quality assurance processes, they become more vigilant about detecting and addressing potential issues. Regular feedback and continuous improvement initiatives also help employees stay focused on maintaining high-quality standards throughout the production process.
By implementing standardized processes, leveraging technology, and involving employees in quality management, manufacturers can achieve consistent product quality, reduce errors, and improve customer satisfaction.
Consistency Strategy | Zamiar | Korzyści | Example |
---|---|---|---|
Standardized processes | Ensure uniformity in production | Reduce variability, improve quality | Documented work instructions, SOPs |
Automated quality checks | Real-time quality monitoring | Catch defects early, reduce errors | Machine vision systems for defect detection |
Employee training | Educate workers on quality standards | Increase awareness, improve product consistency | Regular training sessions on quality control |
12. How Does Continuous Improvement Contribute to Reducing Manufacturing Errors?
Continuous improvement is a key philosophy in modern manufacturing. But here’s the deal: it’s not just about making incremental changes; it’s about fostering a culture of ongoing innovation that reduces errors, enhances quality, and drives efficiency. Continuous improvement involves constantly looking for ways to improve processes, eliminate waste, and enhance product quality.
One of the most popular methods for continuous improvement is Six Sigma, a data-driven approach that seeks to reduce process variation and eliminate defects. By using statistical analysis, Six Sigma helps identify the root causes of errors and develop solutions to address them. Another key aspect of continuous improvement is the Plan-Do-Check-Act (PDCA) cycle, which encourages manufacturers to plan improvements, implement changes, monitor results, and adjust as needed.
What’s the kicker here? Continuous improvement doesn’t stop after implementing a single solution. It’s an ongoing process that requires regular reviews and feedback loops. By maintaining a focus on improvement, manufacturers can stay ahead of potential errors and ensure that their processes remain efficient and effective.
By embedding continuous improvement practices into the fabric of the organization, manufacturers can reduce errors, increase efficiency, and deliver higher-quality products. This approach helps create a more resilient, adaptable production environment.
Continuous Improvement Method | Zamiar | Korzyści | Example |
---|---|---|---|
Six Sigma | Reduce process variation | Eliminate defects, improve quality | DMAIC methodology |
PDCA cycle | Implement systematic improvements | Ensure continuous process optimization | Regular reviews and feedback loops |
Lean manufacturing | Eliminate waste | Improve efficiency, reduce errors | 5S, Kaizen |
13. How Do You Ensure High-Quality Supplier Relationships?
The quality of raw materials and components plays a significant role in determining the overall quality of the finished product. But here’s the kicker: maintaining strong, quality-driven relationships with suppliers is key to ensuring that the materials you receive meet your standards. Suppliers are your partners in the manufacturing process, and their performance directly impacts your product quality.
Establishing clear expectations and requirements is the first step in ensuring high-quality supplier relationships. Manufacturers should communicate their quality standards, delivery schedules, and expectations clearly to their suppliers. Regular audits and inspections of supplier processes also help ensure that the materials received meet the required specifications. Working closely with suppliers to resolve any issues and improve processes is another crucial step in maintaining a strong relationship.
What’s the kicker here? By fostering long-term partnerships with reliable suppliers, manufacturers can reduce the risk of receiving defective materials and ensure a steady supply of high-quality components. This collaboration can lead to improvements in both product quality and production efficiency.
Supplier Relationship Strategy | Zamiar | Korzyści | Example |
---|---|---|---|
Clear communication | Align expectations, ensure quality | Reduce misunderstandings, improve efficiency | Regular meetings to discuss standards |
Supplier audits | Inspect supplier processes | Ensure compliance with quality standards | On-site supplier inspections |
Long-term partnerships | Build trust, improve reliability | Ensure steady supply of quality materials | Joint problem-solving with suppliers |
14. How Can You Improve Production Efficiency to Reduce Errors?
Improving production efficiency is not just about speeding up the process; it’s about eliminating inefficiencies that lead to errors and waste. But here’s the deal: when you streamline production, you reduce the chances of mistakes, increase throughput, and enhance overall product quality.
One of the best ways to improve efficiency is by automating processes where possible. Automated systems reduce the chances of human error, speed up production, and ensure consistency. Another strategy is to implement a lean manufacturing approach, which focuses on reducing waste and optimizing resources. Techniques like 5S, Kaizen, and JIT (Just-In-Time) can help improve the flow of materials and ensure that production runs smoothly.
What’s the kicker here? Continuous monitoring and data analysis are essential for identifying bottlenecks and inefficiencies. By using real-time data and performance tracking, manufacturers can pinpoint areas of the production process that need improvement and make adjustments accordingly.
By improving efficiency, manufacturers can reduce production errors, increase output, and lower costs, all while delivering higher-quality products.
Efficiency Improvement Method | Zamiar | Korzyści | Example |
---|---|---|---|
Automatyzacja | Reduce human error, speed up production | Increase throughput, improve consistency | Robotic arms for assembly |
Lean manufacturing | Eliminate waste, optimize resources | Improve flow, reduce errors | JIT inventory system |
Data analysis | Monitor performance, identify bottlenecks | Improve decision-making, optimize production | Real-time production data tracking |
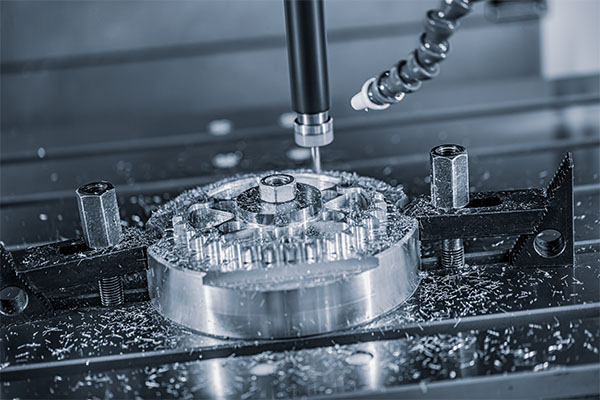
15. How Can You Create a Culture of Quality to Reduce Manufacturing Errors?
A culture of quality is essential for ensuring that manufacturing errors are kept to a minimum. But here’s the kicker: it’s not just about policies and procedures; it’s about making quality a core value that everyone in the organization embraces. When quality becomes ingrained in the company’s culture, employees at every level work together to maintain high standards.
Creating a culture of quality starts with leadership. Leaders must set an example by prioritizing quality and showing commitment to continuous improvement. It’s also important to involve employees in the process. Providing training, encouraging feedback, and recognizing achievements related to quality can help employees feel more invested in the company’s success.
What’s the real story here? By fostering a culture of quality, manufacturers can create an environment where everyone works together to minimize errors, improve processes, and deliver high-quality products. This proactive approach to quality ensures that mistakes are caught early, preventing larger issues down the line.
By embedding quality into the organization’s culture, manufacturers can reduce errors, enhance efficiency, and improve customer satisfaction.
Cultural Strategy | Zamiar | Korzyści | Example |
---|---|---|---|
Leadership involvement | Set the tone for quality | Improve commitment, inspire action | Quality-focused leadership |
Employee engagement | Involve workers in quality management | Increase ownership, improve outcomes | Employee feedback sessions |
Recognition programs | Reward quality achievements | Motivate employees, reinforce quality focus | Employee of the month for quality improvements |
Wniosek
Manufacturing errors are inevitable in any production environment, but with the right strategies, they can be minimized. From understanding the types of tolerances to using advanced measurement tools, there are numerous ways to reduce errors and improve production efficiency. By implementing GD\&T, investing in high-quality measurement tools, and maintaining a focus on quality control, manufacturers can significantly reduce errors, ensuring that products meet the required specifications. In the end, it’s about creating a streamlined, efficient process that delivers high-quality products consistently.
Często zadawane pytania
Pytanie 1: What is a manufacturing error?
A manufacturing error is a discrepancy or defect in a product that occurs during the production process. These errors can be caused by various factors, such as human mistakes, machine malfunctions, or material defects.
Pytanie 2: How does GD\&T help reduce manufacturing errors?
GD\&T helps reduce manufacturing errors by providing a standardized system for specifying tolerances. This ensures that everyone involved in the production process understands the required specifications, minimizing the risk of errors.
Pytanie 3: What is tolerance in manufacturing?
Tolerance in manufacturing refers to the acceptable variation in dimensions and features of a part. It ensures that parts fit and function correctly despite minor variations during production.
Pytanie 4: How can technology minimize manufacturing errors?
Technology such as CAD, CAM, and AI-powered error detection systems can help minimize manufacturing errors by improving design accuracy, automating processes, and identifying potential issues before they occur.
Pytanie 5: What is statistical process control (SPC) and how does it help reduce errors?
Statistical Process Control (SPC) is a method of monitoring and controlling a manufacturing process using statistical tools. It helps identify variations that may lead to errors, enabling corrective actions before defects occur.