Introduction
Designing for CNC machining is critical to ensuring the production of high-quality, cost-effective parts. CNC machining offers precision and flexibility, but without the right design, you may encounter issues that affect efficiency, cost, and quality. This article explores essential tips and insights that will help you master the design process for CNC machining projects. By the end, you’ll have a clear understanding of how to design for CNC machining to achieve the best results.
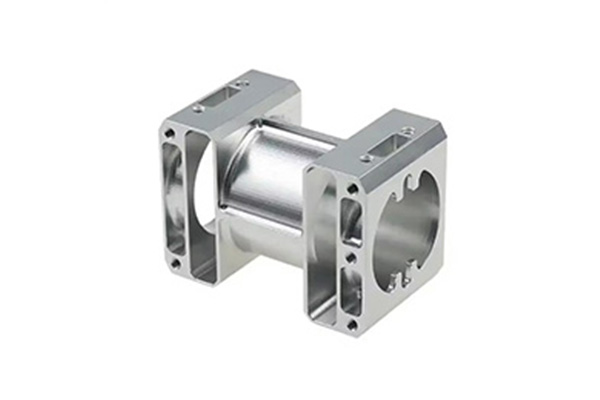
1. Why is Design Crucial for CNC Machining Projects?
The design phase is the foundation of every CNC machining project. Without a well-thought-out design, machining efficiency, part accuracy, and material costs could suffer. But here’s the kicker… an improper design can lead to increased lead times, cost overruns, and unnecessary material waste. So, how do we avoid that? Simple: start with the fundamentals of design that are essential for CNC machining.
First, consider the material you plan to use. The properties of materials such as strength, flexibility, and thermal resistance must align with the intended use of the final product. For instance, aluminum is easy to machine but might not be the best choice for a heavy-duty industrial part. Secondly, the complexity of your design must be compatible with the machining process. Too many intricate features or undercuts could lead to higher costs due to the increased difficulty of machining.
CNC machining is precise, but only if your design accounts for specific tolerances, material constraints, and tool paths. When these factors are considered upfront, you can ensure that your part is not only manufacturable but also optimized for performance. What’s the real story? The design stage sets the tone for the entire project’s success.
Design Factor | Importance | Example |
---|---|---|
Material Choice | Affects machinability, part durability, and cost | Aluminum |
Design Complexity | Impacts cost, lead time, and machining difficulty | Simple vs Complex |
Tolerance Levels | Defines part precision and machinability constraints | Tight vs Loose |
2. What Are the Key Design Principles for CNC Machining?
The key principles of design for CNC machining revolve around simplicity, efficiency, and functionality. Ready for the good part? These principles not only make your design process smoother but also contribute to better overall product performance and reduced production costs.
Start by designing with manufacturability in mind. This means creating parts that can be easily machined without unnecessary complexity. For example, opting for simple geometric shapes, rather than intricate contours, helps reduce machining time and tool wear. Incorporating features like rounded edges and avoiding sharp corners or deep holes can prevent issues during the machining process.
Another principle is understanding the relationship between the cutting tool and the part. Ensuring that the tool can access all parts of the design without obstruction is crucial. For example, designing a part that requires multi-axis machining should allow for adequate tool access to avoid collisions or tool path errors.
Finally, consider the material’s limitations. Some materials, such as stainless steel or titanium, require specific tools or techniques to machine effectively. If your design calls for a material that is difficult to machine, it might be worth reconsidering whether it’s the best choice for your application.
Design Principle | Benefit | Example |
---|---|---|
Manufacturability | Reduces machining time and costs | Simple shapes |
Tool Accessibility | Prevents tool interference and errors | Multi-axis design |
Material Selection | Ensures efficiency and durability | Aluminum for lightweight parts |
3. How Do You Choose the Right Material for CNC Machining?
Selecting the appropriate material for CNC machining can significantly impact the overall quality, performance, and cost of your project. But wait, there’s more… The material choice not only affects the machining process but also influences the final product’s strength, weight, and appearance.
For instance, aluminum is one of the most commonly used materials in CNC machining because it is lightweight, easy to machine, and relatively inexpensive. However, it may not be suitable for high-stress applications. In contrast, steel is much stronger and can withstand higher loads, but it’s also more expensive and harder to machine.
It’s also essential to consider the material’s thermal properties. Some materials expand or contract significantly when exposed to heat, which could lead to dimensional instability in your final product. Materials such as plastics and composites, while easy to machine, may not be ideal for high-heat environments due to their low thermal resistance.
This is where it gets interesting… The right material can reduce post-processing work, improve the longevity of the finished part, and optimize the machining process. For example, using a material that is easier to machine may allow you to use faster cutting speeds, ultimately reducing machining time and cost.
Material | Strength | Machinability | Cost | Best Use Case |
---|---|---|---|---|
Aluminum | Low | Easy | Low | Aerospace |
Stainless Steel | High | Moderate | High | Automotive |
Plastic | Low to Medium | Very Easy | Low to Medium | Consumer Goods |
4. What Are Common Design Mistakes in CNC Machining?
Design errors are common in CNC machining, but they are entirely avoidable with the right knowledge and careful planning. What’s the deal? By understanding and avoiding common design mistakes, you can prevent costly delays and rework.
One of the most frequent mistakes is overcomplicating the design. Intricate features, such as deep holes or tight radii, can be difficult to machine, especially if the part is made from a hard material. The more complex the design, the longer it will take to machine, leading to higher costs. Instead, try to simplify your design by reducing unnecessary features.
Another mistake is not accounting for material limitations. Different materials have different machinability properties, and choosing the wrong material for a specific design can lead to tooling issues, excessive wear, or inaccurate parts. It’s essential to research material properties before deciding which one to use for your design.
Lastly, ignoring tolerances is a critical mistake. Setting overly tight tolerances can result in unnecessary complexity, while too-loose tolerances can lead to parts that don’t meet functional requirements. It’s essential to balance the need for precision with the cost and time associated with achieving those tolerances.
Mistake | Impact | Example |
---|---|---|
Overcomplicating Design | Increases machining time and cost | Tight radii, deep holes |
Ignoring Material Limits | Causes tool wear, errors, or poor part quality | Using hard materials for intricate cuts |
Incorrect Tolerances | Leads to parts that are either inaccurate or expensive to make | Tight tolerance for a non-critical feature |
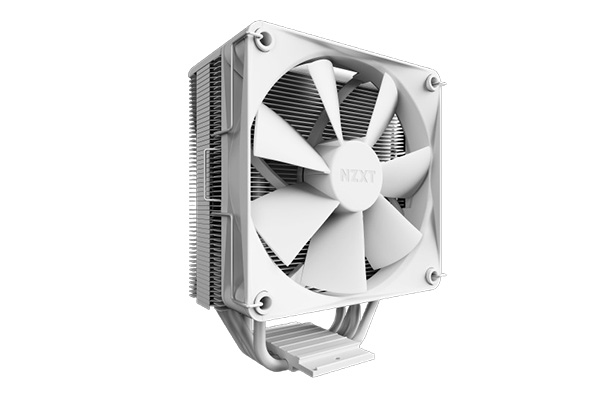
5. How Can You Optimize Your CNC Design for Cost Efficiency?
When designing for CNC machining, optimizing for cost efficiency should always be a top priority. Here’s the thing… By following a few key design strategies, you can reduce manufacturing costs without compromising on quality.
One way to reduce costs is by minimizing machining time. Design parts that can be easily machined with fewer tool changes or simpler cutting paths. For example, avoiding sharp corners and overly detailed features allows the CNC machine to cut more efficiently, reducing machining time and cost.
Another strategy is to reduce the number of parts required in the assembly. Designing parts that are multifunctional can eliminate the need for additional components and assembly time. This streamlining of the design process results in lower costs and faster turnaround times.
Additionally, selecting cost-effective materials is a simple way to reduce expenses. For example, using aluminum instead of stainless steel for less demanding applications will reduce both material and machining costs.
Cost-Reduction Strategy | Benefit | Example |
---|---|---|
Minimize Machining Time | Reduces labor and tooling costs | Simple shapes and tool paths |
Eliminate Parts | Cuts down assembly and material costs | Multi-functional designs |
Material Selection | Reduces raw material and machining costs | Aluminum vs Stainless Steel |
6. How Does Tolerance Impact CNC Machining Design?
Tolerance plays a critical role in CNC machining design. But here’s the kicker… It’s not just about fitting parts together; it’s about ensuring they work perfectly. Tolerance refers to the allowable deviation from a nominal value, essentially defining how precise the finished part should be. Tight tolerance specifications demand higher machining precision, often increasing cost and time, whereas loose tolerances are generally easier and quicker to machine but may result in parts that don’t meet functional requirements.
The key is finding a balance. Tight tolerances can be necessary when parts need to fit together perfectly, such as in aerospace components. However, requiring overly tight tolerances for non-critical features leads to inefficiency. A good design will specify the necessary tolerances for each part based on the application, ensuring that you’re not over-engineering areas that don’t require such precision.
In contrast, loose tolerances can result in easy machining, but the risk is that they might not meet the mechanical performance requirements, such as in high-pressure or high-heat environments. For example, a part used in an automotive engine would require tight tolerances for key functional areas like engine fittings, but other, non-critical areas can afford more flexibility.
Why is Tolerance So Important?
Setting proper tolerances ensures parts fit together, function as intended, and don’t lead to rework or failure in critical applications. It’s essential to communicate these tolerances clearly in the design phase to avoid complications during production.
Tolerance Type | Precision Requirement | Cost and Time Impact | Example |
---|---|---|---|
Tight Tolerances | High | Increased cost/time | Aerospace components |
Loose Tolerances | Low | Lower cost/time | Non-critical components |
7. What is the Role of CAD Software in CNC Machining Design?
CAD software has revolutionized the world of CNC machining. What’s the real story? Without CAD software, it would be almost impossible to achieve the precision, efficiency, and repeatability that CNC machining demands. CAD (Computer-Aided Design) software enables designers to create detailed and accurate 2D or 3D models, which can then be converted into machine-readable instructions.
By using CAD software, designers can simulate the machining process and identify potential issues before the actual machining begins. This eliminates the risk of costly mistakes and design flaws that might only appear after production. For example, using CAD to visualize how the machine will move through the material helps to avoid errors such as tool collisions or inefficient cutting paths, ultimately saving both time and money.
CAD software also enables easier collaboration. Designers, engineers, and manufacturers can all work from the same digital files, ensuring consistency and accuracy across the team. Additionally, updates and changes to the design can be made quickly and efficiently, allowing for faster iterations and greater flexibility.
In terms of CNC programming, CAD files are used to generate toolpaths through CAM (Computer-Aided Manufacturing) software. This process automatically converts the design into the commands needed for CNC machines to execute the part.
CAD Software Benefit | Impact | Example |
---|---|---|
Simulates Machining | Helps identify errors early | Tool collision prevention |
Easier Collaboration | Ensures consistency across teams | Shared digital files |
Quick Iterations | Speeds up design adjustments | Fast prototyping |
8. How Can You Minimize Waste in CNC Machining Projects?
Minimizing waste is essential in any CNC machining project. This is where it gets interesting… By designing parts with material efficiency in mind, you can significantly reduce both waste and cost. Waste in CNC machining typically results from leftover material after machining, or from parts that are scrapped due to design issues.
A key strategy for minimizing waste is optimizing the material layout. This involves strategically placing parts on the raw material to ensure the least amount of unused space. A design with proper nesting takes advantage of the material’s full potential, leaving minimal offcuts that would otherwise go to waste.
Another strategy involves designing parts that require less machining time. For instance, incorporating features like undercuts or deep pockets into the design might require excessive cutting, leading to more scrap. By designing simpler parts with fewer intricate features, you reduce the chances of wasted material and tooling.
Furthermore, designing parts that are compatible with common material sizes also helps in reducing waste. Many CNC machines operate most efficiently with standard sheet sizes. Designing parts that fit within these parameters will allow you to use common materials without having to purchase specialized sizes.
Waste Reduction Strategy | Benefit | Example |
---|---|---|
Optimizing Material Layout | Reduces leftover material | Efficient nesting |
Simplified Design | Reduces machining complexity | Fewer intricate features |
Common Material Sizes | Decreases scrap material | Standard sheet dimensions |
9. What is the Importance of Part Orientation in CNC Machining?
Part orientation refers to the positioning of the part on the CNC machine relative to the tool path. But here’s the kicker… The way a part is oriented can significantly affect the quality, cost, and efficiency of machining. Proper orientation ensures that the tool can access the entire part without interference and minimizes machining errors.
Orientation impacts the surface finish of the part, as certain orientations may lead to more precise cuts or smoother finishes. For example, a part oriented in a way that allows the tool to approach the surface at a shallow angle may result in a finer, more accurate surface finish. In contrast, a less ideal orientation might result in tool marks or surface imperfections.
Additionally, the right part orientation can reduce the number of tool changes required, improving machining efficiency and reducing costs. By positioning parts in such a way that fewer setups are necessary, you can speed up the production process and save both time and money.
Finally, some designs may require multiple orientations to achieve different features, but it’s essential to minimize the number of changes to avoid errors or excessive tool wear.
Orientation Factor | Impact | Example |
---|---|---|
Tool Access | Affects surface finish and precision | Shallow angle for fine finishes |
Efficiency | Reduces setup time and tool changes | Single setup for multiple cuts |
Multiple Orientations | May increase machining time | Parts requiring multiple orientations |
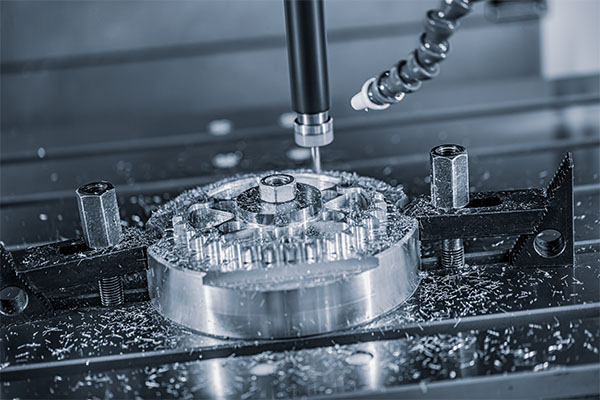
10. How Do You Ensure Your CNC Design is Machinable?
A key part of CNC machining design is ensuring that the design can actually be produced by the machine. What’s the deal? Machinability is the ease with which a material can be cut into a desired shape. Designs that are not machinable will lead to production delays, tooling issues, and poor-quality parts.
Start by ensuring that the design avoids sharp corners or tight radii that are difficult for CNC tools to reach. For example, sharp internal corners can be difficult for tools to machine without causing damage to the part or tool. Instead, rounding the corners or increasing the radius can reduce these risks and make the part easier to machine.
Another factor to consider is undercuts, which occur when a feature is hidden under another feature, making it difficult to machine. Always ensure that your design allows for adequate tool access. Additionally, providing adequate allowances for tool clearance ensures that the tools can effectively remove material and reach the desired part geometry.
Finally, communicate directly with the machinists. They can help identify potential issues before production starts and provide insights into making your design more machinable.
Machinability Factor | Impact | Example |
---|---|---|
Sharp Corners | Can damage tools or parts | Rounded corners for tool access |
Undercuts | Limits tool access and increases machining difficulty | Avoid complex undercuts |
Tool Clearance | Ensures effective material removal | Adequate space around features |
11. What Are the Key CNC Machining Processes You Should Know About?
CNC machining encompasses a variety of processes, each suitable for different types of parts and applications. Here’s the thing… Knowing which process to use for a given part is essential to ensuring cost-effective production and high-quality results.
One of the most common CNC machining processes is milling. Milling involves rotating a cutting tool against a part to remove material, and it’s used for creating complex shapes, holes, and features. It’s ideal for both 2D and 3D shapes and can be used on a wide range of materials.
Another key process is turning. Turning uses a rotating part and a stationary cutting tool to shape the part. It’s especially useful for producing cylindrical parts, such as shafts or fittings, with high precision. Turning also allows for the creation of internal features such as grooves or threads.
Drilling, while simple, is a fundamental process that’s often used in combination with milling or turning to create holes in the part. CNC drilling ensures precision and can be applied to a wide range of materials.
CNC Process | Best For | Example |
---|---|---|
Milling | Complex shapes, holes, and 3D features | Gearbox housing |
Turning | Cylindrical parts, shafts, and fittings | Engine components |
Drilling | Creating holes and internal features | Holes for fasteners |
12. How Do You Prepare Your Design for CNC Machining?
Once your design is finalized, the next step is preparing it for CNC machining. But wait, there’s more… The process of preparing your design involves converting it into machine-readable code that CNC machines can understand.
Start by converting your CAD model into a compatible file format, such as .STL or .STEP. These file types are universally recognized by CNC machines and will contain all the necessary geometric information needed for machining. Once the file is prepared, you need to ensure it’s free from any design errors, such as unclosed loops or incorrect dimensions, which can interfere with the machining process.
Next, you’ll need to choose the appropriate CNC machine for your project. Not all CNC machines are created equal—each is suited for different types of work. A CNC lathe might be required for turning parts, while a CNC mill is more suitable for complex 3D shapes.
Lastly, check the machine’s tool paths and set-up configurations to ensure that everything aligns with your design. This preparation step is crucial to avoiding errors during the machining process and ensuring that your part comes out as intended.
Preparation Step | Purpose | Example |
---|---|---|
CAD Conversion | Converts design into machine-readable format | .STL or .STEP files |
CNC Machine Selection | Ensures the right machine is used for the job | CNC lathe or CNC mill |
Tool Path Planning | Aligns machine tools with the design | Correct tool selection for machining |
13. What Role Does Finishing Play in CNC Machining Design?
Finishing plays a vital role in ensuring that the final product meets aesthetic, functional, and mechanical specifications. Here’s the kicker… Without proper finishing, even the most precise CNC machined parts can have a rough, unfinished look that affects their functionality.
There are several types of finishing processes used in CNC machining, including grinding, polishing, and anodizing. Grinding is used to remove material from the surface to smooth it out, while polishing provides a high-shine finish. For parts that require increased corrosion resistance, anodizing or coating processes may be used.
The finish you choose depends on both the functionality and appearance of the part. For instance, parts used in automotive applications may require a certain surface finish to ensure they perform well under stress. Aesthetic considerations, such as the finish for consumer goods or jewelry, may prioritize appearance over functionality.
Lastly, consider the machining cost when selecting a finish. Some finishes require additional steps, such as electroplating or coating, which can increase the cost of production. Ensure that the finish is essential for the part’s use and is appropriate for the material.
Finishing Type | Purpose | Example |
---|---|---|
Grinding | Removes surface imperfections | Smoothness of automotive parts |
Polishing | Provides a shiny surface finish | Consumer goods aesthetics |
Anodizing/Coating | Increases resistance to corrosion | Aerospace components |
14. How Do CNC Machining and Prototyping Work Together in Design?
Prototyping is an integral part of CNC machining design. What’s the real story? By creating prototypes before full-scale production, you can test the design, check for errors, and make adjustments before committing to mass production.
Prototyping allows you to see your design in 3D and identify any issues that might not be apparent in the CAD model. It’s a chance to evaluate the functionality, fit, and finish of the part before investing in expensive tooling or machining time.
In CNC machining, prototypes can be made using the same processes that will be used in full-scale production. This gives you an accurate representation of how the final product will behave, including material properties, tolerance requirements, and surface finishes. It’s also an opportunity to test the part in real-world conditions.
Once the prototype is tested and any necessary adjustments are made, the design can be finalized for full production. This iterative approach ensures a higher-quality final product and reduces the chances of costly mistakes in the production process.
Prototype Benefit | Impact | Example |
---|---|---|
Error Detection | Identifies potential design flaws | Test fit and function |
Real-world Testing | Verifies the part’s performance | Performance under stress |
Design Adjustments | Allows for changes before full production | Refined CAD model |
15. How Can You Improve Your CNC Machining Design Skills?
Becoming proficient at CNC machining design takes practice, knowledge, and continuous learning. But here’s the kicker… Even the most experienced designers can always improve their skills.
One way to enhance your design abilities is by keeping up with industry trends and technologies. New machining techniques, materials, and software tools are constantly emerging, and staying informed about these developments will give you a competitive edge.
Joining CNC machining communities or forums is another great way to learn. Sharing knowledge and learning from the experiences of others can help you discover new approaches and avoid common mistakes. Additionally, taking courses or certifications on CNC design and machining can solidify your skills and help you stay ahead of the curve.
Finally, practice makes perfect. The more you design, the better you’ll get at understanding the nuances of CNC machining and how to optimize designs for the process.
Improvement Strategy | Benefit | Example |
---|---|---|
Stay Informed | Keeps you up-to-date with industry trends | New machining software |
Join Communities | Learn from others’ experiences | CNC forums and webinars |
Practice and Train | Refines your design process | CNC design courses |
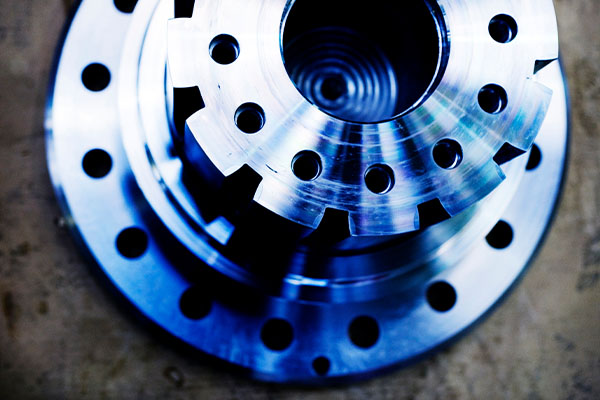
FAQ Section
Q1: What is CNC machining design?
CNC machining design refers to the process of creating a detailed digital model for a part that will be manufactured using CNC machines. This design ensures precision and efficiency during production.
Q2: How does material selection affect CNC machining?
Material selection impacts the machinability, cost, and durability of the final product. Choosing the right material ensures the part is functional and cost-effective.
Q3: What are the benefits of using CAD software in CNC design?
CAD software helps create accurate and detailed models, which can be directly translated into machine-readable files. It also allows for design modifications, error checking, and simulations before machining.
Q4: How can I avoid common design mistakes in CNC machining?
To avoid mistakes, simplify your design, choose the right material for the job, and set appropriate tolerances that balance precision with cost-effectiveness.
Q5: Why is it important to consider tolerance in CNC machining design?
Tolerance defines the permissible variations in the final dimensions of a part. Tight tolerances ensure high precision but can increase machining time and cost, while loose tolerances may compromise part functionality.