การแนะนำ
In this article, we’ll explore the world of custom tool steel parts for precision CNC machining. Tool steel is a specialized material crucial in industries that require high-performance components. We’ll dive into the various aspects of tool steel parts, from their importance in CNC machining to the types, processes, and considerations involved in creating custom parts. Whether you’re designing a product for automotive, aerospace, or general manufacturing, understanding custom tool steel parts will help ensure precision and efficiency in your CNC machining processes.
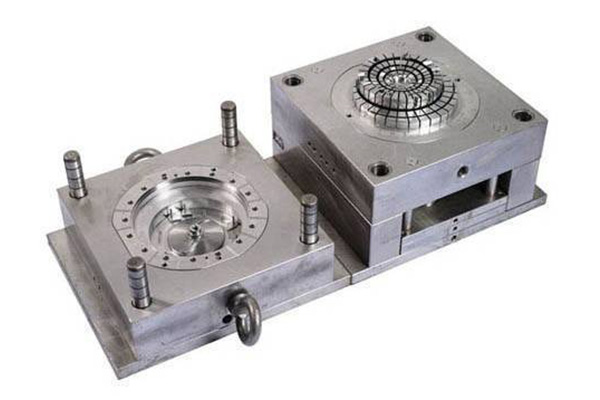
1. What are tool steel parts?
Tool steel parts are components made from tool steel, a high-carbon steel alloy designed specifically for making tools. This material is ideal for creating parts that must withstand high wear and tear. Tool steel parts are characterized by their hardness, strength, and ability to retain sharp edges under stress. What’s the real story? Tool steel is used in various industries to make cutting tools, dies, and molds due to its durability and heat-resistant properties.
Definition and Characteristics of Tool Steel
Tool steel is a special category of steel used in the manufacturing of tools. It is defined by its ability to retain hardness at high temperatures, which makes it perfect for making items like cutting tools, dies, and molds. These steels generally contain high levels of carbon and alloying elements such as chromium, vanadium, molybdenum, and tungsten. These elements help in increasing hardness, wear resistance, and toughness.
Common Types of Tool Steel
There are several types of tool steel, each suited to different applications. Some common categories include:
- High-speed steel (HSS): Ideal for high-temperature applications like cutting tools.
- Cold-work tool steel: Best for tools used in cold conditions and lower temperatures.
- Hot-work tool steel: Designed for applications involving high temperatures, such as dies and molds.
- Plastic mold steel: Specifically used for molding applications due to its ability to withstand high pressure.
Applications and Industries that Use Tool Steel Parts
Tool steel parts are critical in several industries. In the automotive industry, they are used for making tools, dies, and fixtures that are subject to wear and tear. In aerospace, tool steel parts are used for precision instruments, where high strength and heat resistance are essential. Manufacturing and toolmaking industries also rely on tool steel for producing high-quality cutting and shaping tools.
Type of Tool Steel | Characteristics | Common Uses |
---|---|---|
High-speed steel | Retains hardness at high temperatures | Cutting tools, drills |
Cold-work tool steel | Works well in lower temperatures | Punches, dies, shear blades |
Hot-work tool steel | Resistant to high-temperature deformation | Dies for hot forging, extrusion |
Plastic mold steel | Strong and resistant to wear | Molds for plastic injection |
2. Why are custom tool steel parts important for CNC machining?
Custom tool steel parts play a vital role in CNC machining. But here’s the kicker: by customizing the tool steel, manufacturers can achieve specific properties that optimize their parts for performance and durability. Let’s explore why custom parts are so important.
Benefits of Custom Tool Steel Parts in Machining
When designing parts for CNC machining, using custom tool steel allows manufacturers to select the precise alloy and treatment needed to meet the demands of the specific application. Custom tool steel parts are tailored to the exact specifications of a project, ensuring high performance and minimizing waste. This level of customization provides significant advantages in precision, speed, and cost-efficiency.
Precision and Accuracy in Machining Tool Steel
Tool steel is known for its hardness and ability to hold a precise edge, but when custom parts are produced, manufacturers can control the properties of the steel in a way that improves overall precision. With CNC machining, it’s possible to achieve tight tolerances that are required for high-quality components. Customization allows for optimized tool steel performance in specific applications, from cutting tools to intricate machine parts.
How Custom Parts Improve Product Quality
Custom tool steel parts directly contribute to improved product quality by ensuring that the right material properties are matched to the intended application. When tool steel is customized, its inherent qualities—such as hardness, resistance to wear, and strength—are optimized for the production process. This leads to more reliable and long-lasting products, with less chance of failure due to material weaknesses.
Benefit of Custom Tool Steel Parts | Impact on CNC Machining |
---|---|
Precision tailoring | Ensures optimal performance for specific parts |
Reduced material waste | Reduces costs and improves efficiency |
Improved product longevity | Increases the lifespan of the final product |
3. How are custom tool steel parts made?
The process of making custom tool steel parts involves several steps, each designed to enhance the performance and durability of the part. What’s the real story? CNC machining plays a crucial role in the production of custom tool steel parts by offering high precision and repeatability.
CNC Machining Process for Tool Steel
The CNC machining process starts with a carefully designed CAD (computer-aided design) model, which is then used to guide CNC machines in creating the part from tool steel. The process typically involves cutting, milling, turning, and drilling the material to achieve the desired shape and size. CNC machines are programmed with precise instructions to ensure that the part meets the required specifications. Tool steel is durable and requires high precision when being shaped, making CNC machining an ideal process.
Importance of Selecting the Right Tool Steel Grade
Not all tool steels are created equal, and choosing the right grade of steel is critical to ensuring the part will perform as required. Different grades of tool steel offer different characteristics, such as hardness, wear resistance, and toughness. Selecting the right grade ensures that the custom tool steel part can handle the specific stresses of the machining process and the intended application. Grades like A2, D2, and M2 are commonly used for different purposes, depending on the requirements.
Tools and Machines Used in CNC Machining
CNC machining of tool steel requires specialized tools and machines to achieve precision and quality. Common tools used include end mills, drills, and lathes, all of which must be suited for the hardness of tool steel. Machines like CNC lathes, mills, and EDM (electrical discharge machining) are used to create the parts to the precise dimensions required.
Process Step | คำอธิบาย | Key Tools |
---|---|---|
CAD design | Creation of part specifications | CAD software |
เครื่องจักรกลซีเอ็นซี | Cutting and shaping the steel | CNC lathes, mills, drills |
Final inspection | Ensuring quality and precision | Micrometers, calipers |
4. What types of custom tool steel parts can be produced?
Custom tool steel parts can be produced in a wide variety of forms, tailored for different industrial applications. Ready for the good part? Here’s a breakdown of the main types of parts you can create with custom tool steel.
Cutting Tools and Dies
One of the most common uses of tool steel is in the production of cutting tools and dies. These parts are used in a range of applications, from manufacturing to construction. Cutting tools made from tool steel, such as drills, taps, and reamers, need to be hard, wear-resistant, and durable to withstand the forces applied during use.
Molds and Jigs
Tool steel is also essential in making molds and jigs for mass production processes like injection molding and die casting. Molds need to be designed for high precision and strength to ensure that each product produced meets tight tolerances. Jigs, on the other hand, are used to hold parts in place during machining, ensuring consistent and accurate production.
Aerospace and Automotive Parts
Tool steel parts are widely used in the aerospace and automotive industries for manufacturing components that require high strength, resistance to heat, and precision. Aerospace components, such as turbine blades and landing gear, rely on tool steel for its strength and fatigue resistance, while automotive parts like engine blocks and transmission gears use tool steel for durability and performance under high stress.
Type of Tool Steel Part | แอปพลิเคชัน | Key Requirements |
---|---|---|
Cutting tools | Drills, taps, reamers | Wear resistance, hardness |
Molds | Plastic injection, die casting | High precision, strength |
Automotive parts | Gears, engine components | Durability, heat resistance |
5. What is the role of heat treatment in tool steel parts?
Heat treatment is a critical process in the production of tool steel parts, as it significantly influences the material’s properties. This is where it gets interesting: heat treatment can make or break the performance of tool steel components, improving strength, hardness, and wear resistance.
What is Heat Treatment?
Heat treatment is a controlled process used to alter the physical and mechanical properties of tool steel by heating and cooling it in specific ways. This process helps optimize the material’s hardness, toughness, and wear resistance, making it suitable for demanding applications. Common heat treatment processes include annealing, quenching, and tempering.
How Heat Treatment Affects Tool Steel Properties
Heat treatment allows tool steel to reach the ideal balance between hardness and toughness. For example, quenching (rapid cooling) hardens the material, making it suitable for cutting tools, while tempering (slow reheating) reduces brittleness and increases toughness. The right combination of these processes ensures that tool steel parts can withstand the stresses of their application without breaking or wearing down prematurely.
Common Heat Treatment Methods for Tool Steel Parts
Some common heat treatment methods for tool steel include:
- Annealing: Softens the steel to improve machinability.
- Quenching: Increases hardness by rapidly cooling the steel.
- Tempering: Reduces brittleness after quenching, improving toughness.
- Austempering: Provides a balance of hardness and toughness without excessive brittleness.
Heat Treatment Method | Purpose | Effect on Tool Steel |
---|---|---|
Annealing | Softens steel for machining | Improves machinability |
Quenching | Hardens the steel | Increases hardness |
Tempering | Reduces brittleness | Improves toughness |
Austempering | Balances hardness and toughness | Prevents brittleness |
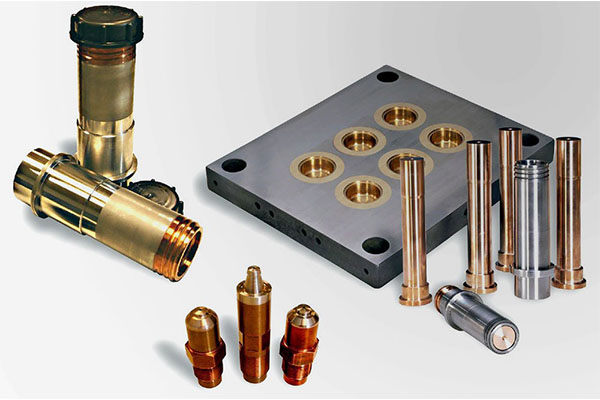
6. How does CNC machining improve the production of tool steel parts?
CNC machining revolutionizes the production of tool steel parts by offering unparalleled precision, repeatability, and efficiency. But here’s the kicker: CNC machining can achieve higher speeds and tighter tolerances than traditional machining methods, making it ideal for complex custom tool steel parts.
CNC vs Traditional Machining Methods
While traditional machining methods like manual milling and turning still have their place, CNC machining takes things to the next level. CNC machines are fully automated and can operate 24/7 with minimal oversight, ensuring that tool steel parts are produced faster and with greater accuracy. Traditional machining, on the other hand, often requires more hands-on involvement and is slower in comparison.
How CNC Machining Enhances Precision and Speed
CNC machining allows for precise control over every aspect of the manufacturing process, ensuring that tool steel parts meet strict tolerances. The ability to input detailed CAD models into CNC machines means that the production of complex geometries is much easier. This is crucial when producing parts that require high precision, such as molds or cutting tools.
Benefits of CNC in Mass Production
For mass production, CNC machining is a game-changer. The ability to replicate the same part over and over with consistent accuracy ensures high-volume manufacturing can meet tight deadlines without sacrificing quality. Furthermore, CNC machines can handle intricate designs and complex shapes, making it possible to produce custom tool steel parts at scale.
CNC Machining Benefit | Impact on Tool Steel Production |
---|---|
ความแม่นยำ | Ensures parts meet tight tolerances |
ความเร็ว | Increases production efficiency |
Scalability | Enables mass production of custom parts |
7. What are the advantages of using tool steel in manufacturing?
Tool steel is widely regarded for its exceptional properties, which make it an essential material in manufacturing. Let’s dig into why tool steel is so highly valued.
Durability and Wear Resistance
One of the key advantages of tool steel is its ability to withstand wear and tear. This is especially important in industries like automotive, aerospace, and manufacturing, where parts are exposed to high friction and stress. Tool steel’s durability ensures that parts can perform for extended periods without the need for frequent replacements.
Hardness and Strength Properties
Tool steel is renowned for its hardness, which is essential for parts that are exposed to heavy stress. Whether it’s a cutting tool, a mold, or a die, the hardness of tool steel ensures that these parts can maintain their sharpness and structural integrity during use. The high strength of tool steel also makes it resistant to deformation under load.
Resistance to High Temperatures
Tool steel is also highly resistant to high temperatures, making it ideal for applications that involve heat. For instance, hot-work tool steels are designed for parts that will be exposed to extreme heat during the manufacturing process, such as forging dies or molds used in injection molding.
Tool Steel Advantage | Benefit to Manufacturing | Example Applications |
---|---|---|
ความทนทาน | Long-lasting parts | Cutting tools, dies |
Hardness | Maintains sharpness under stress | Automotive parts, molds |
Temperature resistance | Withstands heat | Aerospace components |
8. What industries rely on custom tool steel parts?
Custom tool steel parts are essential in several industries, where high-performance components are required. Ready for the good part? Here’s a look at the industries that rely on custom tool steel parts.
อุตสาหกรรมยานยนต์
The automotive industry relies heavily on tool steel for producing high-performance parts like gears, axles, and engine components. These parts must withstand high stresses and extreme conditions, and tool steel offers the durability needed.
อุตสาหกรรมการบินและอวกาศ
In aerospace, tool steel is used for components that must endure high pressures and temperatures, such as turbine blades and structural parts. The strength and heat resistance of tool steel are crucial in ensuring the reliability and safety of these parts.
Manufacturing and Toolmaking Industries
Tool steel is essential in manufacturing industries that produce cutting tools, dies, and molds. These industries rely on tool steel for its ability to withstand the rigors of production and maintain precision over time.
อุตสาหกรรม | Tool Steel Applications |
---|---|
ยานยนต์ | Gears, axles, engine parts |
การบินและอวกาศ | Turbine blades, structural components |
Manufacturing | Cutting tools, molds, dies |
9. How do I choose the right tool steel for my custom parts?
Choosing the right tool steel for your custom parts is crucial to ensuring the performance and longevity of your components. This is where it gets interesting: selecting the right material depends on several factors, including the part’s intended use, required strength, and environmental conditions.
Factors to Consider When Selecting Tool Steel
When choosing tool steel for custom parts, it’s important to consider the part’s purpose. Will it be exposed to high temperatures? Will it need to withstand heavy wear? Understanding these factors will help you select the right tool steel grade. Hardness, toughness, and corrosion resistance are some key properties to look for.
Popular Tool Steel Grades and Their Uses
Different tool steel grades are suited for different applications. For example, A2 is an air-hardening steel suitable for cold-work tools, while D2 is a high-carbon, high-chromium tool steel used for making cutting dies and knives. M2 is a high-speed steel used for cutting tools.
How to Match Tool Steel to the Application
To match tool steel to the application, consider the material’s specific requirements. High-speed steels are ideal for cutting tools, while cold-work tool steels are best for making stamping dies. For hot-work applications, use hot-work tool steels that can withstand high temperatures without losing their strength.
Tool Steel Grade | Best Use | Key Properties |
---|---|---|
A2 | Cold-work tools | Air-hardening, toughness |
D2 | Cutting dies | High-carbon, wear-resistant |
M2 | Cutting tools | High-speed, heat-resistant |
10. What are the cost factors for custom tool steel parts?
The cost of custom tool steel parts depends on several factors, from material costs to machining labor. What’s the real story? Let’s break down the cost factors for creating high-quality custom tool steel parts.
Material Cost Considerations
The material cost for tool steel parts can vary depending on the grade of steel chosen. Higher-grade tool steels tend to be more expensive due to their enhanced properties, such as increased hardness or heat resistance. It’s important to balance material costs with the required performance for the part.
CNC Machining Labor and Setup Costs
CNC machining involves labor and setup costs, which can add to the total cost of manufacturing. The complexity of the custom part will determine how much setup and machining time is required. Parts that require tight tolerances or complex geometries will take longer to machine, increasing labor costs.
Economies of Scale in Mass Production
For large-volume production, economies of scale can significantly reduce the cost per part. The more parts you produce, the less each individual part costs in terms of labor and materials. In mass production, CNC machines can work at high speeds with minimal downtime, improving overall cost-efficiency.
Cost Factor | Impact on Price | Example |
---|---|---|
Material grade | Higher-grade steels cost more | M2 steel vs. A2 steel |
Machining complexity | More complex parts take longer to make | Tight tolerances increase labor |
Production volume | Larger orders reduce per-unit costs | Bulk orders for automotive parts |
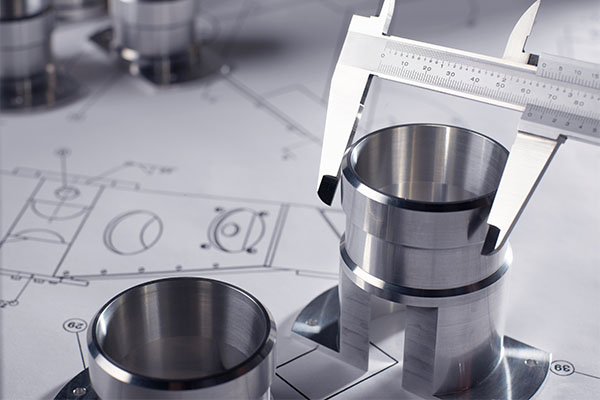
11. How do you ensure quality in custom tool steel parts?
Ensuring quality is crucial in custom tool steel parts. What’s the secret? Maintaining rigorous quality control standards during the CNC machining process ensures that parts meet specifications and perform as required.
Quality Control During Machining
Quality control involves checking the part at various stages of the machining process to ensure that it adheres to the specified dimensions. CNC machines are equipped with sensors and measuring tools to monitor tolerances in real-time. Parts are also inspected visually for defects.
Inspection Methods for Tool Steel Parts
Inspection methods include using tools such as calipers, micrometers, and coordinate measuring machines (CMMs) to check the dimensions and accuracy of the parts. Non-destructive testing methods like ultrasonic testing or X-ray inspection are also used to detect internal flaws without damaging the parts.
Importance of Certifications and Standards
Certifications like ISO 9001 ensure that a manufacturer adheres to high-quality standards. These certifications are essential for proving that the parts meet industry standards and are reliable for use in critical applications.
Quality Control Method | คำอธิบาย | Tools Used |
---|---|---|
Dimensional inspection | Checking part dimensions | Micrometers, calipers |
Non-destructive testing | Detecting internal flaws | Ultrasonic testing, X-ray |
Certification | Ensuring industry compliance | ISO 9001 certification |
12. What are some common challenges in manufacturing custom tool steel parts?
Manufacturing custom tool steel parts presents a unique set of challenges, even for experienced machinists. The complexities of working with tool steel require expertise in both the material properties and the machining process. Let’s dive into the main issues companies face when manufacturing custom tool steel parts.
But here’s the kicker: tool steel is a notoriously tough material, which, while great for durability, can lead to significant wear on tools and equipment. Tool wear and tear is one of the biggest challenges, especially during high-volume production. As tool steel is dense and tough, it rapidly dulls cutting tools, forcing companies to either extend downtime for tool replacements or accept a higher tool cost.
Another key issue is managing material distortion and cracking. When machining custom tool steel parts, the material tends to experience thermal expansion, which can lead to distortion if not carefully controlled. This can result in parts that do not meet the precise dimensions required for their intended application. It’s important to use proper cooling techniques and understand the material’s thermal properties to prevent such issues.
Lastly, machining complexity often presents a barrier. Tool steel has a high tensile strength and hardness, which means it is more difficult to cut, shape, and finish compared to softer materials. Specialized CNC machinery and expertise are essential to overcome this complexity, and the cost of such equipment can be prohibitive for some smaller operations.
With these challenges in mind, companies need to invest in high-quality machinery, proper cooling systems, and skilled technicians to ensure smooth production. It’s a delicate balance, but when done right, the results are worth it.
ท้าทาย | สารละลาย |
---|---|
การสึกหรอของเครื่องมือ | Use carbide tools, regular maintenance |
Material distortion | Apply proper cooling and heating techniques |
Machining complexity | Use high-quality CNC machinery and skilled labor |
13. How can custom tool steel parts be used in prototype manufacturing?
When it comes to prototype manufacturing, custom tool steel parts offer distinct advantages. Tool steel’s ability to withstand high stress, resist wear, and maintain hardness makes it an excellent choice for prototype applications that need to replicate real-world conditions.
What’s the real story? Using tool steel in prototypes allows for a closer simulation of the final product’s performance. When testing parts that will eventually undergo harsh conditions, such as in automotive or aerospace industries, tool steel provides a more accurate reflection of how the material will behave once fully manufactured.
Rapid prototyping with CNC machining has revolutionized the manufacturing process. Companies can quickly create prototype parts using custom tool steel without the extensive lead times that traditional methods require. The precision of CNC machines means that even highly complex designs can be created with remarkable accuracy and speed, facilitating faster product development cycles.
For example, in the automotive industry, tool steel is often used in the creation of prototype gears, brackets, and other critical components. One well-known case involved a company developing a prototype gear that would withstand extreme temperatures and stress. The use of custom tool steel allowed the design to undergo rigorous testing, ensuring that the final product met all performance standards before production began.
So, when developing prototypes, tool steel is not just a durable option—it’s a game changer for companies looking to speed up their development process while maintaining the integrity and functionality of their designs.
แอปพลิเคชัน | ประโยชน์ |
---|---|
Automotive prototypes | High strength, wear resistance, thermal stability |
Aerospace components | Ability to withstand high temperatures and pressure |
Industrial machinery parts | Durability and precision for functional testing |
14. What are the environmental considerations in machining tool steel parts?
Environmental considerations in machining custom tool steel parts are becoming more pressing as industries face increased pressure to adopt sustainable practices. But here’s the kicker: CNC machining, while efficient, can have significant environmental impacts if not managed properly.
One of the most important sustainable practices is waste management. Machining tool steel produces a significant amount of waste, including metal chips, dust, and coolant. Companies must implement effective recycling programs to minimize this waste. For example, many companies recycle the metal chips produced during machining by reprocessing them into new tool steel or using them in other applications. Proper disposal of coolant is also vital to prevent pollution, and many manufacturers now use biodegradable or water-soluble coolants to reduce harmful environmental effects.
Energy consumption in CNC machining is another important consideration. The energy used by CNC machines can be substantial, and as production ramps up, so does energy consumption. Companies are increasingly turning to energy-efficient machinery and practices to lower their carbon footprint. Using renewable energy sources to power CNC machines, for instance, can reduce the environmental impact significantly. Additionally, some CNC machines are now designed to operate with lower energy consumption, providing a win-win for both manufacturers and the environment.
As environmental regulations continue to tighten, companies involved in tool steel machining need to stay ahead of the curve by embracing more sustainable practices. Not only does this help the planet, but it also helps improve operational efficiency and meet the increasing demand for eco-friendly manufacturing.
Environmental Consideration | สารละลาย |
---|---|
Waste management | Implement recycling programs and use biodegradable coolants |
Energy consumption | Invest in energy-efficient machinery, use renewable energy sources |
Pollution prevention | Proper disposal of waste, focus on sustainable practices |
15. How does the future of custom tool steel parts look?
The future of custom tool steel parts looks promising, with innovations on the horizon that will improve both the quality and efficiency of machining processes. Ready for the good part? Technology is driving change, and it’s paving the way for better, faster, and more sustainable production methods.
Trends in tool steel and CNC machining technology are shifting toward more automated, precise, and efficient methods. CNC machines are becoming faster and more accurate, reducing the time it takes to machine custom tool steel parts. Additionally, advancements in laser and plasma cutting technologies are allowing manufacturers to cut tool steel with greater precision and speed, further enhancing productivity.
Innovations in materials and processes are also making an impact. The development of advanced alloy compositions, such as high-speed steels (HSS) and carbide-infused tool steels, is improving the performance of custom tool steel parts in demanding applications. These materials offer superior wear resistance, higher hardness, and better thermal stability, enabling parts to withstand even harsher conditions. As these materials become more widely available, manufacturers will have more options to choose from for specific applications.
Predictions for the future of custom tool steel production include a greater focus on sustainability and energy efficiency. As manufacturers strive to reduce their environmental impact, there will be a continued push for more energy-efficient processes and the use of recycled tool steel. The integration of AI and machine learning in CNC machining is also expected to optimize production processes, making them more adaptive and capable of handling even more complex designs.
Future Trend | Implications |
---|---|
Advanced materials | Improved wear resistance, higher performance |
Automation and AI | Increased speed, precision, and adaptability |
Sustainable manufacturing | Reduced energy consumption and waste |
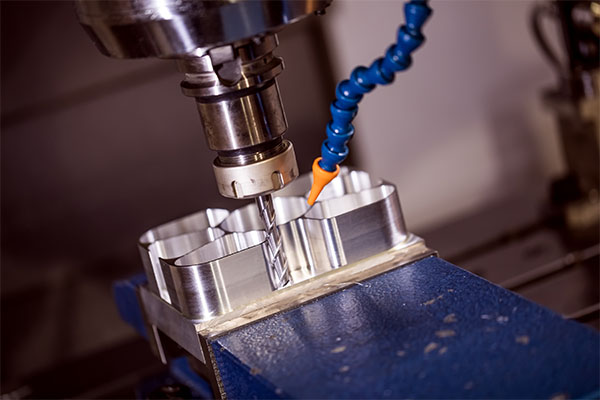
บทสรุป
The future of custom tool steel parts is set to be shaped by continued advancements in technology and materials. Companies that embrace these changes and focus on sustainability will be better positioned to thrive in an increasingly competitive marketplace. Whether it’s through reducing waste, embracing more efficient machining processes, or developing innovative materials, the possibilities for custom tool steel parts are endless. The key to success will be staying ahead of trends and adapting to the evolving demands of the industry.
ส่วนคำถามที่พบบ่อย
- Q1: What are custom tool steel parts?
Custom tool steel parts are specially manufactured components made from high-quality tool steel, designed to meet specific requirements for industries like automotive, aerospace, and manufacturing. - Q2: How does CNC machining work for tool steel parts?
CNC machining uses computer-controlled machines to precisely cut, shape, and finish tool steel parts, ensuring high accuracy and repeatability in production. - Q3: Why is heat treatment important for tool steel parts?
Heat treatment is essential for enhancing the hardness, strength, and durability of tool steel parts, making them suitable for demanding applications. - Q4: What are some common types of tool steel used in machining?
Common types include high-speed steel (HSS), carbon tool steel, and alloy tool steel, each offering unique properties for different machining applications. - Q5: How can I ensure the quality of my custom tool steel parts?
Quality can be ensured through rigorous inspection, adherence to manufacturing standards, and using advanced CNC machinery for precise machining.