Вступ до допусків обробки з ЧПК
Обробка з ЧПУ є одним із найточніших методів виробництва, що дозволяє виготовляти деталі з високою точністю та повторюваністю. Однак критичним фактором обробки з ЧПК є концепція допусків, які визначають допустимі варіації розмірів деталей. Допуски мають важливе значення для того, щоб деталі підходили та функціонували належним чином під час остаточного складання, особливо під час індивідуальних замовлень. Розуміння різних типів допусків і того, як вони впливають на процес обробки, має вирішальне значення як для виробників, так і для клієнтів. У цьому посібнику ми розглянемо ключові аспекти Допуски обробки з ЧПУ, включаючи їх типи, фактори, що на них впливають, і способи їх оптимізації для економічності та точності.
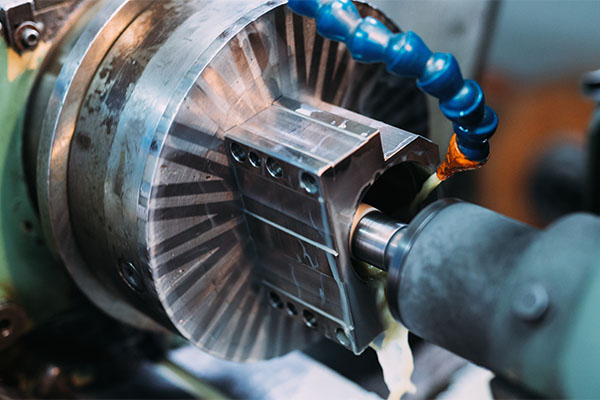
Що таке допуски на обробку з ЧПУ?
Визначення допусків при обробці з ЧПК
Допуски — це допустимі межі зміни розмірів деталей. При обробці з ЧПК це стосується того, наскільки фактичні розміри даної деталі можуть відрізнятися від запланованих проектних розмірів, але залишаються прийнятними для функціонування. По суті, допуски визначають діапазон, у межах якого деталь може змінюватися, і це гарантує, що деталь усе ще може правильно підходити до запланованої збірки.
Існує два основних типи допусків при обробці з ЧПУ: допуски на розміри і геометричні допуски. Допуски на розміри стосуються допустимих відхилень від заданих вимірювань (таких як довжина, ширина та висота), тоді як геометричні допуски описують прийнятні відхилення у формі або формі частини (наприклад, прямолінійність, площинність або округлість). Ці допуски мають вирішальне значення для забезпечення правильного функціонування та сумісності деталей з іншими компонентами.
Чому допуски є критичними при обробці з ЧПК
Точність верстата з ЧПК значною мірою визначається його здатністю підтримувати жорсткі допуски. У таких галузях, як авіакосмічна, автомобільна чи медична промисловість, де компоненти мають бездоганно підходити один до одного, допуски стають ще більш значними. Вказуючи точні допуски, виробники можуть гарантувати, що деталі відповідають необхідним функціям і надійні в умовах експлуатації.
Навпаки, якщо допуски занадто вільні, кінцева частина може не відповідати запланованим критеріям продуктивності, що призведе до дорогих помилок або збоїв. З іншого боку, занадто вузькі допуски можуть збільшити витрати на виробництво та збільшити час виконання без потреби. Встановлення правильного балансу має важливе значення для досягнення як якості, так і економічності.
Типи допусків на обробку з ЧПК, які ви повинні знати
Допуски на розміри
Допуски на розміри визначають, наскільки розміри частини можуть відрізнятися від запланованих вимірювань. Це найпоширеніші допуски в обробці з ЧПУ. Наприклад, вал може мати довжину 100 мм з допуском ±0,1 мм. Це означає, що фактична довжина може коливатися від 99,9 мм до 100,1 мм і залишатися прийнятною.
Допуски на розміри можна застосовувати до лінійних вимірювань (наприклад, довжина, ширина або висота частини) і кутових вимірювань (таких як кути між елементами). Чим більший допуск, тим точнішими повинні бути вимірювання, що часто вимагає передових верстатів з ЧПК і більше часу на виготовлення.
Геометричні допуски
Геометричні допуски використовуються для керування формою, орієнтацією та розташуванням елементів на деталі. Ці допуски мають вирішальне значення для забезпечення того, щоб деталі відповідали один одному. Наприклад, отвір може бути ідеально круглим або розташовуватися в точному місці відносно інших елементів деталі. Геометричні допуски включають:
- прямолінійність: гарантує, що об’єкт, наприклад край або вісь, ідеально прямий.
- площинність: гарантує рівність поверхні в межах заданого допуску.
- Округлість: Забезпечує ідеальну круглу форму отвору або циліндричного елемента.
- Позиція: визначає точне розташування об’єкта відносно інших.
Вказуючи ці геометричні допуски, дизайнери можуть гарантувати, що деталі відповідають необхідним функціональним критеріям.
Допуски обробки поверхні
Допуски на обробку поверхні визначають гладкість поверхні деталі. У багатьох сферах застосування якість поверхні може бути критичною для продуктивності деталей, особливо для компонентів, які рухаються або контактують з іншими частинами. Оздоблення поверхні часто визначається за допомогою вимірювань шорсткості, таких як Ra (середня шорсткість), Rz (середня максимальна висота) і Ry (максимальна висота профілю).
Чому допуски важливі: вплив на якість і функціональність деталей
Роль допусків у функціональності деталей
Коли йдеться про функціональність деталі, допуски, які застосовуються під час процесу обробки, можуть суттєво вплинути на те, чи підійде деталь і функціонуватиме за призначенням. Наприклад, у автомобільних або аерокосмічних компонентах невеликі відхилення в розмірах деталей можуть вплинути на те, наскільки добре деталі взаємодіють, що призведе до таких проблем, як погане припасування, неефективність або навіть поломка під навантаженням.
У деяких випадках незначне відхилення розміру чи форми може не бути критичною проблемою. Однак для високопродуктивних застосувань, таких як компоненти двигуна, медичні пристрої або високоточні інструменти, навіть найменші порушення допуску можуть призвести до дорогих помилок і виходу з ладу продукту. Тому важливо розуміти, як вибрати правильний допуск для кожної частини.
Допуски та контроль якості деталей
Допуски безпосередньо впливають на процес контролю якості. Жорсткі допуски вимагають складнішого обладнання та більш високого рівня перевірки, що забезпечує відповідність деталей суворим стандартам. Методи контролю якості, такі як координатно-вимірювальні машини (CMM) або оптичні вимірювальні системи, часто використовуються для перевірки того, що деталі знаходяться в межах заданого діапазону допусків. Чим вищий допуск, тим суворішим стає процес перевірки.
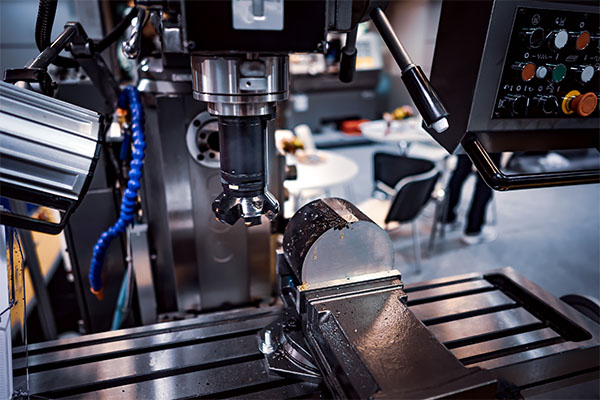
Фактори, що впливають на допуски обробки з ЧПУ
Властивості матеріалів і допуски
Матеріал, обраний для деталі, має значний вплив на допуски, яких можна досягти. Деякі матеріали, як-от метали, можуть бути більш стабільними та їх легше обробляти з жорсткими допусками, тоді як інші, як-от пластмаси чи композити, можуть зазнавати більшої деформації під час механічної обробки. Твердість матеріалу, теплове розширення та міцність відіграють важливу роль у тому, наскільки легко матеріал може підтримувати жорсткі допуски.
Наприклад, такі метали, як нержавіюча сталь і алюміній, зазвичай використовуються для обробки з ЧПК, оскільки вони забезпечують чудову стабільність розмірів і можуть досягати жорстких допусків без надмірного зносу інструментів. Однак м’які матеріали, такі як пластик або гума, можуть вимагати особливої уваги, щоб забезпечити точну обробку.
Можливості верстатів з ЧПУ
Тип верстата з ЧПК також відіграє вирішальну роль у визначенні рівня точності, якого можна досягти. Верстати з ЧПК мають різний ступінь точності, і кожен верстат має власні обмеження, коли мова йде про дотримання жорстких допусків. Високоточні верстати, такі як ті, що використовуються в аерокосмічному виробництві, можуть підтримувати допуски ±0,001 мм або навіть більше, тоді як машини загального призначення можуть мати лише допуски ±0,05 мм.
При виборі верстата важливо відповідати його можливостям вимогам конкретної деталі, що виготовляється. Розуміння обмежень вашого обладнання з ЧПК допоможе вибрати правильний допуск для деталі та уникнути непотрібних коригувань, які можуть збільшити витрати.
Інструменти та знос
Якість інструменту та його знос з часом також можуть впливати на допуски, досягнуті при обробці з ЧПК. Коли інструменти зношуються, вони можуть спричинити незначні зміни розмірів деталей. Регулярне технічне обслуговування та заміна інструментів мають вирішальне значення для підтримки постійної точності.
Щоб зменшити вплив зносу інструменту, багато виробників використовують удосконалені покриття або твердосплавні інструменти, які призначені для довшої служби та збереження гостроти. Крім того, регулювання параметрів обробки, таких як швидкість, швидкість подачі та глибина різання, може допомогти підвищити точність готової деталі.
Загальні діапазони допусків обробки з ЧПК для різних матеріалів
Допуски на металеві частини
Металеві частини часто мають відповідати дуже жорстким допускам, особливо в таких галузях, як авіакосмічна та автомобільна. Наприклад, деталі, виготовлені з нержавіючої сталі, можуть бути оброблені з допуском ±0,05 мм, тоді як деталі, виготовлені з алюмінію, можуть досягати таких жорстких допусків, як ±0,025 мм. Ці допуски гарантують, що металеві частини правильно підходять одна до одної та добре працюють у складних умовах.
Допуски для пластикових деталей
З іншого боку, пластикові деталі, як правило, складніше обробляти з такими ж жорсткими допусками, як і метали. Допуск для пластикових деталей зазвичай коливається від ±0,1 мм до ±0,5 мм залежно від типу пластику та складності деталі. Пластмаси можуть бути схильні до деформації, усадки або розширення через зміни температури, що ускладнює дотримання стабільних допусків.
У деяких випадках високоякісні пластики, такі як PEEK або PTFE, можуть використовуватися для критичних застосувань. Ці матеріали можуть мати більш жорсткі допуски, але вимагають більш досконалих технологій обробки.
Допуски на композиційні матеріали
Композитні матеріали, які часто використовуються в аерокосмічній та автомобільній промисловості, створюють свої проблеми, коли мова йде про обробку з ЧПУ. Композитні матеріали часто є шаруватими та можуть мати різні властивості залежно від напрямку волокон, що може спричинити зміни в міцності та стабільності розмірів деталей. Допуски для композитних деталей зазвичай коливаються від ±0,1 мм до ±0,3 мм залежно від конкретного матеріалу та геометрії деталі.
Вибір правильних допусків для деталей, виготовлених на замовлення
Визначення вимог до допуску
Вибір правильних допусків для деталей, виготовлених на замовлення, починається з розуміння конкретної функції деталі. Наприклад, деталі, які повинні підходити один до одного або взаємодіяти з іншими компонентами, вимагають жорсткіших допусків, щоб забезпечити належне вирівнювання та функціональність. З іншого боку, деталі, які не потребують точної підгонки, можуть бути розроблені з меншими допусками, щоб зменшити витрати на виробництво.
Щоб визначити оптимальний допуск для деталі, важливо враховувати як вимоги до конструкції, так і можливості виробничого процесу. Занадто жорсткі допуски можуть збільшити час виробництва, витрати на інструменти та ймовірність помилок, тоді як занадто вільні допуски можуть поставити під загрозу функцію або якість деталі.
Баланс між точністю та ціною
Хоча може виникнути спокуса вказати якомога точніші допуски для забезпечення найвищого рівня точності, це часто коштує дорожче. Досягнення жорсткіших допусків зазвичай вимагає більш досконалого обладнання, більш тривалого часу обробки та збільшення витрат на перевірку. Для багатьох деталей рентабельніше вказати допуски, які відповідають призначеній функції частини, не перевищуючи точності.
Встановлення правильного балансу між толерантністю та вартістю є ключовим для досягнення як якості, так і ефективності обробки на замовлення.
Як допуски впливають на витрати на обробку з ЧПК
Зв'язок між допустимими відхиленнями та виробничими витратами
При обробці з ЧПК існує пряма залежність між щільністю допуску та загальною вартістю виробництва. Більш жорсткі допуски зазвичай вимагають більш досконалих технологій, підвищеної точності та більше часу, щоб гарантувати, що деталь відповідає специфікації. Як наслідок, витрати на виробництво мають тенденцію до зростання з потребою більш жорстких допусків. Це пояснюється тим, що на кожному етапі процесу, від початкового проектування до кінцевої перевірки, потрібна більша увага до деталей.
Наприклад, при обробці деталі з допуском ±0,1 мм машині може знадобитися зробити більше проходів або використовувати спеціалізовані інструменти, щоб забезпечити досягнення бажаних розмірів. Це може збільшити час обробки та використання матеріалу, що сприяє підвищенню витрат. З іншого боку, виготовлення деталі з допуском ±0,5 мм може не потребувати багато часу або спеціального обладнання, що знижує вартість виробництва.
Крім того, деталі з жорсткішими допусками часто вимагають більш суворого контролю якості та перевірки. Залежно від застосування, це може включати використання складних інструментів, таких як координатно-вимірювальні машини (CMM), лазерне сканування або інші високоточні вимірювальні пристрої. Вартість цих інструментів разом із часом, витраченим на перевірку кожної деталі, може швидко зрости при виготовленні компонентів із дуже жорсткими допусками.
Як допуски впливають на час виготовлення
Допуски також впливають на час виконання проектів обробки з ЧПК. Деталі з більш жорсткими допусками вимагають більш ретельного планування та додаткового часу для процесу обробки. Наприклад, обробка деталі, для якої потрібен допуск ±0,01 мм, може тривати на кілька годин довше, ніж аналогічна деталь із допуском ±0,5 мм.
Додатковий час, потрібний для виконання більш жорстких допусків, також може затримати загальний графік виробництва, особливо в проектах з кількома деталями або складною геометрією. Крім того, якщо під час процесу виникають помилки обробки, їх, можливо, доведеться виправити, що призведе до додаткової переробки та подальшого збільшення часу виконання.
Щоб звести до мінімуму вплив жорстких допусків на час виконання робіт, виробникам часто доводиться ретельно планувати й оптимізувати процес обробки. Це може включати вибір правильних верстатів, коригування параметрів різання та використання найефективніших траєкторій руху інструментів, щоб забезпечити виконання деталі за розкладом.
Розуміння обмежень вашого обладнання та інструментів із ЧПК
Точність верстата з ЧПУ та її вплив на допуски
Можливості обладнання з ЧПК, що використовується, є вирішальним фактором у визначенні рівня точності, якого можна досягти під час процесу обробки. Різні типи верстатів з ЧПК мають різний ступінь точності, тому важливо розуміти обмеження верстатів, які використовуються, щоб уникнути встановлення нереалістичних очікувань допуску.
Наприклад, високоякісні фрези чи токарні верстати з ЧПК, що використовуються в аерокосмічній або медичній промисловості, можуть досягати таких жорстких допусків, як ±0,001 мм. У цих верстатах використовуються передові технології, такі як багатоосьове фрезерування, лазерне калібрування та системи зворотного зв’язку в реальному часі для підтримки надзвичайної точності.
З іншого боку, верстати з ЧПК загального призначення можуть бути нездатними підтримувати такі жорсткі допуски, і досяжна точність може становити лише ±0,05 мм або ±0,1 мм. Важливо узгодити необхідні допуски деталі з можливостями доступного обладнання з ЧПК, щоб гарантувати, що виробництво є здійсненним і економічно ефективним.
Вибір правильного верстату з ЧПК для роботи
Вибір правильного верстата з ЧПК для роботи є життєво важливим для досягнення бажаного допуску. Наприклад, якщо необхідний допуск є вузьким і деталь має складну геометрію, може знадобитися інвестувати у високоточні верстати, такі як токарні верстати з ЧПК або 5-осьові фрези. Ці верстати пропонують можливість обробляти складні деталі з мінімальними помилками, але вони мають вищі початкові витрати та довший час виробництва.
Однак для більш простих деталей із меншими допусками може бути достатньо стандартного фрезерного верстата з ЧПК. Вибір правильної машини на основі необхідних допусків може допомогти оптимізувати виробництво, зменшити витрати та забезпечити відповідність деталі стандартам якості.
Інструменти та знос інструментів
Якість і стан інструментів, які використовуються при обробці з ЧПК, також відіграють значну роль у точності кінцевого продукту. З часом інструменти можуть зношуватися, що призводить до зміни розмірів і відхилень від заданих допусків. Тому регулярне технічне обслуговування та своєчасна заміна інструментів мають вирішальне значення для підтримки незмінних результатів, особливо під час обробки деталей із жорсткими допусками.
Крім того, матеріал і покриття інструменту можуть впливати на його довговічність і точність. Наприклад, твердосплавні інструменти, як правило, зберігають свою гостроту та стабільність розмірів з часом, що робить їх кращим вибором для високоточної обробки з ЧПУ. Інструменти з покриттям, наприклад з покриттям з нітриду титану (TiN) або алмазоподібного вуглецю (DLC), також можуть допомогти зменшити знос і подовжити термін служби інструменту, що особливо важливо під час обробки складних матеріалів або виготовлення деталей із жорсткими допусками.
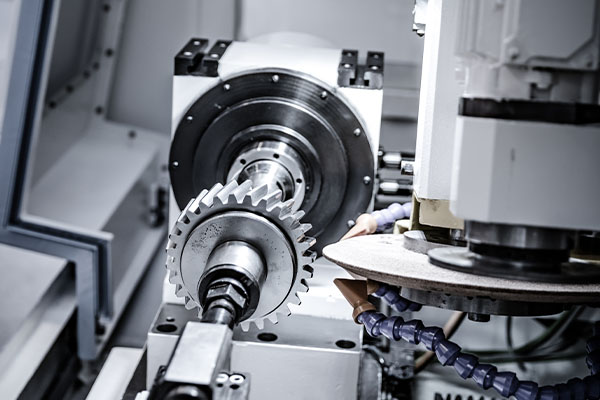
Оптимізація допусків для швидшого виконання робіт і зниження витрат
Баланс між точністю та ефективністю
Хоча жорсткі допуски необхідні для певних застосувань, вони можуть призвести до більш тривалого часу виконання та вищих витрат на виробництво. Тому одним із ключових завдань обробки з ЧПК є пошук правильного балансу між точністю та ефективністю. Досягнення необхідних допусків при збереженні низьких витрат на виробництво та збереженні швидкого часу виконання є важливим для задоволення вимог клієнтів і збереження конкурентоспроможності на ринку.
Один із способів оптимізувати допуски, зберігаючи ефективність, — це зосередитися на критичних розмірах деталі. Не всі характеристики деталі повинні відповідати найжорсткішим допускам. Визначаючи, які розміри є найбільш важливими для функціональності деталі, і застосовуючи більш жорсткі допуски лише там, де це необхідно, виробники можуть скоротити час і витрати на обробку без шкоди для продуктивності деталі.
Оптимізація процесу обробки
Щоб оптимізувати час обробки та зменшити витрати, виробники також повинні розглянути питання про оптимізацію процесу обробки. Цього можна досягти шляхом вибору правильних стратегій обробки, таких як використання найбільш відповідних ріжучих інструментів, регулювання швидкості подачі та оптимізація траєкторії інструменту. Верстати з ЧПК, які мають розширені можливості автоматизації, такі як пристрої для зміни інструментів або автоматизовані системи завантаження, також можуть допомогти скоротити час, витрачений на виконання непродуктивних завдань, ще більше прискорюючи процес.
Іншим ефективним способом оптимізації допусків є використання передових технологій виробництва, таких як адитивне виробництво або гібридна механічна обробка. Ці методи часто можуть досягти того ж рівня точності, що й традиційна обробка з ЧПК, одночасно зменшуючи відходи матеріалу, знос інструменту та час виробництва.
Реальні приклади викликів толерантності та їх вирішення
Приклад 1: Аерокосмічний компонент із жорсткими допусками
В аерокосмічному виробництві такі деталі, як компоненти двигуна та конструктивні елементи, повинні відповідати надзвичайно жорстким допускам, щоб забезпечити безпеку та продуктивність. Один із реальних прикладів пов’язаний із виготовленим на замовлення алюмінієвим кронштейном, який використовується в системі шасі літака. Допуск, необхідний для цієї деталі, становив ±0,01 мм, що викликало труднощі через здатність матеріалу до теплового розширення та складну геометрію конструкції.
Щоб відповідати жорстким вимогам допуску, виробник використав високоточний 5-осьовий верстат з ЧПК з лазерним калібруванням. Крім того, вони впровадили багатоетапний процес обробки, який включав точну чорнову обробку, напівчистову обробку та чистові операції. Деталь також пройшла кілька раундів контролю якості за допомогою координатно-вимірювальної машини (CMM), щоб переконатися, що вона відповідає необхідним специфікаціям.
Приклад 2: Компонент медичного пристрою зі складною геометрією
У галузі виробництва медичних пристроїв такі компоненти, як хірургічні інструменти та імплантати, вимагають високої точності, щоб забезпечити їх правильне та безпечне функціонування. Одним із прикладів була обробка титанового колінного імплантату, яка вимагала складних геометричних допусків, включаючи точні допуски на округлість і позиційні допуски для отворів для гвинтів.
Щоб досягти цих допусків, виробник використовував токарний верстат з ЧПК Swiss з можливостями живого інструменту. Це дозволило їм обробляти деталь за одну установку, зменшуючи ризик помилок, спричинених зміною позиції. Потім деталь перевіряли за допомогою високоточної оптичної вимірювальної системи, щоб переконатися, що дотримані всі геометричні допуски.
Контроль якості: забезпечення точності та узгодженості в обробці з ЧПУ
Важливість ретельної перевірки
Контроль якості відіграє життєво важливу роль у забезпеченні того, щоб деталі відповідали встановленим допускам і стандартам. При обробці з ЧПУ перевірка починається під час процесу налаштування та триває протягом усього виробничого циклу. Багато виробників використовують координатно-вимірювальні машини (КІМ) і системи лазерного сканування для точного вимірювання деталей і виявлення будь-яких відхилень від бажаних характеристик.
Перевірка також може включати візуальні перевірки, оцінку якості поверхні та функціональне тестування, залежно від передбачуваного використання деталі. Для деталей з особливо жорсткими допусками можуть знадобитися додаткові етапи перевірки, щоб переконатися, що під час процесу обробки не відбуваються зміни.
Роль автоматизованих систем контролю
З розвитком технологій багато виробників тепер покладаються на автоматизовані системи перевірки для контролю точності деталей, виготовлених на верстаті з ЧПК. Ці системи використовують лазери, камери чи інші датчики для постійної перевірки розмірів деталей під час їх виготовлення. Автоматизована перевірка не тільки покращує точність, але й прискорює процес контролю якості, дозволяючи виробникам завчасно виявляти помилки та запобігати дорогим помилкам.
Постійне вдосконалення та цикли зворотного зв’язку
Окрім офіційних перевірок, виробники повинні впроваджувати програми постійного вдосконалення для моніторингу продуктивності обробки з часом. Відстежуючи ключові показники, такі як знос інструменту, продуктивність машини та точність виробництва, виробники можуть визначити області, які потребують вдосконалення, і внести необхідні коригування, щоб постійно підтримувати жорсткі допуски.
Роль допусків у індивідуальних замовленнях обробки
Індивідуальна обробка та специфікації допусків
Розміщуючи індивідуальні замовлення на обробку, клієнти повинні чітко повідомити свої вимоги щодо допуску, щоб уникнути непорозумінь або дорогих помилок. Надання детальних креслень із зазначенням бажаних допусків для кожної особливості деталі допоможе гарантувати, що процес обробки проходить гладко. Клієнти також повинні співпрацювати зі своїми партнерами-виробниками, щоб визначити, чи можна досягти зазначених допусків протягом заданого періоду часу та бюджету.
Співпраця з постачальниками ЧПУ
Співпраця між замовником і постачальником має вирішальне значення для забезпечення чіткого розуміння та дотримання допусків. Це може включати обговорення вибору матеріалів, перегляд можливостей обладнання з ЧПК і забезпечення оптимізації конструкції деталей як для технологічності, так і для вимог допуску.
Постачальники часто можуть надати цінну інформацію про те, як скоригувати конструкції деталей, щоб полегшити їх обробку, але при цьому відповідати специфікаціям допуску. Працюючи разом, виробники та клієнти можуть досягти найкращого балансу точності, вартості та часу виконання.

поширені запитання
Які найпоширеніші допуски для обробки з ЧПК?
Найпоширеніші допуски для обробки з ЧПУ діапазон від ±0,05 мм до ±0,5 мм, залежно від складності та матеріалу деталі. Більш жорсткі допуски, наприклад ±0,01 мм, зазвичай потрібні для високоточних застосувань, таких як аерокосмічні чи медичні пристрої.
Як допуски впливають на витрати на обробку з ЧПК?
Більш жорсткі допуски зазвичай збільшують витрати на обробку з ЧПК, оскільки вони вимагають більш вдосконаленого обладнання, більш тривалого часу обробки та більш ретельного контролю. Менші допуски можуть допомогти скоротити витрати та час виробництва.
Чи може обробка з ЧПК досягти жорстких допусків для всіх матеріалів?
У той час як для багатьох матеріалів, таких як метали, можна досягти жорстких допусків за допомогою обробки з ЧПУ, деякі матеріали, як-от пластмаси та композити, складніше обробляти з високою точністю через їхні властиві властивості. Важливо вибрати відповідний матеріал для необхідного допуску.
Як я можу зменшити вартість обробки деталей із жорсткими допусками?
Щоб зменшити витрати, зосередьтеся на оптимізації конструкції для технологічності. Вказуйте допуски лише там, де вони необхідні для функціонування деталі, і вибирайте правильний процес обробки та обладнання для роботи. Співпраця з виробником також може допомогти визначити сфери, де витрати можна знизити без шкоди для якості.
Які інструменти найкраще підходять для досягнення вузьких допусків при обробці з ЧПК?
Твердосплавні інструменти та інструменти з покриттям, наприклад з покриттям з нітриду титану (TiN), ідеально підходять для досягнення жорстких допусків. Ці інструменти довше зберігають свою гостроту, зменшуючи ризик зносу інструменту та зміни розмірів.