Giới thiệu
When designing or manufacturing chemical-resistant parts, selecting the right materials is crucial for ensuring durability, safety, and cost-effectiveness. In industries ranging from chemical processing to aerospace, the right choice of material can significantly impact product performance and the overall longevity of equipment. This guide explores the top materials used for chemical-resistant parts, the factors to consider when choosing them, and their various applications.
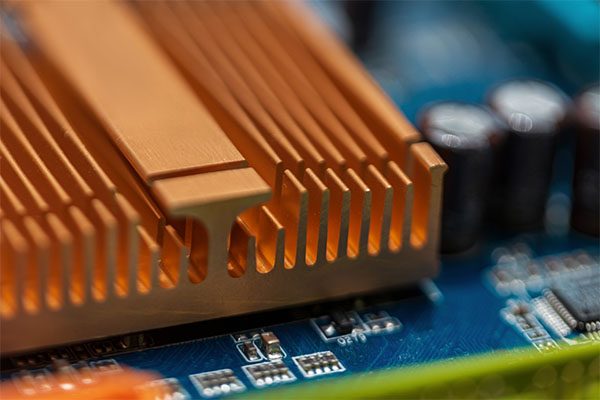
1. What Are Chemical-Resistant Parts?
Chemical-resistant parts are materials specifically designed to resist the degrading effects of exposure to various chemicals. These materials are essential in protecting equipment and machinery from the harmful impact of harsh substances that could lead to corrosion, weakening, or failure. But here’s the kicker: without chemical resistance, industries that rely on machinery and processing systems are at risk of frequent breakdowns and safety issues. Chemical-resistant parts play a vital role in industries such as manufacturing, automotive, and medical devices, where exposure to aggressive chemicals is common.
Key characteristics of chemical-resistant materials include high durability, the ability to maintain structural integrity in corrosive environments, and resistance to heat, pressure, and other extreme conditions. These materials are often tested to withstand not just a single type of chemical but a broad spectrum of chemicals, from acids and alkalis to solvents and oils.
2. Why Are Chemical-Resistant Parts Important?
Chemical-resistant parts are more than just a protective measure; they directly impact the safety, performance, and cost-efficiency of operations. What’s the real story? In environments where chemicals are used extensively, parts made from non-resistant materials will corrode, degrade, or fail, leading to costly downtime, repairs, and even hazardous incidents. The importance of chemical-resistant materials cannot be overstated.
The first and most significant benefit of chemical-resistant parts is their contribution to industrial safety. By preventing corrosion and degradation, these materials help avoid leaks, spills, or accidents that could pose a risk to workers and the environment. Additionally, the lifespan of products made with these materials is significantly extended, reducing the frequency of replacements and repairs. In the long run, this results in substantial cost savings, making chemical-resistant materials an essential investment for any business.
3. What Types of Materials Are Chemical-Resistant?
When selecting materials for chemical-resistant parts, there are several options to consider. Ready for the good part? Each type of material offers unique benefits depending on the specific requirements of the application.
Metals such as stainless steel, titanium, and alloys are often used for their inherent resistance to corrosion. Stainless steel, for example, is a common choice for environments where resistance to acidic or saline conditions is required. Titanium, though more expensive, offers superior resistance in high-temperature and highly corrosive environments.
Polymers like PTFE, PFA, and PVC are also widely used in chemical-resistant parts. PTFE, also known as Teflon, is highly resistant to a wide range of chemicals and maintains its integrity even at high temperatures. PVC is a more affordable option for less demanding applications but still offers substantial chemical resistance.
Rubber materials, such as EPDM and Viton, are ideal for seals, gaskets, and other flexible parts. EPDM is resistant to weathering, ozone, and a variety of chemicals, while Viton is known for its superior resistance to high-temperature and chemical exposure.
4. How Do You Choose the Right Chemical-Resistant Material?
Choosing the right material for chemical-resistant parts involves a comprehensive assessment of various factors. What’s the real story here? It’s all about matching the material’s properties with the conditions it will face during operation. Here are the most important considerations:
First, you need to assess the type of chemicals that the material will come into contact with. Different chemicals have varying degrees of corrosiveness, so it’s essential to choose a material that can resist the specific chemical environment. Next, consider the temperature and pressure conditions. High temperatures can accelerate chemical reactions and degrade materials, so heat-resistant properties are crucial.
Finally, cost-effectiveness and longevity should also play a role in your decision-making process. While premium materials like titanium offer excellent resistance, they may not always be necessary for every application. Balancing performance with cost is key to ensuring the best value for your business.
5. What Are the Best Materials for Chemical-Resistant Parts?
What’s the best material for chemical-resistant parts? The answer depends on the specific chemical exposure and application, but certain materials are universally recognized for their durability and resistance.
Metals like stainless steel and titanium alloys stand out when it comes to extreme chemical exposure. Stainless steel, with its corrosion-resistant properties, is commonly used in industries such as food processing and pharmaceuticals. Titanium, although more expensive, is often the go-to choice for high-temperature environments where other metals might fail.
For polymers, PTFE is a leader in the field, offering exceptional resistance to a broad range of chemicals. It’s perfect for applications where both chemical and thermal resistance are required. PFA, similar to PTFE, is another excellent option, especially when flexibility is needed. PVC, while not as resistant as PTFE, is still a reliable, cost-effective solution for a range of industrial applications.
In rubber materials, Viton is the gold standard. Its ability to resist high temperatures and aggressive chemicals makes it ideal for seals, gaskets, and O-rings in industries like automotive and aerospace.
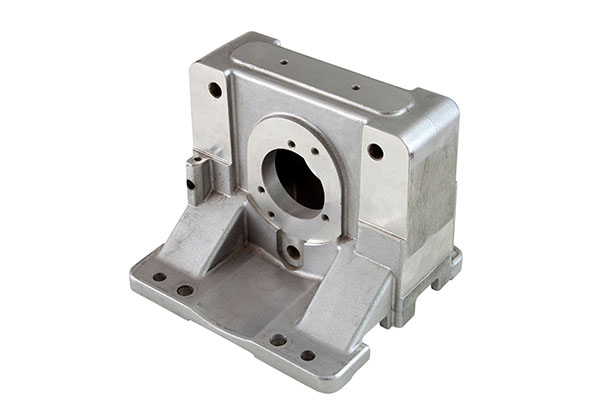
6. How Do Chemical-Resistant Parts Impact Manufacturing Processes?
Chemical-resistant parts aren’t just useful in preventing corrosion and degradation—they also play a significant role in the manufacturing process itself. This is where it gets interesting. The use of chemical-resistant materials can improve manufacturing efficiency, reduce the risk of failures, and ensure consistent product quality.
In industries like chemical processing, maintaining quality control is essential. Parts that degrade over time can lead to inconsistencies in production, resulting in faulty products. By using chemical-resistant materials, manufacturers can ensure that their equipment remains reliable, reducing the risk of failure and costly downtime.
Moreover, chemical-resistant parts minimize maintenance costs. When parts are resistant to corrosion and wear, the need for frequent repairs and replacements is reduced, ultimately lowering the overall operational costs. In addition, using these materials can enhance product performance by maintaining their structural integrity and chemical resistance over time.
7. What Are Common Applications of Chemical-Resistant Parts?
Chemical-resistant parts are used in a wide array of industries, each with its unique requirements. Let’s take a closer look at some of the most common applications.
In chemical processing plants, chemical-resistant materials are critical for equipment such as tanks, pumps, and pipes, which come into constant contact with corrosive substances. Aerospace and automotive industries also rely on these materials for components that must withstand high temperatures and extreme chemical exposure, such as seals and gaskets. In medical devices and pharmaceutical applications, chemical-resistant parts ensure that equipment remains sterile and uncontaminated by harsh chemicals.
No matter the industry, chemical-resistant materials are essential for maintaining safety, performance, and longevity of equipment.
8. How Do Chemical-Resistant Parts Perform Under Harsh Conditions?
When subjected to harsh conditions, chemical-resistant materials maintain their integrity and functionality. The performance of these materials under extreme temperatures, pressure, and corrosive environments is a testament to their durability.
For example, stainless steel can handle high temperatures and aggressive chemicals, making it ideal for industrial applications like reactors and heat exchangers. Polymers such as PTFE offer exceptional performance even in the harshest chemical environments, remaining intact in the presence of acids, alkalis, and solvents. Rubber materials like Viton can withstand extreme temperatures and maintain their elasticity and sealing properties under high-pressure conditions.
Understanding how these materials perform under harsh conditions ensures that manufacturers can choose the right material for their specific needs.
9. What Are the Challenges of Working with Chemical-Resistant Materials?
While chemical-resistant materials offer significant benefits, working with them presents several challenges. First, material sourcing can be expensive, especially for premium options like titanium and specialized polymers. The costs associated with acquiring high-quality materials can be a barrier for some manufacturers.
Additionally, certain materials may be difficult to machine due to their hardness or structural properties. Titanium, for example, requires specialized equipment to machine effectively. There are also compatibility issues to consider when combining chemical-resistant materials with other materials in a system, as some materials may not bond well or may cause degradation over time.
Despite these challenges, the benefits of using chemical-resistant materials far outweigh the difficulties, making them an essential choice for many industries.
10. How Are Chemical-Resistant Parts Tested for Durability?
Testing the durability of chemical-resistant parts is a crucial step in ensuring their performance in real-world conditions. Chemical exposure testing involves exposing the material to a variety of chemicals to assess its resistance and integrity over time. Temperature and pressure testing protocols simulate the harsh conditions the material will face during operation, ensuring it can withstand extreme environments without failure.
Wear resistance evaluations are also essential to determine how well a material holds up under mechanical stress and prolonged use. By conducting these tests, manufacturers can ensure that the parts they produce meet the necessary standards for safety, performance, and longevity.
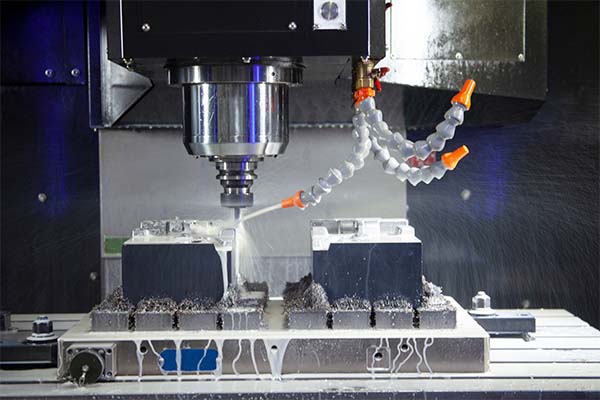
11. What Innovations Are Being Made in Chemical-Resistant Parts?
The development of new composite materials and advances in coatings are driving innovation in the field of chemical-resistant parts. Composite materials, which combine different types of materials to optimize performance, are becoming increasingly popular due to their superior strength, chemical resistance, and lightweight properties.
Advances in surface treatments, such as coatings and galvanization, are also enhancing the durability of chemical-resistant materials. These treatments provide additional layers of protection against corrosive substances, extending the lifespan of parts and equipment.
Emerging trends in material design are focused on improving sustainability while maintaining the high performance required in chemical-resistant applications.
12. How Can Chemical-Resistant Parts Save Costs for Businesses?
Chemical-resistant parts are an investment that can save businesses significant amounts in the long term. Ready for the good part? By reducing the frequency of replacements and repairs, companies can lower maintenance costs and extend the lifespan of their equipment.
Additionally, using durable materials that resist chemical exposure reduces the likelihood of equipment failure, preventing costly downtime. The long-term benefits of using chemical-resistant parts often outweigh the initial costs, making them an essential component for businesses looking to improve efficiency and minimize operating costs.
13. How Do You Maintain Chemical-Resistant Parts?
Proper maintenance is key to ensuring the longevity of chemical-resistant parts. Regular inspections and cleaning are essential to identify any signs of wear or degradation early. Handling and storing parts correctly can also prevent damage and ensure that they maintain their performance over time.
To extend the lifespan of chemical-resistant materials, businesses should follow best practices for maintenance, including using the right cleaning agents and tools that won’t damage the material. Proper storage conditions, such as avoiding extreme temperatures and exposure to incompatible substances, will also help preserve the material’s integrity.
14. What Are the Environmental Considerations of Chemical-Resistant Parts?
The environmental impact of chemical-resistant materials is an important consideration for many industries. While these materials are essential for product performance, they can pose challenges in terms of disposal and recycling. Many chemical-resistant materials, particularly certain plastics and rubbers, are not easily recyclable.
However, there are growing efforts to develop eco-friendly alternatives and improve the recyclability of chemical-resistant materials. Businesses are increasingly seeking sustainable options that minimize environmental impact without compromising on performance. Recycling processes are also being refined to handle chemical-resistant materials more efficiently, contributing to sustainability efforts across industries.
15. What Should You Know Before Purchasing Chemical-Resistant Parts?
Before purchasing chemical-resistant parts, it’s important to consider several factors. First, make sure the supplier you choose offers high-quality materials that meet industry standards. Pricing and cost comparisons are also important to ensure you get the best value for your investment.
Quality assurance is another critical factor. Ensure that the manufacturer has a proven track record of producing reliable, durable chemical-resistant parts. Consulting with an expert or conducting your own material testing can also help ensure that you select the right material for your specific needs.
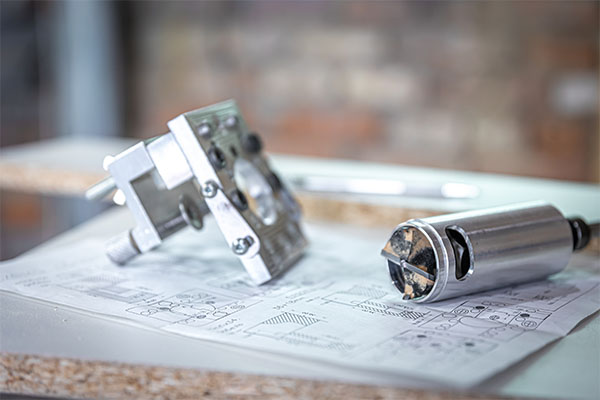
Phần Câu hỏi thường gặp
Câu hỏi 1: What are chemical-resistant parts?
Chemical-resistant parts are materials designed to withstand exposure to various chemicals, ensuring the longevity and safety of equipment and machinery in industrial settings.
Câu hỏi 2: How do chemical-resistant materials work?
Chemical-resistant materials prevent degradation, corrosion, or chemical reactions by forming protective barriers against harmful substances.
Câu hỏi 3: What types of chemical-resistant materials are best for manufacturing?
Materials like stainless steel, titanium alloys, PTFE, and Viton rubber are widely used in manufacturing for their resistance to harsh chemicals and extreme conditions.
Câu hỏi 4: How can I determine which chemical-resistant material is right for my project?
Choosing the right material involves evaluating the chemicals involved, temperature and pressure conditions, and cost considerations. Consulting with a material expert is often a good first step.
Câu hỏi 5: Are there sustainable options for chemical-resistant parts?
Yes, there are emerging eco-friendly materials and recycling processes that help reduce environmental impact while maintaining chemical resistance in various applications.