Injection Molding Company
Injection Molding Experts Help You Easily Meet the Production Needs of Complex Plastic Parts
We provide full-process services from mold design to batch injection molding production to meet the high-precision and high-efficiency requirements of multiple industries.
1. Precision and Consistency
Our injection molding services ensure high precision and consistent quality, meeting exact specifications for every product.
2. Cost-Effective Production
High-efficiency processes reduce material waste and production costs, making large-scale manufacturing economical.
3. Versatile Material Options
We offer a wide range of materials, enabling customized injection molding solutions for diverse applications and industries.
Book Our Service
Contact us now for reliable, cost-effective, and precision-driven manufacturing services.
Meaning
What is Precision Injection Molding?
Precision injection molding is an advanced manufacturing process used to produce highly accurate and intricate plastic components with tight tolerances. This technique involves injecting molten plastic into a meticulously designed mold under high pressure, ensuring consistency, repeatability, and minimal material waste. It is ideal for applications requiring complex geometries, fine details, and strict quality standards, such as in the automotive, medical, and electronics industries. Precision injection molding delivers parts with excellent surface finishes, structural integrity, and dimensional accuracy, making it a preferred choice for industries demanding reliability and performance in their plastic components.
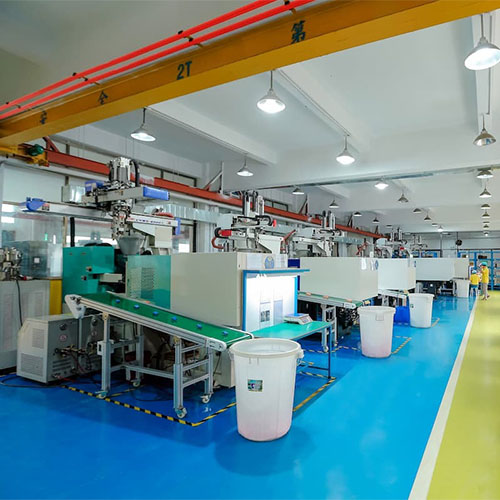
Products
High-Quality Injection Molding Solutions for Plastic and Metal
We specialize in precision injection molding materials, offering exceptional plastic and metal injection molding services tailored to meet diverse industrial needs.
Plástico
Metais
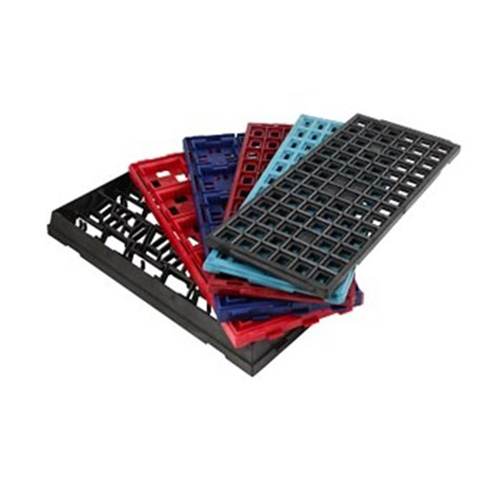
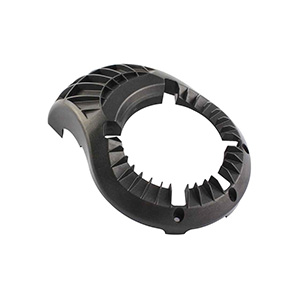
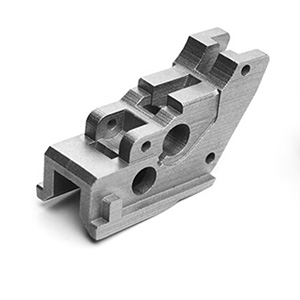
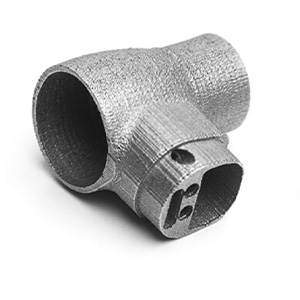
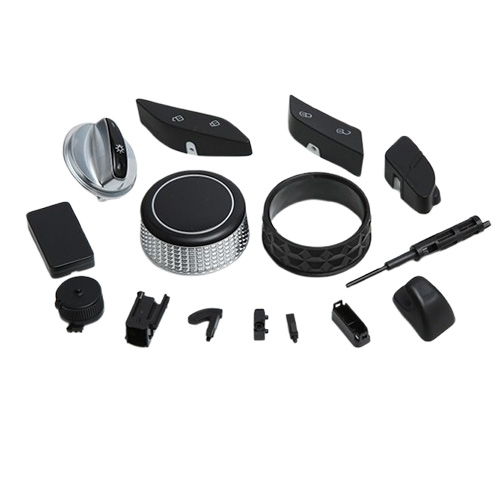
What is Plastic Injection Molding
Plastic injection molding is a manufacturing process that produces high-precision plastic parts by injecting molten plastic into a mold. This method is widely used in various industries due to its efficiency, scalability, and ability to create complex shapes with consistent quality. Suitable for mass production, it supports a range of materials to meet specific application needs.
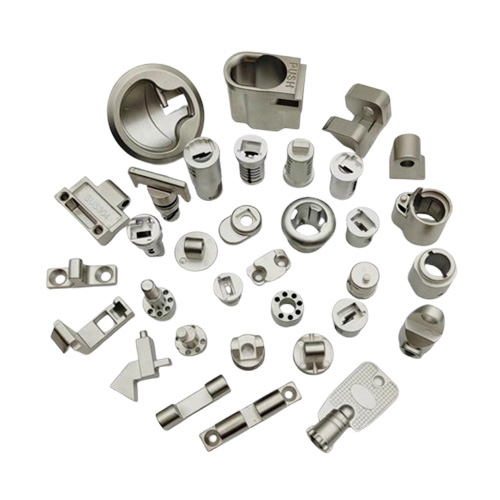
What is Metal Injection Molding
Metal Injection Molding (MIM) is a manufacturing process that combines the precision of plastic injection molding with the strength of metal materials. It involves mixing metal powders with a binder to create a feedstock, which is then injected into molds to form complex shapes. After molding, the binder is removed, and the parts are sintered to achieve high-density and durable components. MIM is ideal for producing small, intricate, and high-performance metal parts efficiently and cost-effectively.
Process
Injection Molding Process

1, Material Preparation: Raw materials, either plastic or metal powders, are prepared and mixed to ensure uniformity.
2, Injection: The material is heated and injected into a precision-designed mold under high pressure.
3, Cooling: The mold is cooled to solidify the material and form the desired shape.
4, Ejection: The finished part is carefully ejected from the mold to avoid damage.
5, Finishing: Final parts are inspected, trimmed, or polished as needed to meet quality standards.
Surface
Injection Mold Surface Finishes
We provide surface finishing in full compliance with SPI standards (A/B/C/D). From high-gloss finishes (Grade A) to matte textures (Grade D), our options ensure the perfect look and feel for your injection molding parts. Each finish is achieved through precise polishing and inspection to meet your aesthetic and functional requirements.
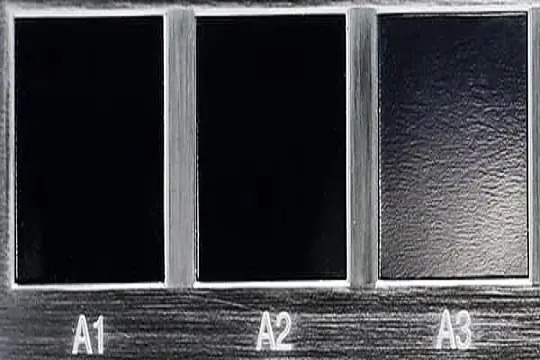
SPI A
Finishing Look: High Gloss
SPI Finish Grades: SPI A1, A2, A3
Surface Roughness Ra (μm):
SPIA1: 0.012 to 0.025
SPIA2: 0.012 to 0.025
SPIA3: 0.05 to 0.10
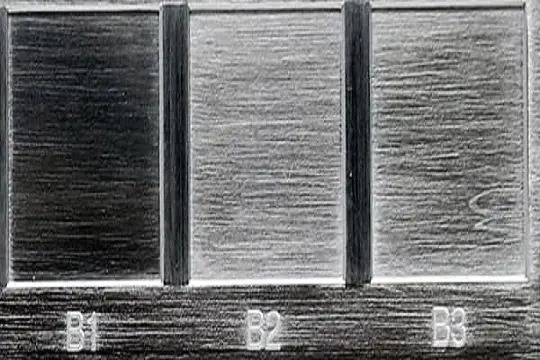
SPI B
Finishing Look: Semi Gloss
SPI Finish Grades: SPI B1, B2, B3
Surface Roughness Ra (μm):
SPI B1: 0.05 to 0.10
SPI B2: 0.10 to 0.15
SPI B3: 0.28 to 0.32
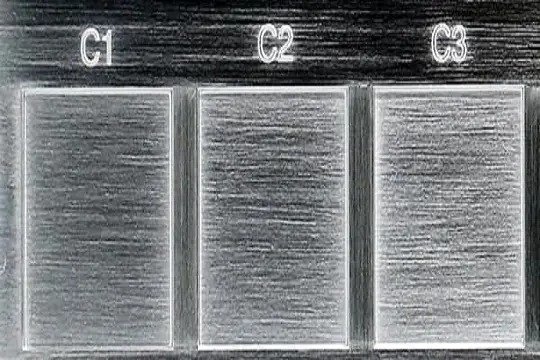
SPI C
Finishing Look: Low Gloss
SPI Finish Grades: SPI C1, C2, C3
Surface Roughness Ra (μm):
SPI C1: 0.35 to 0.40
SPI C2: 0.45 to 0.55
SPI C3: 0.63 to 0.70
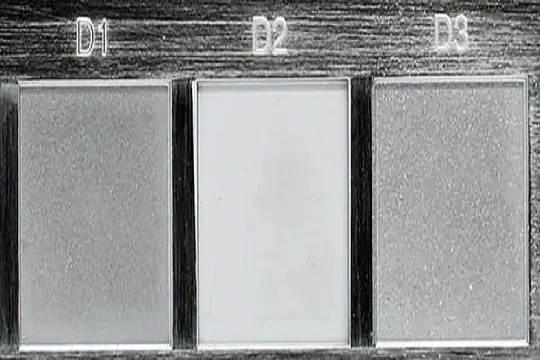
SPI D
Finishing Look: Matte
SPI Finish Grades: SPI D1, D2, D3Surface Roughness Ra (μm):
SPI D1: 0.80 to 1.00
SPI D2: 1.00 to 2.80
SPI D3: 3.20 to 18.0
Capacidades
Precision Injection Molding Capabilities
We offer comprehensive injection molding services, including expert injection molding design to ensure precision and efficiency. Our prototype injection molding allows for rapid testing and validation of your concepts. Additionally, we provide high-quality injection molding tooling, ensuring durable molds for consistent production results.
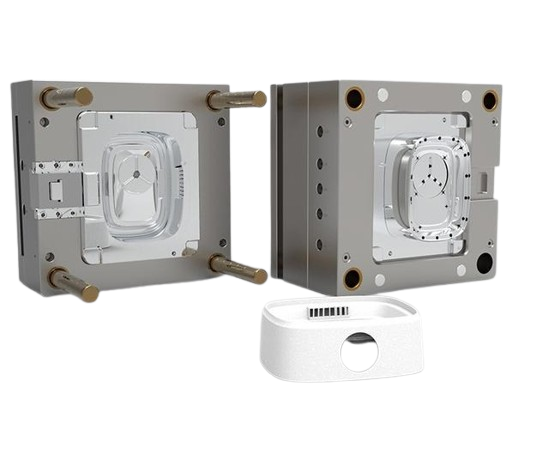
Standards
Maximum Part Size: 1200×1000×500 mm
Manimum Part Size: 5×5×5 mm
Part to Part Repeatability: +/- 0.1 mm
Mold Cavities: Single-cavity molds, multi-cavity molds, family molds
Available Mold Types: Steel and aluminum molds. Production levels below 1000, 5000, 30000, and over 100000 uses
Mold Cavity Tolerances: +/- 0.02 mm
Secondary Operations: Mold texturing, pad printing, laser engraving, threaded inserts, and basic assembly
Undercuts: Y-type, L-type undercuts
Wall Thickness: 0.5 mm to 5 mm
Draft: 0.5° to 2°
Ribs/Gussets: 0.5 mm to 3 mm thick
Bosses: Diameter 3 mm to 10 mm
Lead Time: Most orders can be completed within 15 working days
Video
How Are Your Injection Molding Products Made?
Uncover the secrets behind precision injection molding—watch the step-by-step process that ensures top-quality results for your business.
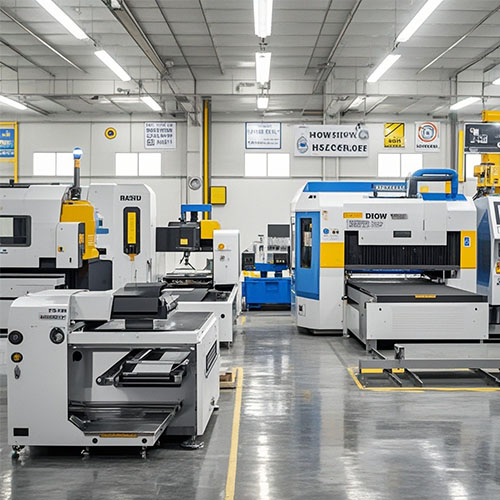
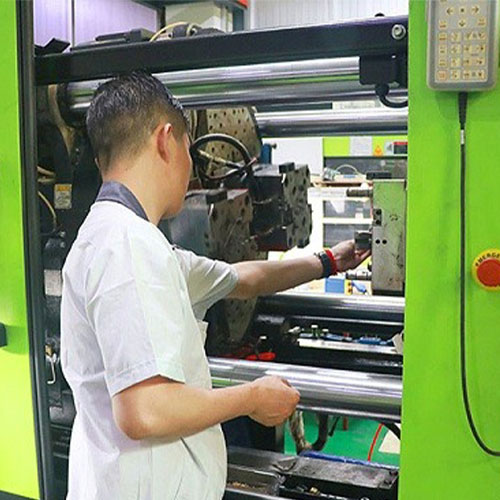
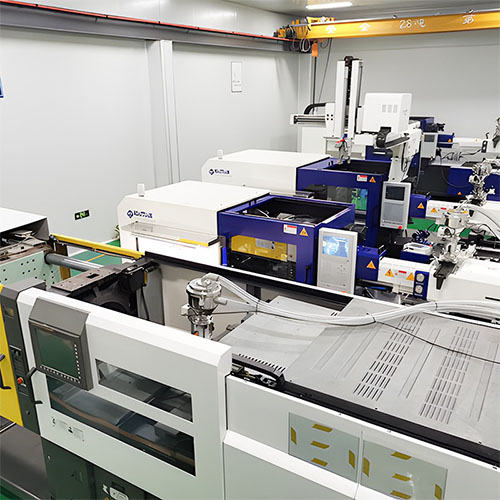
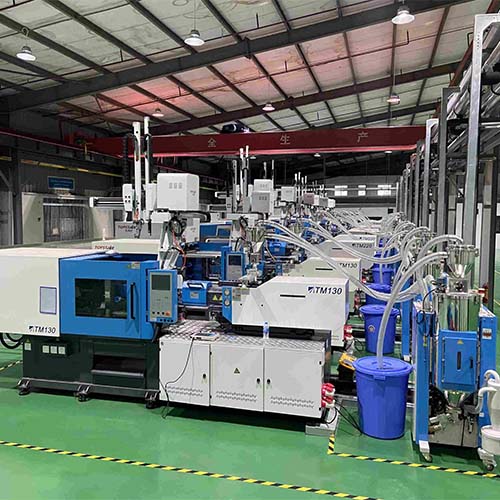
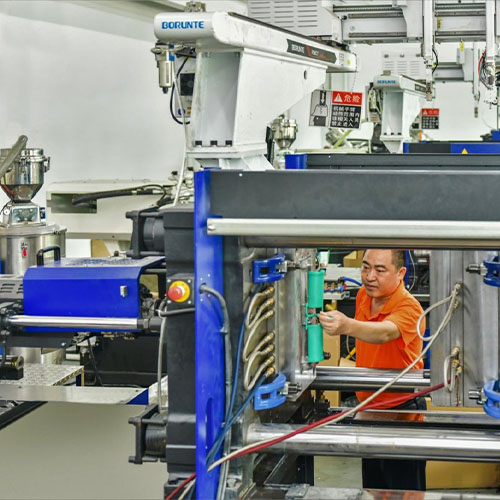
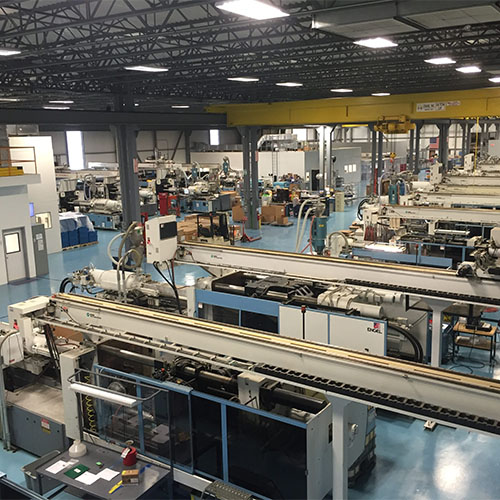
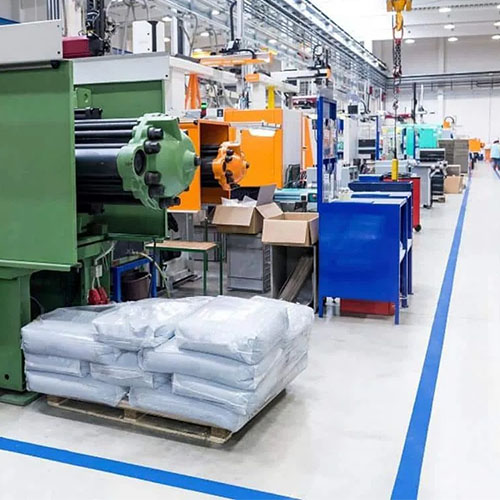