Введение
Обработка крупных деталей представляет уникальные проблемы и требует специализированных методов и оборудования. Поскольку отрасли продолжают требовать высокоточные и высококачественные крупные компоненты, производители должны адаптироваться для удовлетворения этих меняющихся потребностей. В этой статье мы рассмотрим проблемы, возникающие при обработке крупных деталей, инструменты и методы, используемые для их преодоления, а также передовые методы обеспечения эффективности и качества. Независимо от того, занимаетесь ли вы производством, обработкой или работаете с крупномасштабными проектами, понимание этих проблем и решений может дать значительные преимущества. Давайте углубимся и посмотрим, как правильный подход может иметь решающее значение.
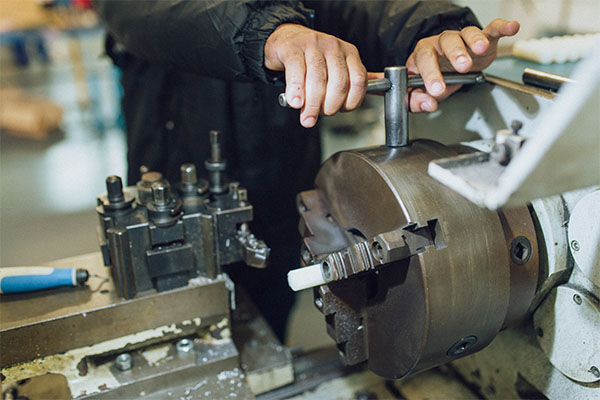
1. Каковы основные проблемы при обработке крупногабаритных деталей?
Когда дело доходит до обработки крупных деталей, проблемы многогранны. Первое серьезное препятствие — это огромные размеры и вес компонентов. Более крупные детали часто требуют станков с большими возможностями, а управление возросшими силами во время обработки может привести к осложнениям.
Но вот в чем загвоздка: достижение высокой точности в крупных деталях — нелегкая задача. При обработке более крупных деталей даже незначительные отклонения в измерениях могут привести к значительным ошибкам. Одной из ключевых проблем при обработке крупных деталей является обеспечение того, чтобы вся деталь оставалась выровненной в ходе процесса. Смещение позиционирования может привести к дорогостоящим ошибкам, поэтому правильное крепление и зажим имеют решающее значение.
Еще одной проблемой является износ инструмента. Более крупные детали требуют более длительного времени обработки, что приводит к большему износу инструмента. В таких ситуациях долговечность режущих инструментов становится еще важнее. Кроме того, процесс требует управления повышенным тепловым расширением и тепловой деформацией из-за тепла, выделяемого в процессе резки.
Еще один момент: обработка и транспортировка крупных деталей может быть столь же сложной, как и сама обработка. Перемещение крупных деталей между различными станками, этапами процесса или даже на станции окончательного контроля может представлять логистические проблемы, которые могут повлиять на рабочий процесс и сроки.
Чтобы преодолеть эти проблемы, производители часто полагаются на высокоточные станки с ЧПУ и опытных операторов. Однако тщательное планирование и точность имеют важное значение для обеспечения правильной обработки крупных деталей.
Таблица 1: Основные проблемы при обработке крупных деталей
Испытание | Влияние | Решение |
---|---|---|
Размер и вес | Увеличение усилий при обработке | Используйте мощные машины и приспособления |
Достижение точности | Потенциальная возможность несоосности и ошибок | Используйте передовые системы ЧПУ и измерения |
Износ инструмента | Сокращение срока службы инструмента из-за более длительной обработки | Выбирайте долговечные инструменты и управляйте их износом |
Тепловое расширение и деформация | Влияние на точность обработки | Внедрение эффективных методов охлаждения |
Обработка и транспортировка | Риск задержек или повреждений во время переезда | Использование специализированного подъемного оборудования и оптимизация рабочего процесса |
2. Как выбрать подходящие инструменты для обработки крупногабаритных деталей?
Выбор правильных инструментов для обработки крупных деталей имеет решающее значение для эффективности и точности. Речь идет не просто о выборе любого инструмента; речь идет о выборе правильного типа режущего инструмента для материала и поставленной задачи.
Какова реальная история? Ключ к успеху заключается в понимании уникальных требований обработки крупных деталей. Процесс выбора инструмента начинается с материала, с которым вы работаете. Более твердые материалы, такие как титан или инструментальная сталь, требуют более прочных инструментов с более высокой режущей способностью. С другой стороны, более мягкие материалы, такие как алюминий, могут обеспечить более высокую скорость резки и меньший износ инструментов.
Прочность инструмента является критическим фактором, особенно при работе с тяжелыми, большими заготовками. Инструменты должны быть достаточно прочными, чтобы выдерживать высокие силы резания, возникающие при обработке больших деталей. Наряду с прочностью, геометрия режущего инструмента также играет важную роль. Инструмент с неправильной геометрией может привести к чрезмерному износу, повышенным температурам и плохой отделке.
Готовы к лучшему? Выбор правильной скорости резания и подачи не менее важен. При обработке крупных деталей важно регулировать скорость резания и подачи, чтобы сбалансировать производительность со сроком службы инструмента. Использование слишком высокой скорости может привести к чрезмерному накоплению тепла, а слишком низкая скорость может привести к неэффективности и увеличению времени обработки.
Другим соображением является использование многоинструментальных систем, которые могут повысить производительность, позволяя операторам быстро переключаться между различными инструментами для различных операций. Кроме того, важно убедиться, что инструмент может соответствовать размерам заготовки, поскольку некоторые инструменты могут не достигать всех областей крупных деталей.
Таблица 2: Факторы, влияющие на выбор инструмента для обработки крупногабаритных деталей
Фактор | Влияние | Рассмотрение |
---|---|---|
Тип материала | Влияет на прочность инструмента и мощность резания | Выберите подходящий материал инструмента |
Прочность инструмента | Влияет на долговечность и производительность | Выбирайте надежные инструменты для интенсивного использования |
Геометрия инструмента | Влияет на эффективность резания и срок службы инструмента | Оптимизировать геометрию для конкретных задач |
Скорости резания и подачи | Влияет на время обработки и срок службы инструмента | Баланс скорости резания и долговечности инструмента |
Совместимость инструментов | Определяет способность достигать всех частей области | Используйте регулируемые или многофункциональные системы инструментов. |
3. Каковы наилучшие методы настройки крупных деталей на станках с ЧПУ?
Настройка крупных деталей на станках с ЧПУ требует тщательного планирования и выполнения. Процесс начинается с закрепления заготовки на станине станка. Но вот в чем загвоздка: если заготовка не закреплена должным образом, даже самые незначительные движения во время обработки могут вызвать серьезные отклонения, что приведет к дефектам или браку. Правильный зажим и фиксация абсолютно необходимы при обработке крупных деталей.
Первым шагом в процессе настройки является определение подходящей системы зажима. Для крупных деталей производители часто полагаются на мощные системы зажима, которые могут обеспечить равномерное давление по всей заготовке. Эти системы помогают удерживать положение заготовки во время обработки, предотвращая любые перемещения, которые могут повлиять на точность.
После того, как деталь надежно закреплена, следующей задачей является выравнивание. Обеспечение идеального выравнивания заготовки с режущими инструментами станка имеет решающее значение для достижения точных результатов. Любое несоосность может привести к неточностям размеров, которые могут усугубляться по мере продвижения процесса обработки.
В чем же здесь реальная история? Время настройки для крупных деталей часто может быть довольно продолжительным. Но, уделив время тому, чтобы убедиться, что все идеально выровнено и надежно с самого начала, вы в конечном итоге сэкономите время и деньги, предотвратив ошибки во время обработки. Кроме того, важно откалибровать станок с ЧПУ перед началом любых операций по обработке, чтобы убедиться, что он работает с оптимальной производительностью.
Еще одна передовая практика — регулярная проверка износа как станка, так и инструмента в ходе всего процесса обработки. Регулярный осмотр инструментов и деталей гарантирует, что процесс обработки останется эффективным и что любые проблемы будут выявлены до того, как они станут серьезными.
Таблица 3: Лучшие практики настройки ЧПУ для крупных деталей
Упражняться | Выгода | Советы по передовой практике |
---|---|---|
Надежный зажим | Предотвращает перемещение и обеспечивает точность | Используйте прочные, равномерно распределенные системы зажимов. |
Правильное выравнивание | Обеспечивает точность обработки | Используйте инструменты и методы точного выравнивания |
Калибровка станка с ЧПУ | Обеспечивает работу машины при оптимальных настройках | Регулярно проводите калибровку для достижения наилучших результатов |
Проверка инструментов и деталей | Предотвращает ошибки и обеспечивает качество | Проводите регулярные проверки инструментов и деталей. |
4. Как добиться точности при обработке крупных деталей?
Достижение точности в обработка крупных деталей является одной из самых серьезных проблем, с которыми сталкиваются производители. Чем больше деталь, тем сложнее поддерживать точные измерения и допуски на протяжении всего процесса обработки.
Готовы к лучшему? Один из самых эффективных способов обеспечения точности — использование современных станков с ЧПУ, включающих высокоточные измерительные системы. Эти системы непрерывно отслеживают размеры детали во время обработки, предоставляя оператору обратную связь в реальном времени. Если обнаруживаются какие-либо отклонения от требуемых размеров, система может вносить корректировки на лету, гарантируя, что конечный продукт соответствует требуемым спецификациям.
Другим методом достижения точности в крупных деталях является использование высококачественного инструмента. Чем острее инструмент, тем точнее резы. Со временем инструменты изнашиваются, что может привести к неточностям в готовой детали. Использование инструментов с более длительным сроком службы и регулярная проверка состояния инструментов имеют важное значение для поддержания качества и точности крупных деталей.
Кроме того, контроль температуры играет ключевую роль в поддержании точности. При обработке крупных деталей процесс генерирует значительное количество тепла, что может привести к тепловой деформации. Это особенно проблематично для крупных деталей, поскольку даже небольшое количество тепловой деформации может вызвать значительные изменения размеров детали. Эффективные системы охлаждения являются обязательными для поддержания стабильной температуры заготовки и снижения риска теплового расширения.
Другим фактором, влияющим на точность, является правильное программирование. Программы ЧПУ для крупных деталей должны быть тщательно протестированы и оптимизированы, чтобы гарантировать точность всех траекторий резки. Даже небольшая ошибка в программе может привести к серьезным дефектам в конечном продукте.
Таблица 4: Методы достижения точности при обработке крупных деталей
Техника | Влияние | Рассмотрение |
---|---|---|
Системы измерения с ЧПУ | Обеспечивает обратную связь в реальном времени для точности | Инвестируйте в высокоточные системы |
Высококачественная оснастка | Повышает точность и эффективность резки | Используйте прочные и острые инструменты для более длительного срока службы |
Контроль температуры | Предотвращает тепловую деформацию | Используйте эффективные системы охлаждения |
Оптимизированное программирование ЧПУ | Обеспечивает точные траектории резки | Тщательно тестируйте программы перед использованием |
5. Какие материалы обычно используются при обработке крупных деталей?
При обработке крупных деталей выбор материала играет решающую роль в определении как сложности, так и эффективности процесса. Не все материалы подходят для крупномасштабной обработки, и выбор правильного материала может обеспечить или помешать успеху проекта.
Какова реальная история? Наиболее часто используемые материалы для обработки крупных деталей включают различные металлы, такие как сталь, алюминий и титан. Сталь, будучи одним из наиболее широко используемых материалов в производстве, известна своей прочностью и долговечностью. Однако ее также может быть сложно обрабатывать, особенно в случае крупных деталей, из-за ее твердости и тенденции к выделению тепла во время обработки.
С другой стороны, алюминий гораздо легче поддается обработке и обычно используется в таких отраслях, как аэрокосмическая и автомобильная промышленность для крупных компонентов. Он легкий, что делает его идеальным для крупных деталей, требующих мобильности, но он не такой прочный, как сталь или титан. Тем не менее, его более низкая стоимость и простота обработки делают его популярным выбором для многих применений.
Титан, хотя и более дорогой, часто используется в приложениях, требующих высокого соотношения прочности к весу, например, в аэрокосмической промышленности. Однако обработка титана имеет свои собственные проблемы, включая более высокие силы резания и износ инструмента. Для успешной работы с титаном часто требуются специальные инструменты и методы резки.
Наконец, некоторые крупные детали могут потребовать использования композитных материалов или пластика, в зависимости от области применения. Эти материалы часто легче и дешевле, но они могут не обеспечивать такой же уровень прочности, как металлы.
Таблица 5: Распространенные материалы для обработки крупных деталей
Материал | Характеристики | Приложения |
---|---|---|
Сталь | Прочный, долговечный, более устойчив к механической обработке | Строительство, автомобилестроение |
Алюминий | Легкий, простой в обработке, экономичный | Аэрокосмическая, автомобильная |
Титан | Высокая прочность на единицу веса, дороговизна | Аэрокосмическая промышленность, медицинские приборы |
Композитные материалы и пластмассы | Легкий, менее долговечный | Потребительские товары, автомобилестроение |
Заключение
В заключение следует отметить, что обработка крупных деталей сопряжена с определенным набором проблем, но понимание этих препятствий и реализация правильных стратегий могут привести к успешным результатам. Ключ к преодолению этих проблем заключается в выборе правильных инструментов, управлении точностью, выборе соответствующих материалов и соблюдении передовых методов настройки и эксплуатации. Решая эти факторы, производители могут сократить количество ошибок, повысить эффективность и обеспечить высококачественные результаты в своих проектах по обработке крупных деталей. Правильный подход в сочетании с новейшими технологиями и методами может помочь преодолеть эти проблемы и улучшить операции по обработке в различных отраслях промышленности.
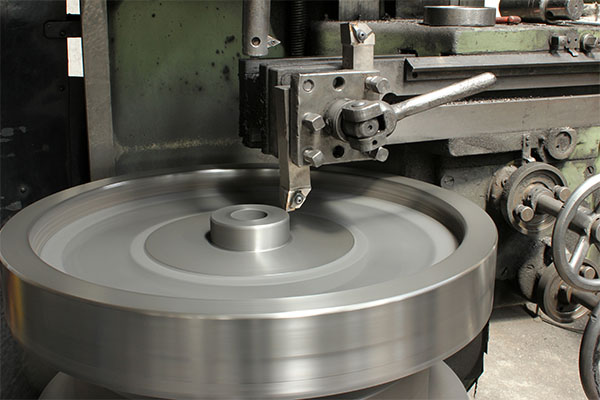
6. Как контролировать нагрев и минимизировать термическую деформацию?
Контроль тепла и минимизация термической деформации во время обработки крупных деталей являются решающим фактором в достижении точности и сохранении качества деталей. Процесс обработки крупных деталей генерирует значительное количество тепла из-за резания, трения и удаления материала. Если это тепло не контролировать должным образом, оно может привести к тепловому расширению или деформации, что повлияет на конечные размеры детали.
Какова реальная история? Самый эффективный способ контролировать тепло — это использовать правильные методы охлаждения. Охлаждающие жидкости используются для поглощения тепла, выделяемого во время обработки, и рассеивания его, предотвращая чрезмерное повышение температуры. Существует несколько типов охлаждающих жидкостей, таких как масла, растворы на водной основе и воздушное охлаждение, каждый из которых подходит для различных применений. Тип охлаждающей жидкости, которую вы выбираете, зависит от обрабатываемого материала, скорости резки и используемого станка.
Другим ключевым фактором контроля тепла является выбор правильных параметров резки. Слишком высокие скорости резки могут привести к чрезмерному выделению тепла, а слишком низкие скорости резки могут привести к неэффективному удалению материала. Найдя оптимальную скорость резки для материала и размера детали, производители могут снизить риск деформации, связанной с нагревом.
Но вот в чем загвоздка: выбор материала инструмента — еще один критический фактор. Некоторые инструменты рассчитаны на более высокие температуры, что снижает вероятность термической деформации во время обработки. Например, твердосплавные инструменты выдерживают более высокие температуры, чем быстрорежущая сталь, что делает их идеальными для высокотемпературной обработки.
Термическую деформацию также можно минимизировать с помощью управления станком. Современные станки с ЧПУ оснащены передовыми системами охлаждения и датчиками температуры, которые отслеживают температуру во время обработки и при необходимости регулируют ее для поддержания постоянной производительности. Некоторые станки даже оснащены функциями температурной компенсации, которые позволяют им вносить корректировки в процесс обработки в режиме реального времени, гарантируя минимизацию термических эффектов.
Таблица 6: Методы охлаждения для управления теплом при обработке крупных деталей
Метод охлаждения | Эффективность | Рассмотрение |
---|---|---|
Охлаждающие жидкости на масляной основе | Эффективен при высоких скоростях резания | Требует надлежащего управления утилизацией |
Охлаждающие жидкости на водной основе | Обычно используется для точной резки. | Может подвергнуться коррозии, если не обслуживать должным образом |
Воздушное охлаждение | Идеально подходит для легких резов и небольших деталей. | Менее эффективен для крупных деталей или высокоскоростной резки. |
Интегрированные системы охлаждения машин | Обеспечивает охлаждение в реальном времени во время работы | Обеспечивает постоянное управление температурой |
7. Каковы основные факторы, которые следует учитывать при обработке поверхностей крупногабаритных деталей?
Достижение желаемой отделки поверхности на крупных деталях является одним из важнейших аспектов обработки. Отделка поверхности имеет решающее значение как для функциональности, так и для эстетики детали. Она напрямую влияет на такие факторы, как трение, износостойкость и взаимодействие детали с другими компонентами в ее сборке.
Какова реальная история? Качество поверхности, которого вы достигаете, зависит от различных факторов, включая используемый режущий инструмент, процесс обработки и обрабатываемый материал. Например, при работе с более мягкими материалами, такими как алюминий, вы можете добиться более гладкой поверхности при более высоких скоростях резки, тогда как для более твердых материалов, таких как сталь, могут потребоваться более низкие скорости резки и более тонкие инструменты для достижения желаемой отделки.
Одним из наиболее эффективных способов контроля качества поверхности является выбор инструмента. Инструменты с острыми краями и точной геометрией могут помочь получить более гладкую поверхность за счет снижения вибраций и сил резания во время обработки. Кроме того, выбор правильного покрытия для инструментов, например, твердосплавного или керамического покрытия, может снизить трение и улучшить качество отделки.
Готовы к хорошей части? Другим ключевым фактором в достижении качественной отделки поверхности является контроль вибрации во время обработки. Крупные детали более восприимчивы к вибрации из-за своего размера и веса, и даже небольшие вибрации могут вызвать дефекты на поверхности. Чтобы минимизировать вибрацию, производители используют такие методы, как системы амортизации машины или специальные крепления для более эффективной фиксации детали.
Наконец, процессы постобработки, такие как шлифование, полировка или хонингование, могут дополнительно улучшить качество поверхности крупных деталей. Эти процессы отделки обычно используются для деталей, требующих сверхгладкой отделки, например, тех, которые используются в аэрокосмической или автомобильной промышленности.
Таблица 7: Методы обработки поверхности при обработке крупногабаритных деталей
Техника | Эффективность | Рассмотрение |
---|---|---|
Острый инструмент и геометрия | Снижает вибрацию и улучшает гладкость поверхности | Требуется точная заточка инструмента |
Покрытия инструментов (например, карбидные) | Уменьшает трение и износ | Выбор покрытия зависит от материала |
Системы амортизации машин | Предотвращает появление дефектов поверхности из-за вибрации | Требуется правильная настройка машины |
Процессы последующей обработки (шлифовка, хонингование) | Улучшает качество отделки для высокоточных применений | Требует много времени и дополнительных затрат |
8. Как размер заготовки влияет на процесс обработки?
Размер заготовки существенно влияет почти на каждый аспект процесса обработки, от типа используемого оборудования до времени, необходимого для выполнения работы. Более крупные детали требуют более совершенного оборудования, более длительного времени обработки и более осторожного обращения для поддержания точности.
Какова реальная история? Одной из первых вещей, которая меняется при обработке крупных деталей, является тип используемого оборудования. Стандартные станки с ЧПУ могут не справляться с более крупными деталями, поэтому производителям часто приходится вкладывать средства в специализированное оборудование, такое как портальные станки, большие вертикальные фрезы или горизонтально-расточные станки. Эти станки предназначены для обработки более крупных деталей и обеспечивают необходимую устойчивость для обработки возросших сил резания.
Другим фактором является время, необходимое для обработки. Более крупные детали обычно требуют больше времени для обработки из-за их размера и большего количества операций, необходимых для завершения детали. Более длительное время обработки увеличивает риск износа инструмента, что может повлиять на точность и качество. Кроме того, крупные детали требуют большего охлаждения и смазки для управления накоплением тепла в процессе обработки.
Но вот в чем загвоздка: обработка крупных деталей так же важна, как и сам процесс обработки. Крупные детали могут быть громоздкими и сложными для транспортировки между различными станками или этапами производства. Для обеспечения безопасного перемещения деталей без повреждения часто требуется специализированное подъемное оборудование и приспособления.
Наконец, размер детали также может влиять на точность обработки. Более крупные детали более восприимчивы к вибрациям, тепловому расширению и прогибам во время обработки, что может привести к неточностям. Важно использовать правильную настройку, инструмент и калибровку станка, чтобы гарантировать, что деталь соответствует требуемым спецификациям.
Таблица 8: Влияние размера заготовки на обработку
Фактор | Влияние | Рассмотрение |
---|---|---|
Размер оборудования | Определяет тип используемой машины | Требуются машины большой мощности |
Время обработки | Более длительное время обработки и износ инструмента | Увеличивает эксплуатационные расходы |
Обработка и транспортировка | Увеличение сложности перемещения крупных деталей | Используйте специализированное подъемное и погрузочно-разгрузочное оборудование |
Точность | Более крупные детали более восприимчивы к вибрациям и тепловым воздействиям | Реализовать контроль вибрации и точную настройку |
9. Каковы финансовые последствия обработки крупных деталей?
Обработка крупных деталей может быть значительно дороже обработки более мелких компонентов из-за различных факторов, включая стоимость материалов, инструментов, рабочей силы и машинного времени. Понимание последствий затрат имеет решающее значение для производителей, чтобы оптимизировать свои операции и максимизировать прибыльность.
Какова реальная история? Одним из основных факторов, влияющих на стоимость обработки крупных деталей, является стоимость материалов. Крупные детали требуют больше сырья, что увеличивает общую стоимость материалов. Кроме того, сложность обработки крупных деталей может привести к более высоким затратам на рабочую силу. Для настройки, контроля и эксплуатации машин, которые могут обрабатывать крупные детали, требуются квалифицированные рабочие, и эти знания в цене.
Расходы на инструмент также увеличиваются с размером детали. Более крупные детали требуют более прочных инструментов, которые могут выдерживать повышенные силы резания, что может быть дороже. Более длительное время обработки, связанное с крупными деталями, также увеличивает общую стоимость. Более длительное время обработки приводит к более высокому потреблению энергии, повышенному износу станков и большему потреблению охлаждающих жидкостей и смазочных материалов.
Готовы к лучшему? Один из способов снизить затраты на обработку крупных деталей — оптимизировать процесс обработки. Тщательно выбирая правильные инструменты, материалы и параметры обработки, производители могут сократить отходы, минимизировать износ инструментов и сократить время обработки. Автоматизация — еще одна потенциальная мера экономии. Использование роботов или автоматизированных систем для обработки крупных деталей может снизить затраты на рабочую силу и повысить эффективность.
Наконец, производители должны также учитывать потенциальный брак и переделку. Крупные детали дороже перерабатывать, а любая переделка, необходимая после обработки, может значительно увеличить стоимость конечного продукта. Поддержание строгого контроля качества на протяжении всего процесса может помочь снизить эти расходы.
Таблица 9: Факторы стоимости при обработке крупных деталей
Фактор | Влияние | Рассмотрение |
---|---|---|
Материальные затраты | Более высокий расход материала для крупных деталей | Требуется эффективное планирование материалов |
Расходы на рабочую силу | Для более крупных деталей требуется квалифицированная рабочая сила | Инвестируйте в обучение или автоматизацию |
Стоимость оснастки | Для более крупных деталей требуются более надежные инструменты | Выбирайте инструменты, которые обеспечивают наилучшую ценность |
Время обработки | Более длительное время обработки увеличивает затраты | Оптимизируйте параметры резки и время работы машины |
Лом и переделка | Увеличение затрат в случае утилизации или переделки деталей | Внедрите контроль качества, чтобы свести к минимуму ошибки |
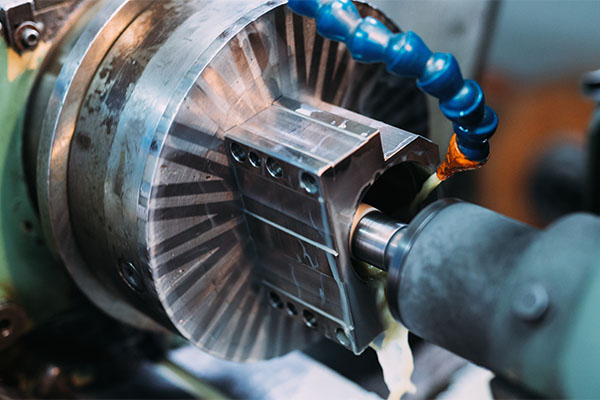
10. Каковы новейшие технологические достижения в обработке крупногабаритных деталей?
Достижения в области технологий продолжают преобразовывать область обработки крупных деталей. Новые инновации в области машиностроения, автоматизации и материаловедения позволяют производителям достигать большей точности, эффективности и экономичности при работе с крупными деталями.
Какова реальная история? Одним из самых значительных достижений последних лет является разработка многоосевых станков с ЧПУ. Эти станки позволяют выполнять более сложные разрезы и более высокую точность обработки крупных деталей. Используя несколько осей движения, производители могут обрабатывать более сложные элементы на крупных деталях без необходимости перепозиционирования заготовки.
Еще одним новшеством является более широкое использование робототехники и автоматизации в обработке крупных деталей. Роботы могут использоваться для таких задач, как перемещение материалов, смена инструмента и проверка, что снижает потребность в ручном труде и повышает эффективность. Автоматизация также помогает снизить риск человеческой ошибки, гарантируя, что процесс обработки останется последовательным и точным.
Готовы к лучшему? ИИ и машинное обучение начинают играть более значимую роль в обработке крупных деталей. Эти технологии можно использовать для оптимизации параметров обработки в режиме реального времени, гарантируя, что процесс резки останется эффективным и точным на протяжении всего процесса. ИИ также может прогнозировать износ инструмента, позволяя производителям планировать техническое обслуживание до возникновения проблем, сокращая время простоя и повышая общую эффективность.
Кроме того, разрабатываются новые материалы и покрытия для улучшения производительности режущих инструментов. Эти инновации помогают снизить трение, увеличить срок службы инструмента и улучшить общее качество обработанных деталей. Достижения в области аддитивного производства также открывают новые способы создания крупных деталей, предлагая потенциальную экономию средств и сокращение отходов материалов.
Таблица 10: Технологические достижения в обработке крупных деталей
Технологии | Влияние | Рассмотрение |
---|---|---|
Многоосевые станки с ЧПУ | Повышенная точность и сложность | Требуются расширенная настройка машины и обучение |
Робототехника и автоматизация | Сокращение ручного труда и повышение эффективности | Инвестируйте в роботизированные системы для перемещения материалов и смены инструментов |
ИИ и машинное обучение | Оптимизирует параметры резания и прогнозирует износ инструмента | Внедрение систем искусственного интеллекта для оптимизации процессов в реальном времени |
Новые материалы и покрытия | Уменьшает трение и увеличивает срок службы инструмента | Инвестируйте в высокопроизводительные покрытия |
Аддитивное производство | Снижает отходы материалов и затраты | Идеально подходит для прототипов или мелкосерийного производства |
11. Как вы обеспечиваете контроль качества при обработке крупных деталей?
Обеспечение контроля качества при обработке крупных деталей имеет важное значение для производства деталей, которые соответствуют требуемым спецификациям и функционируют должным образом в предполагаемых областях применения. Контроль качества заключается не только в проверке размеров; он подразумевает комплексный подход, включающий мониторинг всего процесса обработки.
Готовы к хорошей части? Одним из ключевых инструментов обеспечения качества является использование систем точных измерений. Эти системы могут быть интегрированы в станки с ЧПУ или использоваться как автономные инструменты для проверки размеров деталей в режиме реального времени. Это гарантирует, что любые отклонения от желаемых спецификаций будут обнаружены на ранних этапах процесса, что снижает вероятность дефектов в готовой детали.
Другим важным аспектом контроля качества является использование передовых методов проверки. Координатно-измерительные машины (КИМ) обычно используются для проверки крупных деталей, поскольку они могут измерять точные размеры детали с высокой точностью. КИМ используют зонды для касания различных точек на поверхности детали и создания 3D-модели детали, которую можно сравнить с исходным проектом.
Но вот в чем фишка: постоянный мониторинг процесса обработки необходим для поддержания качества. Сегодня многие станки с ЧПУ оснащены датчиками, которые отслеживают различные факторы, такие как температура, вибрация и силы резания во время обработки. Эти данные в реальном времени позволяют операторам вносить необходимые коррективы в процесс, чтобы гарантировать, что деталь остается в пределах допуска.
Наконец, регулярные аудиты и проверки жизненно важны. Даже при использовании лучшего оборудования все равно может произойти человеческая ошибка. Регулярные проверки инструментов, машин и конечной части необходимы для того, чтобы гарантировать, что все аспекты процесса соответствуют стандарту.
Таблица 11: Методы контроля качества при обработке крупных деталей
Метод | Влияние | Рассмотрение |
---|---|---|
Системы точного измерения | Обеспечивает точные размеры во время обработки | Интеграция со станками с ЧПУ для проверок в реальном времени |
Координатно-измерительные машины (КИМ) | Обеспечивает детальный осмотр крупных деталей | Требуются опытные операторы для интерпретации результатов |
Системы мониторинга в реальном времени | Отслеживает данные процесса и обеспечивает согласованность | Используйте датчики температуры, вибрации и силы резания |
Регулярные аудиты и проверки | Обеспечивает соблюдение стандартов качества | Запланируйте частые проверки на протяжении всего процесса |
12. Чем обработка крупногабаритных деталей отличается от стандартной обработки?
Обработка крупных деталей имеет несколько отличий по сравнению с обработкой более мелких, более стандартных компонентов. Хотя основные принципы обработки остаются теми же, уникальные проблемы и требования обработки крупных деталей отличают ее.
В чем же здесь реальная история? Одно из самых больших различий — это размер используемого оборудования. Крупные детали требуют гораздо более крупных станков с ЧПУ, которые могут справиться с размером, весом и сложностью компонентов. Эти станки должны выдерживать силы, возникающие в процессе обработки, что часто приводит к более сложным конструкциям станков и более высоким первоначальным инвестициям.
С точки зрения самого процесса обработки, крупные детали часто требуют большего количества шагов, более длительного времени обработки и более частой смены инструмента. Как упоминалось ранее, это связано с повышенным износом инструментов, необходимостью более длительного времени резки и проблемами, связанными с поддержанием выравнивания заготовки.
Другим важным отличием является требуемая точность. В то время как мелкие детали часто требуют высокой точности, крупные детали требуют еще большей заботы и внимания для поддержания необходимых допусков. Малейшее отклонение в большой детали может привести к серьезным проблемам, особенно в таких отраслях, как аэрокосмическая, автомобильная и оборонная.
Готовы к лучшему? Крупные детали также требуют специализированной обработки и логистики. Перемещение крупных деталей между обрабатывающими центрами или на контрольные станции требует специализированного оборудования и может привести к дополнительным рискам повреждения или задержек.
Таблица 12: Основные различия между обработкой крупных и стандартных деталей
Фактор | Обработка крупных деталей | Стандартная обработка деталей |
---|---|---|
Размер оборудования | Требуются большие станки с ЧПУ | Использует более стандартные машины меньшего размера |
Время обработки | Более длительное время обработки и больше операций | Более быстрое время обработки и меньше операций |
Точность | Требуется более высокая точность | Стандартной точности часто бывает достаточно |
Обработка и логистика | Требуется специализированное подъемное и транспортное оборудование | Легче в обращении и перемещении |
Износ инструмента | Больший износ инструмента из-за более длительного времени обработки | Меньший износ инструмента при обработке мелких деталей |
13. Какие типы станков с ЧПУ наиболее распространены для обработки крупногабаритных деталей?
При обработке крупных деталей производители должны использовать специализированные станки с ЧПУ, предназначенные для обработки более крупных заготовок. Эти станки обеспечивают необходимую точность и стабильность для обработки крупных компонентов и гарантируют, что они соответствуют требуемым спецификациям.
Какова реальная история? Наиболее распространенный тип станка с ЧПУ, используемый для обработки крупных деталей, — это портальная машина. Портальные станки спроектированы с большой жесткой конструкцией, которая может поддерживать крупные детали. Они идеально подходят для обработки крупных плоских компонентов, таких как автомобильные детали, фюзеляжи самолетов и компоненты тяжелой техники. Эти станки имеют несколько осей движения, что позволяет выполнять сложные операции резки крупных деталей.
Другим часто используемым станком с ЧПУ является горизонтально-расточной станок. Эти станки используются для обработки больших, тяжелых деталей, требующих точного сверления и расточки. Горизонтально-расточные станки могут обрабатывать детали, которые слишком велики для вертикальных станков, и их можно использовать для сверления больших отверстий, фрезерования плоских поверхностей и даже для выполнения полной обработки массивных деталей.
Готовы к самой приятной части? Вертикально-фрезерные станки также используются при обработке крупных деталей, особенно для крупных деталей, требующих точной обработки поверхности. Эти станки могут быть оснащены поворотными столами и другими приспособлениями для размещения более крупных заготовок.
Другие специализированные машины включают в себя токарные центры и токарные станки который может обрабатывать большие цилиндрические детали, а также 5-осевые станки с ЧПУ которые обеспечивают непревзойденную гибкость при обработке крупных и сложных деталей.
Таблица 13: Распространенные станки с ЧПУ для обработки крупных деталей
Тип машины | Возможности | Приложения |
---|---|---|
Портальные машины | Большая, жесткая конструкция для сложных разрезов | Аэрокосмическая промышленность, автомобилестроение, тяжелое машиностроение |
Горизонтально-расточные станки | Сверление и расточка крупных, тяжелых деталей | Автомобилестроение, строительство, энергетика |
Вертикально-фрезерные станки | Прецизионное фрезерование крупных деталей | Аэрокосмическая, автомобильная, оборонная |
Токарные центры и станки | Обработка крупных цилиндрических деталей | Нефть и газ, аэрокосмическая промышленность, автомобилестроение |
5-осевые станки с ЧПУ | Высокая гибкость для сложных деталей | Аэрокосмическая промышленность, медицинское оборудование, автомобилестроение |
14. Какие правила безопасности следует соблюдать при обработке крупногабаритных деталей?
Безопасность имеет первостепенное значение при обработке крупных деталей из-за размера и веса компонентов, а также сложности используемого оборудования. Существует несколько протоколов безопасности, которых производители должны придерживаться, чтобы защитить как рабочих, так и оборудование.
Какова реальная история? Первым шагом в обеспечении безопасности является правильная настройка станка. Перед началом любой операции по обработке операторы должны убедиться, что все компоненты надежно закреплены и что станок функционирует должным образом. Калибровка станка имеет решающее значение для обеспечения правильного выравнивания режущих инструментов и отсутствия риска неисправности станка.
Но вот в чем фишка: операторы также должны знать о физических рисках, связанных с обработкой крупных деталей. Эти детали тяжелые и с ними может быть трудно обращаться, для предотвращения травм требуется специальное подъемное оборудование и поддержка. Использование соответствующих подъемных инструментов и оборудования для перемещения крупных деталей может значительно снизить риск несчастных случаев.
Другим ключевым фактором безопасности являются средства индивидуальной защиты (СИЗ). Операторы должны носить необходимые СИЗ, включая защитные очки, средства защиты органов слуха и перчатки, чтобы защитить себя от летящего мусора, высокого уровня шума и острых краев. Кроме того, для поддержания безопасности во время операций по обработке необходимо убедиться, что рабочая зона чистая и свободна от препятствий.
Готовы к хорошей части? Регулярное обслуживание как машин, так и рабочей среды имеет жизненно важное значение для обеспечения постоянной безопасности. Машины следует регулярно обслуживать, чтобы избежать поломок, а рабочее место следует содержать в порядке, чтобы не допустить несчастных случаев.
Таблица 14: Основные протоколы безопасности при обработке крупных деталей
Протокол | Важность | Рассмотрение |
---|---|---|
Настройка и калибровка машины | Обеспечивает точность и безопасность машины | Всегда калибруйте перед использованием |
Подъемно-транспортное оборудование | Снижает риск получения травм от тяжелых деталей | Используйте соответствующие подъемные инструменты. |
Средства индивидуальной защиты (СИЗ) | Предотвращает травмы во время обработки | Обеспечьте, чтобы работники носили соответствующую одежду |
Чистое и организованное рабочее место | Минимизирует риски и несчастные случаи | Регулярно убирайте и организовывайте рабочее пространство |
Регулярное техническое обслуживание машины | Предотвращает поломки и аварии | Внедрите график планового технического обслуживания |
15. Как выбрать услугу по обработке крупногабаритных деталей?
Выбор правильного услуги по обработке для крупных деталей — это критическое решение, которое может повлиять на общий успех проекта. Правильный поставщик услуг должен иметь опыт, оборудование и экспертизу для точной и эффективной обработки крупных деталей.
Готовы к лучшему? Первый фактор, который следует учитывать при выборе услуг по обработке, — это их опыт работы с крупными деталями. Опытные производители будут обладать необходимыми знаниями для решения уникальных задач по обработке крупных компонентов. Они должны быть в состоянии продемонстрировать свои возможности с помощью прошлых проектов и отзывов клиентов.
Другим ключевым фактором является оборудование, которое использует поставщик услуг. Служба обработки должна иметь доступ к высококачественному специализированному оборудованию, способному обрабатывать крупные детали. Сюда входят станки с ЧПУ, фрезерные станки и другие инструменты, необходимые для достижения требуемой точности при обработке крупных деталей.
Какова реальная история? Общение так же важно. Служба обработки, которая отзывчива и готова тесно сотрудничать с вами, чтобы понять ваши потребности и требования проекта, может обеспечить более плавный процесс от начала до конца. Четкое общение также гарантирует, что любые проблемы или опасения будут решены быстро, что сведет к минимуму задержки и ошибки.
Наконец, следует также учитывать цены и сроки выполнения. Хотя стоимость не должна быть единственным решающим фактором, важно найти поставщика услуг, который предлагает конкурентоспособные цены без ущерба качеству. Убедитесь, что сроки выполнения разумны и что поставщик услуг может уложиться в ваши сроки.
Таблица 15: Ключевые факторы при выборе услуг по обработке крупных деталей
Фактор | Важность | Рассмотрение |
---|---|---|
Опыт работы с крупными деталями | Обеспечивает экспертные знания в области обработки крупных компонентов | Ищите проверенную репутацию |
Оборудование и возможности | Определяет качество и точность работы | Проверить спецификации оборудования |
Коммуникация | Обеспечивает бесперебойную реализацию проекта | Выберите поставщика с отзывчивой коммуникацией |
Цены и сроки поставки | Влияет на бюджет и сроки поставки | Сравните расценки и графики поставок |
Репутация и отзывы | Указывает на надежность и качество обслуживания | Проверьте рекомендации и отзывы клиентов |

Часто задаваемые вопросы
В1: Что такое обработка крупногабаритных деталей?
Обработка крупных деталей — это процесс обработки крупных компонентов или деталей, требующий специального оборудования и технологий для производства с высокой точностью.
В2: Как работает обработка на станках с ЧПУ крупных деталей?
Обработка с ЧПУ осуществляется с помощью станков с компьютерным управлением для точной резки, формовки и отделки крупных деталей в соответствии с конкретными проектами и размерами.
В3: Какие материалы лучше всего подходят для обработки крупногабаритных деталей?
Распространенными материалами для обработки крупных деталей являются такие металлы, как сталь, алюминий и титан, а также специальные неметаллы в зависимости от требований проекта.
В4: Какие проблемы возникают при обработке крупногабаритных деталей?
К числу проблем относятся необходимость обработки крупных деталей определенного размера и веса, достижение точности, управление выделением тепла и использование специализированных инструментов и оборудования.
В5: Как можно сократить затраты при обработке крупных деталей?
Чтобы сократить расходы, сосредоточьтесь на эффективном использовании инструмента, минимизируйте отходы материала, оптимизируйте время работы станка и тщательно планируйте операции обработки, чтобы сократить время простоя.