Introduction
CNC machining plays a pivotal role in the aerospace industry, helping manufacturers meet the rigorous demands for precision, reliability, and efficiency. It allows for the production of complex and durable parts that are essential for the safety and functionality of aircraft. As the aerospace sector continues to advance, CNC machining offers an innovative solution for creating high-performance components while reducing costs and improving turnaround times. In this article, we will explore the various ways CNC machining is used in aerospace parts production, highlighting its benefits, challenges, and future potential.
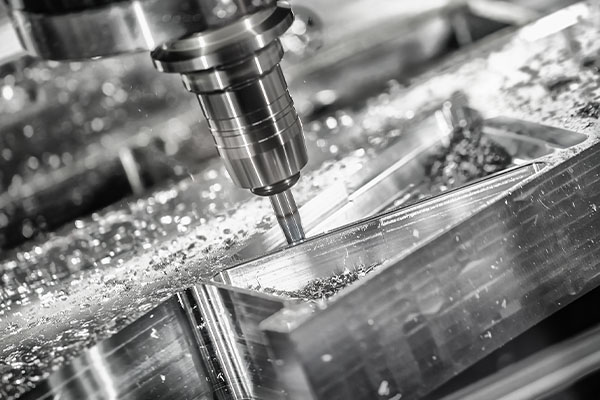
1. Importance of CNC Machining in Aerospace
Why CNC Machining is Critical for Aerospace Parts Production
In the aerospace industry, the importance of CNC machining cannot be overstated. Aerospace components are often complex, with intricate geometries and strict tolerance requirements. CNC machining is critical because it allows manufacturers to achieve the high precision and repeatability necessary for such parts. Whether it’s for structural elements like fuselages or critical engine components, the ability to produce parts that meet stringent specifications is paramount to ensuring safety and performance.
The precision and repeatability offered by CNC machining are unmatched in traditional methods. The aerospace industry demands parts that are not only accurate but also reliable over long periods of use. CNC machining ensures that every part produced is identical, eliminating the variability that can arise from human error in manual processes. This level of accuracy is essential, as even the smallest deviation can compromise the performance of an aircraft.
Moreover, CNC machining allows for rapid production and minimal waste. In a competitive industry like aerospace, time is of the essence, and CNC machines can produce parts much faster than traditional methods. This efficiency translates to cost savings for manufacturers, making CNC machining an attractive option for both large-scale production and specialized, custom parts.
2. Key Benefits of CNC Machining in Aerospace
Precision and Accuracy
One of the most significant advantages of CNC machining is its ability to deliver exceptional precision and accuracy. In aerospace parts production, tolerances are often as tight as a few microns. CNC machines are designed to meet these exacting standards, ensuring that every part produced is consistent in size, shape, and function. The use of sophisticated software and automated processes allows CNC machines to make thousands of identical parts without deviation.
Cost Efficiency and Reduced Waste
Another major benefit of CNC machining is its ability to reduce material waste. CNC machines are programmed to cut parts with minimal scrap, ensuring that materials are used efficiently. This not only helps lower the cost of production but also supports sustainability efforts within the aerospace industry. By reducing waste, CNC machining aligns with the industry’s growing focus on eco-friendly manufacturing practices.
Repeatability and Consistency
CNC machining excels at producing parts with high repeatability. Once a part design is finalized, CNC machines can reproduce it indefinitely with the same precision. This consistency is crucial in aerospace, where parts need to fit together perfectly to ensure the safety and integrity of the aircraft. The ability to create thousands of identical parts, with no variation, is a significant advantage for manufacturers producing components for airplanes, satellites, and other aerospace technologies.
3. Types of Aerospace Parts Made with CNC Machining
Structural Components
CNC machining is widely used in the production of structural components for aircraft, including fuselages, wings, and frames. These parts require both strength and lightness to withstand the demands of flight. CNC machining enables manufacturers to create complex structures with precise dimensions and optimal material distribution, ensuring that parts are both durable and lightweight. Using high-performance alloys, CNC machining produces parts that can withstand extreme conditions while maintaining high strength-to-weight ratios.
Engine Components
Aerospace engines are some of the most complex parts to manufacture, requiring both intricate designs and materials that can withstand extreme heat and pressure. CNC machining is essential for the production of engine components such as turbines, compressor blades, and housings. These components often require the use of advanced materials like titanium and high-strength alloys. CNC machines allow for the intricate shaping of these materials, ensuring that the components meet the performance standards required in aviation.
Landing Gear Components
The landing gear of an aircraft is another critical component produced using CNC machining. These parts must be incredibly strong and resilient, as they bear the weight of the entire aircraft during takeoff, landing, and while taxiing on the runway. CNC machining is capable of producing the intricate designs required for landing gear, ensuring that every part meets the exacting standards for strength and durability.
Interior Components
Aerospace interior components, such as seating elements, panels, and brackets, also benefit from CNC machining. These parts require both strength and aesthetic quality, as they must not only perform well but also provide comfort and safety to passengers. CNC machining offers the precision necessary to manufacture these parts with a perfect balance of strength, weight, and style.
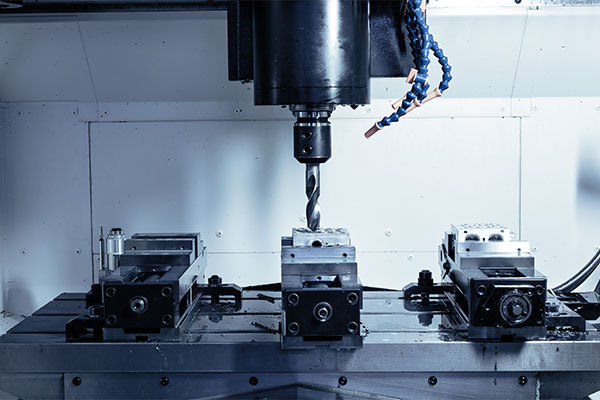
4. CNC Machining Processes for Aerospace
Milling
Milling is one of the most commonly used CNC processes in aerospace manufacturing. This process involves rotating a cutting tool to remove material from a workpiece. CNC milling machines are particularly effective at producing flat surfaces, slots, and complex geometries, which are common in aerospace parts. By using multi-axis CNC machines, manufacturers can create complex shapes with a high degree of accuracy.
Turning
Turning is another key process used in aerospace CNC machining. Turning machines work by rotating the workpiece while a stationary tool removes material. This process is ideal for producing cylindrical parts such as shafts, bushings, and engine components. CNC turning allows for tight tolerances and smooth finishes, ensuring that parts meet the performance requirements of the aerospace industry.
Grinding
For aerospace parts that require an ultra-fine finish, grinding is used to achieve a smooth surface. Grinding is often used for components like turbine blades and precision gears, where even a slight imperfection can compromise performance. CNC grinding machines are capable of achieving incredibly fine finishes, ensuring that parts meet the high standards for both function and appearance.
EDM (Electrical Discharge Machining)
EDM is a process used for producing complex shapes with high precision, especially for hard materials. This process uses electrical discharges to erode material from the workpiece. EDM is particularly useful for intricate aerospace parts, such as those with fine details or small, delicate features. The precision of EDM ensures that even the most complicated parts can be manufactured with high accuracy.
5. Materials Used in Aerospace CNC Machining
Aluminum Alloys
Aluminum alloys are a popular choice for aerospace components because of their combination of strength and light weight. CNC machining is highly effective at working with aluminum alloys, as they can be easily shaped and finished to precise specifications. The ability to machine these materials quickly and accurately makes aluminum alloys a preferred material for a wide range of aerospace parts.
Titanium Alloys
Titanium alloys are known for their strength, lightness, and resistance to high temperatures, making them ideal for use in aerospace applications. However, machining titanium can be challenging due to its toughness and tendency to wear tools quickly. CNC machines are designed to handle these materials efficiently, allowing manufacturers to produce titanium parts with high precision and minimal tool wear.
Steel and Stainless Steel
Steel and stainless steel are used in aerospace for parts that require exceptional strength and durability. CNC machining is critical for producing these materials into complex shapes and ensuring that the final products meet strict performance standards. The precision of CNC machining ensures that even the toughest steel parts are shaped accurately to the required specifications.
Composites and Other Materials
The aerospace industry is increasingly turning to composites such as carbon fiber, which provide excellent strength-to-weight ratios. CNC machining is versatile enough to handle these advanced materials, ensuring that parts maintain their structural integrity while remaining lightweight. CNC machines can easily adapt to different materials, making them ideal for producing composite parts and other specialized materials used in the aerospace sector.
6. Advanced CNC Technologies in Aerospace
Multi-Axis CNC Machines
Multi-axis CNC machines are among the most advanced tools in aerospace manufacturing. These machines have the ability to move a workpiece in multiple directions simultaneously, allowing for the production of highly complex parts with intricate geometries. Multi-axis CNC machines are particularly valuable in aerospace because they can handle parts that require multiple cuts from different angles, all in one setup. This reduces the need for retooling and increases production efficiency.
Automation and Integration
As the aerospace industry continues to innovate, automation is becoming increasingly important in CNC machining. Automated systems allow for the continuous production of parts, reducing the need for human intervention and ensuring consistent quality. Robotic arms and automated loading systems work alongside CNC machines to increase production speed and reduce costs. Integration with advanced software also enables real-time monitoring, further enhancing the efficiency of the machining process.
7. Design Considerations for CNC Machining in Aerospace
Design for Manufacturability (DFM)
In the aerospace industry, Design for Manufacturability (DFM) is a critical aspect of CNC machining. Engineers must design parts with the machining process in mind, ensuring that components are easy to manufacture while maintaining the required strength and precision. DFM principles help reduce manufacturing costs and lead times by optimizing the design to align with the capabilities of CNC machines.
Tolerance and Precision in Design
Aerospace parts often require extremely tight tolerances to ensure proper fit and function. Designing parts with the necessary tolerance specifications is essential for the success of CNC machining. Engineers must account for factors such as material behavior and machine limitations when designing parts, ensuring that the final product meets the necessary performance standards.
8. Challenges of CNC Machining in Aerospace Parts Production
Material Hardness and Complexity
One of the primary challenges in aerospace CNC machining is working with tough materials like titanium, which can be difficult to machine due to its hardness. CNC machines are designed to handle these challenges, but the process can still be time-consuming and costly. Manufacturers must carefully select the right tools and techniques to ensure that these materials are machined accurately without excessive tool wear.
Cost of High-End CNC Machines
The investment in high-precision CNC machines can be substantial, and for smaller aerospace companies, the upfront cost can be a barrier. However, the benefits of using CNC machining, such as reduced labor costs and increased production efficiency, often outweigh the initial investment. Many aerospace manufacturers opt for leasing or outsourcing machining to reduce capital expenditure while still benefiting from CNC technology.
Machining Complex Geometries
CNC machining is incredibly effective at producing complex geometries, but there are still challenges involved, particularly with parts that have intricate internal features or non-standard shapes. Multi-axis CNC machines can handle most complex parts, but the programming and setup for these parts can be time-consuming. Manufacturers must balance the complexity of the design with the capabilities of the machine to ensure efficient production.
9. Quality Control in CNC Machining for Aerospace
Inspection and Testing
Quality control is crucial in aerospace manufacturing. After CNC machining, parts undergo rigorous inspection and testing to ensure they meet the required specifications. Methods such as coordinate measuring machines (CMM), ultrasonic testing, and X-ray inspections are used to identify any defects or inconsistencies in the parts. These tests ensure that the final product is safe and reliable for use in the aerospace industry.
Certifications and Standards
Aerospace manufacturers must adhere to strict certifications and standards to ensure the quality and safety of their parts. Certifications like AS9100 ensure that manufacturers follow the highest quality standards, including those related to CNC machining. Compliance with these standards is essential for manufacturers who wish to work with aerospace companies and produce parts that meet regulatory requirements.
10. Future Trends in CNC Machining for Aerospace
Additive Manufacturing Integration
As additive manufacturing, or 3D printing, continues to advance, it is being integrated with CNC machining to create hybrid manufacturing processes. This combination allows for faster prototyping and the production of parts with complex geometries that may be difficult to achieve with traditional methods. CNC machines are being adapted to handle 3D-printed components, further increasing the versatility and capabilities of aerospace manufacturing.
AI and Machine Learning in CNC
The introduction of AI and machine learning in CNC machining is changing the way aerospace parts are produced. These technologies help optimize machining processes, predict tool wear, and monitor machine performance in real-time. By integrating AI, CNC machining becomes more efficient, reducing downtime and improving production quality. AI and machine learning also help with predictive maintenance, allowing manufacturers to schedule repairs before problems arise.
Sustainability in Aerospace CNC
The aerospace industry is increasingly focused on sustainability, and CNC machining contributes to this effort by minimizing material waste and energy consumption. Advances in machining technology are leading to more efficient processes that reduce the carbon footprint of aerospace manufacturing. Additionally, the use of recyclable materials in CNC machining supports the industry’s commitment to environmental responsibility.
11. The Role of CNC Machining in Custom Aerospace Parts Production
OEM and Customization
CNC machining plays a critical role in producing custom aerospace parts. Many aerospace manufacturers require original equipment manufacturer (OEM) parts that are tailored to specific aircraft models. CNC machines are incredibly versatile and can produce these parts with high precision, allowing for the customization of components to meet the unique specifications of each aircraft.
12. CNC Machining for Aerospace Prototyping
Rapid Prototyping
Prototyping is an essential part of aerospace manufacturing, and CNC machining is ideal for creating rapid prototypes. Engineers can quickly create test parts to evaluate designs, allowing for adjustments and improvements before full-scale production begins. This saves time and reduces the cost of making mistakes during production.
Prototyping Benefits
CNC machining also allows for faster turnaround times in prototyping, enabling manufacturers to respond quickly to changing design requirements. The precision of CNC machining ensures that prototypes are as close to the final product as possible, reducing the risk of issues during the production phase.
13. CNC Machining vs. Traditional Machining in Aerospace
Comparing the Speed and Precision
Compared to traditional machining methods, CNC machining is significantly faster and more precise. CNC machines can work continuously without the need for human intervention, reducing production times and increasing throughput. This is particularly important in aerospace, where precision and efficiency are essential for maintaining safety standards.
Cost and Production Efficiency
CNC machining is more cost-effective than traditional machining methods due to its automation and efficiency. Traditional machining requires more manual labor and time-consuming processes, which can lead to higher costs. CNC machining helps reduce labor costs, increases production efficiency, and ensures consistent quality across large production runs.
14. Case Studies of CNC Machining in Aerospace
Real-World Examples
Several aerospace companies have successfully implemented CNC machining to manufacture critical components. For example, Lockheed Martin uses CNC machining to produce high-precision parts for its aircraft and satellites. CNC machines are used to manufacture components ranging from turbine blades to structural elements, ensuring that the parts meet the strict requirements of the aerospace industry.
15. Conclusion
Summary of Key Points
CNC machining plays a crucial role in aerospace parts production, offering benefits such as precision, efficiency, and reduced material waste. As the aerospace industry continues to evolve, CNC machining will remain a vital technology for producing high-quality parts that meet stringent safety and performance standards.
Looking Ahead
The future of CNC machining in aerospace looks promising, with innovations like additive manufacturing integration and AI-driven optimization continuing to enhance the process. As technology advances, CNC machining will become even more integral to the production of cutting-edge aerospace components.
Call to Action
For aerospace manufacturers looking to improve their production processes, CNC machining offers an innovative solution. Consider investing in CNC machining to achieve faster, more precise, and cost-effective production of aerospace components.

FAQ Section
- What are the most common aerospace parts made using CNC machining?
CNC machining is commonly used to create aerospace components such as aircraft structural parts (fuselages, wings, and frames), engine components (turbines, compressor blades, and housings), landing gear parts, and interior components (seating elements, panels, and brackets). These parts often require high precision and durability, which CNC machining provides. - How does CNC machining improve the quality of aerospace components?
CNC machining improves quality by delivering extreme precision and repeatability. Every part produced is identical, ensuring tight tolerances and uniformity. CNC machines also use advanced materials and cutting techniques that prevent defects, improving the overall functionality and reliability of aerospace components. - What materials are most commonly used in CNC machining for aerospace parts?
The aerospace industry typically uses aluminum alloys, titanium alloys, steel, stainless steel, and composites like carbon fiber. These materials are chosen for their strength, durability, and lightness, and CNC machining can handle these tough materials with precision, even for complex geometries. - Can CNC machining handle all types of aerospace materials?
CNC machining can handle a wide range of materials, including metals like titanium, steel, and aluminum, as well as composite materials like carbon fiber. However, certain materials, especially harder ones like titanium, may require specialized tools and techniques to ensure efficiency and tool longevity. - What are the challenges of CNC machining in aerospace production?
Challenges in aerospace CNC machining include working with tough materials like titanium, ensuring precise tolerances, and managing the high upfront costs of advanced CNC equipment. Additionally, machining complex geometries and maintaining high efficiency in production can pose challenges for manufacturers. - How does CNC machining contribute to reducing production costs in aerospace?
CNC machining reduces production costs by minimizing material waste, improving production speed, and ensuring high precision. The automation of processes reduces labor costs and ensures consistent quality, preventing costly mistakes and rework. CNC machines also reduce the need for manual setup and tooling, further lowering costs. - What certifications do aerospace manufacturers need for CNC machining?
Aerospace manufacturers must comply with certifications such as AS9100, which specifies quality management standards for the aerospace industry. This certification ensures that CNC machining operations meet the required safety, reliability, and quality standards necessary for aerospace components. - Is CNC machining more efficient than traditional machining for aerospace parts?
Yes, CNC machining is typically more efficient than traditional machining. It offers faster production speeds, greater precision, and higher consistency in the final product. CNC machines can also operate continuously, reducing the overall production time compared to manual methods that require more setup and human involvement. - What is the role of automation in CNC machining for aerospace?
Automation plays a significant role in improving the efficiency and reliability of CNC machining for aerospace. Automated systems, including robotic arms and integrated software, help streamline production by reducing the need for manual intervention. Automation also ensures consistent quality, minimizes errors, and allows for faster production cycles. - How does CNC machining support aerospace prototyping and custom parts production?
CNC machining is highly effective for rapid prototyping in aerospace, allowing designers to quickly test new designs before committing to full-scale production. The precision and versatility of CNC machines also support the customization of parts, ensuring that manufacturers can meet the specific needs of different aerospace projects and clients, from one-off prototypes to large production runs.