Введение в допуски обработки на станках с ЧПУ
Обработка на станках с ЧПУ является одним из самых точных методов производства, позволяющим производить детали с высокой точностью и повторяемостью. Однако критическим фактором в обработке на станках с ЧПУ является концепция допусков, которая определяет допустимые отклонения в размерах деталей. Допуски необходимы для обеспечения того, чтобы детали подходили и функционировали правильно в их окончательной сборке, особенно при работе с индивидуальными заказами. Понимание различных типов допусков и того, как они влияют на процесс обработки, имеет решающее значение как для производителей, так и для клиентов. В этом руководстве мы рассмотрим ключевые аспекты Допуски обработки на станках с ЧПУ, включая их типы, факторы, влияющие на них, и способы их оптимизации для обеспечения экономической эффективности и точности.
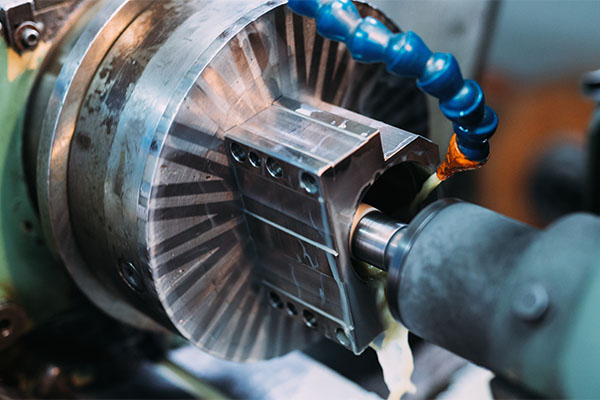
Что такое допуски обработки на станках с ЧПУ?
Определение допусков при обработке на станках с ЧПУ
Допуски — это допустимые пределы отклонений в размерах детали. В обработке на станках с ЧПУ это относится к тому, насколько фактические размеры данной детали могут отличаться от предполагаемых проектных размеров, оставаясь при этом приемлемыми для функционирования. По сути, допуски определяют диапазон, в котором может изменяться деталь, и это гарантирует, что деталь все еще может правильно вписаться в предполагаемую сборку.
При обработке на станках с ЧПУ используются два основных типа допусков: допуски размеров и геометрические допуски. Допуски размеров относятся к допустимому отклонению от указанного измерения (например, длины, ширины и высоты), в то время как геометрические допуски описывают приемлемые отклонения в форме или виде детали (например, прямолинейность, плоскостность или округлость). Эти допуски имеют решающее значение для обеспечения правильного функционирования деталей и их совместимости с другими компонентами.
Почему допуски имеют решающее значение при обработке на станках с ЧПУ
Точность станка с ЧПУ во многом определяется его способностью поддерживать жесткие допуски. В таких отраслях, как аэрокосмическая, автомобильная или медицинская промышленность, где компоненты должны подходить друг другу безупречно, допуски становятся еще более значимыми. Указывая точные допуски, производители могут гарантировать, что детали соответствуют требуемой функциональности и надежны в условиях эксплуатации.
Напротив, если допуски слишком свободны, конечная часть может не соответствовать предполагаемым критериям производительности, что приведет к дорогостоящим ошибкам или сбоям. С другой стороны, слишком жесткие допуски могут увеличить производственные затраты и неоправданно увеличить сроки выполнения заказа. Достижение правильного баланса имеет важное значение для достижения как качества, так и экономической эффективности.
Типы допусков обработки на станках с ЧПУ, которые вам следует знать
Допуски размеров
Допуски размеров определяют, насколько размеры детали могут отличаться от предполагаемого измерения. Это наиболее часто указываемые допуски в обработке на станках с ЧПУ. Например, вал может иметь длину 100 мм с допуском ±0,1 мм. Это означает, что фактическая длина может варьироваться от 99,9 мм до 100,1 мм и все еще быть приемлемой.
Размерные допуски могут применяться к линейным измерениям (например, длина, ширина или высота детали) и угловым измерениям (например, углы между элементами). Чем жестче допуск, тем точнее должно быть измерение, что часто требует использования современных станков с ЧПУ и большего времени на изготовление.
Геометрические допуски
Геометрические допуски используются для управления формой, ориентацией и расположением элементов на детали. Эти допуски имеют решающее значение для обеспечения того, чтобы детали подходили друг другу так, как задумано. Например, отверстие может быть идеально круглым или располагаться в точном месте относительно других элементов на детали. Геометрические допуски включают:
- Прямолинейность: Гарантирует, что элемент, например край или ось, является идеально прямым.
- Плоскостность: Гарантирует, что поверхность ровная в пределах указанного допуска.
- Округлость: Гарантирует, что отверстие или цилиндрический элемент имеют идеально круглую форму.
- Позиция: Определяет точное местоположение объекта относительно других.
Указывая эти геометрические допуски, конструкторы могут гарантировать, что детали соответствуют требуемым функциональным критериям.
Допуски на качество обработки поверхности
Допуски на качество поверхности определяют гладкость поверхности детали. Во многих приложениях качество поверхности может иметь решающее значение для производительности детали, особенно для компонентов, которые движутся или контактируют с другими деталями. Качество поверхности часто указывается с использованием измерений шероховатости, таких как Ra (средняя шероховатость), Rz (средняя максимальная высота) и Ry (максимальная высота профиля).
Почему допуски имеют значение: влияние на качество и функциональность деталей
Роль допусков в функциональности детали
Когда дело доходит до функциональности детали, допуски, применяемые в процессе обработки, могут существенно повлиять на то, будет ли деталь соответствовать и функционировать так, как задумано. Например, в автомобильных или аэрокосмических компонентах небольшие отклонения в размерах деталей могут повлиять на то, насколько хорошо детали взаимодействуют друг с другом, что приводит к таким проблемам, как плохая подгонка, неэффективность или даже отказ под нагрузкой.
В некоторых случаях небольшое отклонение размера или формы может не быть критической проблемой. Однако для высокопроизводительных приложений, таких как компоненты двигателей, медицинские приборы или высокоточные приборы, даже самые незначительные нарушения допусков могут привести к дорогостоящим ошибкам и отказу продукта. Поэтому понимание того, как выбрать правильный допуск для каждой детали, имеет важное значение.
Допуски и контроль качества деталей
Допуски напрямую влияют на процесс контроля качества. Жесткие допуски требуют более сложного оборудования и более высоких уровней контроля, гарантируя, что детали соответствуют строгим стандартам. Такие методы контроля качества, как координатно-измерительные машины (КИМ) или оптические измерительные системы, часто используются для проверки того, что детали находятся в указанном диапазоне допусков. Чем выше допуск, тем более строгим становится процесс контроля.
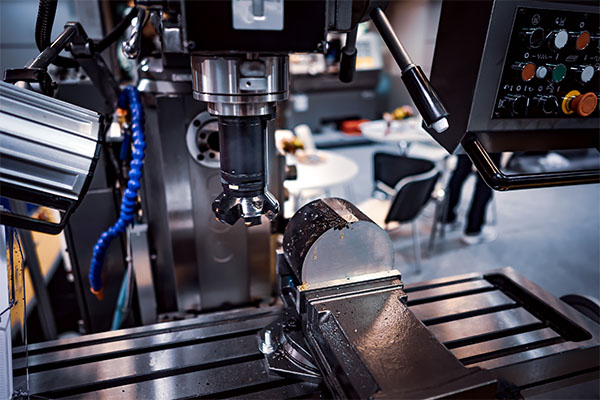
Факторы, влияющие на допуски обработки на станках с ЧПУ
Свойства материалов и допуски
Материал, выбранный для детали, оказывает значительное влияние на допуски, которые могут быть достигнуты. Некоторые материалы, такие как металлы, могут быть более стабильными и их легче обрабатывать с жесткими допусками, в то время как другие, такие как пластики или композиты, могут испытывать большую деформацию во время обработки. Твердость материала, тепловое расширение и прочность играют роль в том, насколько легко материал может поддерживать жесткие допуски.
Например, такие металлы, как нержавеющая сталь и алюминий, обычно используются для обработки на станках с ЧПУ, поскольку они обеспечивают отличную размерную стабильность и позволяют достичь жестких допусков без чрезмерного износа инструмента. Однако более мягкие материалы, такие как пластик или резина, могут потребовать особых мер для обеспечения точной обработки.
Возможности станков с ЧПУ
Тип используемого станка с ЧПУ также играет решающую роль в определении уровня точности, который может быть достигнут. Станки с ЧПУ имеют различную степень точности, и у каждого станка есть свои ограничения, когда дело касается поддержания жестких допусков. Высокоточные станки, такие как те, которые используются в аэрокосмическом производстве, могут поддерживать допуски ±0,001 мм или даже жестче, в то время как станки общего назначения могут достигать допусков только ±0,05 мм.
При выборе станка важно сопоставить его возможности с требованиями конкретной изготавливаемой детали. Понимание ограничений вашего оборудования с ЧПУ поможет выбрать правильный допуск для детали и избежать ненужных корректировок, которые могут привести к увеличению затрат.
Инструментальная обработка и износ
Качество инструмента и его износ с течением времени также могут влиять на допуски, достигаемые при обработке на станках с ЧПУ. По мере износа инструментов они могут вызывать небольшие изменения размеров деталей. Регулярное техническое обслуживание и замена инструментов имеют решающее значение для поддержания постоянной точности.
Чтобы уменьшить влияние износа инструмента, многие производители используют усовершенствованные покрытия или твердосплавные инструменты, которые рассчитаны на более длительный срок службы и сохранение остроты. Более того, регулировка параметров обработки, таких как скорость, скорость подачи и глубина резания, может помочь повысить точность готовой детали.
Распространенные диапазоны допусков обработки на станках с ЧПУ для различных материалов
Допуски для металлических деталей
Металлические детали часто должны соответствовать очень жестким допускам, особенно в таких отраслях, как аэрокосмическая и автомобильная. Например, детали из нержавеющей стали могут быть обработаны с допуском ±0,05 мм, в то время как детали из алюминия могут достигать допусков ±0,025 мм. Эти допуски гарантируют, что металлические детали правильно подходят друг другу и хорошо работают в сложных условиях.
Допуски для пластиковых деталей
С другой стороны, пластиковые детали, как правило, сложнее обрабатывать с теми же жесткими допусками, что и металлы. Допуск для пластиковых деталей обычно составляет от ±0,1 мм до ±0,5 мм в зависимости от типа пластика и сложности детали. Пластик может быть склонен к короблению, усадке или расширению из-за перепадов температур, что может усложнить поддержание постоянных допусков.
В некоторых случаях для критических применений могут использоваться высокопроизводительные пластики, такие как PEEK или PTFE. Эти материалы могут достигать более жестких допусков, но требуют более передовых методов обработки.
Допуски для композитных материалов
Композитные материалы, которые часто используются в аэрокосмической и автомобильной промышленности, представляют свои собственные проблемы, когда дело доходит до обработки на станках с ЧПУ. Композиты часто являются слоистыми и могут иметь разные свойства в зависимости от направления волокон, что может привести к изменениям прочности и размерной стабильности детали. Допуски для композитных деталей обычно составляют от ±0,1 мм до ±0,3 мм в зависимости от конкретного материала и геометрии детали.
Выбор правильных допусков для деталей, изготовленных по индивидуальному заказу
Определение требований толерантности
Выбор правильных допусков для ваших изготовленных на заказ деталей начинается с понимания конкретной функции детали. Например, детали, которые должны подходить друг другу или взаимодействовать с другими компонентами, требуют более жестких допусков для обеспечения надлежащего выравнивания и функциональности. С другой стороны, детали, которые не требуют точной подгонки, могут быть спроектированы с более свободными допусками для снижения производственных затрат.
Чтобы определить оптимальный допуск для детали, важно учитывать как требования к конструкции, так и возможности производственного процесса. Слишком жесткие допуски могут увеличить время производства, затраты на оснастку и вероятность ошибок, в то время как слишком свободный допуск может поставить под угрозу функциональность или качество детали.
Баланс между точностью и стоимостью
Хотя может возникнуть соблазн указать максимально жесткие допуски, чтобы обеспечить наивысший уровень точности, это часто приводит к более высоким затратам. Достижение более жестких допусков обычно требует более современного оборудования, более длительного времени обработки и повышенных расходов на проверку. Для многих деталей более экономически эффективно указать допуски, которые соответствуют предполагаемой функции детали, не выходя за рамки точности.
Достижение правильного баланса между допуском и стоимостью является ключом к достижению как качества, так и эффективности при индивидуальной обработке.
Как допуски влияют на стоимость обработки на станках с ЧПУ
Взаимосвязь между допусками и производственными затратами
В обработке на станках с ЧПУ существует прямая связь между жесткостью допуска и общей стоимостью производства. Более жесткие допуски обычно требуют более продвинутой технологии, повышенной точности и большего времени для обеспечения соответствия детали спецификации. В результате производственные затраты, как правило, растут с необходимостью более жестких допусков. Это связано с тем, что на каждом этапе процесса, от первоначального проектирования до окончательной проверки, требуется больше внимания к деталям.
Например, при обработке детали с допуском ±0,1 мм, станку может потребоваться сделать больше проходов или использовать специализированные инструменты, чтобы обеспечить достижение желаемых размеров. Это может увеличить время обработки и расход материала, что приводит к более высоким затратам. С другой стороны, деталь с допуском ±0,5 мм может не потребовать столько времени или специализированного оборудования для производства, что снижает себестоимость продукции.
Кроме того, детали с более жесткими допусками часто требуют более строгого контроля качества и проверки. В зависимости от области применения это может включать использование сложных инструментов, таких как координатно-измерительные машины (КИМ), лазерное сканирование или другие высокоточные измерительные устройства. Стоимость этих инструментов, а также время, затрачиваемое на проверку каждой детали, может быстро увеличиваться при производстве компонентов с очень жесткими допусками.
Как допуски влияют на время выполнения заказа
Допуски также влияют на время выполнения проектов по обработке на станках с ЧПУ. Детали с более жесткими допусками требуют более тщательного планирования и дополнительного времени для процесса обработки. Например, деталь, требующая допуска ±0,01 мм, может обрабатываться на несколько часов дольше, чем аналогичная деталь с допуском ±0,5 мм.
Дополнительное время, необходимое для соответствия более жестким допускам, также может задержать общие сроки производства, особенно в проектах с несколькими деталями или сложной геометрией. Кроме того, если в процессе обработки возникают ошибки, их может потребоваться исправить, что приведет к дополнительной доработке и дальнейшему увеличению времени выполнения заказа.
Чтобы минимизировать влияние жестких допусков на время выполнения заказа, производителям часто приходится тщательно планировать и оптимизировать процесс обработки. Это может включать выбор правильных станков, корректировку параметров резки и использование наиболее эффективных траекторий инструмента, чтобы обеспечить выполнение детали в срок.
Понимание ограничений вашего оборудования и инструментов с ЧПУ
Точность станков с ЧПУ и ее влияние на допуски
Возможности используемого оборудования с ЧПУ являются решающим фактором в определении уровня точности, который может быть достигнут в процессе обработки. Различные типы станков с ЧПУ имеют разную степень точности, и важно понимать ограничения используемых станков, чтобы избежать установки нереалистичных ожиданий по допускам.
Например, высококлассные фрезерные станки с ЧПУ или токарные станки, используемые в аэрокосмической или медицинской промышленности, могут достигать допусков вплоть до ±0,001 мм. Эти станки используют передовые технологии, такие как многоосевое фрезерование, лазерная калибровка и системы обратной связи в реальном времени для поддержания предельной точности.
С другой стороны, универсальные станки с ЧПУ могут не поддерживать такие жесткие допуски, и достижимая точность может составлять только ±0,05 мм или ±0,1 мм. Важно сопоставить требуемые допуски детали с возможностями имеющегося оборудования с ЧПУ, чтобы гарантировать, что производство является как осуществимым, так и экономически эффективным.
Выбор подходящего станка с ЧПУ для работы
Выбор правильного станка с ЧПУ для работы имеет решающее значение для достижения желаемого допуска. Например, если требуемый допуск жесткий, а деталь имеет сложную геометрию, может потребоваться инвестировать в высокоточные станки, такие как токарные станки CNC Swiss или 5-осевые фрезерные станки. Эти станки позволяют обрабатывать сложные детали с минимальной погрешностью, но они требуют более высоких первоначальных затрат и более длительного времени производства.
Однако для более простых деталей с более свободными допусками может быть достаточно стандартного фрезерного станка с ЧПУ. Выбор правильного станка на основе требуемых допусков может помочь оптимизировать производство, снизить затраты и гарантировать, что деталь соответствует стандартам качества.
Инструменты и износ инструментов
Качество и состояние инструментов, используемых при обработке на станках с ЧПУ, также играют важную роль в точности конечного продукта. Со временем инструменты могут изнашиваться, что приводит к размерным изменениям и отклонениям от указанных допусков. Поэтому регулярное техническое обслуживание и своевременная замена инструментов имеют решающее значение для поддержания стабильных результатов, особенно при обработке деталей с жесткими допусками.
Кроме того, материал и покрытие инструмента могут влиять на его долговечность и точность. Например, твердосплавные инструменты, как правило, сохраняют остроту и размерную стабильность с течением времени, что делает их предпочтительным выбором для высокоточной обработки с ЧПУ. Инструменты с покрытием, например, с покрытием из нитрида титана (TiN) или алмазоподобного углерода (DLC), также могут помочь снизить износ и продлить срок службы инструмента, что особенно важно при обработке сложных материалов или производстве деталей с жесткими допусками.
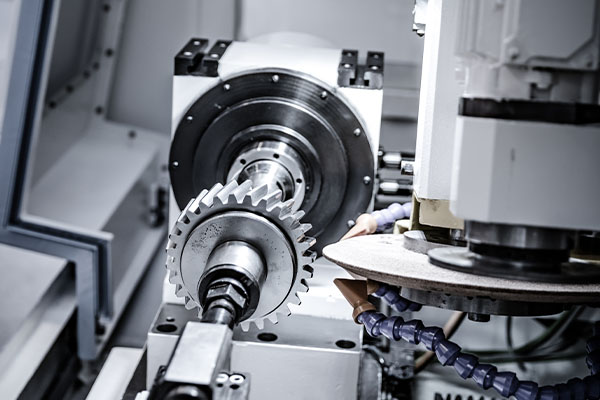
Оптимизация допусков для сокращения сроков выполнения работ и снижения затрат
Баланс точности и эффективности
Хотя для некоторых приложений требуются жесткие допуски, они могут привести к увеличению сроков поставки и повышению производственных затрат. Поэтому одной из ключевых задач в обработке на станках с ЧПУ является поиск правильного баланса между точностью и эффективностью. Достижение требуемых допусков при одновременном снижении производственных затрат и поддержании быстрого времени выполнения заказа имеет важное значение для удовлетворения потребностей клиентов и сохранения конкурентоспособности на рынке.
Один из способов оптимизировать допуски, сохраняя при этом эффективность, — сосредоточиться на критических размерах детали. Не все характеристики детали должны соответствовать самым жестким допускам. Определив, какие размеры наиболее важны для функциональности детали, и применяя более жесткие допуски только там, где это необходимо, производители могут сократить время и затраты на обработку, не ставя под угрозу производительность детали.
Оптимизация процесса обработки
Чтобы оптимизировать время обработки и сократить расходы, производители также должны рассмотреть возможность оптимизации процесса обработки. Этого можно достичь путем выбора правильных стратегий обработки, таких как использование наиболее подходящих режущих инструментов, регулировка скорости подачи и оптимизация траекторий инструмента. Станки с ЧПУ, которые обладают расширенными возможностями автоматизации, такими как устройства смены инструмента или автоматизированные системы загрузки, также могут помочь сократить время, затрачиваемое на непроизводительные задачи, что еще больше ускоряет процесс.
Другим эффективным способом оптимизации допусков является использование передовых производственных технологий, таких как аддитивное производство или гибридная обработка. Эти методы часто позволяют достичь того же уровня точности, что и традиционная обработка с ЧПУ, при этом сокращая отходы материала, износ инструмента и время производства.
Реальные примеры проблем толерантности и их решения
Пример 1: Аэрокосмический компонент с жесткими допусками
В аэрокосмическом производстве такие детали, как компоненты двигателя и структурные элементы, должны соответствовать чрезвычайно жестким допускам для обеспечения безопасности и производительности. Один из реальных примеров касается изготовленного на заказ алюминиевого кронштейна, используемого в системе шасси самолета. Требуемый для этой детали допуск составлял ±0,01 мм, что представляло собой проблему из-за потенциального теплового расширения материала и сложной геометрии конструкции.
Для соответствия жестким требованиям допуска производитель использовал высокоточный 5-осевой станок с ЧПУ с лазерной калибровкой. Кроме того, они внедрили многоступенчатый процесс обработки, включающий прецизионную черновую обработку, получистовую и чистовую обработку. Деталь также прошла несколько раундов контроля качества с использованием координатно-измерительной машины (КИМ), чтобы убедиться, что она соответствует требуемым спецификациям.
Пример 2: Компонент медицинского устройства со сложной геометрией
В индустрии медицинских устройств такие компоненты, как хирургические инструменты и имплантаты, требуют высокой точности для обеспечения их правильной и безопасной работы. Одним из примеров является обработка титанового имплантата колена, которая требовала сложных геометрических допусков, включая точную округлость и позиционные допуски для отверстий, в которых будут размещаться винты.
Для достижения этих допусков производитель использовал швейцарский токарный станок с ЧПУ и возможностью использования приводного инструмента. Это позволило им обработать деталь за одну установку, снизив риск ошибок, вызванных перепозиционированием. Затем деталь была проверена с использованием высокоточной оптической измерительной системы, чтобы убедиться в соблюдении всех геометрических допусков.
Контроль качества: обеспечение точности и постоянства при обработке на станках с ЧПУ
Важность тщательной проверки
Контроль качества играет важную роль в обеспечении соответствия деталей заданным допускам и требуемым стандартам. При обработке на станках с ЧПУ проверка начинается во время процесса настройки и продолжается на протяжении всего производственного цикла. Многие производители используют координатно-измерительные машины (КИМ) и лазерные сканирующие системы для точного измерения деталей и обнаружения любых отклонений от требуемых спецификаций.
Инспекция может также включать визуальные проверки, оценку качества поверхности и функциональное тестирование в зависимости от предполагаемого использования детали. Для деталей с особенно жесткими допусками могут потребоваться дополнительные этапы проверки, чтобы гарантировать отсутствие отклонений в процессе обработки.
Роль автоматизированных систем контроля
С развитием технологий многие производители теперь полагаются на автоматизированные системы контроля точности деталей, обработанных на станках с ЧПУ. Эти системы используют лазеры, камеры или другие датчики для непрерывной проверки размеров деталей по мере их производства. Автоматизированный контроль не только повышает точность, но и ускоряет процесс контроля качества, позволяя производителям выявлять ошибки на ранних стадиях и предотвращать дорогостоящие ошибки.
Постоянное совершенствование и циклы обратной связи
Помимо формальных проверок, производители должны внедрять программы непрерывного улучшения для мониторинга производительности обработки с течением времени. Отслеживая ключевые показатели, такие как износ инструмента, производительность станка и точность производства, производители могут определять области для улучшения и вносить необходимые корректировки для постоянного поддержания жестких допусков.
Роль допусков в индивидуальных заказах на обработку
Спецификации индивидуальной обработки и допусков
При размещении заказов на индивидуальную обработку заказчики должны четко сообщать свои требования к допускам, чтобы избежать недоразумений или дорогостоящих ошибок. Предоставление подробных чертежей, которые указывают желаемые допуски для каждой характеристики детали, поможет обеспечить бесперебойность процесса обработки. Заказчики также должны работать со своими производственными партнерами, чтобы определить, достижимы ли указанные допуски в рамках заданного срока и бюджета.
Сотрудничество с поставщиками станков с ЧПУ
Сотрудничество между заказчиком и поставщиком имеет решающее значение для обеспечения четкого понимания и соблюдения допусков. Это может включать обсуждение выбора материалов, рассмотрение возможностей оборудования с ЧПУ и обеспечение того, чтобы конструкция детали была оптимизирована как для требований технологичности, так и для требований допусков.
Поставщики часто могут предоставить ценные идеи о том, как скорректировать конструкцию деталей, чтобы облегчить их обработку, при этом соблюдая спецификации допусков. Работая вместе, производители и клиенты могут достичь наилучшего возможного баланса точности, стоимости и времени выполнения.

Часто задаваемые вопросы
Каковы наиболее распространенные допуски для обработки на станках с ЧПУ?
Наиболее распространенный допуски для обработки на станках с ЧПУ диапазон от ±0,05 мм до ±0,5 мм, в зависимости от сложности и материала детали. Более жесткие допуски, такие как ±0,01 мм, обычно требуются для высокоточных приложений, таких как аэрокосмические или медицинские приборы.
Как допуски влияют на стоимость обработки на станках с ЧПУ?
Более жесткие допуски обычно увеличивают затраты на обработку с ЧПУ, поскольку они требуют более современного оборудования, более длительного времени обработки и более строгого контроля. Более мягкие допуски могут помочь сократить затраты и время производства.
Можно ли с помощью обработки на станках с ЧПУ добиться жестких допусков для всех материалов?
В то время как многие материалы, такие как металлы, могут достигать жестких допусков при обработке на станках с ЧПУ, некоторые материалы, такие как пластик и композиты, сложнее обрабатывать с высокой точностью из-за их внутренних свойств. Важно выбрать подходящий материал для требуемого допуска.
Как можно снизить стоимость обработки деталей с жесткими допусками?
Чтобы сократить расходы, сосредоточьтесь на оптимизации конструкции для технологичности. Указывайте допуски только там, где они необходимы для функционирования детали, и выбирайте правильный процесс обработки и оборудование для работы. Сотрудничество с производителем также может помочь определить области, где расходы могут быть снижены без ущерба для качества.
Какие инструменты лучше всего подходят для достижения жестких допусков при обработке на станках с ЧПУ?
Твердосплавные инструменты и инструменты с покрытием, например, с покрытием из нитрида титана (TiN), идеально подходят для достижения жестких допусков. Эти инструменты дольше сохраняют остроту, что снижает риск износа инструмента и размерных отклонений.