Introdução
Multi-axis milling is a type of machining process used to shape and cut materials with high precision. It refers to the ability of a milling machine to move a cutting tool or workpiece along multiple axes simultaneously, which allows manufacturers to produce complex and intricate parts that traditional 3-axis milling machines can’t achieve. In this article, we’ll explore what multi-axis milling is, its benefits, applications, and how it works. By the end of this guide, you’ll understand the importance of multi-axis milling in modern manufacturing.
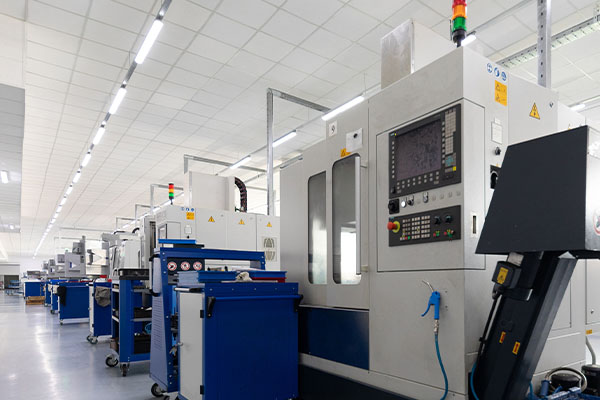
1. What is Multi-Axis Milling?
Multi-axis milling is a precision machining process that allows a cutting tool to move in multiple directions, typically along three or more axes. Unlike traditional 3-axis milling, where the tool can only move in the X, Y, and Z directions, multi-axis milling adds rotational movements, allowing the tool to move along additional axes. This enables manufacturers to produce more complex geometries and shapes.
But here’s the kicker—multi-axis milling offers capabilities that make it ideal for industries where precision and intricate part designs are crucial. Whether you’re in the aerospace, automotive, or medical device manufacturing industries, multi-axis milling machines are key to staying ahead of the competition.
Let’s take a closer look at the different types of multi-axis milling systems. These typically range from 4-axis to 5-axis machines, with some systems capable of up to 6 or more axes. Each machine has its unique strengths, and the choice largely depends on the complexity of the parts being produced. For example, 4-axis milling machines have one rotational axis, while 5-axis milling machines allow for two rotational movements. The more axes you have, the greater your ability to produce parts with complex geometries in a single setup.
2. How Does Multi-Axis Milling Work?
Multi-axis milling machines work by simultaneously moving the cutting tool and the workpiece along multiple axes, providing higher precision and flexibility. The cutting tool’s movements are controlled by a Computer Numerical Control (CNC) system, which is programmed with the necessary instructions to cut materials accurately.
What’s the real story behind how these systems achieve such precision? Well, the key is in the way each axis works in coordination with one another. In a 5-axis milling machine, for example, the cutting tool can move along the X, Y, and Z axes while also rotating along two additional axes (usually A and B). This ability to rotate the tool and workpiece ensures that the cutting tool can reach virtually any angle, reducing the need for repositioning the workpiece during production. It also eliminates errors caused by tool reorientation.
To understand this better, think of it like an artist sculpting a statue. Instead of being limited to one direction, they can approach the material from all angles, creating more intricate and precise designs in less time.
3. What Are the Advantages of Multi-Axis Milling?
The primary advantages of multi-axis milling lie in its ability to handle complex geometries, improve machining efficiency, and reduce the number of setups required. Let’s break these down further.
- Increased precision and efficiency: Multi-axis machines can produce parts with higher precision because they eliminate the need for multiple setups. By reducing the number of times a workpiece has to be repositioned, the chance of error is minimized, and the overall efficiency is improved.
- Reduced production time: Since multi-axis milling allows for more complex cuts in a single setup, you can save a significant amount of time compared to traditional methods. This is especially important for high-volume production runs.
- Ability to create complex geometries: Multi-axis machines can handle complex part designs that would be difficult or even impossible for traditional machines. From intricate aerospace components to medical devices, multi-axis milling is ideal for producing parts with tight tolerances and complex features.
Ready for the good part? These advantages also translate into cost savings in the long run, as the reduction in production time and setup requirements can lead to lower overall manufacturing costs.
4. When Should You Use Multi-Axis Milling?
Multi-axis milling is ideal for a wide variety of industries, including aerospace, automotive, and medical manufacturing. Let’s dive into some of the situations where multi-axis milling is the go-to choice for manufacturers.
- Complex part designs: If you’re working on a part with intricate details that need to be machined from multiple angles, multi-axis milling is your best bet. It allows you to produce parts with complex shapes and tight tolerances.
- Produção de alto volume: Multi-axis milling helps speed up production by allowing manufacturers to produce more parts in less time. This is especially useful for industries like automotive, where high-volume production runs are common.
- Reduced tooling and reorientation time: Traditional machining methods require multiple setups and tool changes, which can lead to increased downtime. With multi-axis milling, you can reduce the need for reorientation and tooling changes, streamlining the entire process.
This is where it gets interesting—the flexibility of multi-axis milling means it can be applied across a wide range of industries and applications, making it an indispensable tool in modern manufacturing.
5. What Types of Materials Can Be Processed with Multi-Axis Milling?
Multi-axis milling machines can handle a variety of materials, ranging from metals like aluminum and titanium to plastics and composites. Let’s explore some of the materials that benefit most from this machining process.
- Metais: Multi-axis milling is commonly used in industries that require precise metal parts, such as aerospace, medical, and automotive. Aluminum, titanium, and steel are common materials used in these industries due to their strength and durability.
- Plásticos: Multi-axis milling can also be used to machine plastic materials, especially when tight tolerances and intricate designs are needed. Industries like electronics and consumer goods rely on multi-axis milling to produce plastic components.
- Compósitos: Materials like carbon fiber composites are becoming increasingly popular in industries such as aerospace and automotive due to their lightweight yet strong properties. Multi-axis milling allows for precise cutting of these tough materials, making it ideal for producing complex composite parts.
The ability to process such a diverse range of materials is one of the reasons multi-axis milling has become an industry standard for high-precision machining.
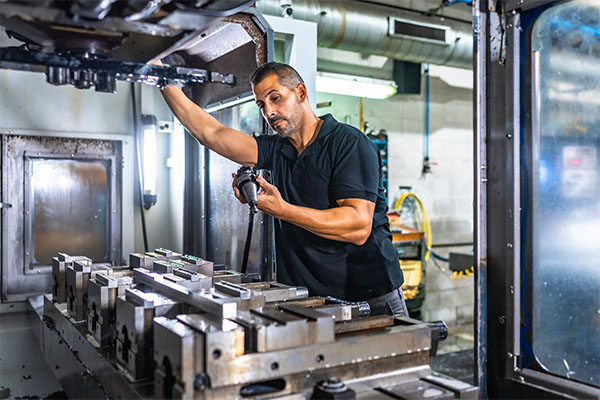
6. What is the Role of CNC in Multi-Axis Milling?
The role of CNC (Computer Numerical Control) in multi-axis milling is crucial. CNC systems control the movements of the cutting tool and workpiece, ensuring the machine operates accurately according to a set of pre-programmed instructions.
But wait, there’s more to CNC systems than just controlling machine movements. CNC allows for the automation of complex processes, enabling manufacturers to produce parts with minimal human intervention. With CNC, the entire machining process can be monitored, adjusted, and fine-tuned remotely, reducing the risk of errors and improving efficiency.
The use of CNC technology in multi-axis milling enables manufacturers to achieve repeatability, precision, and consistency in their products. It also allows for easy programming and reprogramming, making it adaptable to changing production requirements.
7. How to Set Up a Multi-Axis Milling Machine?
Setting up a multi-axis milling machine can be a complex process, but it is essential for achieving high-quality results. Let’s walk through the key steps involved in setting up your machine for optimal performance.
- Selecting the right tools and fixtures: One of the first steps in setting up a multi-axis milling machine is choosing the appropriate cutting tools and fixtures. This will depend on the material you’re machining and the specific features of the part.
- Machine calibration: Proper calibration is essential to ensure that the machine operates within its required tolerances. This includes checking the alignment of the axes, tool offsets, and other critical parameters.
- Programming the CNC system: Once the machine is set up, you’ll need to program the CNC system to ensure the tool movements are precise. This typically involves writing or importing G-code, which contains the instructions the CNC system uses to control the machine.
So, what’s the real story behind all of this? Proper setup is the key to minimizing errors and maximizing efficiency throughout the machining process.
8. What Are the Challenges of Multi-Axis Milling?
While multi-axis milling offers many advantages, it also comes with its own set of challenges. Let’s look at some of the common hurdles faced by manufacturers using multi-axis milling machines.
- High cost: Multi-axis milling machines are more expensive than traditional 3-axis machines, both in terms of initial investment and maintenance. This can be a significant barrier for small manufacturers.
- Complex programming: Programming a multi-axis machine is more complex than programming a traditional machine. It requires specialized knowledge and experience to ensure the machine operates efficiently and accurately.
- Tool wear and tear: Multi-axis milling machines put a lot of strain on tools due to the simultaneous movement of multiple axes. This can lead to faster tool wear, requiring more frequent tool changes and maintenance.
Despite these challenges, the benefits of multi-axis milling often outweigh the drawbacks, especially for manufacturers who require high-precision, complex parts.
9. What Are the Costs Involved in Multi-Axis Milling?
The costs associated with multi-axis milling can vary significantly depending on several factors. These include the type of machine you’re using, the materials being processed, and the complexity of the parts.
- Initial machine cost: Multi-axis milling machines are generally more expensive than 3-axis machines. The higher price reflects the added capabilities and complexity of the machines.
- Maintenance and tooling costs: Multi-axis milling machines require regular maintenance to keep them in optimal working condition. Additionally, the specialized tools used in multi-axis milling can be costly, especially for complex parts.
- Operational costs: The increased precision and efficiency of multi-axis milling machines can reduce overall production costs by minimizing errors and rework. However, the cost savings may not be immediate due to the initial investment and maintenance.
It’s important to consider these factors when deciding whether multi-axis milling is the right choice for your manufacturing needs.
10. How Do You Choose the Right Multi-Axis Milling Machine?
Choosing the right multi-axis milling machine is a critical decision for any manufacturer. The machine you select will depend on several factors, including the complexity of the parts you’re producing and the volume of work.
- Precision requirements: If you need high-precision parts with tight tolerances, you’ll need a machine that can deliver the required level of accuracy.
- Workpiece size: The size of the workpiece will dictate the size of the milling machine you need. Some multi-axis machines are designed for small, intricate parts, while others are built for larger workpieces.
- Budget: The cost of multi-axis milling machines can vary widely, so it’s essential to consider your budget and the long-term ROI of the machine.
This is where it gets interesting—by carefully considering these factors, you can select a multi-axis milling machine that best fits your needs and production requirements.
11. What Are the Latest Trends in Multi-Axis Milling?
The field of multi-axis milling is constantly evolving, with new technologies and innovations being introduced regularly. Here are some of the latest trends in multi-axis milling that are shaping the future of manufacturing.
- Automation: Increasingly, multi-axis milling machines are being integrated with automation systems, allowing for higher levels of efficiency and reduced human intervention.
- Additive manufacturing integration: Some manufacturers are integrating additive manufacturing techniques with multi-axis milling to create even more complex parts that cannot be achieved with traditional methods.
- AI-driven machining: Artificial intelligence is being used to improve the efficiency and precision of multi-axis milling machines by optimizing tool paths and predicting wear patterns.
These trends suggest that multi-axis milling will continue to advance, offering even more opportunities for manufacturers to improve their processes and stay competitive in the market.
12. How Can Multi-Axis Milling Benefit Small Manufacturers?
While multi-axis milling has traditionally been associated with large manufacturers, small manufacturers can also reap the benefits of this technology. Let’s explore how multi-axis milling can benefit small businesses.
- Increased capabilities: Multi-axis milling allows small manufacturers to produce more complex parts that would otherwise be difficult or impossible to create with traditional machines.
- Cost savings: Despite the higher initial investment, multi-axis milling can lead to cost savings in the long run due to reduced setup times, fewer machine reorientations, and increased precision.
- Competitive advantage: By adopting multi-axis milling, small manufacturers can gain a competitive edge in industries that require high-precision, complex parts.
By understanding the advantages of multi-axis milling, small manufacturers can position themselves for success in the highly competitive manufacturing landscape.
13. What Are the Safety Considerations for Multi-Axis Milling?
Safety is a top priority when operating any type of machinery, and multi-axis milling is no exception. Here are some key safety considerations when working with multi-axis milling machines.
- Proper training: Operators should receive thorough training on how to safely operate multi-axis milling machines, including understanding the machine’s movements and how to respond in case of an emergency.
- Protective equipment: Operators should wear appropriate safety gear, including eye protection, hearing protection, and gloves, to minimize the risk of injury.
- Machine maintenance: Regular machine maintenance is crucial for ensuring the safe operation of multi-axis milling machines. This includes checking for worn or damaged parts and ensuring all safety features are functioning properly.
By adhering to proper safety protocols, manufacturers can reduce the risk of accidents and ensure a safe working environment.
14. How Do You Maintain a Multi-Axis Milling Machine?
Proper maintenance of multi-axis milling machines is essential to keep them running smoothly and avoid costly downtime. Here are some tips for maintaining your machine.
- Regular cleaning: Keeping the machine clean is essential for preventing buildup of debris, which can affect performance and precision.
- Tool maintenance: Multi-axis milling machines place a lot of strain on cutting tools, so it’s essential to regularly inspect and replace tools as needed.
- Calibration: Regular calibration is necessary to maintain precision and accuracy. This includes checking machine alignment and tool offsets.
By staying on top of these maintenance tasks, manufacturers can ensure their multi-axis milling machines operate at peak performance for years to come.
15. What Are the Future Prospects of Multi-Axis Milling?
The future of multi-axis milling looks bright, with continued advancements in technology driving the evolution of this machining process. From increased automation to the integration of AI, the capabilities of multi-axis milling machines are expected to expand even further.
As manufacturers seek to improve efficiency and reduce costs, multi-axis milling will play a critical role in meeting these goals. The continued integration of advanced technologies, along with the growing demand for complex, high-precision parts, will ensure that multi-axis milling remains a central tool in modern manufacturing.
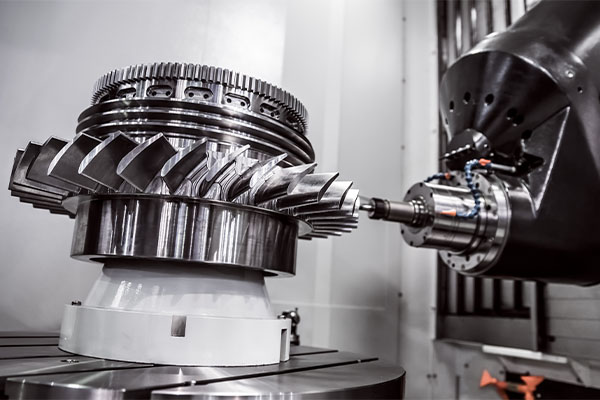
Perguntas frequentes
Q1: What is multi-axis milling?
Multi-axis milling refers to a machining process where a cutting tool moves along multiple axes simultaneously to create parts with complex geometries.
Q2: How does multi-axis milling work?
Multi-axis milling works by controlling the movement of the cutting tool and workpiece along multiple axes, allowing for precise cuts from various angles and reducing setup time.
T3: What are the advantages of multi-axis milling?
The advantages of multi-axis milling include increased precision, faster production times, and the ability to create complex shapes and geometries in a single setup.
T4: What materials can be processed with multi-axis milling?
Multi-axis milling can process a wide range of materials, including metals, plastics, and composites, making it suitable for industries like aerospace, automotive, and medical manufacturing.
Q5: How do you maintain a multi-axis milling machine?
Maintenance includes regular cleaning, inspecting tools for wear, and performing calibration to ensure the machine operates within its required tolerances.