Introduction: Why CNC Machining Manufacturers Matter in 2025
CNC machining is one of the most important processes in modern manufacturing, enabling businesses to produce high-precision parts across various industries. As we enter 2025, CNC machining manufacturers play a crucial role in driving the innovation and productivity of companies worldwide. The demand for CNC machined parts has skyrocketed in industries like aerospace, automotive, medical devices, and more. With technological advancements and industry trends evolving rapidly, choosing the right manufacturer has never been more important. This article explores the top CNC machining manufacturers to know in 2025, what sets them apart, and how to navigate the ever-changing landscape of the CNC machining world.
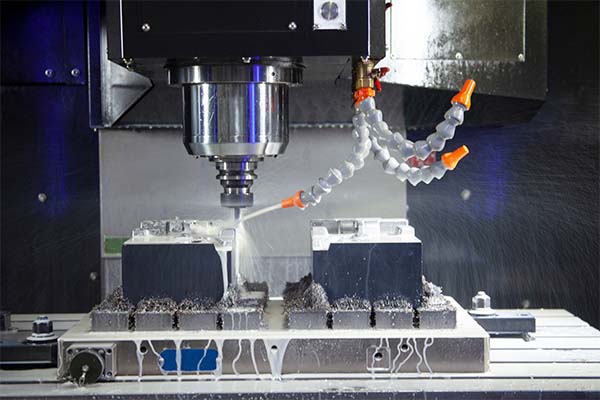
O que é usinagem CNC e por que ela é importante?
CNC machining, or Computer Numerical Control machining, is a process where computer-controlled machines are used to create precise parts from raw materials. These machines follow programmed instructions to perform tasks such as cutting, drilling, milling, and turning. CNC machining has become essential because it allows manufacturers to produce high-precision, complex parts with minimal human intervention. The most common types of CNC machines include CNC mills, CNC lathes, CNC routers, and CNC grinders, each suited for specific tasks. The technology is used in industries that demand high-quality, durable parts, including aerospace, automotive, medical, and electronics.
CNC machining is crucial for modern manufacturing because of its ability to provide precision and repeatability, making it ideal for creating parts that need to meet stringent industry standards. Additionally, CNC machines can work with a variety of materials, including metals, plastics, and composites, allowing manufacturers to offer custom solutions for diverse industries. The process also significantly reduces production time compared to traditional methods, making it a valuable tool for businesses looking to scale their production while maintaining high quality.
Industries That Rely on CNC Machining
CNC machining plays a vital role in several industries. In aerospace, for instance, the demand for lightweight, yet highly durable components is met with precision CNC machining. The medical field also benefits greatly from CNC machining, particularly when it comes to creating implants, prosthetics, and surgical tools that require absolute accuracy. Automotive manufacturers use CNC machines to produce intricate engine components, parts for the body, and interior details. Electronics companies rely on CNC machining to manufacture connectors, housing for devices, and other critical components. The versatility and precision of CNC machining make it indispensable across various sectors.
Key Factors to Consider When Choosing a CNC Machining Manufacturer
When selecting a CNC machining manufacturer, several factors should be taken into account to ensure that your project runs smoothly and meets your quality standards. The most important considerations include the manufacturer’s experience, the quality control measures they implement, and their ability to meet deadlines.
Controle de qualidade
High-quality CNC machining manufacturers employ strict quality control processes to ensure that the parts they produce are free from defects. These processes might include inspections at various stages of production, as well as final inspections to verify that the finished parts meet the required specifications. Manufacturers often hold industry certifications like ISO 9001, which indicates they follow internationally recognized quality management standards.
Experience and Expertise
The experience of a manufacturer is critical in determining their ability to handle complex projects. A company with years of experience in CNC machining will likely have encountered a variety of materials, designs, and challenges, making them well-equipped to handle your specific needs. Moreover, their expertise in your industry can offer additional assurance that they can meet the technical requirements and compliance standards.
Capacity and Capabilities
Capacity refers to the manufacturer’s ability to handle your order size and complexity. Some CNC machining companies may specialize in large volume production, while others are better suited for smaller, custom orders. Understanding the manufacturer’s capacity helps ensure that they can deliver on time and meet your project’s specific needs.
Lead Time and Delivery Reliability
When choosing a CNC machining manufacturer, it’s essential to consider their lead time and ability to meet deadlines. Delays in production can affect the overall timeline of your project, causing disruptions further down the supply chain. It’s important to select a manufacturer with a proven track record of delivering parts on time and who can work with you to meet deadlines.
Pricing Structure
Pricing in CNC machining can vary depending on factors like the complexity of the part, the materials used, and the volume of the order. While price is important, it’s crucial to balance cost with quality and capabilities. Opting for the cheapest option may not always result in the best value if it leads to issues with quality or delays.
Customer Service and Support
Effective communication is key to a successful partnership with a CNC machining manufacturer. A company that offers strong customer support will work closely with you to address any concerns, provide updates on your order, and assist with any modifications or customizations. The best manufacturers value long-term relationships and are committed to providing excellent service.
The Importance of Industry Certifications in CNC Machining
Industry certifications are an essential aspect of selecting a CNC machining manufacturer, as they ensure that the company follows rigorous standards for quality and process control. The most common certifications in CNC machining include ISO 9001, which outlines the requirements for a quality management system, and AS9100, which is tailored to the aerospace industry.
ISO 9001
ISO 9001 is one of the most widely recognized certifications for quality management systems. It sets a framework for organizations to ensure their processes meet the needs of customers while adhering to legal and regulatory requirements. A manufacturer with ISO 9001 certification demonstrates a commitment to maintaining high-quality production standards and continuous improvement.
AS9100 (Aerospace)
AS9100 is a certification specifically for companies operating in the aerospace sector. It builds on the ISO 9001 standards, with additional requirements to ensure safety, reliability, and compliance with stringent aerospace regulations. Manufacturers with AS9100 certification are trusted to produce parts that meet the high safety and performance standards of the aerospace industry.
Other Relevant Certifications
Depending on the industry, CNC machining manufacturers may hold other certifications to demonstrate their expertise in specific areas. For example, the medical industry may require manufacturers to adhere to ISO 13485, which outlines the requirements for a quality management system in the production of medical devices. Understanding the certifications that apply to your project can help ensure that your chosen manufacturer is capable of meeting industry-specific standards.
How Certifications Impact Manufacturer Reliability
Certifications offer assurance that the manufacturer follows internationally recognized quality control practices and is committed to maintaining high standards. When choosing a CNC machining manufacturer, it’s crucial to verify their certifications to ensure that they are capable of delivering parts that meet the necessary specifications and regulatory requirements.
2025 CNC Machining Trends: What to Watch For
As we look ahead to 2025, several key trends are shaping the future of CNC machining. These trends reflect technological advancements that are revolutionizing the industry and improving manufacturing processes.
Automation and AI
One of the most significant trends in CNC machining is the integration of automation and artificial intelligence (AI). CNC machines are becoming more intelligent, with advanced systems that can monitor performance in real-time, detect issues, and even adjust machining parameters automatically. This helps improve efficiency, reduce errors, and lower production costs.
Advanced Materials
In 2025, we can expect to see increased use of advanced materials, such as composites and lightweight alloys, in CNC machining. These materials are often stronger and more durable than traditional metals, making them ideal for applications in industries like aerospace and automotive. Manufacturers will need to invest in machines that can handle these materials without compromising on precision.
Sustentabilidade na Usinagem CNC
Sustainability is an ongoing concern for manufacturers across all industries, and CNC machining is no exception. In 2025, more manufacturers will focus on reducing waste, minimizing energy consumption, and using environmentally friendly materials. Sustainability practices, such as recycling metal waste and using energy-efficient machinery, will become increasingly important in the coming years.
3D Printing Integration
The integration of 3D printing with CNC machining is becoming more prevalent, allowing manufacturers to create prototypes and complex geometries quickly. In some cases, CNC machines are used to finish 3D printed parts, improving their precision and surface quality. This hybrid approach to manufacturing offers greater flexibility and faster turnaround times.
Remote Monitoring and IoT
The Internet of Things (IoT) is transforming CNC machining by allowing machines to communicate with each other and with external monitoring systems. This connectivity enables real-time data collection, which can be used to improve machine performance, predict maintenance needs, and ensure that production runs smoothly.

Top CNC Machining Manufacturers to Know in 2025
In 2025, several CNC machining manufacturers stand out for their capabilities, innovation, and expertise in handling complex projects. These manufacturers have earned their place among the top contenders due to their advanced technology, commitment to quality, and ability to deliver on time.
Company #1: XYZ CNC Machining
XYZ CNC Machining is a leader in the industry, offering state-of-the-art technology and expertise in a variety of industries, including aerospace, automotive, and medical. The company is known for its precision machining and quick turnaround times. With advanced CNC machines and a highly skilled workforce, XYZ CNC Machining is capable of handling projects of any size and complexity. Their dedication to quality control ensures that every part meets the highest standards.
Company #2: ABC Precision
ABC Precision is another top player in the CNC machining space, offering a wide range of services, including milling, turning, and precision grinding. The company is renowned for its work in the aerospace and automotive sectors, where precision and reliability are paramount. With a focus on customer satisfaction and product quality, ABC Precision is trusted by companies around the world to deliver high-quality parts on time.
Company #3: DEF Engineering Solutions
DEF Engineering Solutions specializes in providing CNC machining services for custom projects and prototypes. Known for their flexible approach and innovative solutions, they work with clients in industries such as robotics, defense, and electronics. DEF Engineering Solutions prides itself on its ability to adapt to unique challenges, making it a top choice for businesses that require highly specialized parts.
Specialization in CNC Machining: Understanding the Niche Players
While many CNC machining manufacturers serve a wide range of industries, some specialize in specific niches that require specialized expertise. These manufacturers focus on providing solutions for industries with unique demands, such as aerospace, medical devices, or custom solutions.
Medical Device Manufacturing
In the medical industry, CNC machining manufacturers must adhere to strict regulatory standards and produce parts with high precision and reliability. Companies specializing in medical device manufacturing focus on creating components such as surgical instruments, implants, and prosthetics. These manufacturers are skilled in working with materials like titanium and medical-grade plastics, ensuring that the parts are both functional and safe.
Aerospace and Defense
The aerospace and defense industries require parts that are lightweight, strong, and durable. CNC machining manufacturers specializing in these sectors focus on creating components for aircraft, spacecraft, and defense systems. These parts often need to meet stringent safety and performance standards, making precision machining essential. Aerospace CNC machining also requires a deep understanding of advanced materials, such as titanium alloys and composites.
Automotive Industry
Automotive manufacturers rely on CNC machining to produce a wide range of parts, from engine components to interior details. CNC machining allows for the production of complex parts with high accuracy, which is crucial in the automotive industry, where parts must fit together perfectly. Manufacturers specializing in the automotive industry focus on creating high-volume parts with a quick turnaround, meeting the demands of fast-paced production schedules.
Custom Solutions
Some CNC machining manufacturers offer custom solutions for clients in various industries. These manufacturers focus on creating one-of-a-kind parts or small batches of parts that require unique designs or specifications. Custom CNC machining is ideal for businesses that need parts tailored to their exact needs, whether for prototypes, specialized machinery, or other unique applications.
How Global CNC Machining Manufacturers Differ from Local Ones
When choosing a CNC machining manufacturer, businesses have to decide whether to work with a global manufacturer or a local one. Both options have their advantages and disadvantages, depending on factors like project size, timeline, and budget.
Global vs. Local Production
Global CNC machining manufacturers typically have a larger capacity and the ability to handle high-volume orders. These companies often have access to advanced technologies and a wider range of materials. However, working with global manufacturers can lead to longer lead times and potential communication challenges due to time zone differences.
Benefits of Working with Local Manufacturers
Local CNC machining manufacturers offer several advantages, such as faster lead times, easier communication, and reduced shipping costs. Working with a local manufacturer can also lead to better collaboration, as you can visit the facility and discuss your project in person. Local manufacturers are often more flexible when it comes to customization and special requests.
When to Choose Global vs. Local
The choice between global and local manufacturers depends on the specific needs of your project. If you require a high volume of parts and have a longer lead time, a global manufacturer may be the better choice. However, if you need custom parts quickly and prefer close communication, a local manufacturer might be the ideal option.
What to Expect from CNC Machining Manufacturers in Terms of Lead Times
Lead time is a crucial factor to consider when working with CNC machining manufacturers. It can impact the overall timeline of your project, affecting everything from product delivery to the final assembly of your product. Lead time in CNC machining refers to the amount of time it takes for a manufacturer to complete a production run from receiving the order to delivering the finished parts.
Factors That Impact Lead Times
Several factors influence CNC machining lead times. The complexity of the part is one of the biggest determinants. More intricate parts that require specialized machinery or advanced processes will naturally take longer to produce. Additionally, the materials used can affect production time. For instance, harder metals like titanium require more machining time than softer materials like aluminum. Machine availability and operator efficiency also play a role in determining lead time. High-demand manufacturers may have limited machine capacity, resulting in longer waiting times for your project.
How to Manage Lead Times
Managing lead times effectively requires clear communication with your chosen CNC machining manufacturer. Ensure you provide accurate designs and specifications upfront to minimize delays due to revisions or misunderstandings. Working with a manufacturer that has a reputation for meeting deadlines is critical. To manage lead times, it’s also a good idea to account for potential delays such as material shortages or machine breakdowns, which can affect production schedules.
What Is Considered a “Good” Lead Time?
A “good” lead time depends on the industry and the complexity of the part. For simple parts, a lead time of 1-3 weeks may be typical, while more complex parts or high-volume orders may require 4-6 weeks or more. When selecting a manufacturer, it’s important to discuss your expectations and confirm that they can meet your timeline.
Customer Testimonials and Case Studies: Real-World Applications of CNC Machining
Customer testimonials and case studies provide invaluable insight into how CNC machining manufacturers operate and what you can expect when partnering with them. These real-world applications showcase how CNC machining solves specific challenges and helps businesses achieve their goals.
Success Stories
Many CNC machining manufacturers have successfully completed projects that highlight their capabilities. For example, one manufacturer might have produced parts for a medical device company, ensuring that the components were made to exacting standards of precision. Another case study might showcase how a manufacturer helped an aerospace company reduce its production time by implementing advanced machining techniques. These success stories demonstrate the effectiveness of CNC machining in a wide variety of industries.
How CNC Machining Solved Common Problems
CNC machining has proven effective in addressing several common manufacturing problems. For instance, a company struggling with the complexity of its product design might work with a CNC machining manufacturer to produce intricate, custom parts with a high level of precision. Similarly, a business in need of reducing production costs might partner with a CNC manufacturer that uses automated systems to improve efficiency and reduce the need for manual labor.
The Importance of Reviewing Customer Feedback
Before choosing a CNC machining manufacturer, it’s important to review customer feedback and testimonials. Positive reviews from past clients can provide reassurance about the manufacturer’s capabilities and reliability. You can learn a lot from customers who have worked with the manufacturer in the past, as they can offer insights into lead times, quality, and customer service.
Common Challenges When Working with CNC Machining Manufacturers
Despite their many advantages, working with CNC machining manufacturers is not without challenges. Understanding these challenges can help businesses prepare and address any issues that may arise during the production process.
Quality Inconsistencies
One of the most common challenges faced when working with CNC machining manufacturers is inconsistency in quality. Even the best manufacturers can sometimes experience deviations in part quality due to factors like machine wear, tool defects, or operator error. It’s essential to work with manufacturers who implement strict quality control procedures and who can quickly address any issues when they arise.
Miscommunications
Miscommunications between the manufacturer and the customer can lead to delays and mistakes in production. It’s important to provide clear, detailed specifications and maintain open lines of communication throughout the process. Regular updates and check-ins can help prevent misunderstandings.
Supply Chain Disruptions
External factors like material shortages, shipping delays, and supply chain disruptions can affect CNC machining production timelines. While manufacturers typically plan for such issues, it’s essential to discuss potential risks with your chosen manufacturer and have contingency plans in place to minimize delays.
How to Overcome These Challenges
To overcome common challenges, businesses should work closely with manufacturers and establish clear expectations from the outset. Regular communication, accurate specifications, and proper documentation are key to avoiding miscommunications. Additionally, choosing a manufacturer with a strong track record of reliability and quality control can help reduce the likelihood of encountering quality issues.
The Role of CNC Machining Manufacturers in Your Supply Chain
CNC machining manufacturers play a critical role in your supply chain, as they provide the precision parts needed to assemble your final products. The role of a CNC manufacturer goes beyond just producing parts—it also involves collaborating with other parts of your supply chain to ensure smooth production processes.
Integrating CNC Machining into Your Workflow
CNC machining manufacturers need to be well-integrated into your workflow to ensure that your parts are delivered on time and meet your quality standards. This requires sharing production schedules, quality requirements, and delivery deadlines. A good CNC machining partner will help streamline your workflow and offer solutions to challenges that may arise during production.
The Importance of Strong Supplier Relationships
Building strong relationships with CNC machining manufacturers is vital for success. Manufacturers who understand your business and its specific needs can offer better service, flexibility, and support throughout the project. A long-term partnership with a trusted CNC machining manufacturer can lead to smoother production runs, lower costs, and more consistent results.
Optimizing Your Supply Chain with CNC Machining
CNC machining can help optimize your supply chain by providing fast turnaround times, reducing the need for manual labor, and ensuring that parts are produced to the highest standards of quality. By working with a CNC machining manufacturer that understands your needs and has the capacity to deliver, you can enhance the overall efficiency of your supply chain.
Pricing CNC Machining Services: How to Get the Best Value
Pricing is an important consideration when selecting a CNC machining manufacturer. While cost is always a factor, it’s essential to balance pricing with quality and capabilities. The price of CNC machining services depends on several factors, including the complexity of the part, the materials used, and the volume of the order.
Factors That Influence CNC Machining Costs
Several factors contribute to the cost of CNC machining. The complexity of the design is a major determinant, as more intricate parts require more machine time and specialized equipment. The material used also plays a significant role in pricing—harder materials like steel or titanium tend to cost more to machine. Additionally, higher volumes of production may result in lower per-unit costs due to economies of scale.
How to Get Accurate Quotes
To receive an accurate quote for CNC machining services, it’s important to provide the manufacturer with detailed information about the project. This includes technical drawings, material specifications, and the required quantity of parts. It’s also essential to discuss lead times and any specific requirements or customizations that may impact the price.
Balancing Quality with Cost
While it may be tempting to choose the lowest-priced option, it’s important to consider the long-term value that a CNC machining manufacturer can offer. A cheaper option may result in lower-quality parts or longer lead times, which can ultimately cost more in the end. Choosing a manufacturer with a strong reputation for quality and reliability can save you time and money in the long run.
Future of CNC Machining: What’s Next for Manufacturers and Their Customers?
The future of CNC machining looks bright, with several technological advancements poised to transform the industry. As CNC machining continues to evolve, manufacturers and their customers will benefit from greater efficiency, precision, and customization options.
AI and Automation
Artificial intelligence and automation are expected to play an increasingly important role in CNC machining. AI algorithms can analyze production data and make real-time adjustments to improve efficiency and quality. Automation can reduce labor costs and increase throughput, making CNC machining more accessible to a wider range of industries.
Sustainability and Green Technologies
Sustainability is becoming a key focus in manufacturing, and CNC machining is no exception. More manufacturers are adopting green technologies, such as energy-efficient machines, sustainable materials, and recycling programs, to reduce their environmental footprint. In the future, CNC machining will continue to evolve to meet the growing demand for eco-friendly manufacturing practices.
Next-Gen Materials
The development of new materials, such as lightweight alloys and advanced composites, will continue to drive innovation in CNC machining. These materials offer improved performance and durability, making them ideal for industries like aerospace and automotive. CNC manufacturers will need to invest in new technologies and training to keep up with these advancements.
The Potential for 3D-Printed CNC Parts
As 3D printing technology continues to advance, it will be integrated more closely with CNC machining. Hybrid manufacturing methods, which combine CNC machining and 3D printing, will allow manufacturers to produce parts that are both complex and precise. This combination of technologies opens up new possibilities for innovation and customization in CNC machining.
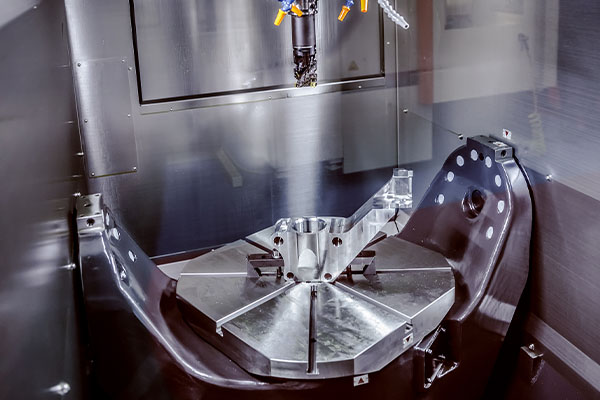
Conclusion: How to Choose the Right CNC Machining Manufacturer for Your Needs
When choosing a CNC machining manufacturer, it’s essential to consider factors such as quality, experience, capabilities, and pricing. By selecting a reputable manufacturer that can meet your specific needs, you can ensure that your project is completed on time and to the highest standards.
Recap of Key Points: Always evaluate the manufacturer’s quality control procedures, expertise in your industry, and ability to meet deadlines. Certifications and customer testimonials can also provide insight into the manufacturer’s reliability.
Final Thoughts: The right CNC machining manufacturer can make all the difference in the success of your project. Take the time to research your options, ask questions, and select a partner who can provide the precision and quality you need.
Chamada para ação: Are you ready to partner with a top CNC machining manufacturer? Reach out to a trusted supplier today to discuss your project requirements and get started on your next manufacturing venture.
Seção de perguntas frequentes
What industries use CNC machining?
CNC machining is used in industries such as aerospace, automotive, medical devices, electronics, and defense.
What are the most common CNC machining processes?
The most common processes include milling, turning, drilling, grinding, and EDM (Electrical Discharge Machining).
How much does CNC machining cost?
CNC machining costs vary depending on factors like material, part complexity, and volume. Generally, more complex parts and higher-end materials cost more.
What materials can be used in CNC machining?
Common materials include metals like aluminum, steel, and titanium, as well as plastics and composites.
How do I choose the right CNC manufacturer for my project?
Consider factors like experience, quality control, pricing, capacity, and customer reviews. Ensure that the manufacturer has the capabilities to meet your specific needs.
How do CNC machines achieve such precision?
CNC machines use computer programs to control movement with extremely high precision. They can make exact measurements down to micrometers, ensuring consistent quality.
Can CNC machining handle complex designs?
Yes, CNC machining is ideal for creating complex, intricate designs that would be difficult to achieve with traditional methods.
What’s the difference between CNC and traditional machining?
Traditional machining requires manual labor to control the machines, whereas CNC machining is automated and computer-controlled, allowing for greater precision and efficiency.