1. Introduction: Why Accuracy is Crucial in Semiconductor CNC Machining
CNC machining in semiconductor production plays a pivotal role in the fabrication of devices that power modern technologies. As the semiconductor industry evolves, the demand for precision has never been greater. The performance and reliability of a semiconductor chip depend on its intricate components, which require exact tolerances. In this article, we’ll explore the significance of accuracy in semiconductor CNC machining, how it influences the industry, and the cutting-edge technologies that are redefining manufacturing standards. With advances in machine technology, automation, and material science, CNC machining is becoming more precise, pushing the boundaries of what’s possible in chip production.
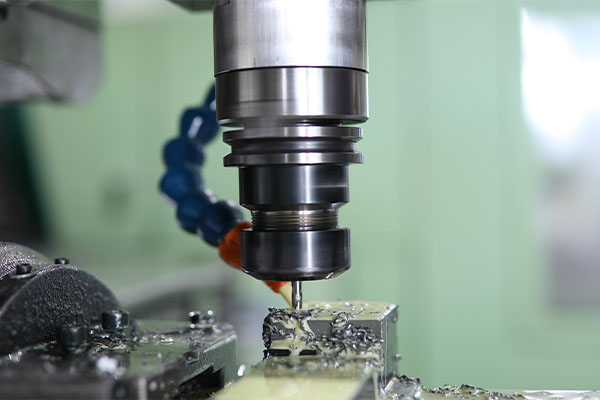
2. Understanding CNC Machining: A Key Technology in Semiconductor Manufacturing
Что такое обработка на станках с ЧПУ?
CNC (Computer Numerical Control) machining is a manufacturing process that uses computer-controlled machinery to perform operations such as drilling, milling, and turning. The technology allows for the precise cutting, shaping, and assembling of materials into highly specific parts. In semiconductor manufacturing, CNC machines play an integral role in producing critical components such as wafers, photomasks, and packaging.
Different Types of CNC Machines Used in Semiconductor Manufacturing
There are several types of CNC machines used in the production of semiconductor components. Vertical CNC machines, for example, are used for more straightforward tasks like drilling and cutting. These machines feature a vertical spindle and are often employed in industries with less demanding tolerances. On the other hand, horizontal CNC machines are designed for more complex operations, allowing for better access to the workpiece from multiple angles. In semiconductor production, the demand for intricate details and multi-axis precision has made 5-axis CNC machines increasingly popular. These machines are equipped with multiple axes of movement, allowing them to execute highly detailed operations on complicated geometries.
How CNC Technology Integrates with Semiconductor Production
CNC machining has revolutionized semiconductor production by enabling manufacturers to produce tiny components with extraordinary precision. For example, CNC machines can mill photomasks, which are used in photolithography, a process that defines circuit patterns on semiconductor wafers. Additionally, CNC machines are used to create the precise cavities and channels needed for packaging microchips. By automating these processes, semiconductor manufacturers can reduce human error, speed up production, and increase output while maintaining the stringent tolerances required for modern electronics.
3. The Challenge of Precision in Semiconductor Manufacturing
Why Precision is Non-Negotiable
In the world of semiconductor manufacturing, even the smallest deviation can result in catastrophic failure. For instance, a misalignment of just a few microns can cause malfunctioning circuits that lead to product failures. Precision is essential not just for aesthetic or mechanical purposes, but for the electrical functionality of semiconductors. The complex nature of semiconductors demands tight tolerances, as even slight inconsistencies in material properties or geometry can lead to costly defects and reduce the overall performance of the final product.
Impact of Tolerances on Performance
Semiconductor chips are designed with extremely small feature sizes. In some cases, features may be smaller than the width of a human hair. Such tiny dimensions require machining with an accuracy that often reaches the nanometer scale. If the components produced by CNC machines don’t meet the exact specifications, even by the smallest margin, the functionality of the chip could be compromised. For example, minor errors in the alignment of a chip’s microscopic circuit can result in performance degradation or complete failure, making precision a matter of utmost importance.
The Complexity of Modern Semiconductor Devices
Modern semiconductor devices are becoming increasingly complex, with new designs and components emerging that demand even higher precision. Features such as 3D stacking and multi-layered designs are pushing the boundaries of what traditional machining methods can achieve. To maintain functionality, each layer of these devices must be perfectly aligned and manufactured to extremely tight tolerances, which further underscores the critical importance of precision in CNC machining.
4. Key Factors That Affect CNC Machining Accuracy in Semiconductor Production
Machine Calibration
One of the most critical factors affecting CNC machining accuracy is machine calibration. Regular calibration ensures that the CNC machine operates within the specified tolerances and performs tasks with the utmost precision. Over time, CNC machines can experience wear and tear, which can affect their accuracy. For instance, small shifts in the machine’s alignment or positioning can lead to deviations in machining results. This is why periodic recalibration is essential to maintain the high standards required in semiconductor production.
Material Properties
The material being machined can also impact the accuracy of the process. Different materials react differently under cutting forces, temperature fluctuations, and vibrations. For example, materials like silicon are brittle and can crack if the machining process isn’t carefully controlled. Conversely, harder materials such as sapphire or gallium arsenide require more advanced machining techniques and specialized tools. Understanding the material properties and selecting the right tooling and techniques for each material is crucial to achieving the desired accuracy in semiconductor CNC machining.
Tool Wear and Maintenance
CNC tools naturally degrade over time due to the constant cutting and abrasion they undergo during machining. As tools wear down, their cutting performance can degrade, which can lead to inconsistencies in machining results. Regular maintenance, tool replacement, and sharpening are essential for ensuring that CNC machines continue to operate with the required precision. Even a slight deterioration in tool sharpness can result in changes to the dimensional accuracy of semiconductor components, which can lead to defects in the final product.
Environmental Factors
Environmental conditions, such as temperature, humidity, and vibration, can have a significant effect on machining accuracy. Temperature fluctuations can cause both the machine and the materials to expand or contract, which could lead to dimensional errors. Humidity can affect certain materials, causing them to swell or contract, further compounding the challenge. Additionally, vibrations from nearby machines or external sources can disrupt the precision of CNC machining. That’s why maintaining a controlled environment is key to achieving the level of accuracy needed in semiconductor production.
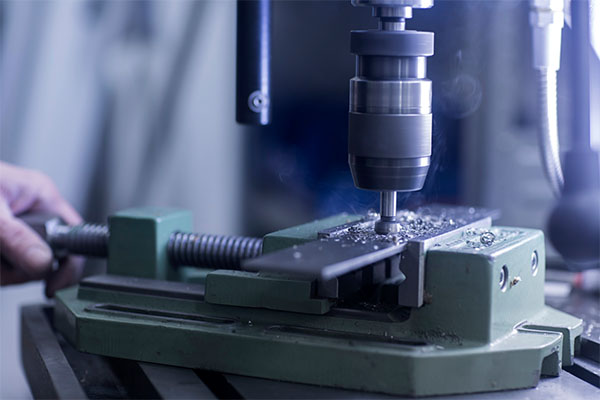
5. Advanced Features in Semiconductor CNC Machines for Enhanced Accuracy
High-Speed Spindles
One of the critical innovations in semiconductor CNC machining is the development of high-speed spindles. These spindles allow for faster cutting speeds, reducing cycle times and improving overall productivity. However, high-speed spindles also come with a trade-off: they generate more heat and require more precise control to maintain accuracy. High-speed spindles can help produce finer, more detailed features, which is especially important in the manufacture of semiconductor components, where accuracy at the micron level is required.
Precision Feedback Systems
Incorporating precision feedback systems into CNC machines has greatly improved machining accuracy. These systems monitor the position and movement of the machine’s tool, providing real-time data that can be used to make adjustments during the machining process. By using closed-loop feedback, CNC machines can compensate for minor deviations and ensure that the final product meets the required tolerances. This technology is particularly beneficial in the semiconductor industry, where even small errors can have a significant impact on the functionality of the final product.
Laser Interferometry for Measurement
Laser interferometry is a non-contact measurement technique that uses laser beams to measure the position of objects with extraordinary accuracy. This technique is increasingly being used in semiconductor CNC machining to ensure that machining operations remain within tight tolerances. Laser interferometry helps to measure the exact position of the cutting tool and workpiece, providing highly accurate data that can be used for real-time adjustments during machining. By employing laser interferometry, manufacturers can ensure that the machining process remains within nanometer-level accuracy.
6. Comparing Traditional vs. Modern CNC Machines for Semiconductor Applications
Traditional CNC Machines
Traditional CNC machines, which typically feature basic control systems and fewer axes of movement, have been used for decades in various manufacturing industries, including semiconductor production. While they offer reliable machining capabilities, they are limited in terms of flexibility and precision. These machines are typically suited for less complex machining tasks and larger components but are not as well-equipped to handle the high precision required for modern semiconductor production.
Modern CNC Machines for Semiconductor Manufacturing
Modern CNC machines, particularly those equipped with multiple axes of movement and advanced control systems, have transformed semiconductor manufacturing. These machines are capable of producing intricate and highly detailed components with unmatched precision. The use of advanced technologies like high-speed spindles, automated tool changers, and precision feedback systems makes modern CNC machines ideal for handling the demanding tolerances of semiconductor production. These machines can also integrate with advanced software systems that optimize machining paths, further enhancing their accuracy.
Which One is Best for Semiconductor Applications?
When it comes to semiconductor manufacturing, modern CNC machines are the clear winner. Their ability to handle complex geometries, achieve ultra-precise tolerances, and accommodate advanced materials makes them the preferred choice for semiconductor production. While traditional CNC machines can still be useful for certain tasks, modern machines offer the flexibility, speed, and accuracy necessary for the highly detailed and precise work required in the semiconductor industry.
7. CNC Machining for Critical Semiconductor Components
What Are the Key Components in Semiconductor Manufacturing?
Semiconductors are made up of various components that each require highly accurate machining. Key components include semiconductor wafers, photomasks, die, heat sinks, and packaging elements. Each of these parts requires a distinct set of machining operations to achieve the precise dimensions and tolerances needed for successful operation in electronic devices.
How CNC Machining Plays a Role in Producing These Components
CNC machining is used at almost every stage of semiconductor manufacturing, from the creation of photomasks to the final packaging of microchips. Photomasks, for example, are produced using CNC machines that carve detailed circuit patterns onto substrates with extreme precision. Similarly, CNC machines are used to create intricate heat sinks, which help dissipate heat from microchips. Every part of the semiconductor must meet the strictest standards for dimensional accuracy, making CNC machining a vital part of the process.
Examples of CNC-Machined Semiconductor Components
Some of the most common semiconductor components produced using CNC machining include wafer carriers, photomasks, and die carriers. These parts require precise machining to ensure that they fit seamlessly into the overall semiconductor production process. For example, a photomask must have circuit patterns etched with incredible detail and accuracy to ensure the integrity of the final product. Similarly, heat sinks must be designed with precise geometries to effectively dissipate heat without interfering with the semiconductor’s performance.
8. The Impact of Material Selection on CNC Machining Accuracy
Choosing the Right Material for Semiconductor Components
The selection of materials used in semiconductor manufacturing has a direct impact on the accuracy of CNC machining. Materials such as silicon, gallium arsenide, and sapphire are commonly used in semiconductor applications, each with its own set of machining challenges. For instance, materials like silicon are prone to brittleness, which can make machining difficult and require careful handling to prevent breakage. Understanding the material properties is essential for selecting the appropriate machining techniques and tooling to achieve high accuracy.
Challenges with Harder Materials
Harder materials, such as sapphire, present unique challenges in CNC machining. These materials are extremely durable and require specialized cutting tools and techniques. When machining these materials, it is essential to use tools made from harder substances, such as diamond or carbide, to ensure a clean cut. Additionally, the higher hardness of these materials means that they are more prone to tool wear, which can affect the accuracy of the machining process if not properly maintained.
Material Behavior Under Stress
Another important consideration in material selection is how the material will behave under stress during machining. Some materials, such as ceramics, can experience significant expansion or contraction when subjected to temperature changes. This can affect their dimensional accuracy during the machining process. To achieve the highest precision, CNC machinists must carefully monitor and control the temperature during machining to prevent any distortions in the final part.
9. Automation and the Future of Semiconductor CNC Machining
The Role of Automation in Enhancing Precision
Automation has become an integral part of CNC machining, especially in semiconductor manufacturing. Automated systems, such as robotic arms and automated loading/unloading systems, help to increase efficiency and precision by reducing human error. These systems can perform repetitive tasks with extreme accuracy, ensuring that parts are produced consistently within the required tolerances.
Smart Manufacturing: Combining CNC with IoT
The integration of CNC machines with Internet of Things (IoT) devices is transforming the semiconductor manufacturing process. IoT-enabled machines can collect real-time data, monitor machine performance, and even predict maintenance needs. This data-driven approach helps manufacturers to avoid downtime, maintain high levels of accuracy, and optimize production efficiency.
How Automation Helps in Reducing Human Error
Human error can be a significant source of inconsistency in traditional manufacturing processes. However, with the advent of automation, human intervention is minimized, allowing for a higher degree of consistency and reliability. Automated systems can perform complex tasks without introducing errors, leading to better accuracy and fewer defects in semiconductor components.
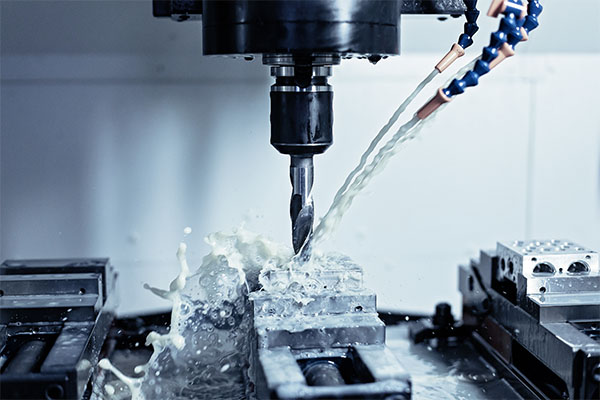
10. Quality Control and Testing in Semiconductor CNC Machining
Inspection Techniques for CNC Machined Parts
The accuracy of CNC-machined semiconductor components must be verified through stringent inspection techniques. Tools like Coordinate Measuring Machines (CMM), Scanning Electron Microscopes (SEM), and X-ray inspection are used to assess the dimensional accuracy and surface finish of components. These technologies allow manufacturers to detect even the smallest deviations from specifications and make necessary adjustments before production continues.
Why Continuous Quality Control is Important
Quality control in semiconductor CNC machining is crucial because even minor flaws can result in major functional issues. Continuous monitoring and testing during the machining process ensure that any errors are caught early, preventing costly rework and ensuring that components meet the high standards required in semiconductor production.
Ensuring Consistency in Mass Production
In high-volume semiconductor production, maintaining accuracy and consistency is paramount. Quality control systems must be in place to ensure that each component meets the required standards. Advanced inspection techniques, along with automated feedback systems, ensure that each part is produced with the same level of precision, even in large batches. This consistency is vital for the reliability and performance of semiconductor products.
11. Common Challenges in Achieving High Accuracy in Semiconductor CNC Machining
Dealing with Small Tolerances
One of the biggest challenges in semiconductor CNC machining is working with extremely small tolerances. For example, in some cases, the dimensions of components need to be accurate within a fraction of a micrometer. Achieving such precision requires advanced CNC machines, specialized tools, and cutting-edge technology. Even minor fluctuations in any part of the process can lead to significant errors.
Thermal Expansion and Its Effects
Thermal expansion is a major factor that can impact the accuracy of CNC machining. As materials heat up during the cutting process, they expand, which can cause dimensional changes. Similarly, the machine itself can experience thermal expansion, leading to misalignments and inaccuracies. To combat this, temperature-controlled environments are often used, and specialized materials and tools are employed to reduce the effects of heat.
Maintaining Accuracy in Multi-Axis Machining
Multi-axis machining, which involves moving the workpiece and cutting tool along multiple axes simultaneously, is often used for complex semiconductor components. However, this method introduces challenges in maintaining accuracy due to the increased number of variables involved. To achieve the desired precision, CNC machines must be carefully calibrated and maintained, and real-time monitoring systems must be in place to detect and correct deviations.
12. How Semiconductor CNC Machining Contributes to Overall Industry Advancements
Enhancing Semiconductor Performance
The accuracy achieved in semiconductor CNC machining directly impacts the performance of the devices produced. Components made with high precision contribute to the overall functionality, speed, and energy efficiency of semiconductor devices. As technology advances, CNC machining continues to play a key role in enabling more powerful and reliable semiconductor products.
Supporting Innovations in Other Industries
Semiconductors are at the heart of numerous industries, from electronics to automotive and healthcare. By improving the accuracy of semiconductor production, CNC machining helps to drive innovations in these fields. For example, more efficient microchips can improve the performance of consumer electronics, while better sensors can revolutionize medical devices and autonomous vehicles.
How Semiconductor Machining is Moving Towards the Future
As semiconductor devices continue to shrink in size and increase in complexity, the demands on CNC machining technology will grow. The future of semiconductor machining will likely involve the use of even more advanced technologies, such as 3D printing and nanoscale machining, to meet the growing need for miniaturized and high-performance components.
13. The Role of Research and Development in Improving CNC Machining for Semiconductor Production
Investing in R\&D for New Materials and Tools
To stay ahead in the competitive semiconductor market, companies are investing heavily in research and development (R\&D). New materials and machining tools are constantly being developed to improve machining accuracy and efficiency. For example, researchers are working on creating new cutting tools that can handle harder materials and withstand the high heat generated during machining.
Collaboration Between Manufacturers and CNC Machine Developers
Collaborations between semiconductor manufacturers and CNC machine developers are leading to breakthroughs in machine technology. By working together, these two groups can create machines that are better suited to the unique challenges of semiconductor manufacturing. Innovations like AI-powered CNC systems and machine learning algorithms are poised to further enhance the precision and efficiency of semiconductor CNC machining.
Emerging Trends and Future Opportunities in CNC Machining
Looking forward, emerging trends in CNC machining include the use of artificial intelligence (AI) and machine learning to optimize machining processes. These technologies will allow for more adaptive machining, where the machine can automatically adjust its parameters based on real-time data. Additionally, as the demand for smaller and more complex components increases, the need for advanced machining methods, such as atomic-scale machining, may become more prevalent.
14. Cost Considerations in High-Precision Semiconductor CNC Machining
Cost vs. Accuracy: Finding the Balance
Achieving high accuracy in CNC machining often comes with significant costs. High-precision machines, specialized tools, and advanced technologies are required to meet the stringent tolerances of semiconductor manufacturing. However, companies must balance the cost of these technologies with the need for accuracy. In some cases, manufacturers may need to invest in more expensive equipment or tooling to achieve the desired precision, but this can pay off in the long run with improved product quality and performance.
Material Costs
The cost of materials used in semiconductor CNC machining can vary widely depending on the type of material and its availability. For example, rare materials like sapphire and gallium arsenide can be much more expensive than standard silicon. Manufacturers need to carefully manage material costs while maintaining the required level of quality and precision.
Cost Efficiency in High-Volume Manufacturing
While the initial investment in high-precision CNC machines may be costly, these machines can provide cost savings in high-volume manufacturing. Automated systems and advanced machine technologies can increase throughput, reduce human error, and minimize waste. This leads to greater efficiency, making high-precision machining more cost-effective in the long term.
15. Conclusion: The Future of Semiconductor CNC Machining and Its Impact on the Industry
Summary of Key Insights
Semiconductor CNC machining is critical to producing components with the accuracy required for modern electronics. Precision at the micrometer and nanometer levels is essential for creating devices that are smaller, faster, and more efficient. Advances in CNC technology, automation, and material science are continually redefining what is possible in semiconductor manufacturing.
The Ongoing Importance of CNC Machining in Semiconductor Production
As the semiconductor industry continues to grow and evolve, CNC machining will remain a cornerstone of production. With ever-increasing demand for smaller and more complex devices, the need for highly precise manufacturing processes will only continue to rise.
Call to Action
For businesses in the semiconductor industry, staying at the forefront of CNC machining technology is essential for maintaining competitive advantage. Investing in advanced CNC equipment and embracing new technologies will help drive innovation and improve product quality.
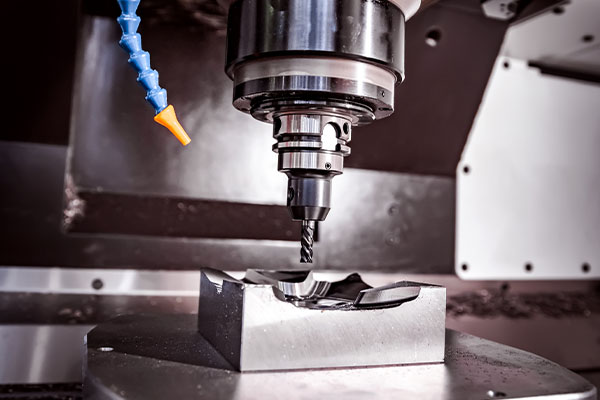
Раздел часто задаваемых вопросов
What is CNC machining, and why is it important in semiconductor manufacturing?
CNC machining refers to the process where computers control the movements of machines to cut and shape materials with high precision. In semiconductor manufacturing, CNC machining is vital because it ensures that components such as wafers, photomasks, and die carriers are produced with extremely tight tolerances. These parts must fit into complex semiconductor devices where even slight errors can cause performance failures.
How accurate is semiconductor CNC machining?
Semiconductor CNC machining must achieve an extraordinary level of accuracy. Many processes in semiconductor manufacturing require tolerances as tight as a few micrometers or even nanometers. The accuracy depends on various factors, such as machine calibration, material properties, tool sharpness, and environmental conditions. Advances in CNC technology, like high-speed spindles and laser interferometry, have significantly improved the precision of machining processes.
What are the main factors that impact CNC machining accuracy?
Several factors affect the accuracy of CNC machining in semiconductor production. These include the calibration of CNC machines, the material properties (such as hardness or brittleness), the maintenance and wear of cutting tools, and environmental conditions like temperature and humidity. Any fluctuations in these factors can lead to inaccuracies in the machining process, which is why constant monitoring and precision adjustments are necessary.
Can CNC machines be automated for semiconductor manufacturing?
Yes, automation plays a critical role in semiconductor CNC machining. Automated systems like robotic arms, tool changers, and IoT-based machines are increasingly used to reduce human error and improve precision. Automation can enhance the consistency of manufacturing processes and help achieve high volumes of semiconductor components without compromising on quality or accuracy.
What are the future trends in semiconductor CNC machining?
Future trends in semiconductor CNC machining include the integration of artificial intelligence (AI), machine learning, and even quantum computing to enhance precision and adaptability. These innovations could allow CNC machines to automatically adjust settings based on real-time data, further reducing errors and optimizing machining processes. Additionally, the growth of 3D printing and nanoscale machining techniques may revolutionize how semiconductor components are produced in the future.
Why are some materials harder to machine accurately in semiconductor production?
Certain materials used in semiconductor production, such as sapphire and gallium arsenide, are much harder than typical metals, which presents unique challenges for CNC machining. Harder materials require specialized cutting tools, such as diamond or carbide, and more careful management of machine settings to prevent tool wear and achieve high precision. Additionally, these materials can have different thermal and mechanical properties, making them more difficult to machine accurately under standard conditions.
How do CNC machines help in producing components for other industries beyond semiconductors?
CNC machining is used in a variety of industries beyond semiconductor manufacturing. For example, in the automotive industry, CNC machines are used to create parts like engine blocks and transmission components. In aerospace, they are used to produce lightweight yet durable components for airplanes and spacecraft. The precision offered by CNC machining ensures that the components meet exact specifications, contributing to the performance and safety of products across multiple industries.
What role does environmental control play in semiconductor CNC machining?
Environmental control is crucial in semiconductor CNC machining because temperature and humidity fluctuations can cause materials to expand or contract, which can impact the dimensional accuracy of components. Many semiconductor manufacturing facilities maintain cleanroom environments, where temperature and humidity are carefully regulated to minimize these effects. Additionally, vibration control is necessary to avoid disruptions during machining that could lead to inaccuracies in high-precision operations.
How does the integration of IoT improve CNC machining in semiconductor production?
The integration of IoT (Internet of Things) into CNC machines enables manufacturers to collect and analyze real-time data about machine performance, tool wear, and product quality. This data can be used to make immediate adjustments, ensuring that machining remains within the required tolerances. IoT also enables predictive maintenance, helping to avoid machine downtime by alerting operators to potential issues before they affect production.
What are the benefits of high-speed spindles in CNC machining for semiconductor manufacturing?
High-speed spindles in CNC machining are designed to cut materials at much higher speeds than traditional spindles, reducing machining time and increasing productivity. For semiconductor manufacturing, this is particularly useful when working with materials that require fine details, as the high-speed spindles can create sharper and more precise cuts. However, they also generate more heat, so proper cooling and temperature control are essential to maintain accuracy.
How can tool wear affect the accuracy of CNC machining in semiconductor production?
Tool wear is a natural part of the CNC machining process, especially when working with hard materials. As tools become worn down, they lose their sharpness, leading to reduced cutting precision. This can cause dimensional errors in semiconductor components. Regular monitoring and maintenance of tools, including replacement and sharpening, are crucial to ensuring continued machining accuracy and consistency.
What makes modern CNC machines better suited for semiconductor applications compared to older models?
Modern CNC machines are equipped with advanced features such as multi-axis movement, high-speed spindles, real-time feedback systems, and enhanced precision measurement tools. These advancements allow for more intricate and precise operations, making them ideal for semiconductor applications where tight tolerances are required. Older machines, while functional, lack the flexibility and precision needed for the complex geometries found in modern semiconductor components.
Why is maintaining a clean environment essential for semiconductor CNC machining?
Maintaining a clean environment is essential for semiconductor CNC machining because even small particles or contaminants can cause defects in highly sensitive components. Semiconductor devices have extremely small features, and any dust or particles can disrupt the machining process or interfere with the device’s functionality. Cleanrooms and air filtration systems are commonly used to ensure that machining environments remain free from contaminants that could compromise production quality.