Giới thiệu
CNC machining is one of the most crucial processes in modern manufacturing. It enables precise, high-quality production of parts for industries ranging from automotive to aerospace. In this article, we’ll dive deep into the various aspects of CNC machining, from choosing the right machine to ensuring quality control. Whether you’re a manufacturer looking to improve your machining processes or a company in need of CNC parts, this guide has you covered. Ready for the good part? Let’s explore how CNC machining can revolutionize your production processes.
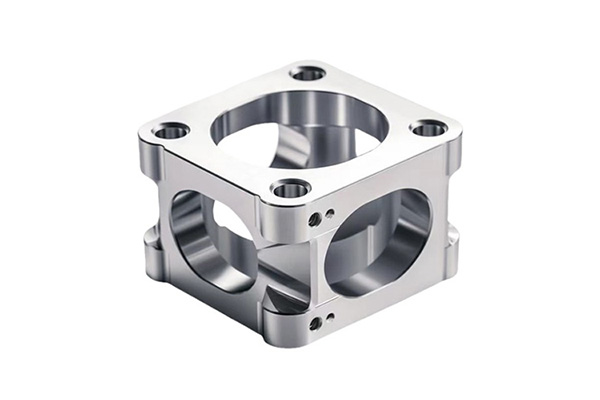
1. Why is CNC Machining Important for Manufacturing Parts?
CNC machining is essential in today’s manufacturing landscape because it offers precise control over the production of parts. Unlike traditional methods, CNC machines are computer-controlled, allowing for incredibly accurate cuts, shapes, and finishes. But here’s the kicker: it’s not just about precision—CNC machining boosts productivity and reduces human error.
The benefits of CNC machining in part production are manifold. It speeds up production timelines, reduces waste, and ensures repeatability. For businesses aiming for high-volume production, CNC machining can provide faster turnaround times without compromising on quality. By automating many of the processes, CNC machines allow operators to focus on optimizing the system rather than manually guiding every move. What’s the real story? CNC machining delivers consistent, reliable parts, whether for one-off prototypes or mass production runs.
Furthermore, CNC machining significantly improves precision and efficiency. With the right design and programming, CNC machines can execute complex cuts that would be nearly impossible by hand. This leads to parts that meet tight tolerances, reducing the need for rework or adjustments.
2. What Are the Different Types of CNC Machining?
CNC machining encompasses several types of operations, each suited for specific manufacturing needs. The primary types include milling, turning, grinding, and electrical discharge machining (EDM). But wait, there’s more to it than just knowing the types! Understanding how each machining process works will help you choose the right one for your project.
Milling is one of the most common CNC processes, where a rotating cutter removes material from a stationary workpiece. This is ideal for creating flat surfaces, slots, and holes. Turning, on the other hand, involves rotating the workpiece while a stationary tool removes material to create cylindrical parts. It’s often used for parts like shafts and gears.
Grinding is a precision process that removes material by rubbing a grinding wheel against the workpiece. It’s ideal for achieving fine finishes and tight tolerances. EDM uses electrical sparks to erode material from the workpiece, making it perfect for intricate or hard materials.
Understanding these different machining processes allows manufacturers to choose the most suitable one based on the type of part they need. The choice depends on factors like the material, the desired finish, and the level of precision required.
3. How Do You Choose the Right CNC Machine for Your Parts?
Choosing the right CNC machine is essential for manufacturing high-quality parts. So, how do you determine which machine fits your needs? Ready for the good part? There are a few key factors to consider: material type, production volume, complexity of the part, and precision required.
When choosing a CNC machine, consider the material of the part you’re manufacturing. Some machines are better suited for harder materials, while others work best with softer materials. Additionally, the complexity of the part plays a significant role in determining which CNC machine will be effective. A more complex part may require a multi-axis CNC machine, which can manipulate the workpiece from several angles.
For high-volume production, it’s critical to choose a machine that balances speed and precision. Machines that can automate certain tasks and offer faster turnaround times will improve production efficiency. Moreover, selecting the correct machine based on the material type and the part’s complexity ensures that your production process will be both efficient and cost-effective.
4. What Materials Are Used in CNC Machining?
The materials used in CNC machining vary greatly, and material selection is critical to the final product’s performance. The right material can affect not just the durability of the part, but also the cost and the time it takes to manufacture it.
Common materials for CNC machining include metals like aluminum, steel, and titanium, as well as plastics, composites, and ceramics. Aluminum is often chosen for its light weight and strength, making it ideal for parts in industries like aerospace and automotive. Steel is chosen for its durability and is commonly used in manufacturing heavy-duty parts. Titanium, though more expensive, is chosen for its strength-to-weight ratio and is used in applications that require extreme durability.
Why is material selection so critical? It affects how the part is machined, how long it lasts, and how much it costs to produce. For example, softer materials are easier to machine, but they may not be suitable for parts that need to withstand high stress or extreme environments. Choosing the right material ensures that your part performs optimally for its intended purpose.
5. What Are the Key Steps in the CNC Machining Process?
The CNC machining process consists of several crucial steps, each of which ensures that the part is produced accurately and efficiently. These steps include design and programming, preparing raw materials, the machining process itself, and finishing processes.
The first step is designing and programming the part. Using CAD software, engineers create the part’s design and then convert it into a CNC machine-readable program using CAM software. This step is essential because the accuracy of the design directly impacts the final product.
Once the design is complete, the next step is preparing raw materials. The material is selected based on the part’s requirements and is then cut to size for the machining process. During the machining process, the CNC machine follows the programmed instructions to cut, shape, and drill the material.
The final step involves finishing processes such as polishing, coating, or adding any additional features to the part. This is where the part is made to meet the required specifications, ensuring a high-quality finish.
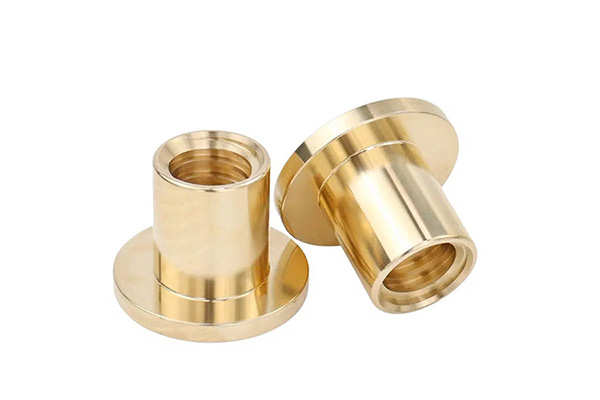
6. How Does CAD/CAM Software Help in CNC Machining?
CAD/CAM software is integral to modern CNC machining. But here’s the kicker: it significantly streamlines the process, saving both time and money. Let’s break it down.
CAD (Computer-Aided Design) software helps engineers and designers create a digital model of the part. These models are crucial because they guide the CNC machine in cutting, shaping, and drilling the material. CAM (Computer-Aided Manufacturing) software takes the CAD model and converts it into a machine-readable program. This allows the CNC machine to execute the design with precision.
The use of CAD/CAM software brings several advantages. First, it improves accuracy by minimizing human error. Second, it speeds up the process, allowing parts to be manufactured faster. And finally, it enables design changes to be made quickly and easily, reducing downtime and costly mistakes during production. So, how does this software streamline the process? By making it easier to design, modify, and program parts, CAD/CAM software makes CNC machining faster, more efficient, and more cost-effective.
7. How Do You Ensure Precision in CNC Machining?
Precision is one of the main advantages of CNC machining, but it requires attention to detail at every step of the process. Ready for the good part? Precision in CNC machining is ensured through careful calibration, accurate measurements, and proper tooling.
First, tool calibration is critical for ensuring that the machine performs correctly. Calibration ensures that the machine’s movements match the program instructions, which is essential for maintaining accuracy. The role of tolerances and measurements is equally important. CNC machines work to tight tolerances, meaning that small deviations from the design can lead to defects. That’s why precise measurements and careful calibration are essential.
To reduce errors in machining, it’s essential to use high-quality tools and materials. Regular maintenance of the machine also helps maintain accuracy over time. Ensuring that your CNC machine is regularly calibrated and that all tools are sharp and in good condition is the key to achieving precise results consistently.
8. What Are the Common Challenges in CNC Machining?
CNC machining offers numerous benefits, but it also comes with its own set of challenges. These include machine wear and tear, material wastage, complicated designs, and tight tolerances. But here’s the kicker: these challenges can be mitigated with the right approach.
Machine wear and tear is a common issue in CNC machining, especially with high-volume production. Over time, parts of the machine can become worn out, leading to inaccurate cuts. Regular maintenance and replacement of worn parts are essential to keeping the machine running smoothly.
Material wastage is another challenge that arises during machining. While CNC machining is highly efficient, excessive cutting and shaping can lead to wasted material. This can be minimized by optimizing the cutting paths and reducing excess material.
Complicated designs and tight tolerances also pose a challenge in CNC machining. These designs require more time and precision, increasing production costs. By investing in high-quality equipment and well-trained operators, these challenges can be overcome, ensuring that CNC machining remains an efficient and cost-effective process.
9. What Are the Costs of CNC Machining?
The cost of CNC machining depends on several factors, including material costs, machine time, and complexity of the part. Ready for the good part? There are several ways to calculate CNC machining costs and identify areas for cost reduction.
First, material costs can vary depending on the type of material used. Metals like aluminum are typically less expensive than more specialized materials like titanium. Second, machine time is another cost driver. The more time a machine spends producing a part, the higher the cost. Optimizing the machining process and minimizing machine downtime can help reduce these costs.
The complexity of the part also affects the cost. Parts with intricate designs or tight tolerances require more time and specialized tools, which can increase costs. By simplifying the design or using more efficient machines, you can reduce these costs.
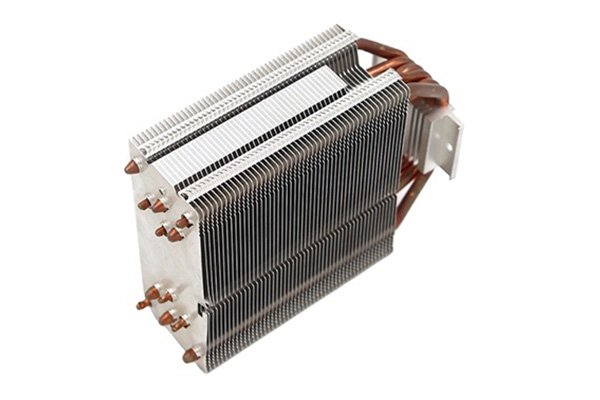
10. How Can You Improve Efficiency in CNC Machining?
Improving efficiency in CNC machining requires a focus on optimization. The first step? Optimizing machine settings to achieve the best balance between speed and quality. Using the right tools and materials is also crucial for maintaining efficiency. By selecting tools that match the material and design, you can reduce machining time and improve part quality.
Automation is another key factor in improving efficiency. Automated systems can reduce the need for manual intervention, speeding up the machining process and reducing human error. By investing in automation technologies, you can increase output and reduce costs.
11. What Is the Role of Quality Control in CNC Machining?
Quality control plays a pivotal role in CNC machining. This ensures that the parts meet the required standards and specifications. The process involves several steps, including in-process inspections and final testing.
During the machining process, operators regularly check the parts for defects or deviations from the design. In-process inspections help detect issues before the part is finished, reducing the need for rework. Final inspection and testing ensure that the part meets all the required specifications, from dimensions to surface finishes.
12. How Do You Handle Post-Processing in CNC Machining?
Post-processing is an essential step in CNC machining, ensuring that the part is finished to the required specifications. There are various types of post-processing techniques, including polishing, coating, and heat treatment.
When post-processing is necessary depends on the material and the desired properties of the part. Some parts require additional finishing to achieve a smooth surface or improve durability. How post-processing affects part performance is significant, as it can enhance wear resistance, corrosion resistance, or aesthetic quality.
13. What Are the Safety Protocols in CNC Machining?
Safety is a top priority in CNC machining, both for the operators and the machines. General safety rules include maintaining a clean workspace, wearing appropriate personal protective equipment (PPE), and ensuring that the machines are properly maintained.
Machine safety features, such as emergency stop buttons, automatic shutoff systems, and safety barriers, are crucial for preventing accidents. Operators should also be trained to recognize hazards and follow safety procedures to ensure a safe working environment.
14. How Does CNC Machining Impact the Environment?
CNC machining can have a significant environmental impact if not managed correctly. Environmental concerns include material waste, energy consumption, and emissions. But here’s the kicker: sustainable practices can minimize these impacts.
Reducing waste in CNC machining involves optimizing material use, improving the efficiency of the machining process, and recycling scrap material. Using energy-efficient machines and renewable energy sources can help reduce the environmental footprint of machining operations.
Sustainable practices in CNC machining not only help the environment but can also reduce costs and improve the company’s reputation.
15. How Do You Choose a Reliable CNC Machining Service Provider?
Choosing the right CNC machining service provider is essential for ensuring quality and reliability. Key qualities to look for include expertise in the required machining processes, the ability to deliver on time, and a track record of producing high-quality parts.
When selecting a CNC service provider, ask questions about their experience, the machines they use, and their quality control processes. Assessing the provider’s reputation and reliability will help ensure that your parts meet the required standards and are delivered on time.
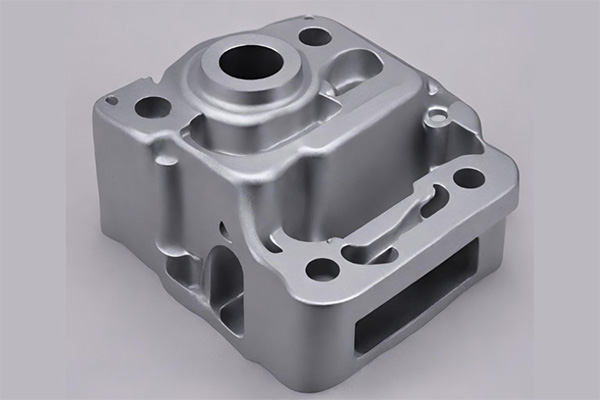
Phần Câu hỏi thường gặp
Câu hỏi 1: What is CNC machining?
CNC machining is a computer-controlled manufacturing process that uses programmed commands to control machine tools, creating precise and complex parts.
Câu hỏi 2: How do you choose the right CNC machine?
Choosing the right CNC machine involves considering the material, complexity of the part, and production volume.
Câu hỏi 3: What materials are commonly used in CNC machining?
Materials commonly used include metals like aluminum, steel, and titanium, as well as plastics and composites.
Câu hỏi 4: How can you ensure precision in CNC machining?
Precision is achieved through tool calibration, accurate measurements, and high-quality tools and materials.
Câu hỏi 5: What are the costs of CNC machining?
Costs depend on factors like material, machine time, and part complexity. Reducing machine time and optimizing designs can lower costs.