вступ
Обробка великих деталей представляє унікальні виклики та вимагає спеціальних методів та обладнання. Оскільки промисловість продовжує вимагати високоточних і високоякісних великих компонентів, виробники повинні адаптуватися, щоб задовольнити ці потреби, що розвиваються. У цій статті ми досліджуємо проблеми, з якими стикаємося під час обробки великих деталей, інструменти та методи, які використовуються для їх подолання, а також найкращі практики для забезпечення ефективності та якості. Незалежно від того, берете ви участь у виробництві, механічній обробці чи працюєте з великомасштабними проектами, розуміння цих проблем і рішень може дати значні переваги. Давайте зануримося в це й побачимо, як правильний підхід може змінити все.
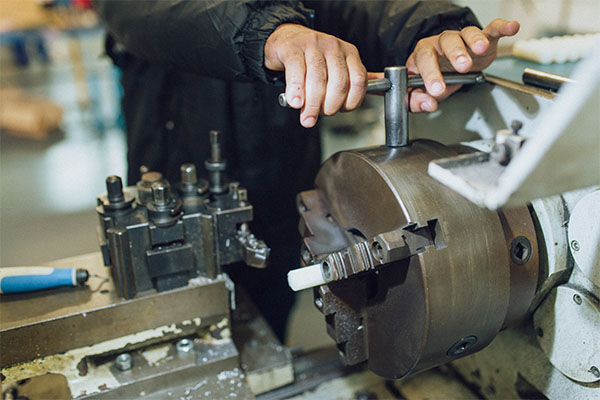
1. Які основні проблеми при обробці великих деталей?
Коли мова заходить про обробку великих деталей, проблеми є багатогранними. Першою основною перешкодою є розмір і вага компонентів. Більші деталі часто вимагають машин з більшими можливостями, і керування збільшеними зусиллями під час обробки може призвести до ускладнень.
Але ось головне: досягти високої точності великих деталей непросто. Для більших деталей навіть незначні відхилення у вимірюванні можуть призвести до значних похибок. Однією з ключових проблем при обробці великих деталей є забезпечення того, щоб уся деталь залишалася вирівняною під час процесу. Зміни в позиціонуванні можуть призвести до дорогих помилок, тому правильне кріплення та затискання є критичними.
Ще однією проблемою є знос інструменту. Великі деталі потребують тривалого часу обробки, що призводить до більшого зносу інструменту. У таких ситуаціях довговічність ріжучих інструментів стає ще важливішою. Крім того, цей процес вимагає керування збільшеним тепловим розширенням і тепловою деформацією через тепло, що виділяється під час процесу різання.
Ще одна річ: обробка та транспортування великих деталей може бути такою ж складною, як і сама обробка. Переміщення великих деталей між різними машинами, етапами процесу або навіть до станцій кінцевої перевірки може створити логістичні проблеми, які можуть вплинути на робочий процес і терміни.
Щоб подолати ці проблеми, виробники часто покладаються на високоточні верстати з ЧПК і досвідчених операторів. Однак ретельне планування та точність необхідні для забезпечення правильної обробки великих деталей.
Таблиця 1: Основні проблеми при обробці великих деталей
Виклик | Вплив | Рішення |
---|---|---|
Розмір і вага | Підвищені зусилля під час механічної обробки | Використовуйте важкі машини та пристосування |
Досягнення точності | Можливість зміщення та помилок | Використовуйте передові системи ЧПУ та вимірювальні системи |
Знос інструменту | Зменшення терміну служби інструменту через більш тривалу обробку | Вибирайте міцні інструменти та керуйте зносом інструментів |
Теплове розширення і деформація | Вплив на точність обробки | Застосуйте ефективні методи охолодження |
Обробка та транспортування | Ризик затримок або пошкодження під час переміщення | Використовуйте спеціалізоване підйомне обладнання та оптимізацію робочого процесу |
2. Як правильно вибрати інструменти для обробки великих деталей?
Вибір правильних інструментів для обробки великих деталей має вирішальне значення для ефективності та точності. Це не просто вибір будь-якого інструменту; мова йде про вибір правильного типу ріжучого інструменту для матеріалу та поставленого завдання.
Яка справжня історія? Ключ до успіху полягає в розумінні унікальних вимог обробки великих деталей. Процес вибору інструменту починається з матеріалу, з яким ви працюєте. Більш тверді матеріали, такі як титан або інструментальна сталь, вимагають міцніших інструментів із вищою потужністю різання. З іншого боку, м’які матеріали, як-от алюміній, можуть забезпечити більшу швидкість різання та менший знос інструментів.
Міцність інструменту є критичним фактором, особливо при роботі з важкими великими заготовками. Інструменти повинні бути достатньо міцними, щоб витримувати високі сили різання, пов’язані з обробкою великих деталей. Крім довговічності, важливу роль відіграє геометрія ріжучого інструменту. Інструмент із неправильною геометрією може призвести до надмірного зносу, підвищення температури та поганої обробки.
Готові до хорошої частини? Не менш важливим є вибір правильних швидкостей різання та подачі. Під час обробки великих деталей важливо регулювати швидкість різання та подачі, щоб збалансувати продуктивність із довговічністю інструменту. Використання занадто високої швидкості може призвести до надмірного накопичення тепла, тоді як занадто низька швидкість може призвести до неефективності та збільшення часу обробки.
Іншим аспектом є використання багатофункціональних систем, які можуть підвищити продуктивність, дозволяючи операторам швидко перемикатися між різними інструментами для різних операцій. Крім того, вкрай важливо переконатися, що інструмент може відповідати розмірам заготовки, оскільки деякі інструменти можуть не охопити всі ділянки великих деталей.
Таблиця 2: Фактори вибору інструменту для обробки великих деталей
Фактор | Вплив | Розгляд |
---|---|---|
Тип матеріалу | Впливає на міцність інструменту та силу різання | Виберіть відповідний матеріал інструменту |
Міцність інструменту | Впливає на довговічність і продуктивність | Вибирайте міцні інструменти для інтенсивного використання |
Геометрія інструменту | Впливає на ефективність різання та довговічність інструменту | Оптимізація геометрії для конкретних завдань |
Швидкості та подачі різання | Впливає на час обробки та термін служби інструменту | Збалансуйте швидкість різання з довговічністю інструменту |
Сумісність інструментів | Визначає здатність досягти всіх частин частини | Використовуйте регульовані або багатофункціональні системи |
3. Які найкращі практики для налаштування великих деталей у верстатах з ЧПК?
Налаштування великих деталей на верстатах з ЧПК вимагає ретельного планування та виконання. Процес починається із закріплення заготовки на станині верстата. Але ось головне: якщо деталь не закріплена належним чином, навіть найменші рухи під час обробки можуть спричинити значні відхилення, що призведе до дефектів або браку. Правильний затиск і кріплення є абсолютно важливими при обробці великих деталей.
Першим кроком у процесі налаштування є визначення відповідної системи затиску. Для великих деталей виробники часто покладаються на потужні затискні системи, які можуть забезпечити рівномірний тиск по всій заготовці. Ці системи допомагають підтримувати положення заготовки під час обробки, запобігаючи будь-яким рухам, які можуть вплинути на точність.
Після того, як деталь надійно закріплена, наступним завданням є вирівнювання. Переконайтеся, що деталь ідеально вирівняна з ріжучими інструментами машини, що має вирішальне значення для досягнення точних результатів. Будь-яке зміщення може призвести до неточностей розмірів, які можуть посилюватися в процесі обробки.
Яка тут справжня історія? Час налаштування великих деталей часто може бути досить тривалим. Але час, щоб переконатися, що все ідеально вирівняно та безпечно з самого початку, зрештою заощадить час і гроші, запобігаючи помилкам під час обробки. Крім того, дуже важливо відкалібрувати верстат з ЧПК перед початком будь-яких операцій обробки, щоб переконатися, що він працює з оптимальною продуктивністю.
Інша найкраща практика полягає в тому, щоб регулярно перевіряти на знос як верстат, так і інструменти протягом усього процесу обробки. Регулярна перевірка інструментів і деталей забезпечить ефективність процесу обробки та виявлення будь-яких проблем до того, як вони стануть серйозними.
Таблиця 3: Найкращі методи налаштування великих деталей з ЧПК
Практика | Вигода | Найкращі практичні поради |
---|---|---|
Надійне затискання | Запобігає руху та забезпечує точність | Використовуйте міцні, рівномірно розподілені затискні системи |
Правильне вирівнювання | Забезпечує точність під час обробки | Використовуйте інструменти та методи точного вирівнювання |
Калібрування верстата з ЧПУ | Забезпечує роботу машини в оптимальних налаштуваннях | Регулярно калібруйте для досягнення найкращих результатів |
Перевірка інструменту та деталей | Запобігає помилкам і забезпечує якість | Проводьте регулярні перевірки інструментів і деталей |
4. Як досягти точності при обробці великих деталей?
Досягнення точності в обробка великих деталей є однією з найбільш серйозних проблем, з якими стикаються виробники. Чим більша деталь, тим важче підтримувати точні розміри та допуски протягом усього процесу обробки.
Готові до хорошої частини? Одним із найефективніших способів забезпечення точності є використання вдосконалених верстатів з ЧПК, які містять високоточні вимірювальні системи. Ці системи постійно контролюють розміри деталі під час обробки, надаючи оператору зворотний зв’язок у реальному часі. У разі виявлення будь-яких відхилень від бажаних розмірів система може внести корективи на ходу, гарантуючи, що кінцевий продукт відповідає необхідним специфікаціям.
Ще один спосіб досягнення точності у великих деталях — використання високоякісного інструменту. Чим гостріше інструмент, тим точніше будуть різи. З часом інструменти зношуються, що може призвести до неточностей готової деталі. Використання інструментів із довшим терміном служби та регулярна перевірка стану інструментів мають важливе значення для підтримки якості та точності великих деталей.
Крім того, контроль температури відіграє ключову роль у підтримці точності. При обробці великих деталей у процесі виділяється значна кількість тепла, що може призвести до термічної деформації. Це особливо проблематично з великими деталями, оскільки навіть невеликі термічні деформації можуть спричинити значні зміни в розмірах деталі. Ефективні системи охолодження є обов’язковими для підтримки стабільної температури заготовки та зменшення ризику теплового розширення.
Іншим фактором збереження точності є правильне програмування. Програми ЧПК для великих деталей повинні бути ретельно протестовані та оптимізовані, щоб гарантувати точність усіх шляхів різання. Навіть незначна помилка в програмі може призвести до істотних дефектів кінцевого продукту.
Таблиця 4: Методи досягнення точності при обробці великих деталей
Техніка | Вплив | Розгляд |
---|---|---|
Вимірювальні системи ЧПК | Забезпечує зворотній зв'язок у реальному часі для точності | Інвестуйте у високоточні системи |
Високоякісний інструмент | Покращує точність і ефективність різання | Використовуйте міцні, гострі інструменти для довшого терміну служби |
Контроль температури | Запобігає термічній деформації | Використовуйте ефективні системи охолодження |
Оптимізоване програмування ЧПУ | Забезпечує точні траєкторії різання | Ретельно тестуйте програми перед використанням |
5. Які матеріали зазвичай використовуються при обробці великих деталей?
При обробці великих деталей вибір матеріалу відіграє вирішальну роль у визначенні як складності, так і ефективності процесу. Не всі матеріали підходять для великомасштабної обробки, і вибір правильного може зробити або порушити успіх проекту.
Яка справжня історія? Найбільш часто використовувані матеріали для обробки великих деталей включають різні метали, такі як сталь, алюміній і титан. Сталь, будучи одним із найпоширеніших матеріалів у виробництві, відома своєю міцністю та довговічністю. Однак його також може бути складно обробляти, особливо великих деталей, через його твердість і схильність до виділення тепла під час обробки.
З іншого боку, алюміній набагато легше обробляти, і він зазвичай використовується в таких галузях промисловості, як аерокосмічна та автомобільна для великих компонентів. Він легкий, що робить його ідеальним для великих деталей, які потребують мобільності, але він не такий міцний, як сталь або титан. Тим не менш, його нижча вартість і легкість обробки роблять його популярним вибором для багатьох застосувань.
Титан, хоч і дорожчий, часто використовується для застосувань, які вимагають високого співвідношення міцності до ваги, наприклад, в аерокосмічній галузі. Однак обробка титану пов’язана з власними труднощами, включаючи вищі сили різання та знос інструменту. Для успішної роботи з титаном часто потрібні спеціальні інструменти та методи різання.
Нарешті, для деяких великих деталей може знадобитися використання композитних матеріалів або пластику, залежно від застосування. Ці матеріали часто легші та менш дорогі, але вони можуть не мати такого ж рівня міцності, як метали.
Таблиця 5: Загальні матеріали для обробки великих деталей
матеріал | характеристики | Додатки |
---|---|---|
сталь | Міцний, довговічний, складніше в обробці | Будівництво, автомобілебудування |
Алюміній | Легкий, легший у верстаті, економічний | Аерокосмічна, автомобільна |
Титан | Високе співвідношення міцності до ваги, дорого | Аерокосмічні, медичні прилади |
Композиційні матеріали та пластмаси | Легка, менша міцність | Споживчі товари, автомобілебудування |
Висновок
Підсумовуючи, обробка великих деталей пов’язана з набором проблем, але розуміння цих перешкод і впровадження правильних стратегій може призвести до успішних результатів. Ключ до подолання цих проблем полягає у виборі правильних інструментів, управлінні точністю, виборі відповідних матеріалів і дотриманні найкращих практик у налаштуванні та експлуатації. Враховуючи ці фактори, виробники можуть зменшити кількість помилок, підвищити ефективність і забезпечити високоякісні результати в своїх проектах обробки великих деталей. Правильний підхід у поєднанні з новітніми технологіями та техніками може допомогти подолати ці проблеми та покращити операції обробки в різних галузях.
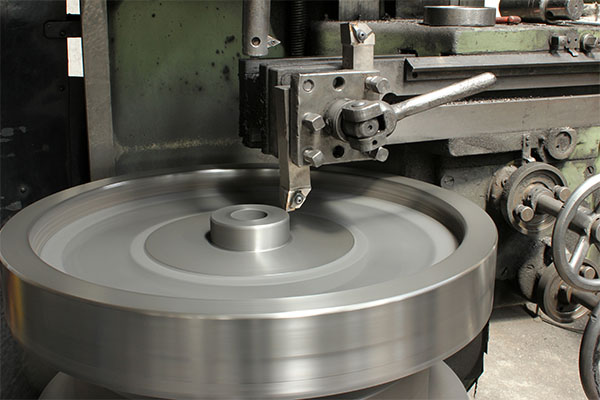
6. Як контролювати тепло і мінімізувати термічну деформацію?
Контроль нагрівання та мінімізація термічної деформації під час обробки великих деталей є вирішальним фактором для досягнення точності та збереження якості деталей. Процес обробки великих деталей генерує значну кількість тепла через дію різання, тертя та видалення матеріалу. Якщо цим теплом не керувати належним чином, це може призвести до теплового розширення або деформації, що вплине на кінцеві розміри деталі.
Яка справжня історія? Найефективніший спосіб контролювати тепло — це правильні методи охолодження. Охолоджуючі рідини використовуються для поглинання тепла, що утворюється під час обробки, і розсіювання його, запобігаючи надмірному нагріванню. Існує кілька типів охолоджувальних рідин, таких як масла, розчини на водній основі та повітряне охолодження, кожен з яких підходить для різних застосувань. Тип охолоджувальної рідини, який ви обираєте, залежить від матеріалу, який ви обробляєте, швидкості різання та використовуваної машини.
Іншим ключовим фактором у контролі тепла є вибір правильних параметрів різання. Надто високі швидкості різання можуть призвести до надмірного виділення тепла, тоді як надто низькі швидкості різання можуть призвести до неефективного видалення матеріалу. Знаходячи оптимальну швидкість різання для матеріалу та розміру деталі, виробники можуть зменшити ризик деформації, спричиненої нагріванням.
Але ось головне: вибір інструментального матеріалу є ще одним критичним фактором. Деякі інструменти розроблені таким чином, щоб витримувати високі температури, що зменшує ймовірність термічної деформації під час обробки. Наприклад, твердосплавні інструменти витримують більш високі температури, ніж швидкорізальна сталь, що робить їх ідеальними для операцій обробки з високою температурою.
Термічну деформацію також можна мінімізувати за допомогою керування машиною. Сучасні верстати з ЧПК оснащені вдосконаленими системами охолодження та датчиками температури, які відстежують температуру під час обробки та коригують, якщо це необхідно, для підтримки постійної продуктивності. Деякі машини навіть оснащені функціями температурної компенсації, які дозволяють їм у режимі реального часу коригувати процес обробки, гарантуючи мінімізацію теплового впливу.
Таблиця 6: Методи охолодження для управління теплом при обробці великих деталей
Спосіб охолодження | Ефективність | Розгляд |
---|---|---|
Охолоджуючі рідини на масляній основі | Ефективний при високих швидкостях різання | Потребує належного управління утилізацією |
Охолоджуючі рідини на водній основі | Зазвичай використовується для точного різання | При неправильному догляді може піддатися корозії |
Повітряне охолодження | Ідеально підходить для легких надрізів і невеликих деталей | Менш ефективний для великих деталей або високошвидкісного різання |
Вбудовані системи охолодження машини | Забезпечує охолодження в режимі реального часу під час роботи | Забезпечує послідовне керування температурою |
7. Які ключові міркування для обробки поверхні великих деталей?
Досягнення бажаної якості поверхні великих деталей є одним із найважливіших аспектів механічної обробки. Оздоблення поверхні має вирішальне значення як для функціональності, так і для естетики деталі. Це безпосередньо впливає на такі фактори, як тертя, зносостійкість і те, як деталь взаємодіє з іншими компонентами в її збірці.
Яка справжня історія? Поверхня, яку ви досягнете, залежить від різних факторів, у тому числі від використовуваного ріжучого інструменту, процесу обробки та матеріалу, з яким працюєте. Наприклад, працюючи з м’якшими матеріалами, такими як алюміній, ви можете досягти більш гладкої обробки за допомогою вищих швидкостей різання, тоді як для більш твердих матеріалів, таких як сталь, може знадобитися менша швидкість різання та більш тонкий інструмент для досягнення бажаної обробки.
Одним із найефективніших способів контролю якості поверхні є вибір інструменту. Інструменти з гострими краями та точною геометрією можуть допомогти створити більш гладку поверхню за рахунок зменшення вібрації та сил різання під час обробки. Крім того, вибір правильного покриття для ваших інструментів, наприклад твердосплавного або керамічного, може зменшити тертя та покращити якість обробки.
Готові до хорошої частини? Іншим ключовим фактором для досягнення якісної обробки поверхні є контроль вібрації під час обробки. Великі деталі більш сприйнятливі до вібрації через їх розмір і вагу, і навіть невеликі вібрації можуть спричинити дефекти на поверхні. Щоб мінімізувати вібрацію, виробники використовують такі методи, як системи амортизації машин або спеціальні кріплення для ефективнішого закріплення деталей.
Нарешті, процеси після механічної обробки, такі як шліфування, полірування або хонінгування, можуть ще більше покращити якість поверхні великих деталей. Ці процеси фінішної обробки зазвичай використовуються для деталей, які вимагають надгладкої обробки, як-от тих, що використовуються в аерокосмічній або автомобільній промисловості.
Таблиця 7: Методи обробки поверхні для обробки великих деталей
Техніка | Ефективність | Розгляд |
---|---|---|
Гострі інструменти та геометрія | Зменшує вібрацію та покращує гладкість поверхні | Потрібна точна заточка інструменту |
Покриття для інструментів (наприклад, твердосплавні) | Зменшує тертя і знос | Вибір покриття залежить від матеріалу |
Системи амортизації машин | Запобігає дефектам поверхні через вібрацію | Потрібне правильне налаштування машини |
Процеси після механічної обробки (шліфування, хонінгування) | Покращує якість обробки для високоточних застосувань | Займає багато часу та збільшує витрати |
8. Як розмір заготовки впливає на процес обробки?
Розмір заготовки суттєво впливає майже на кожен аспект процесу обробки, від типу використовуваного обладнання до часу, необхідного для виконання роботи. Більші деталі вимагають більш досконалого обладнання, довшого часу обробки та обережнішого поводження для підтримки точності.
Яка справжня історія? Однією з перших речей, яка змінюється під час обробки великих деталей, є тип використовуваного обладнання. Стандартні верстати з ЧПК можуть не працювати з більшими деталями, тому виробникам часто доводиться інвестувати в спеціальне обладнання, наприклад портальні верстати, великі вертикальні або горизонтально-розточні фрези. Ці верстати призначені для роботи з більшими заготовками та забезпечують необхідну стабільність для роботи зі збільшеними зусиллями різання.
Іншим фактором є час, необхідний для обробки. Великі деталі зазвичай обробляються довше через їхні розміри та збільшення кількості операцій, необхідних для завершення деталі. Довший час обробки збільшує ризик зносу інструменту, що може вплинути на точність і якість. Крім того, великі деталі потребують більшого охолодження та змащування, щоб контролювати накопичення тепла під час процесу обробки.
Але ось головне: робота з великими деталями є такою ж важливою, як і сам процес обробки. Великі деталі можуть бути громіздкими, і їх важко транспортувати між різними машинами або етапами виробництва. Спеціальне підйомне обладнання та пристосування часто необхідні для забезпечення безпечного переміщення частин без пошкодження.
Нарешті, розмір деталі також може впливати на точність обробки. Більші деталі більш сприйнятливі до вібрації, теплового розширення та прогинів під час обробки, що може призвести до неточностей. Важливо використовувати правильне налаштування, інструменти та калібрування машини, щоб гарантувати, що деталь відповідає необхідним специфікаціям.
Таблиця 8: Вплив розміру заготовки на обробку
Фактор | Вплив | Розгляд |
---|---|---|
Розмір обладнання | Визначає тип використовуваної машини | Потрібні машини великої потужності |
Час обробки | Більший час обробки та знос інструменту | Збільшує експлуатаційні витрати |
Обробка та транспортування | Підвищені труднощі при переміщенні великих частин | Використовуйте спеціалізоване підйомно-транспортне обладнання |
Точність | Великі деталі більш чутливі до вібрації та термічного впливу | Впровадити контроль вібрації та точне налаштування |
9. Якими є витрати на обробку великих деталей?
Обробка великих деталей може бути значно дорожчою, ніж обробка менших компонентів через різні фактори, включаючи вартість матеріалів, інструментів, робочої сили та машинного часу. Розуміння витрат має вирішальне значення для виробників, щоб оптимізувати свою діяльність і збільшити прибутковість.
Яка справжня історія? Одним із головних чинників витрат на обробку великих деталей є ціна матеріалів. Великі деталі потребують більше сировини, що збільшує загальні витрати на матеріал. Крім того, складність обробки великих деталей може призвести до збільшення витрат на робочу силу. Для налаштування, контролю та експлуатації машин, які можуть обробляти великі деталі, потрібна кваліфікована робоча сила, і цей досвід має велике значення.
Витрати на інструмент також зростають із розміром деталі. Більші деталі потребують більш міцних інструментів, які можуть витримувати збільшені сили різання, що може бути дорожчим. Довший час обробки великих деталей також підвищує загальну вартість. Довший час обробки призводить до більшого споживання енергії, збільшення зносу машин і більшого споживання охолоджуючих рідин і мастильних матеріалів.
Готові до хорошої частини? Одним із способів зниження витрат на обробку великих деталей є оптимізація процесу обробки. Ретельно підбираючи правильні інструменти, матеріали та параметри обробки, виробники можуть зменшити відходи, звести до мінімуму знос інструментів і скоротити час обробки. Автоматизація є ще одним потенційним заходом економії. Використання роботів або автоматизованих систем для обробки великих деталей може зменшити витрати на робочу силу та підвищити ефективність.
Нарешті, виробники також повинні враховувати можливість утилізації та переробки. Великі деталі дорожче утилізувати, і будь-яка доопрацювання, необхідна після механічної обробки, може значно збільшити вартість кінцевого продукту. Суворий контроль якості протягом усього процесу може допомогти зменшити ці витрати.
Таблиця 9: Фактори витрат на обробку великих деталей
Фактор | Вплив | Розгляд |
---|---|---|
Матеріальні витрати | Більше використання матеріалу для великих деталей | Потрібне ефективне планування матеріалів |
Витрати на оплату праці | Для більших деталей потрібна кваліфікована робоча сила | Інвестуйте в навчання або автоматизацію |
Витрати на інструменти | Для більших деталей потрібні більш надійні інструменти | Вибирайте інструменти, які забезпечують найкращу вартість |
Час обробки | Довший час обробки збільшує витрати | Оптимізуйте параметри різання та машинний час |
Лом і переробка | Збільшення витрат, якщо деталі списані або перероблені | Запровадити контроль якості, щоб мінімізувати помилки |
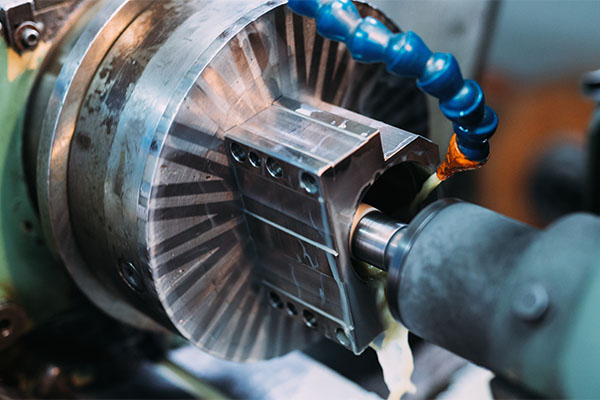
10. Які останні технологічні досягнення в обробці великих деталей?
Удосконалення технологій продовжує змінювати сферу обробки великих деталей. Нові інновації в машинобудуванні, автоматизації та матеріалознавстві дозволяють виробникам досягти більшої точності, ефективності та економічності при роботі з великими деталями.
Яка справжня історія? Одним із найбільш значних досягнень останніх років є розробка багатоосьових верстатів з ЧПК. Ці верстати дозволяють виконувати більш складні розрізи та вищу точність при обробці великих деталей. Використовуючи кілька осей руху, виробники можуть обробляти більш складні елементи на великих деталях без необхідності змінювати положення заготовки.
Ще одним нововведенням є збільшення використання роботизації та автоматизації в обробці великих деталей. Роботів можна використовувати для таких завдань, як обробка матеріалів, заміна інструментів і перевірка, зменшуючи потребу в ручній праці та підвищуючи ефективність. Автоматизація також допомагає зменшити ризик людської помилки, забезпечуючи послідовність і точність процесу обробки.
Готові до хорошої частини? Штучний інтелект і машинне навчання починають відігравати більш значну роль у обробці великих деталей. Ці технології можна використовувати для оптимізації параметрів обробки в режимі реального часу, забезпечуючи ефективність і точність процесу різання. ШІ також може прогнозувати знос інструменту, дозволяючи виробникам планувати технічне обслуговування до того, як виникнуть проблеми, скорочуючи час простою та підвищуючи загальну ефективність.
Крім того, розробляються нові матеріали та покриття для покращення продуктивності ріжучих інструментів. Ці інновації допомагають зменшити тертя, збільшити термін служби інструменту та покращити загальну якість оброблених деталей. Досягнення в адитивному виробництві також пропонують нові способи створення великих деталей, пропонуючи потенційну економію коштів і скорочення відходів.
Таблиця 10: Технологічні досягнення в обробці великих деталей
технології | Вплив | Розгляд |
---|---|---|
Багатоосьові верстати з ЧПК | Підвищена точність і складність | Потрібне розширене налаштування машини та навчання |
Робототехніка та автоматизація | Зменшує фізичну працю та підвищує ефективність | Інвестуйте в роботизовані системи для обробки матеріалів і зміни інструментів |
ШІ та машинне навчання | Оптимізує параметри різання та прогнозує знос інструменту | Впроваджуйте системи ШІ для оптимізації процесів у реальному часі |
Нові матеріали та покриття | Зменшує тертя та збільшує термін служби інструменту | Інвестуйте в високоякісні покриття |
Адитивне виробництво | Зменшує матеріальні відходи та вартість | Ідеально підходить для прототипів або малосерійного виробництва |
11. Як ви забезпечуєте контроль якості при обробці великих деталей?
Забезпечення контролю якості при обробці великих деталей має важливе значення для виготовлення деталей, які відповідають необхідним специфікаціям і належним чином функціонують у призначених для них сферах застосування. Контроль якості — це не лише перевірка розмірів; це передбачає цілісний підхід, який включає моніторинг усього процесу обробки.
Готові до хорошої частини? Одним із ключових інструментів забезпечення якості є використання прецизійних вимірювальних систем. Ці системи можна інтегрувати у верстати з ЧПК або використовувати як автономні інструменти для перевірки розмірів деталей у режимі реального часу. Це гарантує, що будь-які відхилення від бажаних специфікацій будуть виявлені на ранніх стадіях процесу, зменшуючи ймовірність дефектів у кінцевій частині.
Іншим важливим аспектом контролю якості є використання передових методів контролю. Координатно-вимірювальні машини (CMM) зазвичай використовуються для перевірки великих деталей, оскільки вони можуть вимірювати точні розміри частини з високою точністю. КІМ використовують зонди, щоб торкатися різних точок на поверхні деталі та створювати 3D-модель деталі, яку можна порівняти з оригінальним дизайном.
Але ось головне: постійний моніторинг процесу обробки є важливим для підтримки якості. Багато верстатів з ЧПК сьогодні оснащені датчиками, які відстежують різні фактори, такі як температура, вібрація та сили різання під час обробки. Ці дані в режимі реального часу дозволяють операторам вносити необхідні зміни в процес, щоб переконатися, що деталь залишається в межах допуску.
Нарешті, життєво важливі регулярні аудити та перевірки. Навіть з найкращим обладнанням людська помилка все одно може статися. Необхідні регулярні перевірки інструментів, машин і кінцевої частини, щоб гарантувати, що всі аспекти процесу відповідають стандартам.
Таблиця 11: Методи контролю якості при обробці великих деталей
метод | Вплив | Розгляд |
---|---|---|
Системи прецизійних вимірювань | Забезпечує точні розміри під час обробки | Інтеграція з верстатами з ЧПК для перевірок у реальному часі |
Координатно-вимірювальні машини (КВМ) | Забезпечує детальний огляд великих деталей | Для інтерпретації результатів потрібні кваліфіковані оператори |
Системи моніторингу в режимі реального часу | Відстежує дані процесу та забезпечує узгодженість | Використовуйте датчики температури, вібрації та сили різання |
Регулярні аудити та перевірки | Забезпечує дотримання стандартів якості | Заплануйте часті перевірки протягом усього процесу |
12. Чим обробка великих деталей відрізняється від стандартної обробки?
Обробка великих деталей має кілька відмінностей у порівнянні з обробкою менших, більш стандартних компонентів. Хоча основні принципи механічної обробки залишаються незмінними, унікальні виклики та вимоги обробки великих деталей виділяють її.
Яка тут справжня історія? Однією з найбільших відмінностей є розмір задіяного обладнання. Великі деталі потребують набагато більших верстатів з ЧПК, які можуть працювати з розміром, вагою та складністю компонентів. Ці машини повинні витримувати сили, що виникають під час процесу обробки, що часто призводить до більш складних конструкцій машин і вищих початкових інвестицій.
З точки зору самого процесу обробки, великі деталі часто вимагають більше кроків, більшого часу обробки та частішої зміни інструменту. Як згадувалося раніше, це пов’язано з підвищеним зносом інструментів, потребою в більш тривалому часі різання та проблемами, пов’язаними з утриманням вирівняної заготовки.
Ще одна істотна відмінність — необхідна точність. У той час як дрібні деталі часто вимагають високої точності, великі деталі потребують ще більшої обережності та уваги для дотримання необхідних допусків. Найменше відхилення здебільшого може призвести до серйозних проблем, особливо в таких галузях, як аерокосмічна, автомобільна та оборонна.
Готові до хорошої частини? Великі деталі також потребують спеціального транспортування та логістики. Переміщення великих деталей між обробними центрами або на станції перевірки вимагає спеціального обладнання та може створювати додаткові ризики пошкодження або затримки.
Таблиця 12: Ключові відмінності між великою та стандартною обробкою деталей
Фактор | Обробка великих деталей | Стандартна обробка деталей |
---|---|---|
Розмір обладнання | Потрібні великі верстати з ЧПК | Використовує менші, більш стандартні машини |
Час обробки | Довший час обробки та більше операцій | Швидший час обробки та менше операцій |
Точність | Потрібна більш висока точність | Часто достатньо стандартної точності |
Транспортування та логістика | Потрібне спеціальне підйомно-транспортне обладнання | Легше в експлуатації та переміщенні |
Знос інструменту | Більше зношування інструменту через довший час обробки | Зменшення зносу інструменту в менших деталях |
13. Які найпоширеніші типи верстатів з ЧПК для обробки великих деталей?
При обробці великих деталей виробники повинні використовувати спеціалізовані верстати з ЧПК, призначені для роботи з більшими заготовками. Ці машини забезпечують необхідну точність і стабільність для обробки великих компонентів і гарантують, що вони відповідають необхідним специфікаціям.
Яка справжня історія? Найпоширенішим типом верстатів з ЧПК, які використовуються для обробки великих деталей, є портальна машина. Портальні машини розроблені з великою, жорсткою конструкцією, яка може підтримувати великі частини. Вони ідеально підходять для обробки великих плоских компонентів, таких як автомобільні деталі, фюзеляжі літаків і компоненти важкої техніки. Ці машини мають кілька осей руху, що дозволяє виконувати складні операції різання великих деталей.
Іншим часто використовуваним верстатом з ЧПК є горизонтально-розточувальний стан. Ці верстати використовуються для обробки великих важких деталей, які вимагають точного свердління та розточування. Горизонтально-розточні фрези можуть обробляти деталі, які є занадто великими для вертикальних верстатів, і їх можна використовувати для свердління великих отворів, фрезерування плоских поверхонь і навіть виконання повної механічної обробки масивних компонентів.
Готові до хорошої частини? Верстати вертикально-фрезерні також використовуються для обробки великих деталей, особливо для великих деталей, які вимагають точної обробки поверхні. Ці верстати можуть бути оснащені поворотними столами та іншими пристосуваннями для розміщення більших заготовок.
Інші спеціалізовані машини включають токарні центри і токарні верстати який може обробляти великі циліндричні деталі, а також 5-осьові верстати з ЧПУ які забезпечують неперевершену гнучкість при обробці великих складних деталей.
Таблиця 13: Поширені верстати з ЧПК для обробки великих деталей
Тип машини | Можливості | Додатки |
---|---|---|
Портальні машини | Велика, жорстка структура для складних розрізів | Аерокосмічна, автомобільна, важка техніка |
Горизонтально-розточувальні стани | Свердління та розточування великих важких деталей | Автомобілебудування, будівництво, енергетика |
Верстати вертикально-фрезерні | Точне фрезерування великих деталей | Аерокосмічна, автомобільна, оборонна |
Токарні та токарні верстати | Механічна обробка великих циліндричних деталей | Нафта і газ, космонавтика, автомобілебудування |
5-осьові верстати з ЧПУ | Висока гнучкість для складних деталей | Аерокосмічна промисловість, медичне обладнання, автомобільна промисловість |
14. Яких протоколів безпеки слід дотримуватися під час обробки великих деталей?
Безпека має першочергове значення при обробці великих деталей через розмір і вагу компонентів, а також складність використовуваного обладнання. Є кілька протоколів безпеки, яких виробники повинні дотримуватися, щоб захистити як працівників, так і обладнання.
Яка справжня історія? Першим кроком у забезпеченні безпеки є правильне налаштування машини. Перед початком будь-якої операції обробки оператори повинні переконатися, що всі компоненти належним чином закріплені та що машина функціонує належним чином. Калібрування машини має вирішальне значення, щоб переконатися, що ріжучі інструменти вирівняні правильно та немає ризику несправності машини.
Але ось головне: оператори також повинні знати про фізичні ризики, пов’язані з обробкою великих деталей. Ці деталі важкі, з ними важко працювати, тому для запобігання травмам потрібне спеціальне підйомне обладнання та опора. Використання відповідних підйомних інструментів і механізмів для переміщення великих частин може значно зменшити ризик нещасних випадків.
Іншим ключовим аспектом безпеки є засоби індивідуального захисту (ЗІЗ). Оператори повинні носити необхідні ЗІЗ, включаючи захисні окуляри, засоби захисту слуху та рукавички, щоб захистити себе від летючого сміття, високого рівня шуму та гострих країв. Крім того, переконатися, що робоча зона є чистою та вільною від перешкод, є важливою для забезпечення безпеки під час операцій обробки.
Готові до хорошої частини? Регулярне технічне обслуговування як машин, так і робочого середовища є життєво важливим для забезпечення безперервної безпеки. Машини слід регулярно обслуговувати, щоб уникнути поломок, а робочу зону слід упорядковувати, щоб запобігти нещасним випадкам.
Таблиця 14: Основні протоколи безпеки під час обробки великих деталей
Протокол | Важливість | Розгляд |
---|---|---|
Налаштування та калібрування машини | Забезпечує точність і безпеку машини | Завжди калібруйте перед використанням |
Підйомно-транспортне обладнання | Зменшує ризик отримання травм важкими частинами | Використовуйте належні підйомні інструменти |
Засоби індивідуального захисту (ЗІЗ) | Запобігає травмам під час обробки | Переконайтеся, що працівники носять відповідне спорядження |
Чиста та організована робоча зона | Мінімізує ризики та нещасні випадки | Регулярно прибирайте та організовуйте робоче місце |
Регулярне обслуговування машини | Запобігає поломкам і аваріям | Впровадити плановий графік технічного обслуговування |
15. Як вибрати послугу з обробки великих деталей?
Вибір правильного послуги механічної обробки для великих деталей є критичним рішенням, яке може вплинути на загальний успіх проекту. Правильний постачальник послуг повинен мати досвід, обладнання та знання, щоб точно й ефективно працювати з великими деталями.
Готові до хорошої частини? Першим фактором, який слід враховувати при виборі послуги з обробки, є їхній досвід роботи з великими деталями. Досвідчені виробники матимуть необхідний досвід для вирішення унікальних завдань обробки великих компонентів. Вони повинні мати можливість продемонструвати свої здібності через минулі проекти та відгуки клієнтів.
Іншим ключовим фактором є обладнання, яке використовує постачальник послуг. Служба механічної обробки повинна мати доступ до високоякісного спеціалізованого обладнання, здатного обробляти великі деталі. Це включає верстати з ЧПК, фрезерні верстати та інші інструменти, необхідні для досягнення необхідної точності при обробці великих деталей.
Яка справжня історія? Спілкування не менш важливе. Служба обробки, яка чуйна та готова тісно співпрацювати з вами, щоб зрозуміти ваші потреби та вимоги проекту, може забезпечити більш плавний процес від початку до кінця. Чітка комунікація також гарантує швидке вирішення будь-яких питань або проблем, мінімізуючи затримки та помилки.
Нарешті, також слід враховувати ціни та терміни виконання. Хоча вартість не повинна бути єдиним вирішальним фактором, важливо знайти постачальника послуг, який пропонує конкурентоспроможні ціни без шкоди для якості. Переконайтеся, що терміни виконання робіт розумні, а постачальник послуг може дотриматися встановлених термінів.
Таблиця 15: Ключові фактори при виборі служби обробки великих деталей
Фактор | Важливість | Розгляд |
---|---|---|
Досвід роботи з великими деталями | Забезпечує досвід роботи з великими компонентами | Шукайте перевірену історію |
Обладнання та можливості | Визначає якість і точність роботи | Перевірити характеристики обладнання |
спілкування | Забезпечує безперебійне виконання проекту | Виберіть провайдера з чуйним зв'язком |
Ціни та терміни виконання | Впливає на бюджет і терміни доставки | Порівняйте ціни та графіки доставки |
Репутація та відгуки | Вказує на надійність і якість обслуговування | Перевірте рекомендації та відгуки клієнтів |

FAQ
Q1: Що таке обробка великих деталей?
Механічна обробка великих деталей відноситься до процесу обробки великих компонентів або деталей, для виробництва яких з високою точністю потрібне спеціальне обладнання та технології.
Q2: Як працює обробка великих деталей з ЧПУ?
Механічна обробка з ЧПК використовує верстати з комп’ютерним керуванням для точного вирізання, формування та обробки великих деталей відповідно до певних проектів і розмірів.
Q3: Які матеріали найкраще підходять для обробки великих деталей?
Звичайні матеріали для обробки великих деталей включають такі метали, як сталь, алюміній і титан, а також спеціальні неметали відповідно до вимог проекту.
Q4: Які труднощі виникають при обробці великих деталей?
Проблеми включають обробку розміру та ваги великих деталей, досягнення точності, управління теплогенерацією та використання спеціалізованих інструментів і обладнання.
Q5: Як я можу зменшити витрати на обробку великих деталей?
Щоб зменшити витрати, зосередьтеся на ефективному використанні інструменту, мінімізуйте відходи матеріалу, оптимізуйте робочий час машини та ретельно плануйте операції обробки, щоб зменшити час простою.