การแนะนำ
เครื่องจักรกลซีเอ็นซีที่มีความแม่นยำ refers to the use of computer-controlled machinery to create highly accurate and customized parts. This process allows manufacturers to produce parts with incredible precision, which is essential in industries such as automotive, aerospace, medical devices, and consumer electronics. Precision is crucial for ensuring that these parts fit together perfectly and function as expected. You might be wondering how CNC machining can make a difference in your operations—the answer lies in its ability to produce high-quality parts consistently, with tight tolerances and minimal error. In this article, we will explore the key features of CNC precision machining parts, helping you understand their importance in modern manufacturing.
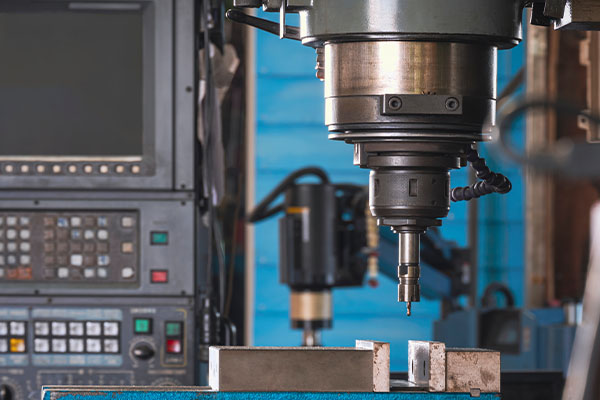
How CNC Machining Works: A Simplified Overview
CNC (Computer Numerical Control) machining involves using computer software to control the movements of machinery such as mills, lathes, and grinders. The process begins with a 3D digital model of the part to be produced. This model is translated into machine instructions through CAD/CAM software, which guides the machine in cutting and shaping the material with extreme precision.
The Role of Computer Programming
The heart of CNC machining lies in its programming. CAD (Computer-Aided Design) software creates the blueprint for the part, while CAM (Computer-Aided Manufacturing) software takes over to transform that design into machine instructions. This ensures that every cut, drill, and mill is executed precisely according to the design specifications.
Machine Components Involved
CNC machines are equipped with various components that work together to achieve precision. These include the controller, which is responsible for interpreting the code, the tool head, which performs the cutting, and the workpiece, which is the material being shaped. Each component must work in harmony to produce parts that meet the desired specifications.
Bucket Brigade: You might be wondering, how does the machine know exactly what to do? Through a series of programmed movements based on the CAD/CAM data, CNC machines follow a set path, ensuring that every part is consistent with the others.
Key Features of CNC Precision Machining Parts
The key features of CNC precision machining parts lie in their accuracy, repeatability, and material integrity. Unlike traditional manufacturing methods, which can result in variability and human error, CNC machining ensures that parts are produced with exceptional consistency.
Accuracy and Repeatability
CNC machines excel at creating parts with tight tolerances, often within a few microns. This means that the same part can be reproduced hundreds or thousands of times without deviation from the original design. This consistency is vital in industries where even the smallest error can lead to malfunctions or failure.
Tolerances and Their Importance
Tolerances refer to the allowable deviation from the desired dimensions. Tight tolerances are crucial in applications such as aerospace or medical device manufacturing, where parts must fit and function precisely. CNC machining allows for the production of parts with tolerances as tight as ±0.001 mm, ensuring that they meet stringent quality standards.
The Role of Material Selection
The materials used in CNC machining can vary greatly, from metals like steel and aluminum to plastics and composite materials. The choice of material can impact the strength, durability, and weight of the part. CNC machines are capable of working with a wide range of materials, allowing manufacturers to select the best option for their specific needs.
Bucket Brigade: So, how do manufacturers ensure parts meet these tolerances? By using advanced CNC machines, automated quality checks, and constant monitoring throughout the machining process, manufacturers can achieve and maintain tight tolerances on every part.
Material Selection for CNC Precision Machining Parts
The materials chosen for CNC precision machining play a significant role in determining the strength, durability, and overall performance of the final product. CNC machines can handle a wide variety of materials, each with its unique properties and challenges.
Commonly Used Materials
Aluminum, steel, and titanium are among the most commonly used materials in CNC machining due to their strength, durability, and versatility. Aluminum is lightweight and highly machinable, making it ideal for a range of applications, from consumer electronics to automotive parts. Steel offers greater strength and resistance to wear, while titanium is known for its corrosion resistance and high strength-to-weight ratio.
How Material Choice Affects Quality
The choice of material directly influences the precision and durability of the part. Softer materials like plastics are easier to machine but may lack the strength required for heavy-duty applications. Conversely, harder materials like steel or titanium may be more challenging to machine but offer superior strength and longevity.
Balancing Cost and Quality
Material costs can vary significantly, so it’s important to balance the need for high-quality materials with the project budget. While higher-end materials may offer superior performance, they may also come with a higher price tag. Manufacturers must consider the requirements of the part and the expected conditions it will face to choose the best material for the job.
Bucket Brigade: Wondering how material selection impacts the machining process? It directly affects the machine settings, cutting tools, and the overall cost of production. By understanding material properties, manufacturers can optimize the machining process for better results.
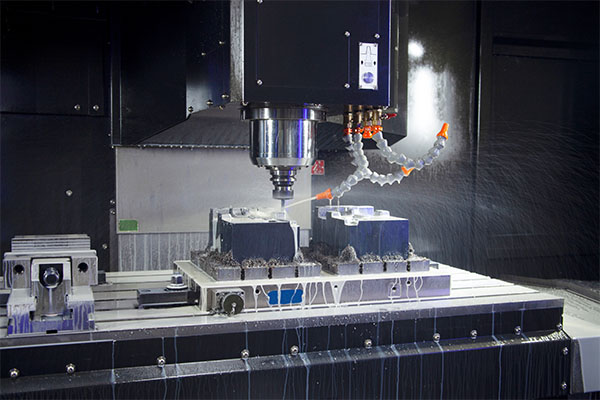
Tolerances in CNC Precision Machining: What You Need to Know
Tolerances are a critical aspect of CNC precision machining, ensuring that each part meets the desired specifications. In manufacturing, tolerances refer to the acceptable limits of variation in the dimensions of a part. In the context of CNC machining, these tolerances are extremely tight, often within thousandths of an inch.
Defining Tolerances and Why They Matter
Tolerances are essential because they dictate how closely a part’s dimensions align with the design specifications. For example, in aerospace or medical device manufacturing, tight tolerances ensure that parts fit together correctly and function properly. Even a small deviation can cause malfunctions or lead to costly repairs.
How Tight Tolerances Affect Part Function and Assembly
Tighter tolerances result in parts that fit more precisely during assembly, reducing the likelihood of defects or failures. However, achieving these tight tolerances requires advanced CNC machines and skilled operators who can monitor the process and make adjustments as needed.
Examples of Tolerance Ranges
In general, CNC machining can achieve tolerances ranging from ±0.005 inches for less critical applications to as tight as ±0.001 inches for high-precision parts. These tolerances ensure that parts meet the exact requirements of industries such as aerospace, automotive, and medical devices, where precision is crucial.
Bucket Brigade: You’re probably wondering, how can manufacturers guarantee such precision? Through a combination of advanced CNC technology, constant monitoring, and testing, manufacturers can ensure that parts consistently meet the required tolerances.
The Role of CAD/CAM Software in CNC Precision Machining
CAD (Computer-Aided Design) and CAM (Computer-Aided Manufacturing) software are essential tools in the CNC machining process. These software programs allow designers and manufacturers to create detailed models of parts, simulate machining processes, and generate the code that guides CNC machines.
What Is CAD and CAM?
CAD software is used to create digital designs and 3D models of parts, while CAM software takes these designs and translates them into machine-readable instructions. CAM software allows for the optimization of the machining process, ensuring that parts are produced efficiently and with high precision.
How CAD/CAM Software Improves Accuracy and Efficiency
By using CAD/CAM software, manufacturers can reduce the likelihood of errors and optimize the machining process for better accuracy and speed. CAD models provide a clear blueprint for the CNC machine to follow, while CAM software helps streamline the production process, minimizing downtime and improving overall efficiency.
Integration with CNC Machines
CAD and CAM software are integrated with CNC machines, ensuring a seamless transition from design to production. The software generates the necessary code to guide the machine, allowing for precise cuts and shaping of the material. This integration ensures that parts are produced exactly as specified, reducing the risk of mistakes.
Bucket Brigade: You might be asking, how does software improve the overall CNC machining process? By automating many aspects of the design and production process, CAD and CAM software help manufacturers achieve higher accuracy, reduced waste, and faster production times.
CNC Machining vs Traditional Manufacturing: A Comparison
When comparing CNC machining to traditional manufacturing methods, the key difference lies in the level of precision and automation. Traditional manufacturing methods often rely on manual labor and are more prone to human error, while CNC machining uses computer-controlled machines that ensure parts are produced with greater consistency and accuracy.
Precision Comparison
CNC machining offers superior precision, with tolerances as tight as ±0.001 inches. Traditional methods, on the other hand, can struggle to achieve such high levels of accuracy, especially when working with complex designs or intricate parts.
Speed and Efficiency
CNC machines can produce parts faster than traditional methods due to automation and programming. Once the machine is set up, it can run continuously, making it ideal for mass production. Traditional methods, however, may require more manual labor, which can slow down production and increase costs.
Cost-Effectiveness
While CNC machining may have higher upfront costs due to the machinery and software involved, it can be more cost-effective in the long run due to its speed and precision. Traditional methods, while less expensive initially, may result in higher production costs due to inefficiencies and the need for manual labor.
Bucket Brigade: Wondering which method is better for your business? It all depends on the complexity, quantity, and required precision of the parts being produced. CNC machining is ideal for high-precision, complex parts, while traditional methods may still be useful for simpler designs.
Types of CNC Machining: Milling, Turning, and More
CNC machining encompasses a variety of techniques, each with its own strengths and applications. Some of the most common types of CNC machining include milling, turning, and electrical discharge machining (EDM).
การสี
งานกัดซีเอ็นซี is a process where a rotating cutter removes material from a workpiece. It’s ideal for creating parts with complex shapes or features, such as holes, slots, and contours. Milling machines are versatile and can handle a wide range of materials.
การเปลี่ยนแปลง
CNC turning involves rotating a workpiece while a cutting tool removes material. This process is commonly used to create cylindrical parts, such as shafts or bolts. Turning is ideal for parts that require precision on the outside diameter.
Electrical Discharge Machining (EDM)
EDM is a process that uses electrical sparks to remove material from a workpiece. This method is ideal for creating parts with intricate details or very hard materials that cannot be machined with traditional cutting tools.
Bucket Brigade: Wondering which CNC machining technique is best for your parts? It all depends on the shape and features of the part you need to create. CNC milling is versatile and can handle complex shapes, while turning is ideal for cylindrical parts.
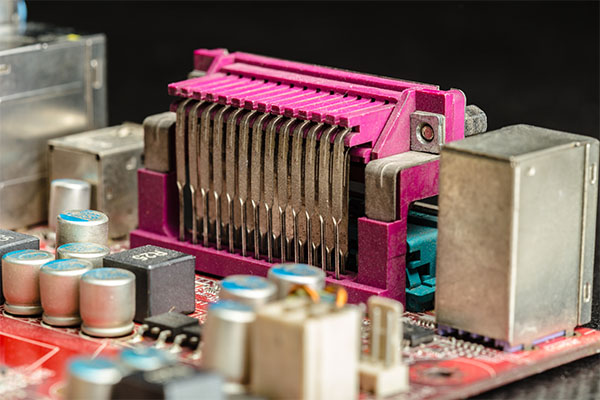
The Benefits of Using CNC Precision Machining Parts
CNC precision machining offers several advantages over traditional manufacturing methods, including improved accuracy, repeatability, and efficiency. The precision and flexibility provided by CNC machines make them ideal for producing high-quality parts in industries ranging from aerospace to medical devices.
High Accuracy and Consistency
One of the key benefits of CNC machining is the ability to produce parts with high accuracy and consistency. CNC machines are capable of achieving tolerances as tight as ±0.001 inches, ensuring that each part is produced to exact specifications.
Flexibility in Design
CNC machining allows for the production of parts with complex designs, intricate features, and tight tolerances. This flexibility makes it possible to create custom parts for specialized applications, such as medical devices or aerospace components.
Cost-Effectiveness for Small-Batch Production
While CNC machining can have high upfront costs, it is highly cost-effective for small-batch or custom production. CNC machines can quickly switch between different designs without the need for tooling changes, making them ideal for industries that require frequent design changes or small production runs.
Bucket Brigade: You may be wondering, why is CNC machining so versatile? It’s due to the advanced technology, precise control, and adaptability of CNC machines, which allow for the creation of a wide range of parts for various industries.
Industries That Rely on CNC Precision Machining Parts
CNC precision machining parts are used across a variety of industries, including aerospace, automotive, medical devices, and electronics. Each of these industries has specific requirements for precision and quality, making CNC machining an essential technology.
การบินและอวกาศ
The aerospace industry relies on CNC precision machining to produce parts with tight tolerances and high durability. Parts such as turbine blades, engine components, and structural elements are often produced using CNC machining due to the need for precision and strength.
ยานยนต์
CNC machining plays a critical role in the automotive industry, where high-quality parts are essential for vehicle performance. CNC machines are used to produce engine components, transmission parts, and other critical components that must meet strict quality standards.
อุปกรณ์ทางการแพทย์
In the medical device industry, CNC machining is used to produce components with high precision and reliability. Parts such as surgical instruments, implants, and diagnostic equipment often require tight tolerances to ensure proper functionality and safety.
Bucket Brigade: You may be asking, how do CNC parts fit into these high-tech industries? With their precision and versatility, CNC machined parts are essential for producing reliable, high-performance components for critical applications.
Common Challenges in CNC Precision Machining
ในขณะที่ เครื่องจักรกลซีเอ็นซีที่มีความแม่นยำ offers numerous benefits, it also comes with its own set of challenges. These challenges can include machine maintenance, material selection, and the potential for errors during production.
Machine Wear and Tear
CNC machines are complex pieces of machinery, and over time, parts can wear out. Regular maintenance is essential to ensure that the machine continues to operate at peak performance and produce parts with consistent quality.
Material Defects and Irregularities
Material defects, such as inclusions or uneven hardness, can cause issues during machining. It’s important to carefully inspect materials before beginning the machining process to avoid defects in the final product.
Troubleshooting Common Issues
Some common issues in CNC machining include tool wear, part distortion, and poor surface finish. These issues can usually be mitigated through regular machine maintenance, proper tool selection, and careful monitoring during production.
Bucket Brigade: Wondering how to deal with these challenges? By investing in high-quality machines, regularly maintaining your equipment, and monitoring the production process, you can minimize issues and ensure that your parts meet the desired specifications.
The Future of CNC Precision Machining
CNC precision machining is constantly evolving with the introduction of new technologies and innovations. These advancements are reshaping the future of manufacturing, making it possible to create even more complex parts with greater efficiency and precision.
Emerging Technologies in CNC Machining
Some of the latest innovations in CNC machining include the integration of artificial intelligence (AI) and automation. AI can help optimize machining processes by analyzing data and making real-time adjustments. Automation, on the other hand, can reduce human error and increase production efficiency.
The Role of 3D Printing
3D printing, also known as additive manufacturing, is becoming increasingly important in CNC machining. While CNC machining traditionally involves subtracting material from a workpiece, 3D printing adds material layer by layer to build parts. This technology is being used for rapid prototyping, custom parts, and even complex geometries that are difficult to achieve with traditional machining.
Predictions for the Future
In the next few years, we can expect even more automation and integration of AI in CNC machining. These technologies will enable manufacturers to produce parts faster, with even greater precision, and at a lower cost.
Bucket Brigade: You may be curious, what does the future hold for CNC machining? With the rise of automation and AI, CNC machining will become even more efficient and capable of handling complex designs, allowing manufacturers to push the boundaries of what’s possible.
Quality Control in CNC Precision Machining
Ensuring that CNC machined parts meet the required specifications is essential for maintaining high quality and reliability. Quality control involves a variety of techniques, from visual inspections to advanced measuring tools, to verify that parts are produced to exact tolerances.
The Importance of Quality Control
Quality control is crucial in CNC machining to ensure that parts meet the exact requirements of the design. Any deviation from the desired dimensions can result in faulty parts that may not function properly or fit during assembly.
Methods for Ensuring Quality
Common quality control methods include visual inspections, dimensional measurements, and surface finish checks. High-precision tools such as CMM (Coordinate Measuring Machines) and laser scanners can be used to measure parts with extreme accuracy.
The Role of CNC Operators
CNC operators play a critical role in maintaining quality during the machining process. They are responsible for setting up the machine, monitoring production, and making adjustments as needed to ensure that parts meet the required specifications.
Bucket Brigade: So, how do manufacturers ensure consistent quality? By using advanced inspection tools, following strict quality control procedures, and training operators to spot potential issues, manufacturers can maintain high standards of precision.
Cost Considerations: Is CNC Precision Machining Worth the Investment?
CNC precision machining can be a significant investment for businesses, but the long-term benefits often outweigh the initial costs. It’s important to consider factors such as machine setup, labor, and material costs when evaluating the overall cost-effectiveness of CNC machining.
Breakdown of Cost Factors
The cost of CNC machining depends on several factors, including the complexity of the part, the material used, and the time required to complete the job. Initial setup costs, such as programming and tooling, can be significant, but these costs are often offset by the efficiency and precision offered by CNC machines.
When CNC Machining Is Cost-Effective
CNC machining is most cost-effective when producing parts in medium to high volumes or when tight tolerances and complex geometries are required. For smaller production runs, the cost may be higher, but the benefits of precision and flexibility still make CNC machining a viable option.
Calculating ROI
Calculating the return on investment (ROI) for CNC precision machining involves factoring in both the upfront costs and the long-term savings due to reduced waste, higher efficiency, and fewer defects. Businesses that prioritize quality and precision often find that the investment pays off over time.
Bucket Brigade: Wondering if CNC machining is worth the cost for your business? By evaluating your production needs and considering the long-term benefits, you can determine whether CNC machining is the right choice for your company.
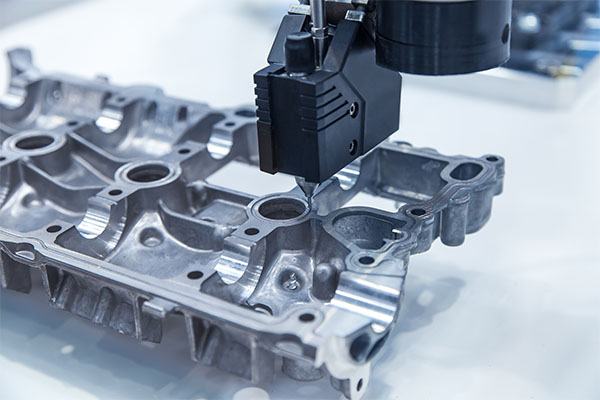
Conclusion: The Value of CNC Precision Machining for Your Business
In conclusion, CNC precision machining offers unparalleled accuracy, flexibility, and efficiency, making it an essential technology for modern manufacturing. Whether you’re in aerospace, automotive, medical devices, or electronics, CNC machining can help produce high-quality parts that meet stringent requirements. By understanding the key features of CNC precision machining parts and how they benefit your business, you can make informed decisions about incorporating this technology into your operations.
Bucket Brigade: Are you ready to explore the advantages of CNC precision machining for your business? Get in touch with a CNC machining service provider to learn more about how this technology can improve your manufacturing processes and lead to higher-quality products.
ส่วนคำถามที่พบบ่อย
- What is CNC precision machining? CNC precision machining involves using computer-controlled machines to manufacture parts with extremely tight tolerances and high accuracy.
- How do CNC machines ensure precision? CNC machines follow programmed instructions from CAD/CAM software, ensuring that each part is produced exactly according to the design specifications.
- What materials are best for CNC machining parts? Common materials include aluminum, steel, titanium, and plastics. The choice of material depends on the application and required properties of the part.
- What is the difference between CNC machining and 3D printing? CNC machining removes material to create a part, while 3D printing adds material layer by layer. Both technologies have unique advantages for different applications.
- How do I select the right CNC machining service? Look for a service provider with experience in your industry, the ability to meet your precision requirements, and a proven track record of delivering high-quality parts.
- What industries use CNC precision machining? CNC machining is used in industries such as aerospace, automotive, medical devices, and electronics, where precision and quality are critical.
- How accurate are CNC machined parts? CNC machines can achieve tolerances as tight as ±0.001 inches, making them ideal for applications that require high precision.
- How much does CNC precision machining cost? The cost depends on factors such as part complexity, material choice, and production volume. CNC machining can be more cost-effective for small to medium production runs.