Introduction:
Why CNC Machining Aluminum is Crucial for Modern Manufacturing?
CNC (Computer Numerical Control) machining has revolutionized manufacturing, particularly in industries requiring precise and consistent components. CNC machining aluminum combines the flexibility of automated processes with the material’s outstanding characteristics, making it a top choice in various fields. Whether you’re in aerospace, automotive, or electronics, aluminum’s lightweight nature and excellent durability make it indispensable. However, machining aluminum isn’t as simple as it seems—understanding the material, choosing the right equipment, and applying the right techniques are crucial for optimal results. In this article, we’ll dive into expert tips and tricks to help you get the best out of CNC machining aluminum.
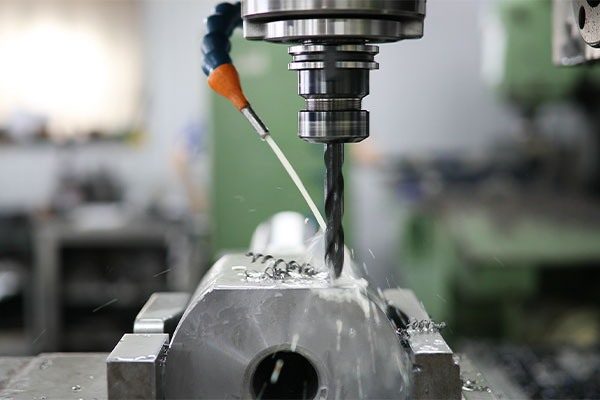
What is CNC Machining and Why Aluminum?
Understanding CNC Aluminum Machining
CNC machining is a process that uses pre-programmed computer software to control the movement of machinery and tools. CNC machines can perform a variety of tasks, including drilling, cutting, milling, and turning. When applied to aluminum, CNC machining allows for high precision and repeatability in producing complex shapes and parts. This is particularly crucial in industries like aerospace, automotive, and electronics, where precision is key.
Why Choose Aluminum for CNC Machining?
Aluminum is a versatile material with a variety of applications in CNC machining. It is lightweight, non-corrosive, and possesses excellent thermal and electrical conductivity. These characteristics make it ideal for producing parts that need to withstand harsh environments or high temperatures without adding excessive weight. Its ability to be easily machined means it can be used for a wide array of custom components, from engine parts to medical devices.
The Benefits of Aluminum in CNC Machining
CNC machining aluminum is especially popular due to its strength-to-weight ratio, ease of cutting, and thermal conductivity. It is more cost-effective than many other metals, making it a go-to choice for mass production. The material’s versatility also means that it can be machined with a variety of tools, making it an excellent candidate for precision applications across several industries.
Selecting the Right CNC Machine for Aluminum
What Are the Best CNC Machines for Aluminum Machining?
When it comes to selecting the best CNC machine for aluminum, the decision largely depends on the complexity of the parts you’re manufacturing. For simple, small-scale operations, a CNC mill might suffice. For large-scale or high-precision needs, a CNC lathe or a multi-axis CNC machine may be the better option. Some CNC machines, like those made by Haas or Okuma, are specifically designed with aluminum machining in mind, offering features that optimize the process.
Considerations for Choosing the Right Machine
Choosing the right machine for aluminum involves understanding several key factors. First, the machine’s rigidity is important because aluminum can generate vibrations that affect the machining process. A rigid machine minimizes these vibrations, ensuring a smoother operation. Additionally, you should consider the size of the machine, its spindle speed, and its tool capacity. High spindle speed is especially important for aluminum, as it allows for faster cutting rates and better surface finishes.
Tools and Equipment Needed for CNC Machining Aluminum
Essential Tools for CNC Aluminum Machining
The tools used for CNC aluminum machining vary depending on the specific operation. Common tools include end mills, drills, and reamers. When machining aluminum, it’s essential to use tools that are designed for the material to ensure both efficiency and tool longevity. For example, carbide tools are commonly used due to their hardness and resistance to wear.
Tool Coatings and Their Importance for Aluminum
In CNC machining, tool coatings are critical for improving tool life and performance. For aluminum, coatings such as TiN (Titanium Nitride) or TiAlN (Titanium Aluminum Nitride) can improve heat resistance and reduce friction, leading to smoother cuts and longer-lasting tools. Choosing the right coating can also help in preventing aluminum from sticking to the cutting tool, ensuring consistent and clean cuts throughout the machining process.
Preparing for CNC Machining: What You Need to Know
Preparing the Aluminum Material
Before starting CNC machining, it’s crucial to properly prepare the aluminum material. This includes ensuring the material is free of contaminants like oils, dust, and dirt, which can affect the quality of the finished part. Aluminum stock should also be checked for any imperfections or deformities that could impact the machining process. Additionally, the material should be properly stored to avoid oxidation or corrosion.
CAD and CAM Software Setup for CNC Aluminum Parts
Computer-Aided Design (CAD) and Computer-Aided Manufacturing (CAM) software are essential tools in the CNC aluminum machining process. CAD software is used to design the part, while CAM software generates the toolpaths required for machining. For aluminum, the toolpaths should be optimized to minimize tool wear and ensure the most efficient machining process. Kova Tugayları such as “Here’s a quick tip” or “You might be wondering” can help guide you through the best practices for software setup.
Cutting Techniques for CNC Machining Aluminum
Understanding Cutting Speeds and Feeds for Aluminum
To achieve optimal results when machining aluminum, understanding cutting speeds and feeds is essential. Cutting speed refers to the rate at which the cutting tool moves through the material, while feed rate refers to how quickly the tool moves along the material’s surface. The right combination of cutting speed and feed rate depends on the type of aluminum alloy being used, the cutting tool, and the desired surface finish.
Common Cutting Strategies
There are several cutting strategies used in CNC machining aluminum, including slotting, profiling, and facing. Slotting involves creating narrow, deep cuts, while profiling refers to cutting along the outer edge of a part. Facing is used to flatten the surface of a part. Each of these techniques requires different speeds, feeds, and tools to ensure the best quality and efficiency.
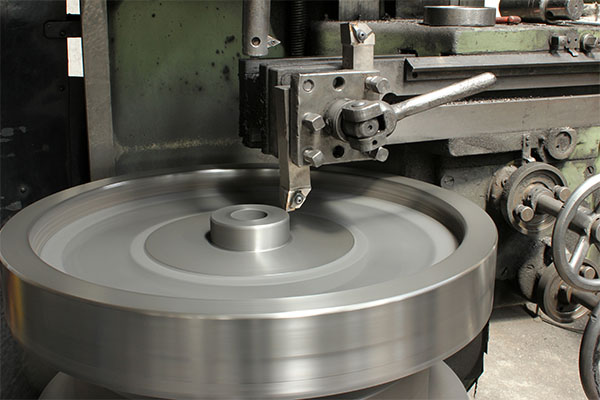
Cooling and Lubrication: The Key to Success
Why Cooling and Lubrication Matter in Aluminum Machining
Aluminum machining generates heat, which can lead to tool wear, material deformation, and poor surface finish. This is why cooling and lubrication are crucial. Proper cooling helps to dissipate heat, reducing friction and extending tool life. Kova Tugayları like “Don’t forget” or “Here’s a secret” can highlight the importance of cooling and lubrication, especially in high-speed machining scenarios.
Choosing the Right Coolant or Lubricant
When machining aluminum, it’s essential to select the right coolant or lubricant. Water-based coolants are often preferred for aluminum because they help to cool the material effectively without leaving residues. Oil-based lubricants, on the other hand, provide better lubrication, reducing friction and wear. Kova Tugayları such as “Trust me, this makes a difference” emphasize the importance of coolant application in the machining process.
Fine-Tuning Your CNC Machine Settings
Adjusting Spindle Speed and Feed Rates
To achieve a quality finish on aluminum parts, it’s important to adjust the spindle speed and feed rates according to the material thickness, tooling, and cutting strategy. Higher speeds are generally used for thinner materials, while slower speeds may be necessary for thicker parts to ensure better control and finish quality.
Cutting Depth and Stepover Considerations
Cutting depth refers to how deep the tool cuts into the material, while stepover refers to the distance between each pass of the tool. In aluminum machining, using the right cutting depth and stepover is crucial to achieve a high-quality surface finish and prevent tool wear.
Troubleshooting Common CNC Aluminum Machining Problems
Surface Finish Issues
Surface finish is often a concern when machining aluminum, as imperfections can lead to a poor final product. Common issues include tool marks, roughness, and chatter. These problems can be mitigated by adjusting the cutting parameters, choosing the right tools, and ensuring that the machine is properly calibrated.
Aluminum Chips and Swarf Management
Managing aluminum chips and swarf is essential for both safety and efficiency. Aluminum chips can clog the machine and affect the cutting process. Proper chip management involves using the right coolant and ensuring that the machine is regularly cleaned and maintained.
Tool Wear and Breakage
Tool wear and breakage are common issues in aluminum machining, especially at high speeds. To prevent this, it’s important to use the right cutting tools, adjust machining parameters, and regularly monitor the tools for wear. Kova Tugayları like “Don’t let this happen to you” can emphasize the importance of monitoring tool condition.
Post-Machining: Ensuring High-Quality Aluminum Parts
Finishing Processes for CNC Aluminum
After CNC machining, aluminum parts often undergo finishing processes such as anodizing, polishing, and powder coating. These finishing methods can enhance the material’s durability and appearance, providing additional protection against corrosion and wear. Choosing the right finishing process depends on the part’s intended use and the required aesthetic.
Quality Control and Inspection
Quality control is a critical aspect of CNC machining aluminum. To ensure that parts meet the required specifications, they should undergo thorough inspection using tools such as Coordinate Measuring Machines (CMM). This helps to identify any deviations from the design and ensures that the parts meet dimensional accuracy.
The Environmental Impact of CNC Machining Aluminum
Waste Management and Recycling in Aluminum Machining
Aluminum is a highly recyclable material, and efforts to manage waste in CNC machining are becoming more common. Aluminum chips, dust, and scraps can often be recycled, reducing the environmental impact of the process. Kova Tugayları like “Here’s the good news” can highlight the benefits of recycling.
Energy Consumption in CNC Machining
CNC machining, especially at high speeds, can consume significant amounts of energy. To minimize the environmental footprint, manufacturers can optimize machine settings, reduce idle times, and implement energy-efficient practices.
CNC Machining Aluminum for Small vs. Large Runs
What Are the Differences in Machining Small Batches vs. Large Batches?
When machining aluminum, the size of the batch plays a significant role in determining the process. Small batches may require more manual intervention and setup time, while large runs benefit from automation and optimized processes. Kova Tugayları like “But here’s the catch” can help explain the challenges of each production scale.
When to Switch to a Different Machining Process
In some cases, large-scale production of aluminum parts may require switching to a different machining process, such as injection molding or die casting. This decision is influenced by factors like cost, complexity, and production volume.
Cost Considerations for CNC Machining Aluminum
Factors Affecting Cost
Several factors contribute to the cost of CNC machining aluminum, including material costs, machine time, tooling, and labor. Understanding how these factors interrelate can help manufacturers optimize production costs.
Reducing CNC Machining Costs
There are several ways to reduce CNC machining costs, such as optimizing tool paths, reducing machine downtime, and choosing cost-effective materials. Kova Tugayları like “Here’s the trick” can provide insights into how to make your process more cost-efficient.
CNC Machining Aluminum: Best Practices for Efficiency and Accuracy
Streamlining Workflow for Maximum Efficiency
Maximizing efficiency in CNC aluminum machining involves streamlining the entire workflow, from material preparation to post-machining processes. Using automation, improving tool selection, and maintaining consistent machine settings all contribute to better overall performance.
Maximizing Precision: Tips from Experts
To achieve the highest precision, CNC operators must regularly calibrate machines, use high-quality tooling, and carefully monitor cutting parameters. Kova Tugayları like “This will blow your mind” emphasize how small adjustments can lead to dramatic improvements in precision.
Conclusion: Mastering CNC Machining Aluminum
Mastering CNC machining aluminum requires a deep understanding of the material, the tools, and the techniques. By following the tips and tricks outlined above, you can achieve high-quality, precise aluminum parts that meet the needs of your industry. Keep experimenting, optimizing, and learning from your experiences, and you’ll see your CNC machining process improve over time.
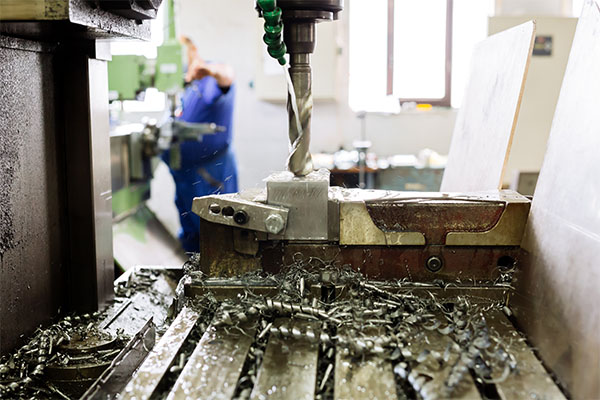
SSS Bölümü
What is the best CNC machine for machining aluminum?
- The best CNC machine for aluminum depends on the type of parts you’re making. CNC mills are great for smaller or simpler parts, while multi-axis CNC machines are better for more complex shapes.
How do I prevent tool wear while machining aluminum?
- Tool wear can be reduced by using proper cooling, selecting the right tools, and optimizing cutting speeds and feeds.
What are the ideal cutting speeds for CNC aluminum machining?
- The ideal cutting speed depends on the aluminum alloy and tool used. Generally, faster speeds are used for thinner materials, while slower speeds work better for thicker materials.
Can I use the same machine for aluminum and other metals?
- Yes, but adjustments to the machine’s settings will be necessary when switching between materials.
Why does aluminum machining require more cooling than other metals?
- Aluminum generates a lot of heat during machining, so cooling is essential to prevent tool wear, material deformation, and poor finishes.