giriiş
5 Axis CNC machining has revolutionized the way manufacturers approach precision and complexity in part production. As industries evolve, so does the need for machinery that can handle increasingly sophisticated designs with accuracy. For anyone involved in manufacturing, understanding 5-axis CNC machining is essential in staying competitive. In this guide, we will explore what 5-axis CNC machining is, how it works, and why it’s becoming indispensable in modern production. Whether you’re in aerospace, automotive, or medical device manufacturing, 5-axis CNC machining can significantly impact your process efficiency and product quality.

CNC İşleme Nedir?
Definition of CNC Machining
CNC machining is a method used in manufacturing to control machine tools via computer programming. CNC, which stands for Computer Numerical Control, allows machines to perform tasks like cutting, drilling, milling, and shaping materials based on instructions from a computer program. This method provides precision and repeatability, making it ideal for mass production and creating complex parts.
Basic Types of CNC Machines
There are several types of CNC machines used in modern manufacturing, with each being suitable for different purposes. The most common are the 3-axis, 4-axis, and 5-axis machines. A 3-axis machine moves the tool along the X, Y, and Z axes. A 4-axis machine adds rotation along one axis to the basic movements. In contrast, a 5-axis machine incorporates two additional axes that allow the tool to move around a rotating workpiece, providing greater flexibility and precision.
Understanding the Axis in CNC Machining
What Does ‘Axis’ Mean in CNC?
In CNC machining, “axis” refers to the directions in which a tool or the workpiece can move. These axes are typically labeled X, Y, and Z. The X and Y axes control the horizontal movements, while the Z axis controls the vertical movement. In the simplest form, a 3-axis machine can move along these three planes to cut or shape a workpiece.
Difference Between 3, 4, and 5 Axis Machines
The difference between a 3-axis and a 5-axis machine lies in the level of control over the workpiece. While a 3-axis machine can only move along three basic directions, a 5-axis machine can manipulate the tool in more complex ways by adding two rotational axes. This allows the machine to reach areas of the part that would be impossible or highly inefficient with a 3-axis machine. The addition of these rotational axes makes 5-axis CNC machines ideal for intricate and detailed machining, providing higher precision and reducing the need for multiple setups.
How Does 5 Axis CNC Machining Work?
The Movement of the 5-Axis CNC Machine
5-axis CNC machines use five axes to control both the position and the orientation of the tool and the workpiece. Typically, three of the axes are linear (X, Y, and Z), while the other two are rotary. The rotary axes, often denoted as A and B, allow for tilting and rotating of the workpiece, which helps the tool access all areas of the part. This flexibility in movement significantly enhances the machine’s ability to handle complex shapes and geometries with high precision.
How 5-Axis Machining Improves Precision
The key advantage of 5-axis machining is its ability to produce more accurate parts than 3-axis machines. With the additional axes, parts can be cut from multiple angles in a single setup, reducing the risk of error or misalignment. This level of precision is especially important in industries like aerospace, where even the smallest error can be catastrophic. The improved accessibility provided by 5-axis machines also ensures smoother surfaces and better finishes, even on intricate or complex designs.
Key Components of a 5 Axis CNC Machine
The Machine Table and Tool Holders
A 5-axis CNC machine features a table that holds the workpiece securely in place while it’s being machined. This table is usually mounted on a rotating mechanism that allows the part to rotate for access to different faces. The tool holders, which are integral to the process, hold the cutting tools in place while they make precise cuts. Together, these components work to allow the machine to manipulate the workpiece from multiple angles, ensuring that all aspects of the part are machined accurately.
Rotary Axes and Tilting Mechanism
The rotary axes (often labeled A and B) are crucial in a 5-axis machine, as they enable the part to be tilted or rotated, giving the cutting tool access to hard-to-reach areas. The tilting mechanism, in particular, helps achieve greater flexibility and precision, allowing the tool to approach the workpiece from any direction. This additional range of motion enhances the machine’s ability to produce highly detailed parts with complex geometries, making it indispensable in industries requiring high precision.
Benefits of 5 Axis CNC Machining
Enhanced Precision and Complex Geometries
One of the biggest advantages of 5-axis CNC machining is its ability to produce complex parts with high precision. By moving the cutting tool along five different axes, the machine can work on all surfaces of a part, including those that are difficult to reach with traditional machines. This allows for more detailed designs and more intricate geometries, which would be impossible to achieve with a 3-axis machine.
Reduction in Production Time
İşte anlaşma: By using a 5-axis CNC machine, manufacturers can significantly reduce the amount of time needed to produce complex parts. This is because the workpiece can be machined from multiple angles without needing to be repositioned, reducing the need for multiple setups. In traditional machining, a part might need to be moved between several machines to achieve the same result. With 5-axis machining, all the necessary cuts can be made in one go, saving time and effort.
Cost-Efficiency for Complex Parts
Another advantage of 5-axis machining is its cost-efficiency, especially for producing parts with complex shapes. Traditional machining often requires multiple tools and setups, which can increase both the time and the cost of production. However, with a 5-axis machine, fewer setups and tools are required, lowering production costs while maintaining high levels of accuracy.
Types of 5 Axis CNC Machines
Trunnion Style Machines
Trunnion-style 5-axis CNC machines are one of the most common types of 5-axis machines. These machines feature a rotating table that tilts, allowing for precise control over the workpiece. The trunnion-style machine is particularly effective for parts that need to be rotated along two axes for complex cutting. These machines are ideal for industries where large, heavy parts need to be worked on from multiple angles.
Rotary Table Machines
Merak ediyor olabilirsiniz: What makes rotary table machines different from trunnion-style machines? Rotary table machines use a rotating platform to achieve the fifth axis movement. This type of machine offers more flexibility for parts that require rotation around a fixed axis, making it ideal for certain types of parts and industries. While rotary tables can provide similar capabilities to trunnion-style machines, they differ in their design and specific application uses.
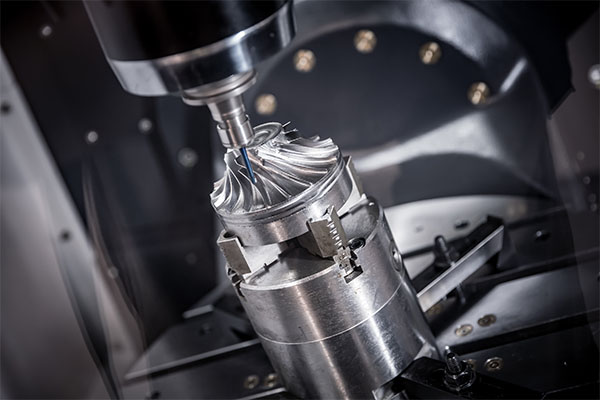
Applications of 5 Axis CNC Machining
Aerospace Industry
The aerospace industry relies heavily on 5-axis CNC machining for producing intricate and highly precise components. Parts such as engine components, turbine blades, and aircraft structural components require the accuracy that only 5-axis machining can provide. With the ability to work on all surfaces in one setup, these machines ensure the production of parts that meet strict aerospace standards for performance and safety.
Automotive Parts
In the automotive industry, 5-axis CNC machining is used to produce complex parts such as engine blocks, transmission components, and custom tooling. The ability to create intricate parts with tight tolerances is essential in automotive manufacturing, where precision and quality are paramount. 5-axis machines help streamline the production process while reducing the need for manual labor.
Medical Devices
Here’s the catch: The medical device industry requires extremely high precision to ensure the safety and effectiveness of its products. Parts such as surgical instruments, implants, and other medical devices benefit from 5-axis machining’s ability to produce fine details and complex geometries. With 5-axis CNC machining, manufacturers can create components that are not only functional but also meet stringent regulatory requirements.
Other Industries Using 5 Axis CNC Machining
Beyond aerospace, automotive, and medical devices, many other industries benefit from 5-axis CNC machining. These include electronics, consumer goods, energy, and more. Essentially, any industry that requires high-precision parts or complex geometries can take advantage of 5-axis CNC machining to improve their manufacturing processes.
Common Materials Used in 5 Axis CNC Machining
Metals (Aluminum, Titanium, Steel, etc.)
Metals are among the most common materials used in 5-axis CNC machining. Aluminum, titanium, steel, and other metals can be easily machined to produce durable parts. These materials are often used in industries like aerospace and automotive, where strength and precision are crucial.
Plastics and Composites
While metals are often the go-to for many applications, plastics and composites also benefit from 5-axis CNC machining. Materials like carbon fiber composites, reinforced plastics, and other advanced polymers are increasingly being used in industries like aerospace and medical device manufacturing. 5-axis machining allows for the production of parts with complex shapes that can withstand the demands of these industries.
The Process of Setting Up a 5 Axis CNC Machine
Step-by-Step Setup Process
Setting up a 5-axis CNC machine involves several steps, including positioning the workpiece, selecting the appropriate tool, and programming the machine. İşte anlaşma: The machine must be calibrated to ensure that the tool is aligned correctly with the workpiece. Once everything is set up, the program is loaded into the machine, and the operator can begin the machining process. Proper setup is crucial to ensure that the machine operates efficiently and produces high-quality parts.
Common Setup Challenges
While setting up a 5-axis CNC machine can seem straightforward, there are several challenges that operators may face. These include aligning the workpiece accurately, selecting the correct tool for the job, and ensuring that the machine’s software is programmed properly. However, with proper training and experience, these challenges can be overcome to achieve optimal results.
How 5 Axis CNC Machining Improves Manufacturing Efficiency
Reducing the Need for Multiple Tools and Setups
5-axis CNC machining greatly improves manufacturing efficiency by reducing the need for multiple tools and setups. Merak ediyor olabilirsiniz how this is possible. By enabling the workpiece to rotate and tilt, 5-axis machines can access multiple faces of the part in a single setup. This eliminates the need for repositioning and reduces setup time, ultimately streamlining the entire production process.
Minimizing Errors and Rework
One of the main benefits of 5-axis CNC machining is its ability to minimize errors. With fewer setups and more precise tool positioning, the risk of mistakes during the machining process is greatly reduced. This means fewer chances for rework, which saves both time and money. The accuracy and repeatability of 5-axis machines also contribute to a higher level of consistency across parts.
5 Axis CNC Machining vs. Traditional Machining
Comparing Cost and Time Efficiency
When comparing 5-axis CNC machining to traditional machining methods, there are significant differences in cost and time efficiency. Traditional methods may require multiple tools and setups to produce a complex part, increasing the overall cost and production time. But here’s the catch: With 5-axis CNC machines, all necessary cuts can be made in one go, reducing both time and cost.
Precision and Complexities in Design
In terms of precision and design complexity, 5-axis CNC machining offers clear advantages. Traditional machines are limited in their ability to handle intricate geometries, whereas 5-axis machines can handle these with ease. The ability to reach all areas of the part, including those that are difficult to access, makes 5-axis CNC machining ideal for producing complex designs with tight tolerances.
Programming and Software for 5 Axis CNC Machining
The Role of CAM Software in 5 Axis CNC
İşte anlaşma: Programming a 5-axis CNC machine requires specialized software known as Computer-Aided Manufacturing (CAM) software. This software helps create the instructions that tell the machine how to move and operate. CAM software is essential for optimizing the machining process, ensuring that the machine runs smoothly and produces the desired results.
Challenges in Programming 5 Axis CNC Machines
Programming a 5-axis CNC machine can be challenging due to the complexity of the machine’s movements. Unlike traditional machines, which only operate on three axes, 5-axis machines require more advanced programming techniques to ensure that the tool moves in the correct directions. However, with modern software and tools, these challenges can be addressed effectively.
Safety Considerations in 5 Axis CNC Machining
Safety Features of 5 Axis CNC Machines
5-axis CNC machines are equipped with numerous safety features to ensure safe operation. These include emergency stop buttons, sensors to detect errors or malfunctions, and automatic tool changers to minimize human interaction with the machine. These safety features help reduce the risk of accidents and ensure that the machine runs efficiently.
Best Practices for Safe Operation
To ensure safe operation, it is important for operators to follow best practices, such as wearing protective gear, keeping the work area clean, and following the machine’s operational guidelines. Training and certification programs are also essential to ensure that operators are familiar with the machine’s capabilities and limitations.
Future Trends in 5 Axis CNC Machining
Advancements in Technology
The future of 5-axis CNC machining is bright, with new technological advancements continually improving the efficiency and capabilities of these machines. Merak ediyor olabilirsiniz what’s next. Innovations such as artificial intelligence (AI) integration and machine learning algorithms are set to further optimize the machining process, making machines smarter and more adaptable to complex tasks.
The Role of Automation in 5 Axis Machining
Automation is another key trend shaping the future of 5-axis CNC machining. As automation continues to grow, we can expect machines to become more self-sufficient, reducing the need for manual intervention. This will not only increase production efficiency but also reduce the potential for human error.
Çözüm
5-axis CNC machining is a game-changer in the world of manufacturing. Its ability to produce precise and complex parts with fewer setups has made it an invaluable tool in industries like aerospace, automotive, and medical device manufacturing. As technology continues to evolve, 5-axis CNC machines will only become more efficient and capable, offering even greater precision and cost savings. If you’re looking to take your manufacturing process to the next level, investing in 5-axis CNC machining could be the key to your success.
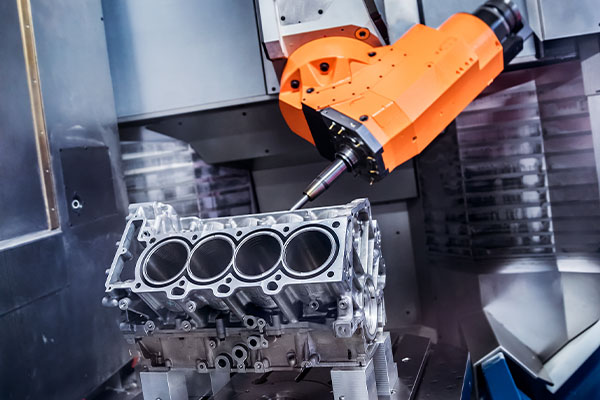
SSS Bölümü
- What is the main difference between 3-axis and 5-axis CNC machining?
The main difference between 3-axis and 5-axis CNC machining lies in the number of axes that control the tool’s movement. In 3-axis CNC machining, the machine moves the cutting tool along the X, Y, and Z axes, which correspond to horizontal, vertical, and depth movements. This is suitable for parts that only require basic cuts and shapes. In contrast, 5-axis CNC machining adds two additional rotational axes, allowing the tool to rotate around the workpiece, making it possible to access all sides of the part. This enables more complex geometries, higher precision, and reduced setup time compared to 3-axis machines, making 5-axis machines ideal for intricate and detailed parts.
- How much more expensive is a 5-axis CNC machine compared to 3-axis machines?
5-axis CNC machines are typically more expensive than 3-axis machines due to their added capabilities and complexity. The price difference can vary significantly depending on the machine’s size, brand, and additional features. While a basic 3-axis machine might cost anywhere from $20,000 to $100,000, 5-axis CNC machines can range from $100,000 to over $500,000 for high-end models. The increased cost is offset by the machine’s ability to handle more complex parts in fewer setups, which ultimately leads to lower operational costs in certain industries. The investment in a 5-axis machine can be worth it for manufacturers who regularly produce intricate and high-precision components.
- Can a 5-axis CNC machine handle all types of materials?
Yes, 5-axis CNC machines can handle a wide variety of materials, including metals (such as aluminum, steel, and titanium), plastics, composites, and more. The versatility of 5-axis machines allows them to work with materials that range from soft plastics to tough, high-strength metals. In industries like aerospace and automotive, where materials like titanium and specialized alloys are common, 5-axis CNC machines are particularly useful because they can handle these tough materials while maintaining high precision. The specific type of material, however, may require different tools or settings to optimize the machining process.
- How long does it take to set up a 5-axis CNC machine for production?
The time it takes to set up a 5-axis CNC machine can vary depending on the complexity of the part, the type of machine, and the experience of the operator. Typically, setting up a 5-axis CNC machine for production can take anywhere from a few hours to a full day. This process involves tasks such as aligning the workpiece, selecting the appropriate tools, programming the machine, and performing test runs to ensure accuracy. More complex parts that require precise tolerances or intricate geometries may take longer to set up. However, the ability of 5-axis machines to complete complex tasks in one setup often saves time in the long run by eliminating the need for multiple machine setups.
- What industries benefit the most from 5-axis CNC machining?
5-axis CNC machining is particularly beneficial in industries that require high precision and the ability to work with complex geometries. These industries include aerospace, automotive, medical devices, and energy. In aerospace, for example, 5-axis machines are used to create intricate turbine blades and other components that require high levels of accuracy. The automotive industry benefits from 5-axis machining when creating parts like engine blocks, transmission components, and custom tooling. In medical device manufacturing, 5-axis CNC machining is essential for producing surgical instruments and implants with tight tolerances. Other industries, such as electronics, defense, and consumer goods, also use 5-axis machining for high-quality and complex parts.
- What are the common mistakes made when programming a 5-axis CNC machine?
When programming a 5-axis CNC machine, common mistakes include improper tool selection, incorrect tool paths, and misalignment of the workpiece. Since 5-axis machines operate with additional rotational axes, errors can occur if the machine is not programmed to handle these movements correctly. One of the biggest challenges is ensuring that the cutting tool reaches all areas of the workpiece without causing interference or collisions. Another common mistake is failing to optimize the machining process for the specific material being used, which can result in poor surface finish or tool wear. To avoid these issues, it’s important to use reliable CAM (Computer-Aided Manufacturing) software and thoroughly test the program before starting production.
- Are there any limitations to 5-axis CNC machining?
While 5-axis CNC machining offers many advantages, there are some limitations. The complexity of the machine’s operation and programming can make it difficult for inexperienced operators to use effectively. Additionally, the initial cost of 5-axis CNC machines can be prohibitive for smaller manufacturers or businesses just starting out. Maintenance costs for 5-axis machines can also be higher than for simpler machines, as these machines have more moving parts and require specialized attention. Lastly, despite their versatility, 5-axis machines may not be the best choice for every job. For certain simple parts, a 3-axis machine may be more efficient and cost-effective. However, for complex, high-precision parts, the benefits of 5-axis machining outweigh the limitations.