Introdução
PEEK (Polyetheretherketone) material has gained significant attention in the Indústria de usinagem CNC due to its exceptional properties and versatility. The purpose of this article is to dive deep into the advantages, applications, and challenges of machining PEEK material, while also addressing the common concerns that businesses might have when considering it for custom parts. By the end of this post, you’ll have a solid understanding of how PEEK can benefit your business and why it’s an ideal choice for high-performance machining applications.
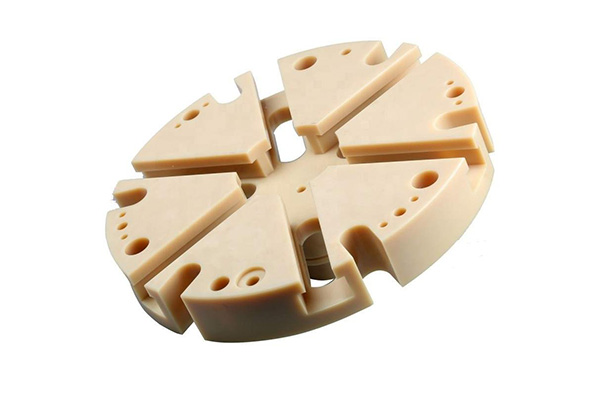
1. What is PEEK material, and why is it important in machining?
PEEK material, commonly referred to as Polyetheretherketone, is a high-performance thermoplastic known for its incredible strength and resistance to extreme conditions. But here’s the kicker – it can withstand temperatures of up to 480°F, making it perfect for industries that deal with high heat and wear. Not only is it heat resistant, but it also boasts excellent chemical resistance, which makes it suitable for a variety of industrial applications.
PEEK is often compared to metals like steel or aluminum due to its high strength-to-weight ratio. It has a unique combination of properties that allow it to function under extreme pressure, high temperatures, and harsh chemical environments. This material is also resistant to wear and tear, making it a durable choice for custom parts.
What’s the real story? PEEK material’s versatility makes it an excellent candidate for a wide range of CNC machining applications. From aerospace components to medical devices, PEEK material is used across various industries due to its ability to handle demanding environments. One of the key reasons PEEK material stands out is its ability to maintain mechanical properties even in extreme conditions, unlike most other plastics or metals.
Table: Key Properties of PEEK Material
Property | Value |
---|---|
Maximum Temperature | 480°F (250°C) |
Tensile Strength | 10,000 psi (69 MPa) |
Chemical Resistance | Excellent (resistant to acids, oils) |
Wear Resistance | Alto |
Aplicações | Aerospace, medical, automotive |
2. How is PEEK material used in CNC machining?
So, you might be wondering, how exactly is PEEK material used in CNC machining? The process involves using computer-controlled machines to precisely cut and shape PEEK into the desired parts. CNC machining is ideal for PEEK because of its ability to achieve tight tolerances and intricate geometries. This is especially crucial for industries like aerospace or medical devices, where precision is key.
PEEK can be machined using a variety of CNC processes, including milling, turning, and drilling. Each process requires specific cutting tools and techniques to ensure the material’s properties are not compromised during machining. For example, carbide tools are often used when machining PEEK due to their durability and ability to handle high heat. But here’s the twist – the heat generated during machining must be carefully managed to prevent the material from degrading.
The versatility of CNC machining for PEEK is evident in its ability to create custom, high-performance parts. With CNC, manufacturers can achieve complex shapes and features such as threads, holes, and other intricate designs. This allows for the creation of one-of-a-kind parts tailored to specific applications.
Table: CNC Machining Techniques for PEEK
Técnica | Description |
---|---|
Moagem | Precision cutting of PEEK into desired shapes |
Virando | Rotating the material to create cylindrical parts |
Perfuração | Creating holes or openings in PEEK material |
Grinding | Smoothing the surface of the material |
3. Why should manufacturers choose PEEK material for CNC machining?
When considering materials for CNC machining, manufacturers often look for strength, durability, and resistance to environmental factors. What’s the real story with PEEK? This material stands out because it delivers all of these qualities, making it the ideal choice for many custom machining applications.
PEEK material’s high tensile strength makes it an excellent choice for parts that need to withstand mechanical stress. Additionally, it is known for its resistance to wear and tear, which extends the lifespan of the components. The material’s superior chemical resistance also ensures that parts made from PEEK can function effectively even in harsh chemical environments. This means that manufacturers can rely on PEEK parts for longer periods without worrying about corrosion or degradation.
Another key benefit is PEEK’s ability to perform well under extreme temperatures. Whether it’s in high-temperature aerospace applications or in medical devices exposed to sterilization processes, PEEK material holds up better than many other alternatives. For industries that demand high-performance parts, PEEK offers an unparalleled combination of attributes.
Table: Benefits of PEEK in CNC Machining
Beneficiar | Explanation |
---|---|
High Strength | Withstands mechanical stress in harsh conditions |
Wear Resistance | Reduces the need for frequent replacements |
Chemical Resistance | Ideal for applications in corrosive environments |
Temperature Resistance | Functions effectively in high-heat environments |
4. What industries commonly use PEEK material in their products?
Ready for the good part? PEEK material is used across a variety of industries, thanks to its unique combination of properties. One of the biggest sectors utilizing PEEK is aerospace. With its ability to withstand high temperatures and mechanical stress, PEEK is a great fit for critical aerospace components such as seals, bearings, and fuel lines. These parts require materials that can perform reliably in extreme conditions – and PEEK does just that.
The medical industry also benefits from PEEK material. Its biocompatibility and resistance to sterilization methods make it ideal for medical devices. From surgical instruments to implants, PEEK material ensures that parts remain durable and effective over time. Additionally, the automotive sector uses PEEK for engine components and other high-performance parts where temperature resistance and strength are essential.
Finally, the industrial sector relies on PEEK material for components that must perform in harsh chemical environments. PEEK is often used for chemical pumps, valves, and seals that need to withstand aggressive substances.
Table: Industries That Use PEEK Material
Industry | Application Examples |
---|---|
Aeroespacial | Seals, bearings, fuel lines |
Medical Devices | Surgical instruments, implants |
Automotive | Engine components, high-performance parts |
Industrial | Chemical pumps, valves, seals |
5. How does CNC machining of PEEK compare to other materials?
What’s the real story here? When it comes to CNC machining, PEEK material often outperforms other plastics and even metals in certain applications. One of the main advantages of PEEK is its ability to withstand high temperatures and mechanical stress without losing its integrity. While traditional plastics like ABS or PVC may perform well in everyday applications, they can degrade quickly when exposed to heat or chemicals. PEEK, on the other hand, holds up under these conditions, making it a more reliable option for custom parts in demanding industries.
Compared to metals, PEEK material offers several benefits. It’s lighter than metals, making it an ideal choice for applications where weight is a concern, such as in aerospace or automotive components. Despite being lighter, PEEK offers similar or even better mechanical properties, such as tensile strength and wear resistance.
One downside is that PEEK machining can be more expensive than machining other plastics due to its high-performance nature. However, the longevity and performance of PEEK components often justify the higher initial cost.
Table: Comparison of PEEK with Other Materials
Material | Força | Temperature Resistance | Custo | Weight |
---|---|---|---|---|
ESPIADA | Alto | Excelente | Alto | Baixo |
abdômen | Médio | Baixo | Baixo | Médio |
Alumínio | Médio | Alto | Médio | Alto |
Aço | Alto | Alto | Médio | Alto |
6. What are the advantages of using PEEK in custom CNC machining?
So, why choose PEEK for custom CNC machining? Well, the versatility of PEEK allows manufacturers to produce high-precision parts with intricate geometries. This is particularly useful in industries like aerospace, where custom components must meet strict design requirements. PEEK material offers not only exceptional strength and durability but also the ability to create custom designs that meet the exact specifications needed for specialized applications.
PEEK also performs well in custom machining because it’s easy to mold and machine into complex shapes. Unlike metals, which can be challenging to work with due to their rigidity and need for specialized tools, PEEK’s thermoplastic nature makes it more malleable. This allows manufacturers to create more detailed and customized parts without sacrificing material performance.
Finally, PEEK material’s cost-effectiveness in the long run is a big draw for businesses. Even though it may have a higher upfront cost, the longevity and reliability of PEEK parts ultimately make them a more economical choice over time.
Table: Advantages of PEEK for Custom CNC Machining
Advantage | Explanation |
---|---|
High Precision | Allows for complex custom designs with tight tolerances |
Malleability | Easier to machine than metals, allowing for more detailed parts |
Long-Term Cost Effectiveness | Durable material that reduces replacement costs over time |
7. What types of CNC machines are used for PEEK machining?
Ready for the good part? When it comes to machining PEEK, the right equipment can make all the difference. The primary CNC machines used for PEEK machining are CNC mills, CNC lathes, and 3D printers. CNC mills are widely used for milling PEEK parts into desired shapes, and CNC lathes are employed to turn the material into cylindrical parts. Both machines allow for high precision and versatility, ensuring that complex features can be added to the material without compromising its integrity.
For more advanced applications, 5-axis CNC machines are also employed. These machines offer enhanced capabilities by allowing the material to be cut from multiple angles, which is essential for intricate designs that require precise detailing. Additionally, 3D printing is becoming an increasingly popular method for PEEK processing, particularly for prototyping.
Table: CNC Machines Used for PEEK Machining
Tipo de máquina | Aplicativo |
---|---|
CNC Mill | Precision cutting for various shapes and sizes |
CNC Lathe | Turning PEEK material into cylindrical parts |
5-Axis CNC | Allows for more complex cutting and shaping |
3D Printer | Ideal for rapid prototyping |
8. What are the common challenges in machining PEEK material?
But here’s the kicker – machining PEEK isn’t without its challenges. The material’s hardness and abrasiveness can cause significant wear on cutting tools, requiring more frequent replacements. To mitigate this, manufacturers often use high-quality carbide tools that can withstand the intense heat generated during the machining process.
Another challenge is the heat generated while machining PEEK. This material has a tendency to melt at high temperatures, so managing heat during the cutting process is crucial. This means that operators need to carefully control feed rates and cutting speeds to ensure that the material doesn’t degrade.
Finally, PEEK material can sometimes produce a rough surface finish after machining, requiring additional post-processing steps like polishing or grinding to achieve the desired smoothness.
Table: Challenges in Machining PEEK
Desafio | Solução |
---|---|
Tool Wear | Use high-quality carbide cutting tools |
Heat Generation | Control feed rates and cutting speeds |
Surface Finish Quality | Post-process with polishing or grinding |
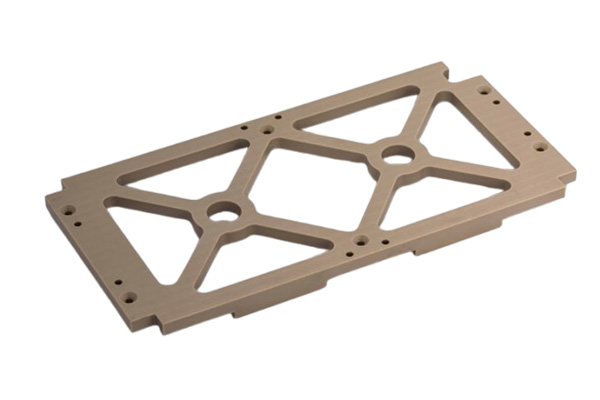
9. How can manufacturers ensure quality when machining PEEK?
What’s the real story here? To ensure top-quality PEEK machining, manufacturers need to follow a strict set of procedures. The key is to choose the right tools for the job. Using carbide tools, for example, can significantly reduce tool wear and improve precision when cutting PEEK. Regular maintenance and calibration of CNC machines are also essential for maintaining high machining standards.
Additionally, controlling the machining environment plays a huge role in quality. By carefully managing temperatures and cutting speeds, manufacturers can avoid material degradation and achieve a more precise and reliable finished product. Regular inspection and testing during the machining process also help ensure that parts meet all necessary specifications.
Table: Ensuring Quality in PEEK Machining
Quality Control Factor | Explanation |
---|---|
Tool Selection | Use carbide tools for durability and precision |
Machine Maintenance | Regular calibration to ensure optimal performance |
Temperature Control | Manage cutting speeds and temperatures to prevent degradation |
Inspection and Testing | Conduct inspections to verify product specifications |
10. What are the machining costs for PEEK material?
So, how much will it cost to machine PEEK material? Well, the cost of machining PEEK can vary depending on several factors, including the complexity of the part, the machining technique used, and the quantity of parts being produced. Generally speaking, machining PEEK is more expensive than machining traditional plastics due to its high-performance nature. However, the long-term benefits of using PEEK, such as its durability and resistance to extreme conditions, can make it a worthwhile investment.
One way to keep machining costs under control is by optimizing the machining process. By selecting the right tools and controlling feed rates and cutting speeds, manufacturers can improve efficiency and reduce material waste. Additionally, bulk production of PEEK parts can help lower per-unit costs, as setup time and machine calibration are spread over a larger number of units.
Table: Factors Affecting PEEK Machining Costs
Fator | Impact on Cost |
---|---|
Part Complexity | More complex parts require more machining time |
Machining Technique | Advanced techniques like 5-axis CNC machining are more costly |
Quantity of Parts | Bulk production reduces per-unit cost |
11. How can post-machining processes affect the properties of PEEK parts?
Now, this is where it gets interesting… Post-machining processes like polishing, coating, and grinding can significantly affect the properties of PEEK parts. After machining, PEEK parts may have rough surfaces that require further processing to achieve the desired finish. Polishing can enhance the material’s surface smoothness, while coating can add additional layers of protection against environmental factors like corrosion.
These processes can also improve the material’s wear resistance and extend its lifespan. However, it’s important to note that post-machining processes must be performed carefully to avoid damaging the PEEK material or altering its properties.
Table: Post-Machining Processes for PEEK
Process | Purpose |
---|---|
Polishing | Enhances surface smoothness |
Coating | Adds protective layers |
Grinding | Improves dimensional accuracy and surface finish |
12. What are some case studies of PEEK material in CNC machining?
What’s the real story? PEEK material has been successfully used in various industries for CNC machining applications. One notable case is the aerospace industry, where PEEK is used to manufacture lightweight, high-strength components like seals and bearings. These components must withstand extreme temperatures and pressures, and PEEK’s performance under such conditions makes it the ideal material choice.
Another example comes from the medical industry. PEEK is used in the creation of implants and surgical instruments due to its biocompatibility and resistance to sterilization processes. These medical devices require materials that are both durable and safe for long-term use, and PEEK meets these requirements perfectly.
Table: Case Studies of PEEK Applications
Industry | Aplicativo | Example Component |
---|---|---|
Aeroespacial | High-performance components | Seals, bearings |
Medical | Medical devices and implants | Surgical instruments |
Automotive | High-strength components for engines | Engine parts |
13. How can you maintain and care for PEEK CNC-machined parts?
Now let’s move on to the good stuff – maintaining and caring for PEEK parts is relatively simple but crucial to ensuring their longevity. Regular cleaning and inspection are essential to keep PEEK parts performing optimally. For instance, parts should be wiped down with a non-abrasive cloth and mild detergent to remove dirt and debris.
What’s the real story? Because PEEK material is resistant to many chemicals, it can be cleaned using a wide variety of solutions without fear of degradation. However, it’s important to avoid abrasive cleaning methods, as this could damage the surface finish.
Another important aspect of care is preventing wear and tear. Since PEEK is resistant to wear, it doesn’t require as much attention as other materials, but regular inspections to check for cracks or other damage are still necessary.
Table: Maintenance Tips for PEEK Parts
Tip | Explanation |
---|---|
Regular Cleaning | Use mild detergent and non-abrasive cloths |
Preventing Wear and Tear | Inspect for cracks or other signs of damage |
Proper Storage | Store parts in cool, dry conditions to avoid degradation |
14. What should you look for in a CNC machining service provider for PEEK?
So, what should you look for when choosing a CNC machining service provider for PEEK? Well, you want to ensure that the provider has experience with high-performance materials like PEEK. A service provider who understands the intricacies of machining PEEK can help ensure that parts are made to the highest standards and meet your exact specifications.
Additionally, you should consider the provider’s quality assurance practices. A reliable CNC machining service provider will have a strong track record of producing consistent, high-quality parts. Certifications and compliance with industry standards, such as ISO, can also indicate a commitment to quality.
Finally, choose a provider that offers flexibility and customization options. Custom parts require precision and adaptability, so the machining service provider should be able to handle unique requests and adjust their processes accordingly.
Table: Key Considerations for Choosing a CNC Machining Service Provider
Consideração | Explanation |
---|---|
Experience with PEEK | Look for a provider with a strong track record in machining PEEK |
Quality Assurance | Check for certifications and adherence to industry standards |
Customization Options | Ensure flexibility in handling custom requests |
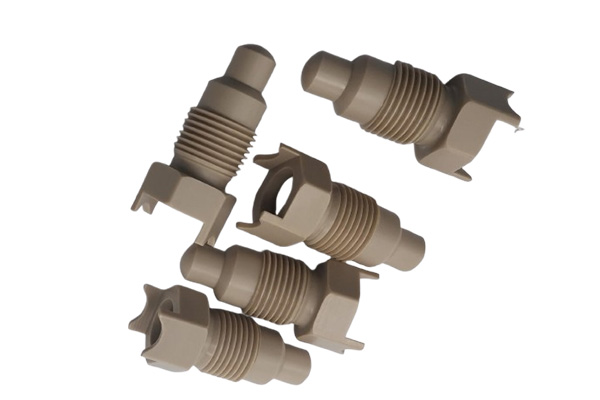
15. How can businesses optimize their PEEK material machining processes?
Finally, let’s talk about optimizing your PEEK machining processes. One of the best ways to improve machining efficiency is by investing in advanced CNC machines that offer greater precision and speed. This reduces cycle time and helps lower the overall production cost.
But here’s the kicker – choosing the right tools for the job can also have a huge impact. Using carbide tools, for instance, can help reduce wear and tear on the machine while ensuring a higher quality finish on the PEEK parts. Additionally, optimizing machine settings, such as feed rates and cutting speeds, can reduce material waste and improve overall efficiency.
Table: Tips for Optimizing PEEK Machining
Tip | Explanation |
---|---|
Invest in Advanced Machines | Use high-performance CNC machines for precision |
Choose the Right Tools | Carbide tools reduce wear and ensure a higher-quality finish |
Optimize Machine Settings | Adjust feed rates and cutting speeds for maximum efficiency |
Conclusão
In conclusion, PEEK material stands out as a superior choice for CNC machining due to its excellent mechanical properties and resistance to extreme environments. By understanding the various aspects of machining PEEK, businesses can take full advantage of its unique capabilities. Whether it’s in aerospace, medical, automotive, or industrial applications, PEEK continues to prove its worth in high-performance machining.