Introduction: What is Automotive CNC Machining?
Automotive CNC machining plays a pivotal role in today’s vehicle manufacturing industry. From engine components to high-precision parts like suspension systems, CNC machining ensures each piece meets the highest standards of quality and performance. But what exactly makes it so vital to automotive manufacturing? It’s simple – CNC machining allows manufacturers to create complex, precise parts in record time. It’s a technology that offers unmatched speed, reliability, and consistency, all of which are essential for the fast-paced automotive world. This article will explore why CNC machining is crucial for automotive parts, its advantages, and how it’s transforming the industry.
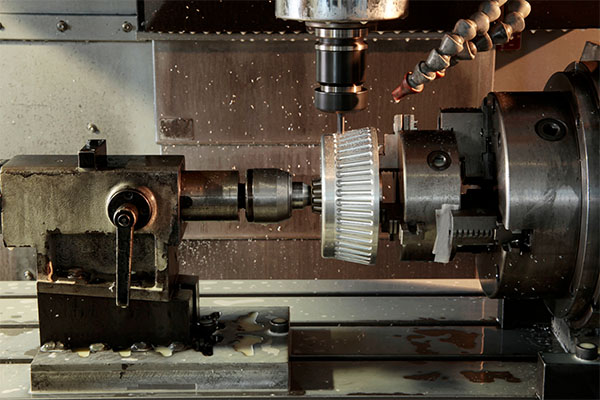
Why CNC Machining is the Preferred Choice for Automotive Parts
CNC machining is widely regarded as the go-to method for manufacturing automotive parts, and for good reason. It allows manufacturers to produce parts with extreme precision, which is crucial in the automotive sector, where performance and safety are top priorities. The ability to create complex shapes and intricate designs makes CNC machining invaluable for producing custom parts tailored to specific vehicle models. Вот в чем дело – the automotive industry requires parts that fit perfectly, function flawlessly, and are ready to go as soon as they are manufactured. CNC machining meets these demands efficiently, providing parts with tight tolerances and minimal defects.
One of the greatest advantages of CNC machining is speed. Once the design is created, CNC machines can churn out multiple parts in a short amount of time, which is particularly important when dealing with high-volume production. This method reduces manual labor and minimizes human error, allowing manufacturers to deliver consistent quality at a much faster pace compared to traditional methods. Whether producing complex engine components or simple interior pieces, CNC machining is capable of delivering both high volume and exceptional quality. So, if you’re aiming to improve productivity without sacrificing quality, CNC machining is the way forward.
Key Benefits of CNC Machining in the Automotive Industry
The automotive industry benefits immensely from CNC machining, making it a go-to manufacturing method for parts of all shapes and sizes. Вам может быть интересно, what exactly are the benefits that make CNC machining so indispensable in the world of automotive manufacturing? Let’s break it down.
- Customization: Automotive manufacturers often require specific designs or unique features that can’t be achieved through traditional methods. CNC machining allows for highly customized parts to be created based on individual specifications, ensuring each part fits its purpose perfectly.
- Speed: The CNC machining process is notably faster than conventional methods. Once the design is finalized, machines can produce a large quantity of parts quickly, reducing turnaround times for car manufacturers. Faster production times also lead to quicker product deliveries, an important factor in the competitive automotive market.
- Cost-effectiveness: Although the initial investment in CNC equipment may seem high, it pays off in the long run. CNC machining minimizes material waste and optimizes the use of raw materials. Additionally, because the process requires minimal human intervention, labor costs are significantly reduced, making it a cost-efficient choice for automotive part production.
- Consistency and Quality: Perhaps the biggest draw of CNC machining is its ability to produce parts with identical dimensions every time. Whether producing 10 parts or 10,000, CNC machines maintain consistency in quality, ensuring each component meets the same high standards.
How Does CNC Machining Work in the Automotive Sector?
Understanding how CNC machining works is key to appreciating its importance in the automotive industry. The CNC (Computer Numerical Control) process uses computer programs to control machine tools, allowing for the automation of tasks that would otherwise require manual labor. In the automotive sector, CNC machines are used to shape, cut, and finish parts with high precision. So, how does it work?
First, a detailed design of the part is created using CAD (Computer-Aided Design) software. Once the design is finalized, CAM (Computer-Aided Manufacturing) software translates the CAD model into machine-readable instructions. These instructions guide CNC machines, such as mills or lathes, to cut, shape, and assemble the part from a block of raw material. The machines operate with incredible accuracy, ensuring that each part is produced to exact specifications.
The materials typically used for automotive parts include metals like aluminum, steel, and titanium, which are selected based on the part’s intended function. CNC machining ensures that these materials are precisely cut and finished, producing high-performance automotive components that meet industry standards.
CNC Machining vs Traditional Manufacturing for Automotive Parts
When comparing CNC machining to traditional manufacturing methods, several key advantages become clear. Why choose CNC machining over traditional methods? Traditional manufacturing processes, like casting or forging, often involve more manual labor and longer production times. In contrast, CNC machining is fully automated, reducing labor costs and minimizing human error. This means parts can be produced faster, with greater accuracy, and at a lower cost.
Traditional methods may also require additional steps, such as molding or heat treatment, which can further extend production times. CNC machining, however, allows for both shaping and finishing in a single step, cutting down production times and increasing efficiency. Another advantage is the versatility of CNC machines. With traditional methods, certain designs or materials may be difficult or impossible to work with. CNC machines, on the other hand, can handle complex geometries and a wide range of materials, making them the go-to choice for custom, high-performance automotive parts.
Materials Used in Automotive CNC Machining
Choosing the right material for CNC machining is essential to ensuring the quality and performance of automotive parts. You’re probably asking, what materials are typically used in CNC machining for automotive components? The answer depends on the specific needs of the part being manufactured, as each material offers unique benefits.
- Алюминий is one of the most commonly used materials due to its light weight, strength, and corrosion resistance. It’s used in engine components, wheels, and suspension parts, where reduced weight can improve fuel efficiency and overall vehicle performance.
- Сталь is another popular material, known for its strength and durability. It’s commonly used in parts that require high tensile strength, such as chassis and transmission components.
- Титан is used for high-performance automotive parts where strength and lightweight properties are crucial, such as in aerospace-grade engines or performance racing vehicles.
Each material has its own set of advantages depending on the part’s requirements, and CNC machining provides the precision necessary to make the most out of these materials.
Types of Automotive Parts Manufactured Using CNC Machining
CNC machining can produce a vast array of automotive parts, from complex engine components to simple interior pieces. Let’s take a look at the types of parts most commonly manufactured using this method.
- Engine Components: Parts like cylinder heads, pistons, and intake manifolds are essential to engine function, and CNC machining provides the precision needed to create these high-performance components.
- Chassis and Suspension Parts: CNC machining is used to manufacture critical components such as suspension arms, axles, and steering columns, all of which must meet rigorous standards for safety and durability.
- Transmission Components: Parts like gearboxes and clutch components require the precise manufacturing capabilities of CNC machining to ensure smooth operation and longevity.
- Custom Aftermarket Parts: Aftermarket manufacturers rely on CNC machining to create custom parts, such as custom exhaust systems, performance modifications, and other specialty components.
- Interior Parts: CNC machining is also used for producing dashboard panels, console components, and trim parts, ensuring that the details in a vehicle’s interior are just as precise as its performance parts.
The Role of CAD/CAM in CNC Machining
The role of CAD (Computer-Aided Design) and CAM (Computer-Aided Manufacturing) software is integral to the CNC machining process. Here’s how they work together to create high-quality automotive parts.
CAD software is used to create a detailed digital model of the part, specifying every dimension, angle, and surface. This design is then translated into machine-readable instructions using CAM software, which controls the CNC machine during the machining process. This seamless integration allows for greater accuracy and efficiency, as the transition from design to production is streamlined. With CAD/CAM, manufacturers can design intricate parts with complex geometries and ensure that they can be manufactured exactly as envisioned.
One of the key advantages of CAD/CAM is that it allows for quick design modifications. If an issue is identified during the design phase, changes can be made easily and quickly. This flexibility is crucial in the fast-paced automotive industry, where time and precision are of the essence.
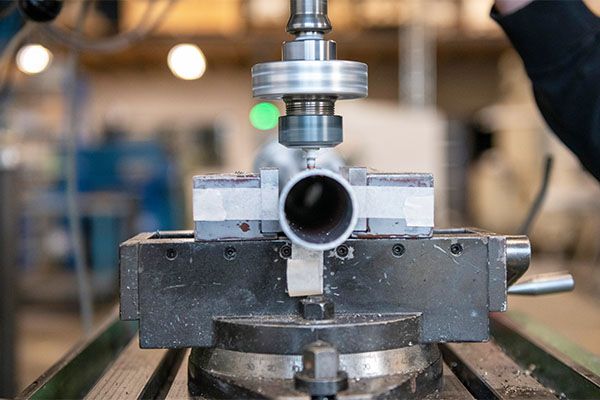
CNC Machining Tolerances: Why They Matter in the Automotive Industry
Tolerances are a critical factor when it comes to CNC machining, particularly in the automotive industry. So, why are tolerances so important? Tolerances refer to the acceptable range of deviation from the desired dimensions of a part. In automotive manufacturing, even the smallest errors can lead to performance issues, safety concerns, or even failure.
Parts like engine components, transmission gears, and braking systems require extremely tight tolerances to function properly. For example, a piston that is off by even a fraction of a millimeter could cause the engine to fail. CNC machining excels at creating parts with tight tolerances, ensuring that every component meets the precise specifications required for optimal performance.
This precision is especially important for high-performance vehicles, where every part must function seamlessly together. CNC machining’s ability to meet these stringent tolerances makes it indispensable in the production of automotive parts that are reliable, durable, and high-performance.
The Impact of CNC Machining on Automotive Performance
CNC machining has a direct impact on the overall performance of vehicles. Вам может быть интересно, how exactly does CNC machining contribute to better automotive performance? It’s all about precision and quality.
High-quality parts produced through CNC machining help improve vehicle efficiency, durability, and safety. For example, perfectly manufactured engine components ensure smoother operation, while well-machined suspension parts result in better handling and stability. By producing parts that fit precisely and function optimally, CNC machining contributes to improved overall vehicle performance, from fuel efficiency to speed and control.
Quality Control in Automotive CNC Machining
Quality control is a vital aspect of CNC machining in the automotive industry. Вот в чем дело, automotive parts need to meet strict industry standards to ensure safety and performance. CNC machining offers several advantages in maintaining high-quality standards throughout the manufacturing process.
First, CNC machines are programmed to follow specific instructions with minimal room for error. This reduces the likelihood of defects caused by human error. Additionally, parts produced through CNC machining are often subjected to stringent quality control measures such as inspections, testing, and measurement. Tools like CMM (Coordinate Measuring Machines) ensure that each part is within the acceptable tolerance range. Furthermore, industry certifications like ISO 9001 and IATF 16949 guarantee that manufacturers meet the necessary quality management standards, providing buyers with additional confidence in the parts produced.
Quality control processes in CNC machining ensure that every part produced meets or exceeds the requirements of automotive manufacturers, ensuring parts are reliable and safe for use.
Challenges in Automotive CNC Machining and How to Overcome Them
Despite its many benefits, CNC machining is not without its challenges. What are the challenges, and how can they be overcome? For one, CNC machining requires skilled operators who are proficient in using complex machinery. Ensuring that operators are well-trained can minimize the risk of human error.
Another challenge is managing the complexity of designs and machining intricate parts. Some parts, especially those with unusual geometries or tight tolerances, can be difficult to machine efficiently. However, advancements in CNC technology, such as multi-axis machines and better software, have made it possible to overcome these challenges.
Finally, cost is a concern for many manufacturers. While CNC machining offers long-term cost savings, the initial investment in machines and software can be high. However, for large-scale production, the benefits far outweigh the initial investment. By optimizing processes and investing in modern technology, these challenges can be mitigated, ensuring efficient and cost-effective production.
The Future of Automotive CNC Machining
The future of CNC machining in the automotive industry looks bright. Вот в чем дело, technology is constantly evolving, and CNC machining is no exception. Advances in automation and robotics are helping manufacturers improve production times and reduce costs. Additionally, new materials and improvements in machining techniques are opening the door to even more opportunities in automotive manufacturing.
The rise of electric vehicles is also having an impact on automotive CNC machining. With new vehicle designs and parts requirements, CNC machining is poised to play a pivotal role in the production of parts for electric cars. As the industry moves toward more sustainable and efficient technologies, CNC machining will continue to evolve to meet these new challenges.
Finding the Right CNC Machining Partner for Your Automotive Needs
Choosing the right CNC machining partner is essential for ensuring high-quality, fast production of automotive parts. Вам может быть интересно, what should you look for in a CNC machining supplier? First and foremost, experience matters. A supplier with a proven track record in automotive machining is more likely to understand the specific requirements of the industry.
Additionally, look for suppliers that offer customization capabilities and can adapt to your specific needs. It’s also important to consider factors like delivery times, cost, and the ability to meet quality standards. When you find the right partner, you’ll have peace of mind knowing your parts will be produced on time, within budget, and to the highest standards.
Conclusion: The Importance of High-Quality, Fast Automotive CNC Machining
In conclusion, CNC machining is a game-changer for the automotive industry. It offers speed, precision, and consistency, all of which are essential for producing high-quality parts that perform well and meet the needs of today’s vehicles. Whether you are looking for custom parts or mass-produced components, CNC machining is the preferred method for getting the job done efficiently and cost-effectively. By embracing CNC technology, manufacturers can stay ahead in the fast-paced automotive world, ensuring that every part is top-notch and ready for the road.

Раздел часто задаваемых вопросов
What are the most common types of automotive parts made using CNC machining?
CNC machining is used to manufacture a wide variety of automotive parts, including engine components such as pistons and cylinder heads, transmission parts, suspension systems, and interior components like dashboard panels. In fact, virtually every part that requires high precision or complex geometries can be produced using CNC technology. This versatility makes it a staple in automotive manufacturing.
How does CNC machining help reduce production costs in the automotive industry?
CNC machining helps reduce production costs by minimizing material waste and labor costs. Because the process is automated, fewer human resources are needed to operate machinery, and the likelihood of defects is drastically reduced. Вот в чем дело – with fewer errors, parts don’t need to be reworked, which cuts down on waste and overall production time, ultimately lowering costs.
What is the role of CAD/CAM in CNC machining for automotive parts?
CAD (Computer-Aided Design) and CAM (Computer-Aided Manufacturing) software are essential to the CNC machining process. Программное обеспечение САПР is used to design the parts, ensuring they meet all required specifications. Then, CAM software takes that design and generates the instructions needed for CNC machines to produce the parts. These tools ensure that parts are made to the exact dimensions and tolerances required for high-quality automotive components.
What materials are commonly used in CNC machining for automotive parts?
The materials used in CNC machining for automotive parts vary based on the part’s function. Алюминий is popular for its light weight and strength, often used in engine components, wheels, and suspension parts. Сталь is widely used for its toughness and strength, suitable for parts like transmission gears and chassis components. Титан, though more expensive, is ideal for high-performance automotive parts due to its superior strength-to-weight ratio.
How does CNC machining impact the performance of automotive parts?
The precision and consistency achieved with CNC machining directly impact the performance of automotive parts. By producing parts with exact measurements and tolerances, CNC machining ensures that each component fits and functions as intended. This leads to better fuel efficiency, improved handling, and overall reliability. In performance vehicles, these precise components are critical to achieving the desired power, speed, and safety standards.
What are the advantages of CNC machining over traditional manufacturing methods?
CNC machining offers several advantages over traditional manufacturing methods, such as increased precision, speed, and cost-efficiency. станки с ЧПУ can create complex parts with very tight tolerances, something that is difficult to achieve with manual labor. Additionally, the process is automated, reducing human error and increasing production speeds, which ultimately lowers overall costs compared to traditional methods like casting or forging.
How do CNC machining tolerances affect automotive part performance?
Tolerances in CNC machining refer to the allowable variations in the dimensions of a part. Tighter tolerances result in more accurate, high-performance parts. In the automotive industry, parts such as pistons, gears, and brake systems require extremely tight tolerances for optimal function. Even a small deviation can lead to malfunction or safety issues, so achieving precise tolerances is crucial in maintaining the performance and safety of the vehicle.
What challenges are faced in automotive CNC machining, and how can they be addressed?
Challenges in CNC machining include material selection, handling complex geometries, and ensuring that parts are produced within strict tolerances. To overcome these challenges, manufacturers invest in advanced CNC technology and ensure that operators are well-trained. Regular maintenance of the machines is also important to prevent breakdowns and ensure smooth operation.
How is the future of automotive CNC machining shaping the industry?
The future of automotive CNC machining looks promising, with advancements in automation, robotics, and artificial intelligence improving speed and precision. As the automotive industry shifts toward electric vehicles, CNC machining will play a crucial role in creating the new types of components required. The integration of Industry 4.0 technologies will make CNC machines smarter, more efficient, and capable of handling even more complex designs and materials.
How do I choose the right CNC machining partner for my automotive manufacturing needs?
Выбор правильного CNC machining partner involves evaluating the company’s experience, capabilities, and reputation in the industry. Look for a supplier that has a proven track record with automotive parts, especially those that require high precision. Additionally, ensure the supplier can meet your production timeline, quality standards, and budget. Clear communication and a collaborative approach are essential to ensuring the successful delivery of your parts.