Wstęp
Nylon is a versatile material widely used in Obróbka CNC. In this article, we’ll delve into the properties, advantages, and applications of nylon material, especially in CNC machining. By the end, you’ll have a clear understanding of why nylon is favored in various industries and how it performs when machined using CNC technology.
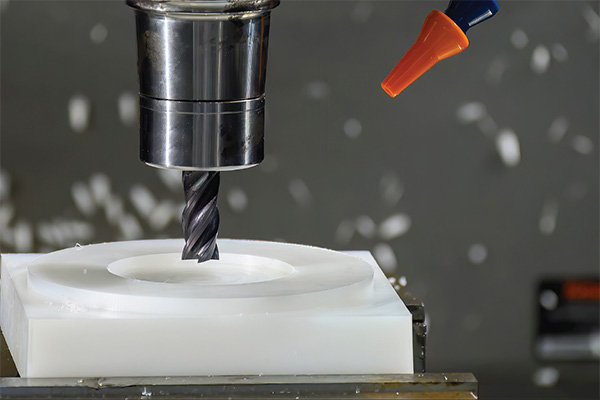
1. What is Nylon and What Are Its Properties?
Nylon is a synthetic polymer that belongs to a family of materials known as polyamides. It was first developed by Wallace Carothers and his team at DuPont in the 1930s, and it has since become a widely used material in various industries, including manufacturing, automotive, and medical devices. But here’s the kicker—what makes nylon so special?
One of the primary reasons nylon is favored in CNC machining is its remarkable combination of mechanical properties. Nylon is known for its high strength-to-weight ratio, meaning it offers significant durability without adding unnecessary weight. It also exhibits excellent resistance to wear and abrasion, making it ideal for parts that will experience frequent friction, like gears, bearings, and bushings.
Moreover, nylon is highly resistant to many chemicals, which makes it a top choice for industries where components need to withstand harsh environments. Another notable property of nylon is its ability to maintain its shape and strength across a wide temperature range, although extreme heat can cause it to soften or warp.
What’s the real story behind nylon’s versatility? Well, it also offers a degree of flexibility that other materials like metals don’t. This flexibility is especially beneficial when machining complex shapes or intricate designs. So, if you’re in need of durable, versatile material for your CNC machining projects, nylon might just be your go-to solution.
Nieruchomość | Nylon |
---|---|
Strength-to-weight ratio | Wysoki |
Resistance to wear | Excellent |
Chemical resistance | Strong |
Elastyczność | Moderate |
Temperature tolerance | Wide range |
2. How Does Nylon Perform in CNC Machining?
CNC machining is one of the most effective methods for processing nylon, and here’s why. The precision offered by CNC machines allows manufacturers to create complex parts with tight tolerances using nylon material. But here’s the catch—nylon has its quirks when it comes to machining.
The first challenge that machinists often encounter with nylon is its tendency to warp or shrink during processing. This occurs because nylon absorbs moisture from the air, causing it to expand. When this moisture evaporates during machining, the material can shrink, leading to dimensional changes in the final product. However, this is where CNC machining excels—by controlling the environment and using proper techniques, such as moisture drying, the effects of shrinkage can be minimized.
Another aspect of nylon machining that’s important to note is the choice of cutting tools. Nylon can be easily machined with carbide tools, but care must be taken with tool coatings and cutting parameters. If the wrong tool is used or machining speeds are too high, the nylon material can melt or become gummy, leading to poor surface finish or tool wear.
What’s the real kicker here? With the right settings and adjustments, machining nylon can be a breeze. Cooling techniques, proper tool selection, and precision control during the process ensure a high-quality outcome, and this is exactly why nylon is often chosen for CNC machining in applications that demand reliability and performance.
Wyzwanie | Rozwiązanie |
---|---|
Warping and shrinkage | Pre-dry the material, control humidity levels |
Zużycie narzędzi | Use carbide or coated tools |
Surface finish | Fine-tune speeds, feeds, and cooling |
3. What Are the Advantages of Using Nylon in CNC Machining?
Nylon offers several distinct advantages when used in CNC machining. To begin with, nylon parts are highly durable, which is crucial for applications that require long-lasting components. Ready for the good part? Nylon’s excellent wear resistance ensures that parts like gears, pulleys, and bearings can withstand extensive use without premature failure.
In addition to its strength and wear resistance, nylon is also a lightweight material. This feature makes it a top choice in industries like aerospace and automotive, where reducing weight is essential for performance and fuel efficiency. Furthermore, the fact that nylon is relatively easy to machine—compared to metals, for example—means that CNC machining processes can be completed quickly and with a high degree of accuracy.
Another huge benefit of using nylon in CNC machining is its cost-effectiveness. Nylon is generally cheaper to work with than many metals, which can reduce production costs while still providing a strong, durable part. But there’s more—nylon is highly versatile and can be modified or blended with other materials to improve specific characteristics, such as enhanced chemical resistance or increased tensile strength.
But here’s the kicker: nylon also offers a good degree of self-lubrication, meaning parts made from nylon often don’t require additional lubrication in certain applications. This can save on maintenance costs and improve the overall performance of the component.
Advantage | Impact |
---|---|
High wear resistance | Long-lasting performance |
Lightweight | Ideal for aerospace and automotive |
Opłacalny | Reduces production costs |
Self-lubricating | Reduces maintenance requirements |
4. What Are the Disadvantages of Using Nylon in CNC Machining?
While nylon boasts numerous advantages, it does come with some disadvantages. One of the primary drawbacks is its sensitivity to moisture. Nylon absorbs water from the environment, which can lead to dimensional instability and weaken its mechanical properties. This is a major concern in precision applications where tight tolerances are critical.
Another challenge with machining nylon is its lower heat resistance compared to metals like steel or aluminum. Although it can withstand a range of temperatures, exposure to high heat can cause nylon to soften, warp, or lose its strength. This can limit its use in high-temperature environments unless additional steps are taken, such as using heat-treated or high-temperature-resistant nylon variants.
What’s the real story here? Nylon is prone to wear over time when exposed to UV radiation, which can cause it to degrade and lose its structural integrity. For outdoor applications, it’s often necessary to incorporate additives to improve UV resistance.
However, despite these disadvantages, nylon is still one of the best materials available for many CNC machining applications due to its balance of cost, strength, and ease of machining. By following best practices, many of the challenges associated with nylon can be mitigated effectively.
Disadvantage | Impact |
---|---|
Moisture absorption | Dimensional instability |
Heat resistance | Limited use in high-temperature areas |
UV degradation | Reduced outdoor application lifespan |
5. What Are Common Applications of Nylon in CNC Machining?
Nylon’s unique properties make it ideal for use in a wide range of industries. One of the most common applications of nylon in CNC machining is in the production of gears and bearings. Nylon’s wear resistance and self-lubricating properties make it perfect for parts that need to withstand constant friction without requiring additional lubrication.
In addition to automotive and aerospace uses, nylon is also frequently used in the manufacturing of electrical components. Its excellent insulation properties make it a preferred choice for parts like connectors, housings, and electrical enclosures. But here’s the thing: nylon can also be found in medical devices, where its biocompatibility is crucial for ensuring the safety of products that come into contact with the human body.
Another growing application for nylon is in consumer goods. Whether it’s the plastic components of a household appliance or the internal mechanisms of a robotic vacuum, nylon plays an important role in providing lightweight yet durable solutions for everyday products.
So, what’s the real kicker? Nylon is so versatile that it can be modified for specialized applications, making it an all-around material for many different CNC machining needs.
Aplikacja | Przemysł | Korzyść |
---|---|---|
Gears and bearings | Automotive, manufacturing | High wear resistance and self-lubrication |
Electrical components | Electronics, manufacturing | Excellent insulation and durability |
Medical devices | Healthcare | Biocompatibility for safety |
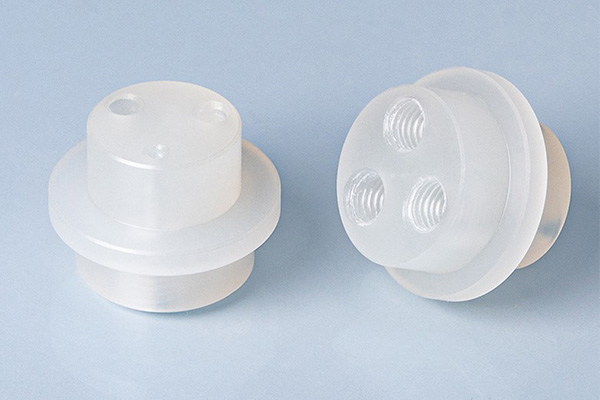
6. How Do You Choose the Right Nylon Grade for CNC Machining?
When selecting the right grade of nylon for CNC machining, there are several factors to consider. The most common grades are nylon 6 and nylon 66, each offering different benefits depending on the application. Nylon 6 is known for its excellent chemical resistance and flexibility, making it ideal for applications like fluid handling and packaging. On the other hand, nylon 66 offers superior strength, stiffness, and heat resistance, which is perfect for parts subjected to high mechanical stresses.
Another important consideration when choosing a nylon grade is the intended use of the part. For example, if you’re machining components that will be exposed to UV light or extreme outdoor conditions, you may need a UV-stabilized nylon to prevent degradation over time. Additionally, certain nylon grades are reinforced with materials like glass fibers to improve strength and durability, making them more suitable for high-load applications.
But here’s where it gets interesting—nylon grades can also be modified with additives to enhance specific characteristics, such as flame resistance or conductivity. So, when selecting the right nylon grade, it’s crucial to carefully assess your project’s requirements and select the material that offers the best balance of performance, cost, and durability.
Grade | Właściwości | Best For |
---|---|---|
Nylon 6 | Flexible, chemical resistance, low friction | Fluid handling, packaging, low-stress parts |
Nylon 66 | Strong, stiff, heat-resistant | High-stress applications, mechanical parts |
Reinforced Nylon | Stronger, more durable, UV-stabilized | Heavy-duty applications, outdoor use |
7. What CNC Machining Techniques Are Used for Nylon?
CNC machining is highly effective for processing nylon, and several techniques are commonly employed to achieve the desired results. So, what’s the real story behind these methods?
One of the most popular techniques for machining nylon is milling. Milling involves rotating a cutting tool to remove material from a workpiece. This technique is used to create parts with precise shapes and detailed features. For example, when machining gears or pulleys from nylon, milling ensures high dimensional accuracy and surface finish. CNC milling machines can handle both soft and reinforced nylon grades, providing flexibility across applications.
Another widely used technique is turning, which involves rotating the nylon workpiece while a cutting tool shapes it. Turning is ideal for cylindrical parts, such as rods and bushings. The precision of CNC turning ensures that these components meet tight tolerances, which is crucial in industries like automotive and aerospace. But here’s the kicker—using the right cutting tool is essential to prevent nylon from melting during the turning process, as overheating can cause surface defects.
Drilling is also a common CNC machining method used for creating holes in nylon. This technique is essential when designing components that require precise hole placement, like electrical connectors or mechanical fittings. Drilling nylon requires special attention to feed rates and tool selection to ensure clean holes without burrs or cracks.
And what’s the catch? Each of these techniques requires proper tooling, speeds, and feeds to ensure the best outcome when machining nylon. Whether you’re using milling, turning, or drilling, understanding the properties of nylon and the CNC machine capabilities is key to achieving high-quality results.
Technika | Aplikacja | Key Consideration |
---|---|---|
Milling | Complex shapes, detailed features | Tool selection and feed rates |
Turning | Cylindrical parts, bushings, rods | Heat management, precise tool selection |
Drilling | Holes for connectors, mechanical fittings | Feed rates and tool choice to avoid cracking |
8. What Tools Are Best for Machining Nylon?
When it comes to machining nylon, selecting the right tools is critical to achieving optimal results. But here’s the kicker—choosing the wrong tool can lead to melted or damaged parts.
Carbide tools are commonly used when machining nylon. These tools are ideal because they maintain sharp edges and resist wear better than other materials, ensuring smooth cuts and reducing the chance of nylon melting during machining. Carbide tools are highly effective for both roughing and finishing operations, making them versatile for a variety of applications.
High-speed steel (HSS) tools are another option, although they wear more quickly than carbide tools. However, HSS tools can still perform effectively on nylon if used with appropriate cutting speeds and feeds. The advantage of HSS tools is their relatively low cost, which makes them suitable for high-volume production runs where tool life is not as critical.
The tool coating also plays a crucial role in machining nylon. Coated tools, such as TiN (Titanium Nitride) Lub TiAlN (Titanium Aluminum Nitride), provide increased hardness and wear resistance, reducing the frequency of tool changes and improving the longevity of the tools. These coatings are especially useful when machining tougher nylon variants or during prolonged machining runs.
What’s the real story here? Using the right tool with the correct settings is essential to maintaining quality and precision in your nylon parts. Carbide tools, HSS, and appropriate coatings can help ensure a high-quality finish and efficient machining process.
Tool Type | Korzyści | Best For |
---|---|---|
Carbide | High wear resistance, sharp edges | Roughing, finishing, high-precision cuts |
HSS | Cost-effective, good for lower-volume runs | Budget-friendly machining |
Coated Tools | Increased tool life, wear resistance | Long machining runs, tough nylon variants |
9. How to Prevent Common Issues When CNC Machining Nylon?
When machining nylon, a few common issues can arise, but here’s the thing—most of these problems can be avoided with the right techniques. Let’s explore how to handle them.
One common issue when machining nylon is wypaczanie. This typically occurs due to the moisture content in nylon. Since nylon absorbs moisture from the air, it expands slightly before machining. When the moisture evaporates during the cutting process, it can cause the material to shrink and warp. To prevent this, drying the nylon before machining is crucial. You can use an oven or specialized drying equipment to remove moisture and reduce the risk of warping.
Another common challenge is burr formation, which can occur when cutting or drilling nylon. Burrs are unwanted edges or material pieces left behind after machining. To prevent burrs, use proper cutting speeds and ensure the cutting tools are sharp. Additionally, controlling the feed rate and using adequate lubrication can help reduce burr formation.
Lastly, zużycie narzędzi is an issue that can affect the quality of your machined parts. To minimize tool wear, always choose tools designed for nylon, such as carbide or coated tools. Additionally, adjusting your cutting parameters (such as speeds and feeds) based on the specific type of nylon you’re working with can help extend tool life and maintain machining quality.
The key to avoiding these common issues lies in preparation. With proper drying, tool selection, and machining techniques, you can prevent most challenges that arise during CNC machining of nylon.
Wydanie | Rozwiązanie | Prevention Tips |
---|---|---|
Deformacja | Pre-dry the nylon material | Store in a controlled humidity environment |
Burr formation | Use proper cutting speeds, sharp tools | Regularly change cutting tools and adjust speeds |
Zużycie narzędzi | Use carbide or coated tools | Fine-tune cutting speeds and feed rates |
10. How Does Temperature Affect Nylon During CNC Machining?
Temperature plays a crucial role when machining nylon, and understanding how it impacts the material is key to achieving optimal results. So, how does temperature affect nylon during machining?
As nylon is being machined, friction between the cutting tool and the material generates heat. Too much heat can soften the nylon, making it more difficult to machine and potentially causing dimensional changes or warping. To prevent this, temperature control is essential during the machining process.
One way to manage temperature is by using coolants or lubricants. These fluids help dissipate heat and prevent the material from overheating. However, it’s important to choose the right coolant or lubricant for nylon, as some coolants can cause nylon to absorb more moisture, leading to warping. Air cooling can also be used, especially when machining smaller parts, to reduce heat build-up.
Additionally, it’s essential to monitor the temperature of the cutting tool itself. Overheating can cause the tool to wear out faster and negatively affect the quality of the cut. That’s why ensuring optimal speeds and feeds, along with adequate cooling, can help keep both the material and the tools at the right temperature for machining.
What’s the real kicker here? By carefully managing temperature throughout the machining process, you can ensure that nylon maintains its strength, shape, and integrity, resulting in high-quality parts.
Temperature Effect | Rozwiązanie | Wskazówka |
---|---|---|
Softening of material | Use proper cooling and lubrication | Adjust speeds and feeds to reduce friction |
Tool wear and damage | Regularly monitor tool temperature | Use air cooling or select appropriate coolants |
Warping due to heat | Maintain consistent machining temperature | Pre-dry nylon and manage environmental factors |
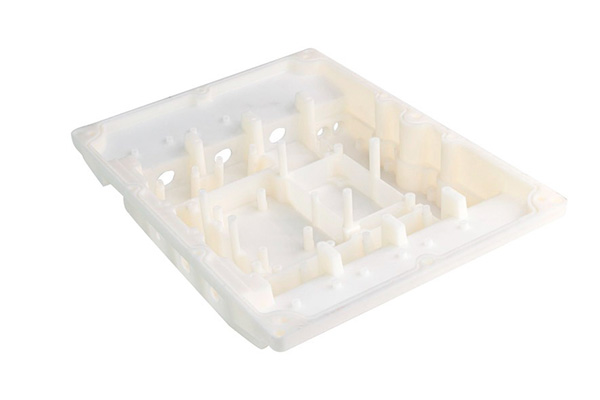
11. How to Finish and Post-Process Nylon Parts After CNC Machining?
Once nylon parts are machined, finishing and post-processing are crucial steps to enhance their appearance, functionality, and durability. But here’s the kicker—post-processing can also improve the overall performance of your nylon components.
One common finishing technique is sanding. Sanding is used to smooth out any rough edges left by the CNC machining process, giving the part a more polished appearance. Depending on the desired surface finish, you can use a combination of coarse and fine sandpapers to gradually smooth the nylon’s surface.
Polerowanie is another post-processing step that can be applied to nylon parts to enhance their surface finish. Polishing nylon requires careful technique, as overheating can cause the material to soften. To avoid this, it’s important to use low-speed polishing equipment and a polishing compound designed for plastics.
Heat treatment can also be applied to improve the strength of nylon components. While nylon has good strength at room temperature, heat treatment can increase its crystallinity, improving its mechanical properties. However, excessive heat can cause deformation, so it’s important to carefully control the process.
And what’s the real story here? After machining, taking the time to carefully finish and post-process your nylon parts can significantly improve their quality, ensuring they meet the required standards for performance and appearance.
Process | Korzyść | Best Use |
---|---|---|
Sanding | Smooths rough edges, improves appearance | Cosmetic finishes or tight tolerance parts |
Polerowanie | Enhances surface finish and gloss | Aesthetic or non-structural components |
Heat treatment | Increases mechanical strength | High-load or high-stress applications |
12. How Does Nylon Perform in Harsh Environments?
Nylon is known for its versatility and durability, but how does it perform in extreme conditions? The good news is, nylon has a relatively high resistance to chemicals, oils, and greases, which makes it an excellent choice for many harsh environments.
However, nylon’s performance can be negatively impacted by prolonged exposure to UV radiation. Over time, UV exposure can cause nylon to become brittle and degrade. This is why it’s essential to use UV-stabilized nylon for outdoor applications or parts that will be exposed to sunlight.
When it comes to extreme temperatures, nylon performs well within a certain range. It can handle temperatures as high as 150°C, but exposure to sustained high heat can lead to softening, warping, or even melting. For applications that require high heat resistance, specially formulated nylon grades, such as high-temperature nylon Lub nylon with glass fiber reinforcement, should be used.
So, what’s the real kicker here? While nylon is robust, its long-term performance in harsh environments depends on the specific conditions it faces. UV stabilizers, proper formulations, and heat-resistant nylon variants can significantly improve its lifespan and functionality in extreme settings.
Condition | Effect on Nylon | Rozwiązanie |
---|---|---|
UV exposure | Degradation, brittleness | Use UV-stabilized nylon |
High temperatures | Softening, warping | Use high-temperature nylon grades |
Chemical exposure | Corrosion, wear | Select chemical-resistant nylon variants |
13. What Are the Cost Considerations for Machining Nylon?
Nylon offers a variety of benefits, but what about the cost? Here’s the kicker: while nylon is relatively inexpensive compared to metals, several factors can influence its cost-effectiveness.
One of the primary cost considerations when machining nylon is material cost. While nylon itself is not particularly expensive, costs can vary depending on the grade, additives, and required certifications. For example, specialized nylon grades, such as those with glass fiber reinforcement or UV resistance, are more costly than standard nylon types.
Another factor is machining time. Because nylon is easy to machine, it generally requires less time than harder materials like metals. This can reduce overall production costs. However, if you’re working with a larger batch of parts or a complex design, the cost of machining may increase due to additional setup time and tool wear.
What’s the real story here? Despite the relatively low material cost of nylon, careful consideration must be given to machining time, tooling, and material grade to ensure that the final cost remains competitive.
Współczynnik kosztów | Impact | Optimization Tips |
---|---|---|
Material cost | Varies by grade and additives | Use standard grades unless specifications demand otherwise |
Machining time | Shorter machining time reduces cost | Optimize tool paths and speeds to reduce time spent |
Tooling | Tool wear can increase costs | Use carbide tools and adjust machining parameters |
14. How to Ensure High-Quality Results When CNC Machining Nylon?
Ensuring high-quality results when machining nylon involves a combination of precise settings, quality materials, I correct techniques. Ready for the good part? High-quality machining is possible with careful attention to the details.
One important factor is controlling feed rates and speeds. Too high or too low feed rates can lead to poor surface finish, excessive tool wear, or even part failure. It’s essential to adjust your CNC machine’s settings based on the specific nylon grade and the complexity of the part.
Another key factor is using the right cooling methods. Improper cooling can cause nylon to soften or warp. For most applications, air cooling Lub lubrication with an appropriate fluid can keep temperatures within optimal ranges. However, excessive cooling or the wrong coolant can have adverse effects, so it’s essential to find the balance that works best for your specific application.
Finally, material selection plays a crucial role. Choosing the right grade of nylon with the desired mechanical properties ensures that the part meets the requirements of its application. For example, selecting a fiber-reinforced nylon can improve strength and durability for high-load applications.
Czynnik | Importance | Rozwiązanie |
---|---|---|
Feed rates and speeds | Prevents tool wear and surface issues | Adjust based on nylon type and part complexity |
Cooling methods | Prevents softening and warping | Use air cooling or select appropriate coolants |
Material selection | Ensures required mechanical properties | Choose the right nylon grade for the application |
15. What Are the Future Trends for Nylon in CNC Machining?
Nylon has been around for decades, but its use in CNC machining continues to evolve. What’s the real kicker? The future of nylon in manufacturing looks brighter than ever.
One of the most exciting trends in nylon development is the rise of sustainable nylon. With increasing focus on sustainability, manufacturers are beginning to explore recycled nylon, which not only reduces waste but also lowers material costs. Innovations in recycling technologies allow nylon waste to be repurposed into high-quality material suitable for CNC machining.
Another trend is the advancement of high-performance nylon grades. Research is focused on developing new formulations of nylon with enhanced properties, such as higher heat resistance, better chemical resistance, and greater strength. These advanced nylons are ideal for use in more demanding applications, such as aerospace, automotive, and heavy machinery.
But here’s where it gets interesting—3D printing with nylon is another exciting area. Nylon filaments are increasingly being used in 3D printers, allowing for rapid prototyping and the creation of custom parts without the need for traditional tooling. This opens up new possibilities for small-scale production and complex geometries that would be difficult or expensive to machine using conventional methods.
Tendencja | Impact | Future Potential |
---|---|---|
Sustainable nylon | Reduces waste and material costs | Increased adoption in eco-friendly applications |
High-performance nylon | Offers superior mechanical properties | Suitable for demanding industries |
3D printing with nylon | Rapid prototyping and custom parts | Opens up new possibilities in manufacturing |
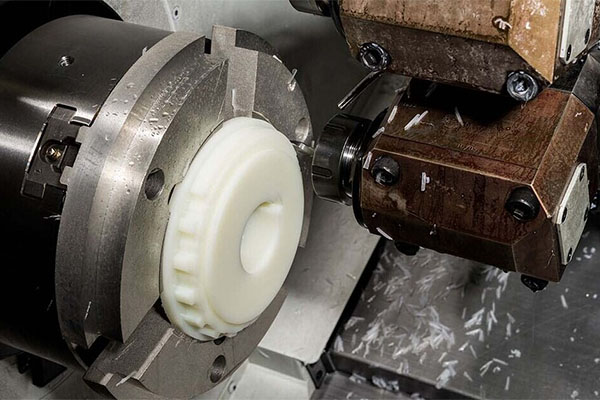
Sekcja FAQ
Pytanie 1: What is nylon?
Nylon is a synthetic polymer known for its high strength, flexibility, and durability. It’s commonly used in CNC machining for producing parts that need to withstand wear and stress.
Pytanie 2: How does CNC machining work with nylon?
CNC machining allows for the precise shaping of nylon parts. However, care must be taken to manage issues like warping, moisture absorption, and heat sensitivity during the machining process.
Pytanie 3: What are the best applications for nylon in CNC machining?
Nylon is ideal for applications such as gears, bearings, electrical components, and medical devices due to its strength, wear resistance, and versatility.
Pytanie 4: What challenges arise when machining nylon?
Some of the challenges include moisture absorption, dimensional instability, and heat sensitivity. Proper techniques and material selection can mitigate these issues.
Pytanie 5: How do you choose the right grade of nylon for CNC machining?
The right nylon grade depends on the application, desired mechanical properties, and environmental conditions. Nylon 6 is flexible, while nylon 66 offers greater strength and heat resistance.