การแนะนำ
การออกแบบเครื่องจักรกลซีเอ็นซี plays a pivotal role in the manufacturing industry, influencing the production of precise and high-quality parts. This guide will walk you through the essential aspects of CNC machining design, covering everything from material selection to the future trends in the field. By understanding the key components of CNC design and its relationship with the machining process, manufacturers can optimize efficiency, reduce costs, and enhance product quality.
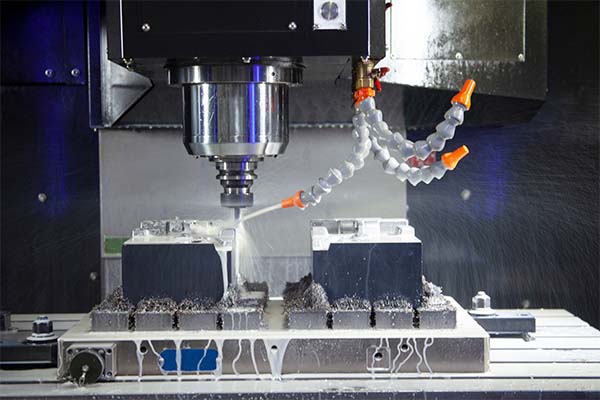
1. What is CNC Machining Design?
When we talk about CNC machining design, we’re referring to the process of creating detailed plans for parts that will be manufactured using CNC machines. But here’s the kicker: it’s not just about creating the shape of the part; it’s about ensuring that every detail, from material selection to tolerance requirements, is carefully considered.
CNC machining design involves several key components. First, designers must select materials that are appropriate for the specific part and machining process. They also need to specify tolerances and fits, which determine the part’s final dimensions and how it will fit with other components. Surface finish requirements are another critical aspect, as these determine how the part will look and function after machining.
The importance of design in CNC machining cannot be overstated. A well-designed part ensures that the manufacturing process runs smoothly, minimizes errors, and ultimately leads to a high-quality product. Without good design, even the most advanced CNC machines can struggle to produce accurate parts, leading to increased costs and production delays.
Key Components of CNC Design | Explanation |
---|---|
การเลือกใช้วัสดุ | Choosing the right material based on part requirements |
Tolerances and Fits | Defining the precision of the part for assembly |
Surface Finish | Determining the texture and appearance of the final product |
2. How Does CNC Machining Design Work?
Understanding how CNC machining design works starts with an overview of the CNC process itself. The CNC machining process involves using computer-controlled machines to shape parts from raw materials. But here’s where it gets interesting: the design of the part dictates how the CNC machine operates, from tool paths to cutting speeds.
One of the primary design considerations during machining is the toolpath. Designers must plan the tool’s movement to ensure it cuts the material in the most efficient way possible. The shape of the part, its geometry, and material properties all affect how the tool moves through the material.
Common CNC machining design challenges include accommodating complex geometries and minimizing material waste. The complexity of a part’s design can influence the time it takes to machine, the number of tools required, and the material’s usage. To overcome these challenges, designers need to think strategically about how to structure the part to minimize the machining process complexity while still achieving the desired design.
Design Considerations | Impact on CNC Machining |
---|---|
Tool Path | Affects machining efficiency and precision |
Complex Geometries | Increases machining time and complexity |
Material Usage | Influences production costs and material waste |
3. What Are the Key Elements of CNC Design?
Several critical elements form the foundation of effective CNC machining design. The first of these is material selection. Choosing the right material for a CNC part affects everything from durability to cost. Metals, plastics, and composites each have unique properties that influence the machining process. For example, while aluminum is relatively easy to machine, harder metals like titanium can be more challenging but are necessary for parts requiring high strength.
Tolerances and fits are another key component of CNC design. These define the acceptable limits of dimensional variations in a part and determine how well the part will fit with other components. Tight tolerances require more advanced machining techniques and may increase production costs, but they’re necessary for high-precision parts used in industries like aerospace or medical devices.
The final critical element is surface finish. CNC machines can produce parts with a variety of surface finishes, from rough to polished. The choice of surface finish will depend on the part’s intended use. For instance, a part that will be exposed to harsh environments may require a smoother surface to prevent corrosion, while a less critical part may have a more textured finish.
Element | Importance |
---|---|
การเลือกใช้วัสดุ | Affects part durability and machining process |
Tolerances and Fits | Ensures proper assembly and functionality |
Surface Finish | Impacts part functionality and appearance |
4. What is the Role of CAD Software in CNC Design?
When it comes to CNC machining design, CAD (Computer-Aided Design) software plays a central role. Ready for the good part? CAD software allows designers to create detailed 3D models of parts, which are then used to generate machine instructions for CNC machines.
The benefits of using CAD software for CNC design are immense. It helps designers visualize parts before they’re made, ensuring that any potential design issues are caught early. CAD also enables the creation of complex geometries that would be challenging to visualize or create manually. For example, 3D modeling in CAD can help predict how the part will behave under stress or how it will fit with other components.
Popular CAD software for CNC machining includes programs like AutoCAD, SolidWorks, and Fusion 360. These tools offer various features, such as simulation capabilities, which allow designers to test their designs virtually before sending them to production. CAD software integrates seamlessly with CNC machines, using CAM (Computer-Aided Manufacturing) systems to convert designs into machine-readable instructions.
CAD Software | Features |
---|---|
AutoCAD | 2D and 3D drawing capabilities |
SolidWorks | Advanced 3D modeling and simulation |
Fusion 360 | Cloud-based design and machining integration |
5. Why Are Tolerances Important in CNC Machining Design?
Tolerances are crucial in CNC machining because they define the limits within which a part’s dimensions are allowed to vary. What’s the real story? Without proper tolerances, parts may not fit together correctly, leading to faulty assemblies or, worse, product failure.
In CNC machining, choosing the right tolerance is vital. If the tolerance is too tight, it may increase production costs and machining time. On the other hand, if the tolerance is too loose, the part may not perform as expected. For example, in the automotive industry, even small deviations in tolerances can affect the performance of parts, leading to safety concerns.
To choose appropriate tolerances, designers must consider the part’s intended use and the capabilities of the CNC machine. For highly critical components, such as those used in aerospace, tight tolerances are necessary, while less critical parts may allow for looser tolerances, saving on production costs.
Tolerance Type | Impact |
---|---|
Tight Tolerances | Higher machining cost and time |
Loose Tolerances | Reduced cost, but potential for poor fit |
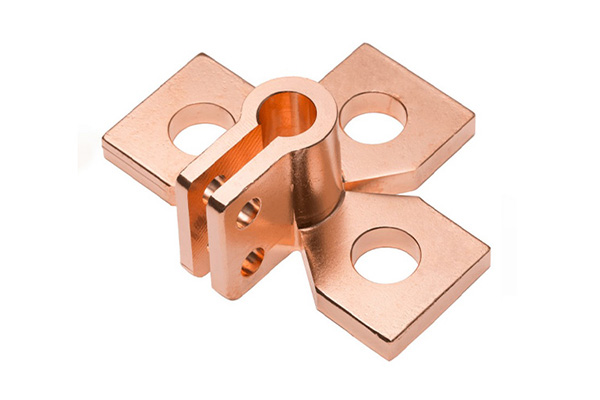
6. How Do Material Choices Impact CNC Design?
Material selection is one of the most important factors in CNC machining design. But here’s the kicker: choosing the right material can make or break a project. Material properties directly affect machining speeds, tool wear, and the final part’s performance.
Different materials respond to machining processes in various ways. For example, metals like aluminum and steel are common in CNC machining because they’re durable and easy to machine. However, harder materials like titanium require specialized tools and techniques due to their toughness. The material you choose will determine the cutting speed, the type of tooling required, and even the level of precision achievable.
To select the right material, designers need to consider factors like strength, weight, and resistance to corrosion. For example, parts used in automotive applications need to be strong and lightweight, so aluminum might be the preferred choice. Conversely, parts used in medical devices must be biocompatible, which may lead to a preference for titanium or certain plastics.
วัสดุ | Key Considerations |
---|---|
อลูมิเนียม | Lightweight, easy to machine, corrosion-resistant |
เหล็ก | Strong, durable, versatile |
ไทเทเนียม | Strong, corrosion-resistant, requires special tooling |
7. What Are the Best Practices for CNC Design for Efficiency?
Efficiency in CNC machining design is all about optimizing the design to reduce production time and cost. The most effective way to achieve this is by designing parts that are easy to machine. Ready for the good part? Simpler designs are often the most efficient, as they require fewer steps and less tool changeover.
To optimize designs for manufacturing, designers should consider the following best practices: choose materials that are easy to machine, simplify part geometries, and design with tool access in mind. Parts with complex shapes or intricate details require more time to machine and can result in higher costs due to increased tool wear and machining time.
Designing for ease of machining also means minimizing the number of tool changes. Each time a tool changes, the machine has to stop, which increases production time. By carefully considering the toolpath and minimizing tool changes, designers can drastically reduce machining time and costs.
Best Practices | ผลประโยชน์ |
---|---|
Simplify Part Geometries | Reduces machining time and complexity |
Optimize Tool Access | Minimizes tool changes and increases efficiency |
Choose Easy-to-Machine Materials | Reduces wear and machining time |
8. How to Handle Complex Geometries in CNC Design?
Handling complex geometries in CNC machining design requires advanced strategies. What’s the real story? It’s all about using the right tools and software to make those complex designs work within the constraints of CNC machines.
The first step in dealing with complex geometries is selecting the appropriate machining process. Some geometries may require multi-axis machining, which allows for greater flexibility in cutting shapes. Additionally, using advanced CAD software can help designers create and simulate intricate geometries before they even get to the machine.
Case studies show that successful complex designs often involve a combination of careful planning, software tools, and skilled machinists. For example, a company designing custom parts for the aerospace industry may rely on multi-axis CNC machines and advanced simulation software to ensure their designs are both manufacturable and cost-effective.
Strategy | ผลประโยชน์ |
---|---|
Multi-Axis Machining | Allows for complex shapes and intricate details |
Advanced CAD Software | Enables simulation of complex designs |
Skilled Machinists | Ensures successful implementation of complex designs |
9. What Are the Common Mistakes in CNC Design?
CNC design is an intricate process, and even small mistakes can have significant consequences. Ready for the good part? The good news is that most mistakes can be avoided with proper planning and attention to detail.
One common mistake in CNC machining design is not considering the limitations of the machine. Every CNC machine has its own set of capabilities, and designing a part that exceeds those capabilities can lead to costly errors. Another common issue is neglecting to account for tool accessibility, which can make the machining process more difficult and time-consuming.
By working closely with experienced machinists and using advanced simulation software, designers can avoid these mistakes. Properly verifying the design with simulations before production begins ensures that the final part will meet expectations.
ความผิดพลาด | How to Avoid |
---|---|
Exceeding Machine Capabilities | Understand the machine’s limitations during design |
Ignoring Tool Accessibility | Design with tool access in mind to reduce machining time |
Skipping Simulations | Use simulation software to verify designs before production |
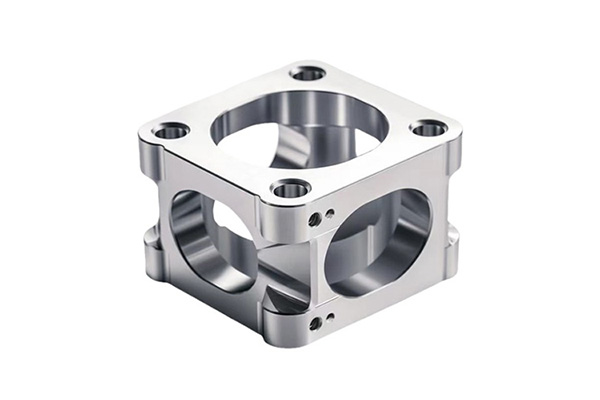
10. How Can You Improve Your CNC Machining Designs?
Improving CNC machining designs requires continuous refinement and the use of the latest tools and techniques. This is where it gets interesting: small adjustments to your design can lead to significant improvements in efficiency and product quality.
One way to improve your designs is by using advanced simulation tools to test how the part will perform during machining. This helps identify potential issues early in the process, allowing for changes before costly mistakes are made. Another way to enhance your designs is by collaborating with your machining team to gather feedback and refine your approach.
By focusing on quality control and using iterative design processes, you can ensure that your CNC machining designs are always improving.
Improvement Method | ผลประโยชน์ |
---|---|
Simulation Tools | Identify issues early, saving time and money |
Collaboration with Machinists | Refine designs for optimal machinability |
Iterative Design Process | Continuously improve design quality |
11. How Does CNC Machining Design Affect Production Time?
CNC machining design plays a direct role in determining production time. But here’s the kicker: a well-designed part can significantly reduce machining time, while a poorly designed part can cause delays and inefficiencies.
Design choices like part complexity, material selection, and tool accessibility all impact machining time. More complex parts require more machining steps, which can increase production time. On the other hand, designing parts with simpler geometries and better tool access can reduce machining time and increase overall efficiency.
By designing with production time in mind, manufacturers can streamline the process, reduce delays, and keep costs down.
Design Factor | Impact on Production Time |
---|---|
Part Complexity | Increases machining time and tool wear |
การเลือกใช้วัสดุ | Affects cutting speeds and machining time |
Tool Accessibility | Minimizes time spent on tool changes |
12. How to Ensure Quality in CNC Machining Design?
Ensuring quality in CNC machining design is about more than just getting the dimensions right. Ready for the good part? Quality control methods, like using CAD software for design verification and testing prototypes before full production, play a major role in achieving consistency.
Testing prototypes allows designers to evaluate the design’s functionality before mass production. By identifying potential issues early, manufacturers can make adjustments before costly mistakes are made. Additionally, using quality control methods such as digital inspection tools ensures that each part meets the required specifications.
Quality Control Method | ผลประโยชน์ |
---|---|
Prototype Testing | Identifies issues before full production |
Digital Inspection Tools | Ensures part consistency and precision |
CAD Design Verification | Detects design flaws early in the process |
13. What Are the Costs Associated with CNC Machining Design?
The costs associated with CNC machining design can vary depending on several factors. What’s the real story? Material selection, part complexity, and the number of design iterations can all affect the overall cost of CNC machining.
For example, selecting high-end materials may increase the cost of both material and machining time. Similarly, designing complex parts with tight tolerances can require more advanced machining techniques, which can drive up production costs. On the other hand, optimizing designs for manufacturability and minimizing material waste can help reduce costs.
By balancing design complexity and cost considerations, manufacturers can create cost-effective CNC machining designs that still meet quality standards.
Cost Factor | Impact on CNC Design Cost |
---|---|
การเลือกใช้วัสดุ | Affects material and machining costs |
Part Complexity | Increases machining time and tool wear |
Design Iterations | More iterations lead to higher costs |
14. How Does CNC Machining Design Relate to Prototyping?
Prototyping plays a crucial role in CNC machining design. This is where it gets interesting: prototyping allows designers to test and refine their designs before full production begins. By creating a prototype, manufacturers can identify design flaws and make necessary adjustments.
The prototyping process involves producing a small batch of parts to test the design’s functionality and fit. During this stage, designers can gather feedback and make improvements to the design before proceeding to mass production. Iteration is key here—refining the design after testing ensures that the final product meets all specifications.
Prototyping Stage | ผลประโยชน์ |
---|---|
Initial Prototype | Identifies design flaws early |
Iteration Process | Refines design for optimal performance |
Final Prototype | Validates design before mass production |
15. What Are the Future Trends in CNC Machining Design?
The future of การออกแบบเครื่องจักรกลซีเอ็นซี is full of exciting possibilities. Innovations in CNC design technology, such as automation and AI, are shaping the future of manufacturing. What’s the real story? These advancements will streamline processes, reduce costs, and increase precision.
Automation is already playing a significant role in CNC machining design, allowing for faster production and fewer human errors. AI is being integrated into CNC machines, enabling them to adapt and optimize machining processes on the fly. As industry demands continue to evolve, CNC design will need to keep up, incorporating the latest technologies to stay competitive.
Future Trend | Impact |
---|---|
ระบบอัตโนมัติ | Speeds up production and reduces errors |
AI Integration | Optimizes machining processes in real time |
Evolving Design Demands | Drives innovation in CNC design technology |
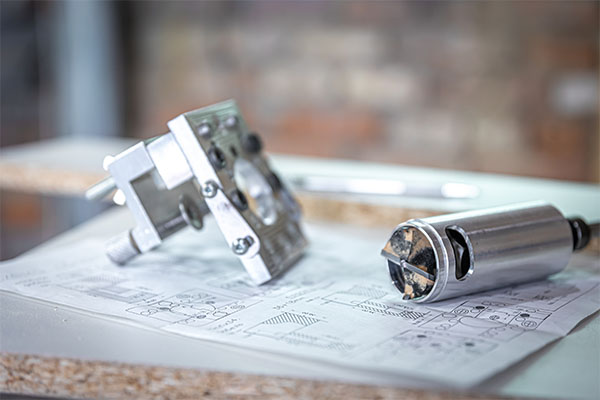
ส่วนคำถามที่พบบ่อย
คำถามที่ 1: What is CNC machining design?
CNC machining design refers to the process of creating blueprints or plans that dictate how a part or component should be shaped using a CNC machine. It includes specifications like material, dimensions, and tolerances.
คำถามที่ 2: How does CAD software work in CNC design?
CAD (Computer-Aided Design) software is used to create detailed 3D models of parts that can be directly fed into CNC machines. It helps streamline the design-to-production process, ensuring precision and efficiency.
ไตรมาสที่ 3: Why are tolerances important in CNC machining?
Tolerances ensure that parts are produced with the correct dimensions, allowing them to fit together properly. Too loose or tight tolerances can affect the performance and functionality of the final product.
ไตรมาสที่ 4: How can I avoid mistakes in CNC machining design?
By double-checking your design, using advanced software for simulations, and working closely with experienced machinists, you can avoid common mistakes such as incorrect dimensions or impractical designs.
คำถามที่ 5: What is the cost of CNC machining design?
The cost can vary depending on factors like material selection, complexity of the design, and the number of iterations required. It’s important to balance design quality with cost-efficiency to get the best value from CNC machining.