Wstęp
Stainless steel machining is an important and highly specialized field in manufacturing. It’s vital for industries such as aerospace, automotive, medical, and construction, where precision, durability, and corrosion resistance are key. If you’re new to stainless steel machining, you might be wondering what it entails and how to approach it. In this guide, we’ll walk you through everything you need to know to get started with machining stainless steel, from the basics of CNC machining to the best practices for choosing the right materials and tools. Ready to dive in?
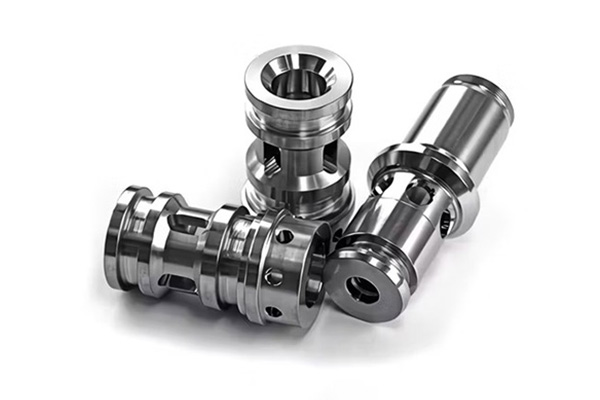
1. What is Stainless Steel Machining?
Stainless steel machining refers to the process of shaping, cutting, and finishing stainless steel components using various machining techniques. This includes processes like CNC machining, turning, and milling, among others. Now, what’s the real story behind stainless steel machining? Let’s break it down.
When it comes to stainless steel, its unique properties like resistance to corrosion, strength, and formability make it an ideal material for a wide range of applications. However, machining stainless steel is more challenging than working with other metals due to its hardness and toughness. This is where the right equipment and techniques come in.
In CNC machining, the material is precisely cut using computer-controlled machines that follow pre-programmed paths. This automation ensures high accuracy, repeatability, and efficiency. But here’s the kicker: stainless steel’s resistance to wear can make it tougher on tools and machinery. So, understanding the material’s properties is key to successful machining.
Types of Stainless Steel Used in Machining
Different grades of stainless steel are suitable for different machining applications. For instance, 304 stainless steel is often chosen for its versatility and good corrosion resistance, while 316 stainless steel is preferred for its enhanced resistance to pitting and corrosion in more demanding environments.
Benefits of Stainless Steel in Machining
One major advantage of using stainless steel in machining is its durability. Whether you’re machining a part for a high-stress environment like aerospace or something more routine, stainless steel provides excellent long-term performance.
Table 1: Common Stainless Steel Grades for Machining
Stainless Steel Grade | Właściwości | Common Applications |
---|---|---|
304 | Good corrosion resistance, versatile | Kitchen equipment, pipes |
316 | Enhanced resistance to corrosion | Marine, chemical equipment |
410 | High strength, good wear resistance | Pumps, valves |
2. Why Choose Stainless Steel for Machining?
You might be wondering why stainless steel is a preferred choice for so many industries. Well, it’s all about its strength, durability, and resistance to corrosion. Let’s take a closer look at why stainless steel is the go-to material for precision machining.
One of the biggest advantages of stainless steel is its corrosion resistance. Unlike other metals, stainless steel doesn’t easily rust or corrode when exposed to moisture, making it ideal for environments that require sanitation or are exposed to harsh elements. What’s the real story here? Stainless steel doesn’t just look good, it performs well even in the toughest conditions.
In addition to its corrosion resistance, stainless steel is also highly durable. It can withstand high temperatures, making it perfect for applications in the aerospace and automotive industries. But there’s more. Stainless steel is also non-reactive, meaning it won’t contaminate sensitive products or environments, a crucial factor in the food and medical industries.
Stainless Steel’s Aesthetic Qualities
Another significant benefit is its aesthetic appeal. Stainless steel has a sleek, modern appearance that’s often a crucial element in the design of consumer goods like kitchen appliances, medical devices, and even electronics. This is where it gets interesting: not only is stainless steel highly functional, but it can also contribute to the look and feel of high-end products.
Table 2: Key Benefits of Stainless Steel
Korzyść | Opis |
---|---|
Corrosion Resistance | Resists rust, pitting, and oxidation |
Durability | Strong, capable of withstanding high temperatures |
Aesthetic Appeal | Clean, modern appearance |
Non-reactive | Ideal for medical, food, and sensitive products |
3. What Are the Common Methods of Stainless Steel Machining?
There are several machining methods used to process stainless steel, each suited to different needs and outcomes. Let’s explore the most common methods and what makes them effective for machining stainless steel.
CNC machining is the most popular method for machining stainless steel due to its precision and repeatability. It involves using computer-controlled machines to cut the material according to a specific program. What’s the kicker? CNC machining allows manufacturers to produce complex parts with high accuracy.
Turning and milling are other popular methods. Turning involves rotating the material while a cutting tool removes material, while milling uses a rotating tool to cut the material. Both of these methods are highly versatile and can be used to produce a wide range of parts. But wait, there’s more. These methods are highly efficient, meaning you can produce large quantities of parts quickly, making them ideal for industries that need to scale production.
Laser Cutting and Water Jet Cutting
For projects that require high precision and clean cuts, laser cutting and water jet cutting are ideal methods. Laser cutting uses a focused laser beam to cut through the material, while water jet cutting uses high-pressure water mixed with abrasives to cut stainless steel. These methods are non-contact, reducing the risk of distortion.
Table 3: Common Stainless Steel Machining Methods
Machining Method | Opis | Idealny dla |
---|---|---|
Obróbka CNC | Computer-controlled cutting for high precision | Complex parts, repeatability |
Turning | Rotating material while cutting with a fixed tool | Cylindrical parts |
Milling | Rotating tool removes material from the workpiece | Flat, curved, or irregular parts |
Laser Cutting | Laser beam cuts through stainless steel | High precision, clean cuts |
Water Jet Cutting | High-pressure water with abrasives cuts stainless | Non-contact cutting, intricate designs |
4. How Does CNC Machining Work with Stainless Steel?
CNC machining is the cornerstone of modern manufacturing, especially when it comes to working with tough materials like stainless steel. But what makes it ideal for stainless steel machining? Let’s take a closer look.
CNC machining uses a series of pre-programmed commands to control the movement of tools. These tools cut, mill, or shape the material according to the design specifications. What’s the real story here? CNC machining eliminates the need for manual labor, ensuring precise, repeatable results that are critical in industries requiring high accuracy.
One of the biggest advantages of CNC machining with stainless steel is the ability to create complex geometries and detailed features with minimal human intervention. This is especially important when working with tough materials like stainless steel, which can be difficult to machine manually. The high-speed rotation and sharp cutting tools used in CNC machining allow for smooth, clean cuts even on hard stainless steel.
Advantages and Challenges of CNC Machining Stainless Steel
While CNC machining offers numerous benefits, there are also challenges to consider. Stainless steel can be harder on tools compared to softer metals like aluminum. It requires careful selection of cutting tools and the right machining parameters to prevent tool wear. Ready for the good part? Once you get the parameters right, CNC machining allows you to produce high-quality, durable parts efficiently.
Table 4: CNC Machining Parameters for Stainless Steel
Parameter | Ideal Setting | Notes |
---|---|---|
Cutting Speed | 100–200 SFM (Surface Feet per Minute) | Varies with grade of stainless steel |
Feed Rate | 0.002–0.005 inches per revolution | Depends on material and tool used |
Tool Material | Carbide, High-speed steel | Carbide preferred for tougher grades |
Coolant | Flood cooling, air or mist cooling | Reduces heat buildup, improves tool life |
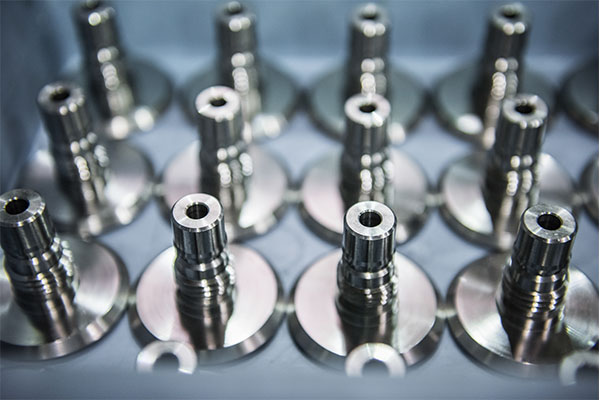
5. What Are the Key Factors in Stainless Steel Machining?
There are several critical factors to consider when machining stainless steel. These factors influence everything from tool life to part quality, so let’s break them down.
First, the hardness of stainless steel is a significant challenge. Because stainless steel is tougher than many other metals, it can wear down cutting tools quickly. That’s where the right tooling comes in. Carbide tools, for example, are ideal for machining harder grades of stainless steel because they maintain their sharpness longer.
Next, cutting speeds and feeds need to be carefully controlled to avoid overheating or premature tool wear. Too high a cutting speed can cause excessive heat, which can damage both the material and the tool. So, what’s the real story here? Getting the speeds and feeds just right is essential to maintaining the quality of the parts being produced and extending tool life.
Lastly, coolant plays a crucial role in stainless steel machining. Stainless steel generates a lot of heat during machining, and coolant helps to keep the material and tool cool. By choosing the right coolant and applying it correctly, you can avoid damaging the part or the tool.
Table 5: Key Factors in Stainless Steel Machining
Czynnik | Impact on Machining | Ideal Settings |
---|---|---|
Hardness of Material | Affects tool wear and cutting efficiency | Carbide tools for hard materials |
Cutting Speed & Feed | Influences heat generation and tool wear | Adjust for material type and tool |
Coolant Usage | Prevents overheating and reduces tool wear | Flood or mist cooling recommended |
Wniosek
In conclusion, stainless steel machining is an essential part of modern manufacturing, offering the versatility and durability needed across a wide range of industries. By understanding the key factors involved in machining stainless steel, from material selection to the right machining methods, you can optimize your production processes. As technology continues to evolve, so too will the techniques and tools used in stainless steel machining, making it even easier to achieve high-precision, cost-effective results.
6. How to Select the Right Stainless Steel Grade for Machining?
Selecting the right grade of stainless steel for machining is critical to ensuring the success of the project. Not all grades of stainless steel are created equal, and each grade offers different properties that make it better suited to certain applications. Let’s dive into how to make the right choice for your machining needs.
Stainless steel comes in various grades, each with unique characteristics such as corrosion resistance, strength, and ease of machining. The most commonly used grades in machining are 304, 316, and 410. Why is this important? Each of these grades offers different benefits that influence the overall machining process.
For example, 304 stainless steel is highly versatile and is known for its excellent corrosion resistance, making it ideal for applications such as food processing, kitchen equipment, and medical instruments. On the other hand, 316 stainless steel has enhanced resistance to pitting and corrosion, making it perfect for marine environments or chemical processing. What’s the kicker? Choosing the right grade impacts machining efficiency and tool life, which can directly affect production costs.
Factors to Consider When Choosing a Grade
When selecting the right grade, consider factors such as the environment the material will be exposed to, the required strength of the final product, and the type of finish needed. For instance, if the part needs to withstand high temperatures, a grade like 310 stainless steel might be a better choice.
Ready for the good part? If your application requires a shiny, polished finish, opt for a grade like 304 that responds well to finishing processes. In contrast, if the part will be exposed to chemicals or high-stress conditions, a more resistant grade like 316 might be required.
Table 6: Common Stainless Steel Grades and Their Applications
Stainless Steel Grade | Corrosion Resistance | Strength | Common Applications |
---|---|---|---|
304 | Excellent | Moderate | Food processing, medical equipment |
316 | Superior | Wysoki | Marine environments, chemical tanks |
410 | Moderate | Wysoki | Pumps, valves, machinery components |
7. What Are the Challenges in Stainless Steel Machining?
Stainless steel machining is not without its challenges. While it’s a highly versatile and durable material, the hardness and toughness of stainless steel can make it difficult to work with. But here’s the kicker: understanding these challenges can help you overcome them efficiently.
One of the most significant challenges in machining stainless steel is its hardness. Unlike softer metals like aluminum, stainless steel is tough and resistant to wear, making it difficult to cut and shape. This hardness increases the wear on cutting tools, shortening their lifespan. What’s the real story? Using the right tools and machinery is essential to overcoming this issue. For example, carbide tools are often recommended for machining stainless steel because they are durable enough to handle its hardness.
Another challenge is maintaining a high-quality surface finish. Stainless steel tends to develop rough edges and burrs during machining, which can affect the appearance and function of the finished part. Achieving a smooth, polished finish often requires additional processes like polishing or passivation, adding time and cost to the overall project.
Tool Wear and Overheating
Tool wear and overheating are also concerns when machining stainless steel. As stainless steel is tough on tools, improper machining speeds or feeds can lead to excessive heat buildup, causing both the material and tools to deteriorate faster. So, what can you do? Ensuring that the machining parameters are correct, including the right cutting speed, feed rate, and coolant application, will help mitigate these problems.
Table 7: Common Challenges in Stainless Steel Machining
Wyzwanie | Przyczyna | Rozwiązanie |
---|---|---|
Zużycie narzędzi | Hardness of stainless steel | Use carbide tools, adjust machining parameters |
Surface Finish | Burrs and rough edges | Use polishing, passivation, or fine finishing |
Przegrzanie | Incorrect speeds or feeds | Optimize cutting parameters, use cooling systems |
8. How Can You Improve Efficiency in Stainless Steel Machining?
Efficiency is critical when machining stainless steel, as this material can be costly, and delays can increase production time and costs. But here’s the kicker: improving efficiency doesn’t just mean speeding things up—it also involves enhancing the quality of the finished product while reducing costs.
One way to improve efficiency is by optimizing cutting parameters. This involves selecting the right cutting speed, feed rate, and depth of cut for the specific grade of stainless steel being machined. What’s the real story here? By fine-tuning these parameters, you can extend tool life, reduce heat generation, and improve the overall efficiency of the machining process.
Another key factor is tool selection. Using high-quality, durable tools like carbide inserts or polycrystalline diamond (PCD) tools can help reduce wear and tear, leading to longer tool life and fewer tool changes. This can significantly increase the efficiency of the entire machining process. Ready for the good part? A well-chosen tool ensures that the job gets done faster, with fewer errors and less downtime.
Automation and Advanced Techniques
Automation can also play a crucial role in improving efficiency. Automated systems can adjust cutting parameters in real time based on sensor data, reducing the need for human intervention and ensuring that the machining process runs as smoothly and efficiently as possible. What’s the kicker here? Automation also helps minimize human error, increasing both consistency and speed.
Table 8: Strategies to Improve Efficiency in Stainless Steel Machining
Strategia | Opis | Korzyści |
---|---|---|
Optimized Cutting | Adjust cutting speed, feed rate, and depth of cut | Extends tool life, reduces heat generation |
High-Quality Tools | Use durable tools like carbide or PCD | Reduces wear, increases tool life |
Automatyzacja | Implement automated systems for real-time adjustments | Increases consistency, minimizes errors |
9. How Do You Achieve Precision and Accuracy in Stainless Steel Machining?
Precision and accuracy are paramount in stainless steel machining, especially in industries like aerospace and medical device manufacturing, where even the slightest deviation can lead to costly failures. Let’s explore the key factors that contribute to achieving high precision.
The first step to achieving precision is ensuring proper machine calibration. This ensures that the CNC machine is set up correctly and operates within the tolerances required for the part. Ready for the good part? When machines are calibrated regularly, they maintain high accuracy over long periods, ensuring that parts are consistently produced with minimal deviation.
Importance of Measurement Tools
Measurement tools also play a crucial role in ensuring precision. Tools such as micrometers, calipers, and coordinate measuring machines (CMM) are essential for checking the dimensions of parts and ensuring they meet the required specifications. What’s the kicker? These tools allow manufacturers to identify issues early in the process, reducing the need for rework or scrapping parts.
Another key factor in achieving precision is the use of high-quality tooling. Tools that are specifically designed for stainless steel machining, such as carbide inserts, provide better performance and longer life, ensuring that the machined part is produced accurately.
Table 9: Tools for Achieving Precision in Stainless Steel Machining
Narzędzie | Zamiar | Korzyści |
---|---|---|
Micrometers | Measure thickness or diameter of parts | High accuracy, fine measurement |
Calipers | Measure internal and external dimensions | Versatile, easy to use for small parts |
Coordinate Measuring Machines (CMM) | 3D measurement of parts | Ensures full dimensional accuracy |
10. What Are the Best Practices for Machining Stainless Steel?
To ensure successful stainless steel machining, it’s essential to follow best practices that reduce tool wear, maintain surface finish, and optimize the overall process. Let’s dive into some of the key best practices.
One of the most important best practices is to use the correct cutting tools. Tools made from carbide or polycrystalline diamond (PCD) are often the best choice for stainless steel machining because they offer superior durability. What’s the kicker? Using the wrong tool can lead to poor surface finishes and premature tool wear, so selecting the right tool is essential for maximizing efficiency.
Another critical best practice is to optimize cutting speeds and feeds. Too high a cutting speed can lead to overheating and poor surface finishes, while too low a cutting speed can cause excessive tool wear. By fine-tuning these parameters, you can achieve both a smooth finish and longer tool life.
Tool Maintenance
Regular tool maintenance is also crucial for maintaining performance. This involves cleaning the tools after each use, inspecting them for wear, and replacing them when necessary. Ready for the good part? Proper tool maintenance not only improves the quality of the parts being produced but also extends the life of the tools, reducing overall costs.
Table 10: Best Practices for Stainless Steel Machining
Najlepsze praktyki | Opis | Korzyść |
---|---|---|
Correct Tool Selection | Use carbide or PCD tools | Ensures longer tool life, reduces wear |
Optimized Cutting Speed | Adjust cutting speed and feed rate appropriately | Reduces tool wear, improves surface finish |
Regular Tool Maintenance | Inspect and clean tools after use | Extends tool life, ensures part quality |
11. What Types of Stainless Steel Machining Machines Are Used?
The type of machine used in stainless steel machining plays a crucial role in the final product. Let’s explore the most commonly used machines and their features.
CNC machines are by far the most popular for stainless steel machining. They provide high precision and repeatability, making them ideal for complex parts. But wait, there’s more. CNC machines also allow for automation, reducing human error and speeding up the production process.
Lathes and Milling Machines
Lathes are another essential tool in stainless steel machining. They rotate the workpiece while a cutting tool removes material to shape the part. Milling machines, on the other hand, use a rotating tool to cut material from the workpiece. What’s the kicker? While CNC machines are highly versatile, lathes and milling machines are often used for simpler, more straightforward parts.
Table 11: Types of Stainless Steel Machining Machines
Machine Type | Function | Ideal for |
---|---|---|
CNC Machines | Computer-controlled machines for high precision | Complex, high-precision parts |
Lathes | Rotating workpiece with stationary tool | Cylindrical parts |
Milling Machines | Rotating cutting tool removes material | Flat, irregular parts |
12. What Are the Costs Involved in Stainless Steel Machining?
The cost of machining stainless steel can vary depending on several factors, including the complexity of the part, the grade of stainless steel used, and the machining method. Let’s break down the costs involved.
One of the major cost drivers in stainless steel machining is the material itself. Stainless steel is typically more expensive than other metals, such as aluminum. What’s the kicker? The price of stainless steel can fluctuate depending on the market, so it’s important to account for this when budgeting for a machining project.
Labor and Machine Costs
Labor and machine time also contribute to the cost of machining. Highly skilled labor is often required for stainless steel machining, especially when dealing with complex parts. Additionally, the machines used for stainless steel machining are often expensive, and the more advanced the technology, the higher the cost.
Table 12: Key Cost Factors in Stainless Steel Machining
Współczynnik kosztów | Opis | Impact on Overall Cost |
---|---|---|
Material Cost | Price of stainless steel material | High due to the cost of stainless steel |
Labor and Machine Costs | Skilled labor and advanced machinery | Increases the cost of production |
Tooling and Setup Costs | Special tools and machine setup | Can add significant overhead |
13. How Does Stainless Steel Machining Impact Product Quality?
The quality of the final product is one of the most important considerations when machining stainless steel. Let’s explore how the machining process influences product quality.
One of the key factors in product quality is the surface finish. Stainless steel can develop rough edges or burrs during machining, which can affect the functionality or aesthetics of the final part. So, what can you do? Using the right machining techniques and tools can help reduce these issues, resulting in a smoother surface.
Tolerances and Dimensional Accuracy
Another critical aspect is dimensional accuracy. In many industries, such as aerospace or medical device manufacturing, precise tolerances are necessary for the part to function as intended. What’s the kicker? Achieving these tight tolerances requires both skilled machinists and high-quality equipment.
Table 13: Factors Influencing Product Quality in Stainless Steel Machining
Czynnik | Impact on Product Quality | Rozwiązanie |
---|---|---|
Surface Finish | Rough edges or burrs can affect appearance and function | Use fine finishing techniques |
Tolerances and Accuracy | Dimensional inaccuracies can cause functional issues | Use precise tools and measurement instruments |
14. How Can You Troubleshoot Common Stainless Steel Machining Problems?
Even the most experienced machinists face challenges when working with stainless steel. Let’s explore some common problems and how to troubleshoot them effectively.
One common issue is excessive tool wear. Stainless steel’s hardness can quickly wear down cutting tools, leading to reduced efficiency and quality. What’s the real story? To address this, ensure that you’re using the right cutting tools for the job, and regularly inspect them for wear.
Chip Build-Up and Material Feed Issues
Chip buildup is another frequent problem. Stainless steel generates tough chips that can clog the machine and cause production delays. Ready for the good part? Using high-pressure coolant systems can help clear chips and prevent them from interfering with the machining process.
Table 14: Troubleshooting Common Machining Problems
Problem | Przyczyna | Rozwiązanie |
---|---|---|
Zużycie narzędzi | Hardness of stainless steel | Use carbide tools, monitor cutting parameters |
Chip Build-Up | Tough chips generated by stainless steel | Use high-pressure coolant, adjust feed rate |
Surface Defects | Rough cutting or incorrect settings | Adjust speeds and feeds, use appropriate tools |
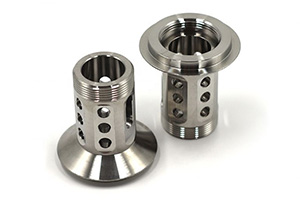
15. What Are the Future Trends in Stainless Steel Machining?
The future of stainless steel machining is bright, with new technologies and techniques making it easier to achieve precision and efficiency. Let’s take a look at some trends that are shaping the future.
One of the biggest trends in stainless steel machining is the increasing use of automation. What’s the kicker? Automated systems can adjust machining parameters in real time, leading to improved efficiency and reduced human error.
Sustainability in Stainless Steel Machining
Sustainability is also a growing trend. With increasing environmental awareness, manufacturers are looking for ways to reduce waste and energy consumption during machining. Ready for the good part? Sustainable machining practices, such as using recyclable materials and optimizing tool life, are becoming more common in the industry.
Table 15: Future Trends in Stainless Steel Machining
Tendencja | Opis | Impact on Industry |
---|---|---|
Automatyzacja | Real-time adjustments for efficiency and accuracy | Reduces human error, increases productivity |
Sustainability | Focus on reducing waste and energy consumption | Minimizes environmental impact, reduces costs |
Sekcja FAQ
Q1: What is stainless steel machining?
Stainless steel machining involves using specialized tools and machines to shape and finish stainless steel components, commonly using CNC machining, turning, and milling techniques.
Q2: How does CNC machining work with stainless steel?
CNC machining automates the cutting and shaping of stainless steel by following precise, pre-programmed instructions, allowing for high accuracy and repeatability.
Q3: What are the common challenges in stainless steel machining?
Challenges include tool wear, heat generation, and achieving the desired surface finish. Proper tool selection and machining parameters can help mitigate these issues.
Q4: How can I choose the right stainless steel grade for machining?
Choosing the right grade depends on factors like strength, corrosion resistance, and application needs. Common grades include 304, 316, and 410 for different purposes.
Q5: What are the best practices for machining stainless steel?
Best practices include using the correct cutting tools, optimizing speeds and feeds, and ensuring proper coolant application to minimize tool wear and maximize part quality.