Introduction: The Growing Demand for Precision in Aerospace
The aerospace industry has long been at the forefront of technological advancement, with precision and reliability being paramount in every component produced. As aviation, space exploration, and defense systems become more complex, the demand for high-quality, durable, and meticulously engineered parts has skyrocketed. In this high-stakes environment, CNC machining has emerged as a critical technology in meeting these demands, offering unparalleled accuracy, speed, and efficiency in the manufacturing of aerospace components. This guide will explore how CNC machining is reshaping the aerospace industry, highlighting its importance, applications, and future potential.
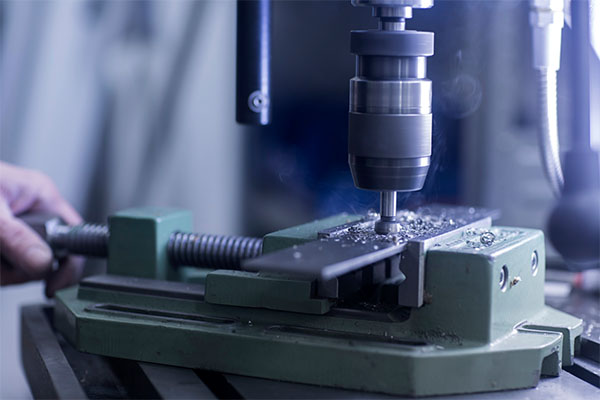
Why CNC Machining is the Backbone of Aerospace Manufacturing
CNC machining has revolutionized the way aerospace parts are produced, ensuring the highest levels of precision, quality, and reliability. The aerospace industry demands perfection in every aspect, from the structural integrity of airframes to the functionality of engine components. CNC machining stands out as the ideal solution because it enables the production of parts with micron-level tolerances, which is essential for the safety and performance of aerospace vehicles.
One of the most significant advantages of CNC machining in aerospace is its ability to produce complex geometries with high accuracy. Unlike traditional methods, which may require multiple manual operations, CNC machines can perform a variety of tasks in a single setup. This capability not only streamlines production but also reduces the likelihood of errors and inconsistencies. With computer-controlled systems guiding the cutting tools, CNC machines can achieve the fine tolerances needed for critical aerospace components.
Another key benefit of CNC machining is its adaptability. Aerospace components often require customization, whether it’s a prototype part or a specialized component for a specific aircraft model. CNC machines offer the flexibility to easily modify designs and accommodate unique specifications. This is especially important in the aerospace sector, where continuous innovation is a driving force.
In addition to precision and flexibility, CNC machining enhances production efficiency. Aerospace manufacturers need to meet tight deadlines and manage high production volumes, and CNC machines are capable of working around the clock without sacrificing quality. The automation of the machining process reduces the time required for manual setup and machining, ensuring that parts are produced quickly and cost-effectively.
CNC Machining vs. Traditional Manufacturing in Aerospace
The shift from traditional manufacturing methods to CNC machining has been a game-changer for the aerospace industry. In traditional manufacturing, components were often made by hand or using basic tools, which limited the complexity and precision of the parts. This approach was time-consuming, labor-intensive, and prone to errors.
In contrast, CNC machining is an automated process that uses computer programs to control the movement of machines and tools. This method provides several advantages over traditional manufacturing, particularly in the aerospace sector. One of the key benefits is the high level of precision that CNC machines can achieve. Unlike manual methods, which rely on the skill of the operator, CNC machines are programmed to follow exact specifications, ensuring consistency and accuracy in every part produced.
Furthermore, CNC machining offers a significant increase in production speed. Traditional manufacturing methods often required multiple steps and manual interventions to produce a single component, whereas CNC machines can complete the entire process in a fraction of the time. This efficiency is crucial in the aerospace industry, where tight production schedules and high demand for components are common.
Another important advantage of CNC machining is the ability to produce complex geometries with ease. Aerospace components, such as turbine blades, wing structures, and engine parts, often have intricate shapes that are difficult or impossible to achieve with traditional methods. CNC machines can handle these complex designs with high precision, making them ideal for the aerospace industry.
In terms of cost-effectiveness, CNC machining also offers significant benefits. Although the initial investment in CNC machines may be higher than traditional methods, the long-term savings are substantial. CNC machines reduce material waste, eliminate the need for skilled manual labor, and can operate continuously without the need for breaks or downtime. This leads to lower production costs and greater profitability for aerospace manufacturers.
Key Aerospace Components Manufactured by CNC Machining
CNC machining plays a critical role in the production of a wide range of aerospace components, each of which must meet strict performance and safety standards. Some of the most commonly produced aerospace parts include:
Turbine Blades: Turbine blades are one of the most complex and critical components in an aircraft engine. They must be highly resistant to heat, wear, and stress while maintaining a precise aerodynamic shape. CNC machining allows for the creation of turbine blades with the exact tolerances required for optimal performance. The use of high-performance materials, such as titanium alloys and advanced composites, further enhances the durability and efficiency of these parts.
Engine Components: Aerospace engines are composed of numerous parts, each of which must perform flawlessly under extreme conditions. CNC machining is used to produce engine components such as compressor blades, nozzles, and combustion chambers, all of which require high precision and strength. The ability to work with materials like heat-resistant alloys and ceramics ensures that these components can withstand the intense temperatures and pressures they are subjected to during flight.
Airframe Parts: The airframe is the structural backbone of an aircraft, providing support for the wings, fuselage, and tail. CNC machining is used to create critical airframe components such as wing spars, fuselage frames, and bulkheads. These parts must be lightweight yet strong enough to withstand the stresses of flight. CNC machining allows for the precise fabrication of these components from materials like aluminum and composite materials, ensuring optimal performance and safety.
Landing Gear Components: The landing gear is responsible for supporting the weight of the aircraft during takeoff and landing. CNC machining is used to produce landing gear components such as struts, wheels, and braking systems. These parts must be both strong and lightweight, and CNC machining provides the precision needed to meet these requirements.
Flight Control Components: Flight control systems, such as actuators, servos, and control surfaces, are vital to the operation of an aircraft. CNC machining is used to produce these components with tight tolerances to ensure proper function and reliability. The use of advanced materials, such as high-strength steel and aluminum alloys, ensures that these parts can withstand the forces encountered during flight.
These are just a few examples of the many aerospace components produced using CNC machining. The versatility of CNC technology allows manufacturers to produce a wide variety of parts, each of which must meet stringent performance and safety standards.
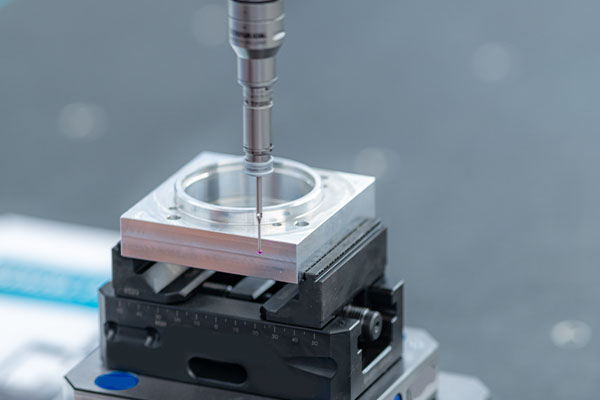
The Role of CNC in Prototyping and Production
In the aerospace industry, prototyping and production go hand in hand. CNC machining plays a crucial role in both stages, enabling manufacturers to produce high-quality prototypes and scale up to full production runs with ease.
Prototyping: The development of new aerospace components often begins with the creation of a prototype. CNC machining is ideal for prototyping because it allows for rapid production of parts with high accuracy. Engineers can quickly modify designs and test different iterations without the need for costly and time-consuming retooling. This speed and flexibility make CNC machining an invaluable tool in the development of new aerospace technologies.
Production: Once a prototype has been finalized, CNC machining can be used to produce parts in larger quantities. One of the key benefits of CNC machining in production is its ability to maintain consistency and precision across all parts. Whether producing a single component or thousands of identical parts, CNC machines can replicate the exact specifications of the prototype, ensuring that each part meets the required standards. This is particularly important in the aerospace industry, where even the slightest deviation from the design can compromise safety and performance.
In addition to its precision, CNC machining also offers speed and efficiency in production. Aerospace manufacturers often face tight deadlines and high demand for components, and CNC machines can operate continuously without the need for breaks or downtime. This allows manufacturers to meet production targets while maintaining high levels of quality and accuracy.
Overall, CNC machining provides a seamless transition from prototyping to production, ensuring that aerospace manufacturers can quickly bring new designs to market while maintaining the highest standards of quality and performance.
Materials Used in Aerospace CNC Machining: Durability and Precision
The materials used in aerospace CNC machining are critical to the performance, safety, and longevity of the components produced. Aerospace manufacturers often work with high-performance materials that can withstand extreme temperatures, pressures, and stresses. CNC machining allows for the precise shaping and fabrication of these materials, ensuring that each component meets the exact specifications required for optimal performance.
Titanium Alloys: Titanium is one of the most commonly used materials in aerospace due to its excellent strength-to-weight ratio and resistance to corrosion. It is often used in engine components, airframes, and landing gear. CNC machining is essential for shaping titanium alloys into the intricate geometries required for these parts. The high strength of titanium allows for the creation of lightweight components that are both durable and strong.
Aluminum Alloys: Aluminum is another popular material in the aerospace industry, especially for airframe components. It is lightweight, yet strong, and has excellent corrosion resistance. CNC machining is used to fabricate aluminum parts with precise dimensions, ensuring that they meet the performance requirements of the aerospace industry. Aluminum alloys are often used in the production of wing structures, fuselage frames, and other critical components.
Composites: Composites, such as carbon fiber and fiberglass, are increasingly being used in aerospace due to their lightweight and high-strength properties. CNC machining allows for the precise cutting and shaping of composite materials, enabling the production of parts with complex geometries. These materials are often used in aircraft wings, fuselages, and interior components.
Steel Alloys: Steel is used in aerospace for components that require high strength and durability, such as engine parts and landing gear. CNC machining can precisely shape steel alloys into the necessary forms, ensuring that these components can withstand the extreme conditions they encounter during flight.
These materials represent just a small sampling of the wide variety of substances used in aerospace CNC machining. The ability to work with such diverse materials allows manufacturers to create components that meet the demanding requirements of the aerospace industry.
The Benefits of Custom CNC Machining for Aerospace Companies
In the aerospace industry, custom machining is often required to meet specific performance and safety standards. Whether producing a one-off prototype or a batch of parts for a particular aircraft, custom CNC machining offers several advantages that make it the ideal solution for aerospace manufacturers.
Tailored Designs: One of the main benefits of custom CNC machining is the ability to create parts that are specifically designed to meet the needs of the customer. Whether it’s a custom engine component or a unique structural part, CNC machining allows manufacturers to create components that fit precisely with the specifications provided. This level of customization is essential in the aerospace industry, where each part must be optimized for performance.
Faster Turnaround Times: Custom CNC machining also enables faster turnaround times for prototype and production runs. Because CNC machines are programmed to follow exact designs, there is little room for error or delays during the manufacturing process. This is particularly important in the aerospace industry, where deadlines are often tight and production schedules can be demanding.
Cost-Effectiveness: Despite the higher initial cost of custom CNC machining, the long-term savings can be substantial. Custom machining eliminates the need for retooling or rework, which can save both time and money. Additionally, the high precision of CNC machines reduces material waste, further contributing to cost savings.
Improved Quality Control: Custom CNC machining offers greater control over the production process, which leads to higher-quality parts. Aerospace manufacturers can ensure that each part is produced to the exact specifications, reducing the likelihood of defects or failures. This is especially critical in the aerospace industry, where even the smallest error can have catastrophic consequences.
Overall, custom CNC machining provides aerospace companies with the flexibility, speed, and cost-effectiveness needed to meet the demands of this highly competitive industry.
Why Quality Control in Aerospace CNC Machining is Non-Negotiable
Quality control is a fundamental aspect of aerospace manufacturing, and CNC machining plays a pivotal role in ensuring that all components meet the required standards. Aerospace parts must undergo rigorous testing and inspection to ensure their safety, reliability, and performance. CNC machining provides several advantages in maintaining high levels of quality control throughout the manufacturing process.
Consistency and Precision: CNC machines are programmed to produce parts with exact specifications, ensuring that each component is consistent and accurate. This level of precision is critical in the aerospace industry, where even the smallest variation from the design can lead to catastrophic failures. By using CNC machining, manufacturers can ensure that every part meets the required tolerances and quality standards.
Inspection and Testing: CNC machining is often accompanied by automated inspection systems that check the quality of the produced parts in real-time. These systems use sensors and cameras to detect any deviations from the specifications, ensuring that any defects are identified before the part is shipped. In addition, many aerospace manufacturers use non-destructive testing methods, such as X-ray inspection, to verify the integrity of critical components.
Certifications: Aerospace manufacturers are often required to meet stringent certifications and standards, such as ISO 9001, AS9100, and NADCAP. These certifications ensure that the manufacturer follows established procedures for quality control and is committed to producing high-quality parts. CNC machining is fully compatible with these certification requirements, making it an essential tool for maintaining compliance with industry standards.
Documentation and Traceability: Another important aspect of quality control in aerospace machining is documentation. CNC machining provides detailed records of every step of the manufacturing process, including machine settings, materials used, and inspection results. This documentation ensures traceability, allowing manufacturers to track each part through every stage of production and ensure that it meets all necessary quality standards.
How CNC Machining Contributes to Safety in Aerospace
The role of CNC machining in ensuring safety in the aerospace industry cannot be overstated. Aerospace components must be able to withstand extreme conditions and perform reliably throughout the lifespan of an aircraft or spacecraft. CNC machining contributes to safety by providing the high precision, quality, and consistency required for critical parts.
Precision and Tolerances: Aerospace components must be manufactured with tight tolerances to ensure that they fit properly and perform as expected. CNC machining is capable of achieving micron-level precision, ensuring that each component is within the exact specifications required for safe operation. Whether it’s a turbine blade or a flight control system, the accuracy of CNC machining ensures that all parts function reliably.
Material Quality: CNC machining is particularly important for working with advanced materials that are commonly used in aerospace, such as titanium, composites, and high-strength alloys. These materials have unique properties that require specialized machining techniques. CNC machines are able to handle these materials with ease, ensuring that they retain their strength and durability even under extreme conditions.
Critical Components: Many of the most critical components in aerospace, such as engine parts, landing gear, and structural elements, are produced using CNC machining. The precision and quality of these parts are essential for the safe operation of the aircraft. Any deviation from the design could result in failure, which is why CNC machining is used to ensure that every component meets the highest standards.
Testing and Inspection: CNC machining is often combined with rigorous testing and inspection processes to verify the integrity of each part. Non-destructive testing methods, such as ultrasound and X-ray inspection, are commonly used to ensure that aerospace components are free of defects and can withstand the stresses of flight. CNC machining plays a key role in ensuring that these parts are produced to the exact specifications required for safety.
The Environmental Benefits of CNC Machining in Aerospace
CNC machining is not only beneficial for the performance and safety of aerospace components, but it also offers significant environmental advantages. In an industry that relies on advanced technologies and high-performance materials, CNC machining helps to reduce waste, increase efficiency, and promote sustainability.
Material Waste Reduction: One of the primary environmental benefits of CNC machining is its ability to reduce material waste. Traditional manufacturing methods often generate significant amounts of scrap material, which can be costly and wasteful. CNC machines, on the other hand, are programmed to cut parts with high accuracy, minimizing the amount of excess material produced. This leads to less waste and more efficient use of resources.
Energy Efficiency: CNC machines are designed to be highly efficient, using less energy compared to traditional manufacturing methods. This is particularly important in the aerospace industry, where large-scale production requires significant amounts of energy. By reducing energy consumption, CNC machining helps aerospace manufacturers lower their carbon footprint and contribute to a more sustainable industry.
Recyclable Materials: Many of the materials used in aerospace manufacturing, such as aluminum and titanium, are highly recyclable. CNC machining makes it easier to recycle these materials by producing clean cuts that allow for easy separation and reuse. This further reduces the environmental impact of aerospace manufacturing and helps to conserve valuable resources.
Sustainable Practices: Many aerospace manufacturers are incorporating sustainable practices into their operations, such as using renewable energy sources and reducing water consumption. CNC machining supports these efforts by enabling efficient production processes that require fewer resources and produce less waste.
Aerospace CNC Machining: From Concept to Finished Product
The process of CNC machining in aerospace manufacturing involves several key stages, each of which is critical to ensuring that the final product meets the required specifications. The journey from concept to finished product is a complex and multi-faceted process that requires careful planning, precise execution, and rigorous quality control.
Design and Prototyping: The process begins with the design phase, where engineers develop detailed specifications for the component. Once the design is finalized, a prototype is created using CNC machining. This allows engineers to test the design, make adjustments, and ensure that the part meets all performance requirements.
Machining and Production: After the prototype has been approved, the component moves into full production. CNC machining is used to produce the part in large quantities, ensuring that each piece is identical and meets the required tolerances. This stage involves careful programming, tool selection, and machine setup to ensure that the component is produced with the highest level of precision.
Inspection and Testing: Once the parts are produced, they undergo a series of inspections and tests to verify their quality. CNC machining plays a crucial role in ensuring that the parts meet the exact specifications required for performance and safety. This includes checking for dimensional accuracy, material integrity, and surface finish.
Delivery and Documentation: Finally, the finished components are delivered to the customer, along with detailed documentation that includes machining records, inspection results, and material certifications. This ensures traceability and provides the customer with the assurance that the parts meet all required standards.
The Role of Innovation in CNC Machining for Aerospace
Innovation is a driving force in the aerospace industry, and CNC machining plays a central role in enabling new technologies and materials. As the industry continues to evolve, CNC machining is being used to produce increasingly complex and sophisticated components that push the boundaries of what is possible.
Advanced Materials: CNC machining is essential for working with advanced materials that are becoming more common in aerospace manufacturing, such as composites and high-strength alloys. These materials offer unique properties that are necessary for modern aircraft and spacecraft but also present challenges in terms of machinability. CNC machines are designed to handle these materials with precision, ensuring that they can be shaped into the necessary components.
Automation and Robotics: Automation and robotics are transforming the aerospace manufacturing process, and CNC machining is at the forefront of this revolution. CNC machines can be integrated with robotic systems to perform tasks such as material handling, inspection, and assembly. This level of automation increases efficiency, reduces human error, and enables faster production cycles.
Additive Manufacturing: Additive manufacturing, or 3D printing, is another innovation that is revolutionizing the aerospace industry. While CNC machining remains the dominant method for producing aerospace components, additive manufacturing is increasingly being used for creating complex geometries and lightweight structures. CNC machines can work in tandem with additive manufacturing systems, providing a hybrid solution for producing highly specialized parts.
How to Choose the Right CNC Machining Partner for Aerospace Projects
Choosing the right CNC machining partner is critical to the success of any aerospace project. The right partner will have the expertise, experience, and technology needed to produce high-quality parts that meet the demanding requirements of the aerospace industry.
Experience and Expertise: When selecting a CNC machining partner, it’s important to look for a company with a proven track record in the aerospace industry. Experience working with aerospace materials and understanding the stringent standards and regulations is essential for ensuring that the parts are produced correctly.
Technology and Capabilities: CNC machining is a highly technical field, and it’s important to choose a partner that has the latest machinery and technology. This includes advanced CNC machines that can handle complex geometries, as well as inspection and testing systems that ensure quality control.
Quality Control and Certifications: Quality control is non-negotiable in the aerospace industry, so it’s important to choose a partner that has strong quality control processes in place. Look for certifications such as ISO 9001, AS9100, and NADCAP, which demonstrate a commitment to quality and compliance with industry standards.
Customer Service and Support: Finally, it’s important to choose a CNC machining partner that offers excellent customer service and support. The aerospace manufacturing process can be complex, and having a reliable partner that can provide guidance and assistance throughout the project is essential.
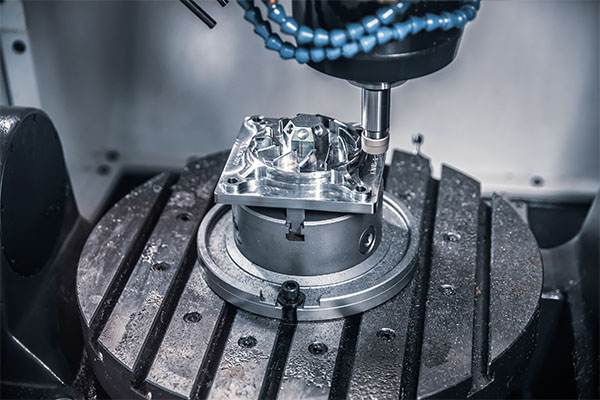
SSS Bölümü
What is CNC machining and why is it important in aerospace?
CNC machining is a computer-controlled manufacturing process that allows for the creation of highly precise and complex components. It’s crucial in aerospace because it ensures the accuracy and consistency required for safety-critical parts.
What are the benefits of CNC machining in aerospace?
The benefits of CNC machining in aerospace include increased precision, faster production times, cost-effectiveness, and the ability to work with advanced materials such as titanium and composites.
How does CNC machining improve safety in aerospace?
CNC machining ensures that aerospace components are produced with tight tolerances and high-quality materials, minimizing the risk of failure and contributing to the safety of aircraft and spacecraft.
What are some examples of aerospace components made with CNC machining?
Examples of aerospace components produced with CNC machining include turbine blades, engine parts, airframe structures, landing gear components, and flight control systems.
How does CNC machining contribute to environmental sustainability in aerospace?
CNC machining reduces material waste, improves energy efficiency, and allows for the use of recyclable materials, making it a more sustainable option for aerospace manufacturing.