giriiş
Aluminum CNC machining plays a crucial role in modern manufacturing, offering precision, efficiency, and versatility. Whether you’re in the aerospace, automotive, or electronics industry, understanding the ins and outs of aluminum CNC machining can significantly impact the quality and cost-effectiveness of your projects. In this comprehensive guide, we’ll explore everything you need to know, from the basics of CNC machining to advanced techniques for achieving high-quality aluminum parts. If you’ve ever wondered how aluminum components are made with such precision, this article is for you. Let’s dive in!
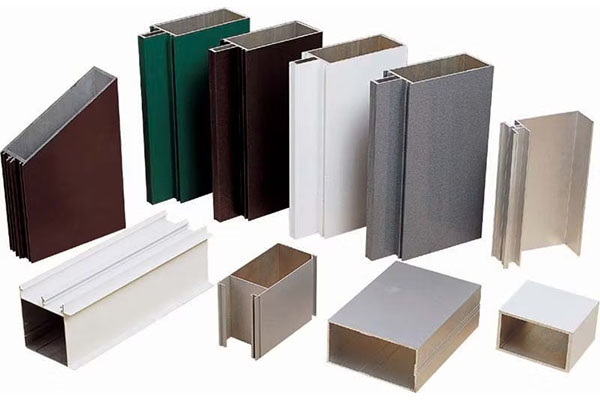
1. CNC İşleme Nedir?
CNC machining, or Computer Numerical Control machining, is a process where computers are used to control machines that cut, drill, and shape materials with high precision. Unlike traditional machining, which relies on manual control, CNC machining automates the entire process, offering enhanced repeatability and accuracy. The machines are programmed with specific instructions, such as tool paths and movement speeds, ensuring that each part is made consistently to the exact specifications.
The CNC machine operates using a pre-programmed computer code, ensuring minimal human intervention during the production process. This allows for intricate and detailed machining of aluminum parts, creating complex shapes that would be challenging to achieve with manual methods. CNC machines can work with a wide variety of materials, including metals, plastics, and composites. However, aluminum is one of the most popular materials used due to its favorable properties, such as lightness, durability, and machinability.
İşte anlaşma: CNC machining allows manufacturers to achieve high precision and efficiency, reducing waste and speeding up production times. Whether you’re working on small batches or mass production, CNC machining delivers results with a level of consistency and accuracy that manual methods simply can’t match. It is the ideal choice for industries that require high-quality, complex parts at scale.
2. Why Choose Aluminum for CNC Machining?
Aluminum stands out as one of the most commonly used materials in CNC machining due to its unique combination of properties. Aluminum is lightweight, corrosion-resistant, and easy to machine, making it perfect for various industries, including automotive, aerospace, and medical device manufacturing.
The low density of aluminum means it is lighter than many other metals, which makes it particularly useful in industries where weight reduction is a priority, such as aerospace and automotive manufacturing. Aluminum also has a high strength-to-weight ratio, offering durability while keeping the weight of the components low.
Another significant advantage of aluminum is its resistance to corrosion. This makes it an excellent choice for outdoor applications or any part exposed to the elements. Additionally, aluminum has a good thermal and electrical conductivity, which makes it useful in electronics and heat exchange systems. It is also relatively easy to machine, thanks to its softness compared to other metals like steel, which allows for smoother, faster cuts and longer tool life.
Merak ediyor olabilirsiniz why aluminum is so popular in CNC machining. The answer lies in its versatility and balance of strength, weight, and machinability, making it ideal for a wide range of applications.
3. Types of Aluminum Alloys Used in CNC Machining
Aluminum alloys come in various grades, each with unique characteristics suited to different machining applications. Some of the most common aluminum alloys used in CNC machining include 6061, 7075, and 2024. Each of these alloys has distinct properties that make them ideal for specific uses.
6061 Aluminum Alloy: This is one of the most commonly used alloys in CNC machining. It offers excellent corrosion resistance, good weldability, and ease of machining. It is often used in aerospace, automotive, and construction industries.
7075 Aluminum Alloy: Known for its high strength and toughness, 7075 is a preferred choice for applications where strength is crucial. However, it is more challenging to machine than 6061 due to its higher strength. It is commonly used in aircraft, military, and marine applications.
2024 Aluminum Alloy: This alloy is known for its excellent fatigue resistance and high strength. It is often used in applications where strength is critical, such as in the construction of airplanes and military vehicles. However, it is more difficult to machine due to its hardness.
İşte anlaşma: The choice of aluminum alloy depends on the specific requirements of the project, such as strength, machinability, and corrosion resistance. Understanding the characteristics of each alloy can help manufacturers select the best material for their CNC machining needs.
4. The CNC Machining Process for Aluminum
The CNC machining process for aluminum involves a series of steps, each essential for producing the final part with precision. The first step in the CNC machining process is to design the part using CAD (Computer-Aided Design) software, which creates a digital model of the part. This model is then converted into machine code that directs the CNC machine’s movements.
Once the program is created, the aluminum material is placed on the CNC machine’s worktable, and the machine begins the machining process. The most common operations used in aluminum CNC machining include milling, turning, drilling, and boring. Milling is typically used to remove material from the surface of the aluminum, while turning is used for cylindrical parts.
Merak ediyor olabilirsiniz what makes the CNC machining process so efficient. The answer lies in the ability to automate and control every aspect of the process. This ensures high precision, minimal human error, and the ability to produce complex shapes with ease.
5. Key Benefits of Aluminum CNC Machining
There are several advantages to using CNC machining for aluminum parts. First and foremost, CNC machining delivers high precision and repeatability. This is crucial for industries where the parts must meet tight tolerances and high standards. Whether you’re producing a small batch of parts or mass-producing components, CNC machines ensure that each part is identical, with minimal variations between them.
Another significant benefit of aluminum CNC machining is its cost-effectiveness. Aluminum is relatively inexpensive compared to other metals, and CNC machining can produce parts quickly and efficiently. This means lower production costs for manufacturers, especially when producing large quantities of parts.
Additionally, CNC machining can create complex shapes that would be difficult or impossible to achieve with traditional methods. The versatility of CNC machines allows manufacturers to produce intricate designs with ease, offering a high degree of flexibility in terms of design.
İşte anlaşma: CNC machining offers high precision, speed, and cost-effectiveness, making it the ideal choice for producing high-quality aluminum parts across various industries.
6. Challenges in Aluminum CNC Machining
Despite the many benefits, there are some challenges associated with aluminum CNC machining. One of the main issues is tool wear, especially when machining tougher alloys like 7075. The hardness of the material can cause tools to wear out more quickly, leading to increased maintenance costs and downtime.
Another challenge is thermal expansion. As aluminum heats up during the machining process, it expands, which can affect the accuracy of the final part. Effective cooling and proper tool selection are essential to manage heat buildup and ensure the precision of the parts.
Finally, achieving the desired surface finish can be challenging, especially when dealing with harder aluminum alloys. The surface finish is critical in many applications, particularly in industries like aerospace and medical manufacturing, where high standards are required.
Merak ediyor olabilirsiniz how these challenges are managed. With proper machine settings, high-quality tools, and efficient cooling systems, many of these challenges can be mitigated, ensuring that aluminum CNC machining remains a reliable and effective process.
7. Choosing the Right CNC Machine for Aluminum Machining
When selecting a CNC machine for aluminum machining, several factors must be considered. The type of CNC machine (milling machine, lathe, or router) will depend on the complexity and shape of the parts being produced. For example, a CNC milling machine is ideal for creating flat or contoured surfaces, while a lathe is used for cylindrical parts.
The size of the machine is another important consideration. The machine must be large enough to accommodate the aluminum workpiece, especially if you’re working with large or complex parts. The spindle speed and feed rate are also critical factors that affect the efficiency and quality of the machining process.
İşte anlaşma: The right CNC machine for aluminum machining should be chosen based on the specific requirements of the project, such as part size, complexity, and material type. With the proper machine, manufacturers can achieve high precision and optimize their production process.
8. Aluminum CNC Machining vs. Other Materials
When compared to other materials like steel, plastics, or titanium, aluminum has several distinct advantages. Aluminum is much lighter than steel, making it ideal for industries where weight is a concern, such as aerospace and automotive manufacturing. It also offers better corrosion resistance than steel, which makes it a popular choice for outdoor applications.
On the other hand, steel offers higher strength, especially in its alloyed forms, and is preferred for applications requiring higher tensile strength. Titanium, while stronger and lighter than steel, is much more expensive and harder to machine. Plastics, while easy to machine, lack the durability and strength of metals like aluminum.
Merak ediyor olabilirsiniz why aluminum is chosen over other materials in CNC machining. The answer lies in its combination of strength, weight, and machinability, which makes it ideal for a wide variety of applications across different industries.
9. Techniques to Improve the Surface Finish of Aluminum Parts
Achieving a smooth and high-quality surface finish is one of the key considerations in aluminum CNC machining. Several techniques can be used to improve the surface finish, such as polishing, anodizing, and coating. Polishing involves mechanically buffing the surface to create a shiny, smooth finish. Anodizing, on the other hand, involves an electrochemical process that creates a protective oxide layer on the aluminum surface, improving corrosion resistance and surface appearance.
Merak ediyor olabilirsiniz how surface finishes affect the final part. A smooth surface finish not only improves the appearance of the part but also enhances its performance, particularly in applications where friction or wear is a concern.
İşte anlaşma: The surface finish of aluminum parts can be improved through various post-processing techniques, each offering unique benefits for different applications.
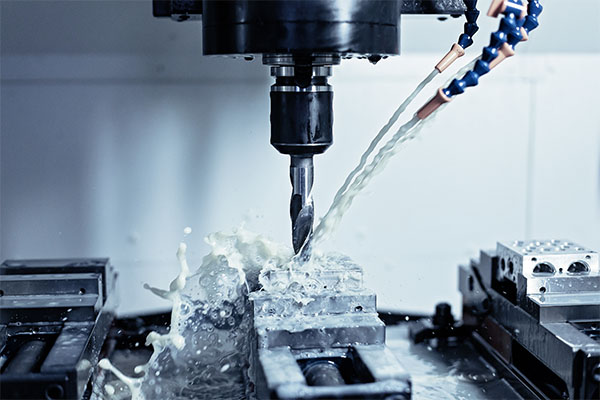
10. Precision and Tolerances in Aluminum CNC Machining
Precision is one of the most important factors in CNC machining. Aluminum CNC machining offers high accuracy and tight tolerances, allowing manufacturers to produce parts with incredible precision. Typical tolerance ranges for aluminum parts vary depending on the complexity of the part and the type of CNC machine used, but it is not uncommon to achieve tolerances as tight as ±0.001 inches.
The key to achieving precision lies in the combination of high-quality CNC machines, skilled operators, and careful programming. With the right setup, CNC machines can deliver parts that meet even the strictest specifications.
Merak ediyor olabilirsiniz what makes aluminum CNC machining so precise. The answer is simple: CNC machines are computer-controlled, ensuring that each movement is executed with precision, resulting in highly accurate and repeatable parts.
11. Applications of Aluminum CNC Machining
Aluminum CNC machining is used in a wide variety of industries. Some of the most common applications include aerospace, automotive, and electronics manufacturing. In the aerospace industry, aluminum parts are often used for aircraft frames, engine components, and brackets. In the automotive industry, aluminum is used for engine parts, wheels, and body panels.
Aluminum CNC machining is also widely used in consumer electronics, such as smartphones and laptops, where lightweight and durable components are essential. Medical devices, furniture, and construction industries also benefit from aluminum parts produced through CNC machining.
Merak ediyor olabilirsiniz why aluminum is used in so many industries. The answer lies in its versatility, strength-to-weight ratio, and ability to be machined with high precision, making it ideal for a wide range of applications.
12. Cost Considerations in Aluminum CNC Machining
The cost of aluminum CNC machining can vary depending on several factors, including material costs, machining time, and tooling requirements. Aluminum is generally less expensive than other metals like steel or titanium, which makes it an attractive choice for manufacturers looking to keep production costs low.
However, there are other factors that can influence the overall cost, such as tool wear Ve machine time. For example, machining harder aluminum alloys like 7075 can result in higher tool wear, which increases production costs. Additionally, the complexity of the part and the required tolerance can also affect machining time, further impacting the cost.
İşte anlaşma: By optimizing the machining process and carefully selecting materials, manufacturers can keep the costs of aluminum CNC machining competitive while maintaining high-quality outputs.
13. Future Trends in Aluminum CNC Machining
The future of aluminum CNC machining looks bright, with advancements in technology driving improvements in speed, precision, and sustainability. Emerging technologies such as automation Ve additive manufacturing are changing the way aluminum parts are produced. Automation allows for faster production times and higher consistency, while 3D printing (additive manufacturing) offers the ability to create complex, lightweight parts with less material waste.
Sustainability is also becoming a key focus in CNC machining. Manufacturers are increasingly looking for ways to reduce energy consumption and material waste, making the process more environmentally friendly.
Merak ediyor olabilirsiniz how these trends will shape the future of aluminum CNC machining. The answer is that automation, additive manufacturing, and sustainability will drive innovation and make the process more efficient, precise, and eco-friendly.
14. Best Practices for Aluminum CNC Machining
To achieve the best results when machining aluminum, manufacturers should follow a few key best practices. Choosing the right tooling is essential to ensure a smooth machining process. For example, carbide tools are often preferred when machining aluminum because they offer better wear resistance and maintain sharpness longer than high-speed steel tools.
Optimizing feed rates and cutting speeds is also crucial to improve efficiency and part quality. Cutting too fast can cause overheating, while cutting too slowly can lead to poor surface finishes and tool wear.
İşte anlaşma: By following best practices, manufacturers can maximize efficiency, reduce wear and tear on machines and tools, and ensure that aluminum parts are produced with high precision.
15. Çözüm
Sonuç olarak, aluminum CNC machining offers numerous advantages, including precision, efficiency, and versatility. From selecting the right material to implementing best practices and overcoming challenges, understanding the ins and outs of aluminum CNC machining is essential for anyone involved in manufacturing. Whether you’re producing small batches or large quantities, CNC machining allows you to create high-quality, durable aluminum parts that meet the strictest standards. The future of aluminum CNC machining is exciting, with advancements in technology making it faster, more efficient, and more sustainable than ever before.
Call to action: If you’re ready to explore the potential of aluminum CNC machining for your next project, contact a CNC machining expert today to get started!
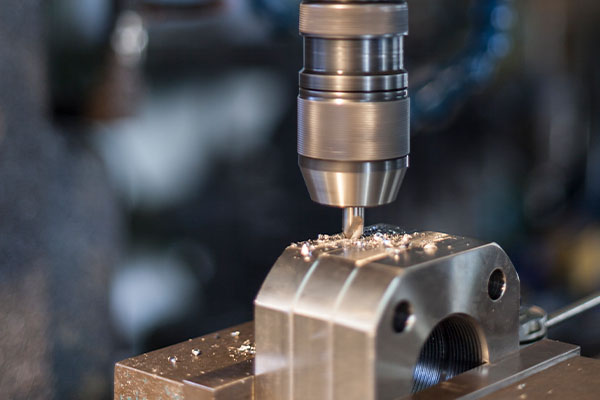
SSS Bölümü
- What is the difference between CNC machining and traditional machining?
CNC machining is a computer-controlled process that automates the cutting, drilling, and shaping of materials. Unlike traditional machining, which relies on manual control, CNC machines follow precise instructions from a computer, ensuring consistency and accuracy. This leads to higher efficiency, repeatability, and the ability to create complex parts that would be difficult to achieve manually. - Can CNC machining be used for all types of aluminum alloys?
Yes, CNC machining can be used for various aluminum alloys, but some alloys are easier to machine than others. For example, 6061 aluminum is highly machinable and commonly used in many industries, while harder alloys like 7075 may require more advanced tools and longer machining times. Choosing the right alloy for your specific project will depend on factors such as strength requirements and machinability. - How do I choose the right aluminum alloy for my project?
When choosing the right aluminum alloy, consider factors such as strength, corrosion resistance, and machinability. For general purposes, 6061 is a popular choice due to its balance of strength and ease of machining. For applications requiring higher strength, such as aerospace, 7075 may be more suitable. It’s important to understand the specific requirements of your project and consult with experts to make the best choice. - What is the best CNC machine for aluminum?
The best CNC machine for aluminum depends on the type and complexity of the parts being produced. CNC milling machines are ideal for creating flat or contoured surfaces, while CNC lathes are used for cylindrical components. For high-volume production, vertical or horizontal machining centers equipped with high-speed spindles and precise tool changes are commonly used to ensure efficiency and precision in aluminum machining. - What factors impact the cost of aluminum CNC machining?
Several factors affect the cost of aluminum CNC machining, including material costs, machine time, tooling, and part complexity. The type of aluminum alloy chosen, the required tolerances, and the machining process all influence the final price. For example, harder alloys may increase tool wear and machining time, raising costs. Additionally, batch size and post-processing requirements can also impact the overall price. - How do I achieve the best surface finish for aluminum parts?
Achieving a smooth surface finish in aluminum machining involves selecting the right tools and machining parameters. Using sharp carbide tools, optimizing feed rates and cutting speeds, and ensuring effective cooling can help improve surface quality. For post-processing, techniques such as polishing, anodizing, or coating can enhance the finish, providing both aesthetic appeal and functional benefits like improved corrosion resistance. - What industries use aluminum CNC machining the most?
Aluminum CNC machining is widely used in industries such as aerospace, automotive, electronics, medical devices, and consumer products. In aerospace, aluminum parts are essential for aircraft frames, engine components, and brackets due to the material’s lightweight and durability. The automotive industry uses aluminum for engine parts, body panels, and wheels, while electronics manufacturers rely on aluminum for housings and heat sinks. - What are the common mistakes in aluminum CNC machining and how can they be avoided? Common mistakes in aluminum CNC machining include incorrect tool selection, improper feed rates, and insufficient cooling. These issues can result in poor surface finishes, tool wear, and part distortion. To avoid these mistakes, it’s important to carefully select the right tools, optimize machining parameters for the specific alloy, and use effective cooling systems to manage heat buildup during the process.
- How do I improve the lifespan of CNC tools when machining aluminum?
To extend the lifespan of CNC tools during aluminum machining, ensure proper tool selection, use appropriate cutting speeds and feed rates, and implement effective cooling strategies. Regular maintenance of tools and machines is also essential to prevent wear and ensure consistent performance. Additionally, using high-quality carbide tools can help reduce wear and improve overall machining efficiency. - Is aluminum CNC machining sustainable?
Yes, aluminum CNC machining can be sustainable when proper practices are followed. Aluminum is a highly recyclable material, and many manufacturers are implementing more sustainable practices such as reducing energy consumption, minimizing waste, and using eco-friendly coolants. By optimizing processes and focusing on efficiency, CNC machining can contribute to reducing environmental impact while maintaining high production quality.