Введение
Plastic CNC machining is a precision manufacturing process used to cut, shape, and finish plastic materials. It offers numerous advantages for small batch production, making it ideal for businesses looking to create custom plastic parts with high accuracy and low volume requirements. In this article, we will explore the benefits, challenges, and practical considerations involved in plastic CNC machining for small batch manufacturing, focusing on how it compares to traditional methods and why it’s an excellent choice for many industries.
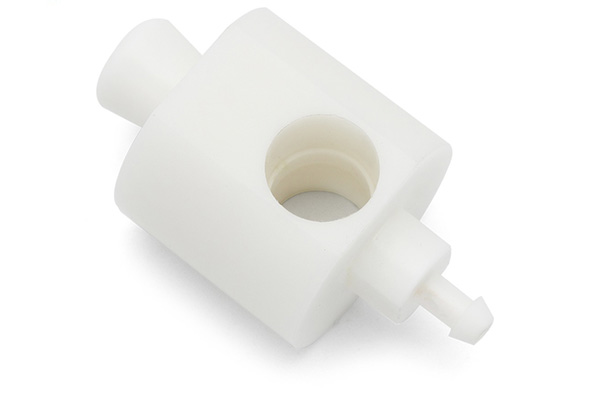
1. What is Plastic CNC Machining?
Plastic CNC machining is the process of using computer-controlled machines to precisely cut and shape plastic materials. It uses a variety of tools, such as mills, routers, and lathes, to create complex designs based on digital models. But here’s the kicker: the automation involved ensures that each part is produced with exacting standards, minimizing human error and maintaining consistency across batches.
The process starts with creating a 3D design or digital model of the part, which is then translated into machine instructions. A variety of plastics can be machined, including materials like acrylic, ABS, and polycarbonate, each selected based on the specific requirements of the job. The precision offered by CNC machines makes them ideal for producing intricate parts with tight tolerances. Furthermore, plastic CNC machining can be used for both prototyping and end-use production, allowing companies to streamline their manufacturing processes.
For businesses involved in industries like automotive, healthcare, and electronics, this method allows for quick, cost-effective production of custom plastic components without the need for expensive molds or tooling. As a result, plastic CNC machining is becoming an increasingly popular choice for small batch manufacturing, where traditional methods might not be as cost-effective.
2. Why Choose Plastic for CNC Machining?
When it comes to CNC machining, the choice of material plays a significant role in the end product’s performance, cost, and durability. So, what’s the real story behind why plastic is such a popular choice for CNC machining?
Plastic offers a combination of flexibility, lightweight properties, and ease of machining that makes it highly advantageous for a wide range of applications. Unlike metals, plastics are generally easier to cut, mold, and shape, which translates to lower production costs. Additionally, plastics like nylon, ABS, and PEEK offer excellent chemical resistance, making them ideal for components exposed to harsh environments.
Moreover, the low cost of raw plastic materials makes it more accessible for small batch production. Plastics are also less likely to warp under machining compared to metals, reducing material waste and ensuring higher-quality parts. On top of that, plastic components can be customized with ease, allowing for quick iteration of designs and fast turnarounds for clients.
Plastic CNC machining allows manufacturers to explore innovative designs and reduce time-to-market for products, which is crucial for businesses that need to remain competitive. Whether it’s for prototyping, short runs, or low-volume production, plastic CNC machining offers the ability to produce parts that meet exact specifications while maintaining cost-effectiveness.
3. What Are the Key Benefits of Plastic CNC Machining?
Plastic CNC machining presents a multitude of benefits, especially when it comes to small batch manufacturing. Ready for the good part? The advantages of this method are truly game-changing for industries relying on high-quality, low-volume production.
One of the key benefits is the ability to produce highly complex and detailed parts with exceptional accuracy. CNC machines are capable of working with tight tolerances, meaning that the final product is consistent and precise, with minimal human intervention. This is particularly important in fields such as medical device manufacturing, where even the smallest deviation can impact the functionality of a product.
Another major advantage is the speed at which parts can be produced. CNC machines operate continuously, cutting down production times significantly when compared to traditional methods like injection molding or handcrafting. For small batches, this means faster lead times and quicker delivery of custom parts.
Plastic CNC machining also offers excellent repeatability. Once the design is programmed into the machine, the same part can be produced consistently without variation, ensuring quality control is maintained throughout the production process. This is a huge benefit for businesses looking to scale operations without sacrificing quality.
4. What Types of Plastic Are Used in CNC Machining?
Not all plastics are created equal, and when it comes to CNC machining, selecting the right plastic material for the job is critical. So, what types of plastic are best suited for CNC machining?
Common plastics used in CNC machining include acrylic, polycarbonate, ABS, nylon, and PEEK, each with unique properties that make them ideal for different applications. Acrylic, for example, is a lightweight material with excellent clarity, making it ideal for applications where transparency is important, such as displays and signage. Polycarbonate is known for its high impact resistance and is often used for automotive or medical device components.
ABS, on the other hand, is a cost-effective plastic with good impact strength and is commonly used for industrial applications and consumer goods. Nylon is a durable material that resists wear and tear, making it suitable for components that require strength and flexibility. Finally, PEEK is a high-performance plastic that offers superior strength, heat resistance, and chemical resistance, ideal for demanding industries like aerospace and medical.
Each plastic type has its own machining characteristics and performance strengths, making it essential for manufacturers to choose the right one based on the specific needs of the part being produced. Factors such as strength, flexibility, environmental exposure, and ease of machining all play a role in the selection process.
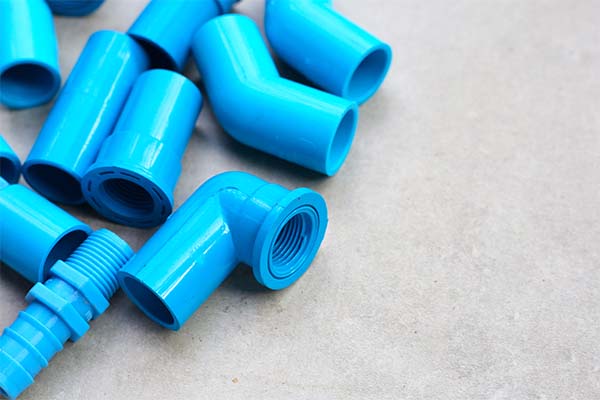
5. How Does Plastic CNC Machining Compare to Metal CNC Machining?
Plastic and metal CNC machining share many similarities, but there are key differences that businesses need to understand when choosing between the two. What’s the real difference?
First, plastics are generally much easier to machine compared to metals. This is because plastics are softer and require less force to cut, which reduces tool wear and extends the lifespan of CNC machines. Additionally, plastics can be machined at higher speeds, which leads to faster production times and lower overall costs.
However, metals are often preferred for applications that require high strength, heat resistance, or durability, such as in aerospace or automotive manufacturing. While plastic CNC machining offers good strength for many applications, metals are typically better suited for parts that need to withstand high stress or harsh environments.
Another difference is the material costs. Plastic materials tend to be less expensive than metals, making plastic CNC machining more cost-effective for small batch production. Plastic parts are also lighter, which is an important consideration for industries like aerospace, where weight reduction is critical.
So, when it comes down to it, plastic CNC machining is ideal for parts that require good strength, lightweight properties, and quick turnaround times without the need for high-performance metals. It offers a balance of cost-effectiveness and precision for many industries, but for applications requiring extreme durability, metal CNC machining might be the better option.
6. What Are the Common Applications of Plastic CNC Machining?
Plastic CNC machining is used across a variety of industries, from automotive to medical to consumer electronics. But what types of parts benefit most from plastic CNC machining?
For the automotive industry, plastic CNC machining is often used to create prototypes and custom components. It allows for the fast production of intricate parts like dashboard components, trim pieces, and electrical connectors, all with the necessary precision for safety and functionality.
In the medical industry, plastic CNC machining is used to produce sterile, high-precision parts for medical devices and instruments. The ability to work with plastics like PEEK, which offer chemical resistance and high strength, is particularly valuable in the production of components used in surgical tools or implants.
Consumer electronics manufacturers use plastic CNC machining to produce custom casings, connectors, and internal components. The speed and precision of the process ensure that these parts meet the strict tolerances required for modern electronics.
The flexibility of plastic CNC machining also makes it an excellent choice for prototyping. Designers can quickly iterate on different designs without the need for expensive tooling or molds. This rapid prototyping capability is invaluable for industries where innovation is constant and time-to-market is critical.
7. What Are the Challenges of CNC Machining Plastic?
While plastic CNC machining offers numerous benefits, there are challenges that need to be addressed to ensure optimal results. One of the main challenges is the risk of warping during machining. Plastics are susceptible to temperature changes, and if the part heats up unevenly, it can warp or deform. This can be avoided by using the right machining techniques and controlling the temperature during the process.
Another challenge is the potential for cracking, especially with brittle plastics like acrylic. It’s crucial to choose the right type of plastic based on the specific needs of the part being produced. Additionally, some plastics may cause excessive tool wear due to their abrasiveness, so using the appropriate tools and maintaining them regularly is essential to avoid costly downtime.
Finally, CNC machining plastic requires careful control of cutting speeds and feeds. If the speeds are too high, the plastic may melt, leading to poor-quality parts. Conversely, if the speeds are too slow, it can result in longer production times and unnecessary costs. By carefully adjusting machine settings and selecting the right cutting tools, these challenges can be minimized.
8. How Can You Improve the Efficiency of Plastic CNC Machining?
Improving the efficiency of plastic CNC machining is key to reducing production costs and improving turnaround times. So, how can you make your plastic CNC machining process more efficient?
First, optimizing cutting speeds and feeds is crucial for improving machining efficiency. By adjusting these parameters based on the type of plastic and the part design, manufacturers can reduce machining time and improve the surface finish of the parts.
Choosing the right cutting tools is also essential. Using high-quality tools designed specifically for plastic machining can help improve both the quality and speed of production. Carbide tools, for instance, tend to last longer and provide better results when machining plastics.
Machine calibration plays a significant role in ensuring efficiency. Regularly maintaining and calibrating CNC machines ensures that they operate at peak performance, reducing the likelihood of defects and increasing the overall speed of production.
Finally, automation can be leveraged to improve efficiency. Using automated CNC machines reduces human intervention, speeding up production and reducing the likelihood of mistakes.
9. What Are the Key Considerations When Machining Plastic Parts?
When machining plastic parts, several key considerations must be kept in mind to ensure optimal results. Let’s dive into what these are.
The first consideration is the material thickness and design. Thicker materials may require slower cutting speeds to prevent warping, while intricate designs may require more detailed tool paths. Adjusting the CNC machine settings to accommodate the design complexity and material thickness is essential for achieving the best results.
Tooling is another critical consideration. Plastic parts often require specialized cutting tools to achieve smooth finishes and prevent burrs. Ensuring that the correct tools are used for each material type is crucial for achieving high-quality parts.
Post-machining finishing is also essential for plastic parts. After machining, plastic parts may need additional processes like polishing or coating to improve their appearance or functionality. By planning for these additional steps, manufacturers can ensure that their plastic parts meet the desired specifications.
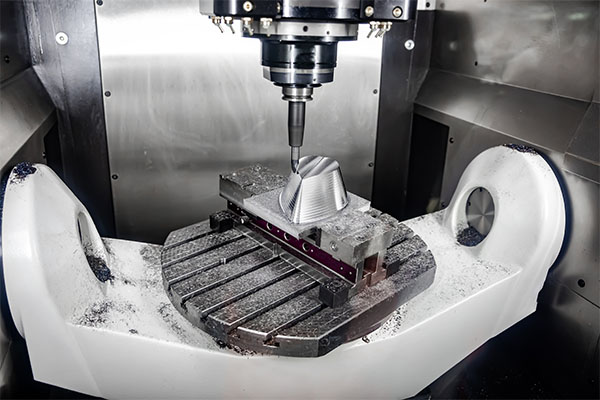
10. How Can You Achieve High-Quality Results with Plastic CNC Machining?
Achieving high-quality results with plastic CNC machining requires a combination of precision, careful planning, and using the right materials and tools. What’s the secret to success?
First, it’s essential to select the right material for the specific application. Different plastics have varying properties, and using the wrong material can result in poor-quality parts that don’t perform as expected.
Next, using the right tools is key to achieving a smooth finish and accurate results. Investing in high-quality cutting tools designed for plastic machining helps reduce tool wear and ensures the production of precision parts. Regular tool maintenance and calibration are also essential for consistent results.
Finally, machine settings should be adjusted to suit the specific type of plastic being machined. Cutting speeds, feed rates, and tool paths should all be optimized for the material to prevent defects like melting or warping.
11. How Does Plastic CNC Machining Work for Small Batch Production?
Plastic CNC machining is an ideal choice for small batch production due to its precision and flexibility. But why is it such a great fit for low-volume manufacturing?
The main advantage of using CNC machining for small batch production is its ability to produce high-quality parts quickly and efficiently. Unlike traditional methods like injection molding, which require expensive molds and setup, CNC machining doesn’t require tooling, making it perfect for small orders and custom parts.
Moreover, CNC machines are programmable, allowing for easy adjustments and reprogramming between batches. This makes it possible to produce a wide variety of parts without needing to invest in multiple molds or production lines.
The fast turnaround time and precision of plastic CNC machining ensure that businesses can meet customer demands quickly without sacrificing quality. Whether it’s for prototype testing or short-run production, CNC machining offers a flexible, cost-effective solution for small batch manufacturing.
12. What Are the Cost Implications of Plastic CNC Machining?
Plastic CNC machining offers several advantages in terms of cost-effectiveness, but it’s essential to understand the cost implications involved. How do costs break down?
Material costs are a significant factor in determining the overall cost of production. While plastic is generally cheaper than metals, the type of plastic used can impact the cost. High-performance plastics like PEEK or polycarbonate tend to be more expensive than common plastics like ABS.
Another cost factor is machine time. CNC machining involves fixed costs for machine setup and programming, so the more parts that are produced, the lower the per-part cost. However, for small batches, these fixed costs can make the per-unit cost higher than mass production methods like injection molding.
Finally, tooling costs can also contribute to the overall cost of production. While CNC machining doesn’t require molds, specialized tooling may still be needed to achieve the desired results. However, these costs are typically lower than the cost of creating injection molds.
13. How Can Plastic CNC Machining Benefit Startups and Small Businesses?
Plastic CNC machining offers several advantages for startups and small businesses, particularly when it comes to custom production and quick turnaround times. So, how can it help your business grow?
For startups, plastic CNC machining provides an affordable way to prototype and create small runs of custom parts. This allows businesses to test products in the market without committing to large-scale production, which can be risky and expensive.
Additionally, CNC machining offers flexibility in production. As businesses grow and evolve, they can quickly adapt their designs and modify production without the need for significant investments in new equipment or tooling.
Finally, the speed and cost-effectiveness of plastic CNC machining make it a viable option for small businesses looking to scale quickly without breaking the bank. Whether it’s for prototyping, short runs, or small batch production, CNC machining offers the flexibility and precision needed for startups to succeed.
14. What Are the Latest Trends in Plastic CNC Machining?
Plastic CNC machining is continually evolving with the advent of new technologies and materials. So, what’s the latest?
One of the key trends is the integration of 3D printing with CNC machining. Hybrid processes that combine 3D printing for rapid prototyping with CNC machining for final production are becoming more common. This allows manufacturers to combine the flexibility of 3D printing with the precision of CNC machining.
Another trend is the use of advanced plastic materials like carbon-fiber-reinforced plastics, which offer high strength-to-weight ratios and are ideal for industries like aerospace and automotive.
Finally, automation is playing an increasingly important role in plastic CNC machining. Automated processes reduce human error, speed up production, and improve overall efficiency, making it an even more attractive option for manufacturers looking to reduce costs and improve turnaround times.
15. How Can You Find the Right Plastic CNC Machining Supplier?
Finding the right plastic CNC machining supplier is crucial for ensuring high-quality results. What should you look for?
Start by evaluating the supplier’s experience in your specific industry. A supplier with expertise in your field will understand your unique requirements and provide the right solutions for your project.
Next, assess the supplier’s equipment and capabilities. Ensure they have the machines and tools needed to handle your project, particularly if you require high-precision parts or specialized materials.
Finally, consider customer reviews and testimonials. A reputable supplier should have a proven track record of delivering high-quality parts on time and within budget. Look for feedback from other customers to gauge their reliability and performance.
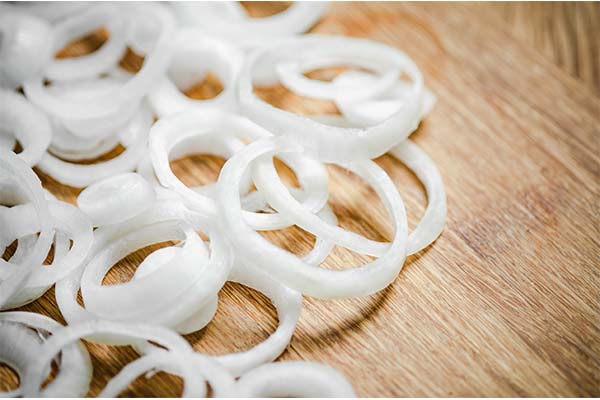
Раздел часто задаваемых вопросов
В1: What is Plastic CNC Machining?
Plastic CNC machining refers to the use of computer-controlled machines to precisely cut, shape, and finish plastic materials for various industries and applications.
В2: How does Plastic CNC Machining work?
Plastic CNC machining works by using rotary tools to cut and shape plastic materials according to a digital design, ensuring precision and repeatability.
В3: What types of plastics are best for CNC machining?
Common plastics for CNC machining include acrylic, polycarbonate, ABS, nylon, and PEEK, each chosen based on their specific properties and applications.
В4: How is Plastic CNC Machining different from Metal CNC Machining?
Plastic CNC machining is generally faster, cheaper, and easier than metal machining due to the softer nature of plastics, but metals offer superior strength and durability for demanding applications.
В5: What industries benefit from Plastic CNC Machining?
Plastic CNC machining benefits industries such as automotive, medical, consumer electronics, and prototyping, where precision and low-volume production are key.