Giới thiệu
Delrin, also known as POM-H (Polyoxymethylene), is a high-performance thermoplastic polymer widely used in CNC machining. Its combination of high strength, low friction, and dimensional stability makes it a preferred material for precision engineering across a variety of industries. In this article, we will explore the key properties of Delrin, its applications in CNC machining, and why it’s an ideal material for creating high-quality, durable parts. By the end of this guide, you’ll have a solid understanding of Delrin’s CNC machining potential and how it stacks up against other materials in the market.
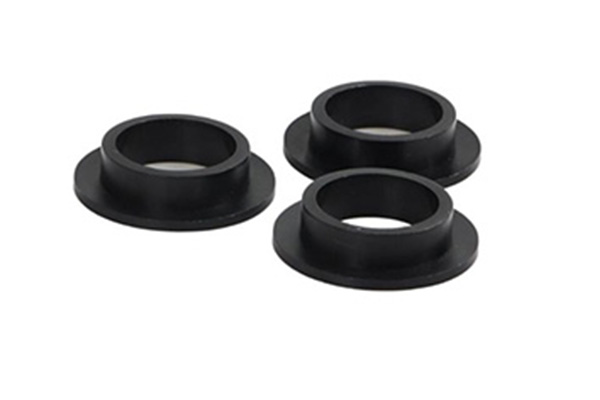
1. What is Delrin (POM-H) and Why is It Used in CNC Machining?
Delrin (POM-H) is a strong, semi-crystalline thermoplastic that offers exceptional mechanical properties. It has low moisture absorption and good dimensional stability, which makes it an ideal candidate for precision CNC machining. But here’s the kicker—it is also highly resistant to wear, making it perfect for high-performance applications.
Delrin is primarily used in industries that require durable and reliable components, such as automotive, aerospace, and industrial machinery. Its inherent strength allows for the creation of parts that withstand heavy loads while maintaining dimensional integrity over time. This material’s ability to withstand continuous friction makes it an attractive alternative to metal components in many applications.
Moreover, its ease of machining ensures that complex designs can be achieved with accuracy, making it a favorite among manufacturers who specialize in tight tolerance parts. Its widespread use in CNC machining can be attributed to its excellent machinability, cost-effectiveness, and versatility in a variety of applications.
2. What Are the Key Properties of Delrin (POM-H)?
Ready for the good part? Delrin boasts a range of properties that make it highly desirable in CNC machining. From its strength to its chemical resistance, this material is one of the most reliable plastics for high-performance parts.
- Strength and Durability: Delrin is known for its robust mechanical properties. It exhibits high tensile strength and resistance to wear, which makes it ideal for parts subjected to frequent mechanical stress.
- Độ ổn định nhiệt: Delrin has an excellent performance range in temperatures up to 120°C (248°F). This property ensures that it retains its shape and strength even under high thermal conditions, making it a reliable choice for many engineering applications.
- Kháng hóa chất: One of Delrin’s standout features is its resistance to a wide variety of chemicals, including solvents, fuels, and oils. This makes it especially suitable for automotive and industrial applications where parts may be exposed to harsh chemicals.
- Electrical Properties: Delrin is a good electrical insulator, which enhances its use in electrical and electronic applications where conductivity must be minimized.
- Wear Resistance: Delrin excels in applications where friction is a concern. It’s highly resistant to wear, which is why it’s often used in gears, bearings, and bushings.
These key properties make Delrin a valuable material in a variety of CNC machining projects.
3. How Does Delrin Compare to Other Plastics in CNC Machining?
Now, let’s dive into how Delrin stacks up against other plastics commonly used in CNC machining. Ready for the comparison?
- Comparison with Acrylic: Acrylic is widely used for its clarity and ease of machining. However, it lacks the toughness and wear resistance of Delrin. While acrylic might be perfect for displays or signs, Delrin outshines it when it comes to strength and durability, making it the better option for mechanical parts.
- Comparison with Polyethylene: Polyethylene is often used for parts that require low friction and chemical resistance. However, Delrin offers better dimensional stability and strength, particularly in applications where precision is critical. Polyethylene’s softer nature doesn’t make it suitable for high-stress, precision CNC parts.
- Advantages over Traditional Metals: Delrin offers several advantages over metals in CNC machining. It is much lighter than metals like steel or aluminum, making it easier to handle and transport. It also resists corrosion and offers better chemical resistance, which makes it ideal for certain applications where metals would degrade over time.
The real advantage of Delrin lies in its unique combination of strength, machinability, and resistance to wear—making it the material of choice for many industries.
4. What Are the Applications of Delrin in CNC Machining?
Delrin is used in numerous industries, thanks to its versatile properties. This is where it gets interesting. Delrin is essential in creating high-performance parts in a wide range of applications.
- Use in Automotive Parts: Delrin is commonly used in automotive components, including gears, bushings, and seals. Its resistance to wear and chemical exposure ensures that parts can endure the rigorous conditions of automotive environments without compromising performance.
- Applications in Aerospace: In aerospace, Delrin is utilized for making high-precision components such as bearings, actuators, and structural parts. Its high strength-to-weight ratio is critical in reducing the overall weight of aerospace systems, while its dimensional stability ensures that parts maintain their form and function even in extreme conditions.
- Industrial and Consumer Products: Delrin is also used in industrial machinery, power tools, and consumer products. Its low friction and high durability make it a valuable material for parts that require frequent movement or contact with other surfaces.
These applications showcase Delrin’s versatility and capability to perform in a variety of industries that demand high precision and durability.
5. Why is Delrin Ideal for Precision Parts in CNC Machining?
What’s the real story behind Delrin’s precision? Let’s take a look at its performance in CNC machining. Delrin’s dimensional accuracy, high tolerance capabilities, and exceptional surface finish properties make it the perfect choice for producing precision parts.
- Dimensional Accuracy: Delrin holds tight tolerances, which means it maintains its dimensions even when subjected to external forces. This is essential for precision parts that need to fit together perfectly.
- High Tolerance Capabilities: Delrin can be machined to tight tolerances, typically in the range of ±0.005 inches. This ensures that parts are manufactured to exact specifications, providing the high performance required in many applications.
- Surface Finish Properties: Delrin’s ability to achieve a smooth surface finish makes it ideal for parts that require minimal post-processing. The surface quality not only improves the aesthetics but also reduces friction, extending the lifespan of the part.
For any CNC machining project requiring precision, Delrin should be a top contender.
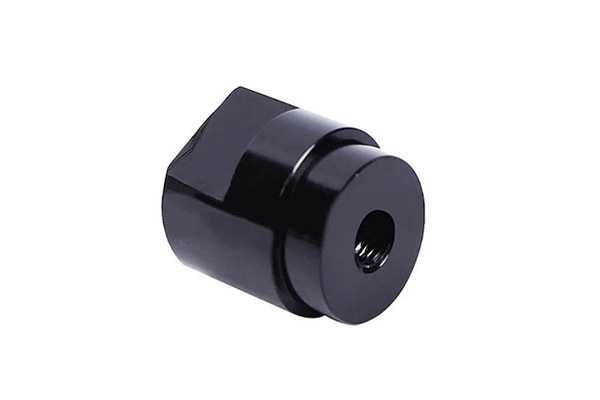
6. How is Delrin Machined in CNC Manufacturing?
When it comes to machining Delrin, there are a few key considerations. Let’s break it down. Delrin can be processed using standard CNC milling and turning techniques, but there are some important best practices to keep in mind.
- Milling and Turning Processes: CNC milling is commonly used to create complex, detailed parts from Delrin. The material machines well under both standard and high-speed operations. Turning processes, particularly on a lathe, are also effective for creating cylindrical components like shafts and bushings.
- Machining Challenges and Considerations: One challenge when machining Delrin is its tendency to warp during the cooling process, particularly if it is not handled properly. Additionally, the material’s ability to generate static electricity can sometimes interfere with precision.
- Best Practices for Machining Delrin: To ensure optimal machining results, it’s crucial to use sharp cutting tools and maintain proper feed rates. Cooling is also essential to prevent overheating, which can lead to deformation.
Delrin’s machinability, when handled properly, allows for high-quality, high-precision components.
7. What Are the Advantages of Using Delrin in CNC Machining?
Let’s talk about the advantages. Delrin offers several key benefits that make it an attractive option for CNC machining projects.
- High Machinability: Delrin is easy to machine with high-speed cutting tools, which improves production efficiency. This reduces machining time, which can save manufacturers money.
- Cost-efficiency: Compared to metals, Delrin is more affordable to process and can help reduce overall project costs, especially in large-scale production runs.
- Lightweight but Strong: Delrin offers a unique balance of strength and low weight, making it ideal for applications where part weight is a concern, such as in automotive and aerospace components.
- Resistance to Wear and Fatigue: Delrin’s ability to withstand continuous use and exposure to wear makes it the perfect material for parts subjected to friction.
With all these benefits, Delrin is clearly a top choice for high-performance CNC machining applications.
8. Are There Any Disadvantages to Using Delrin in CNC Machining?
While Delrin offers many advantages, it’s not without its limitations. Let’s take a look at some of the disadvantages to consider when using Delrin in CNC machining.
- Vulnerability to UV Degradation: Delrin is susceptible to UV degradation when exposed to sunlight for prolonged periods. This can cause the material to weaken and degrade, so it’s important to ensure Delrin parts are used in environments where UV exposure is minimal.
- Limited High-Temperature Stability: While Delrin performs well at moderate temperatures, it has a lower melting point than many metals and can lose its mechanical properties at high temperatures, limiting its use in extreme heat conditions.
- Environmental Concerns: Like many plastics, Delrin poses environmental challenges, particularly in terms of recycling. While some grades of Delrin are recyclable, the material’s overall environmental footprint is still a concern for sustainable manufacturing practices.
These disadvantages should be considered when deciding whether Delrin is the right choice for your CNC machining project.
9. How Can Delrin be Properly Stored and Handled During CNC Machining?
To keep Delrin in top condition, proper storage and handling are essential. Here’s what you need to know.
- Recommended Storage Conditions: Delrin should be stored in a cool, dry place away from direct sunlight. Prolonged exposure to UV light or high temperatures can cause degradation over time, affecting its performance.
- Handling Tips to Prevent Damage: When handling Delrin, it’s important to avoid scratching or damaging the surface. Delrin is susceptible to surface defects, which can affect part functionality.
- Ensuring Quality of Delrin During Machining: When machining Delrin, ensure that the material is free of contaminants, as these can affect the final product. Regular inspection and proper maintenance of machinery will help keep Delrin in top condition throughout the machining process.
By following these guidelines, you can ensure that your Delrin parts maintain their high quality.
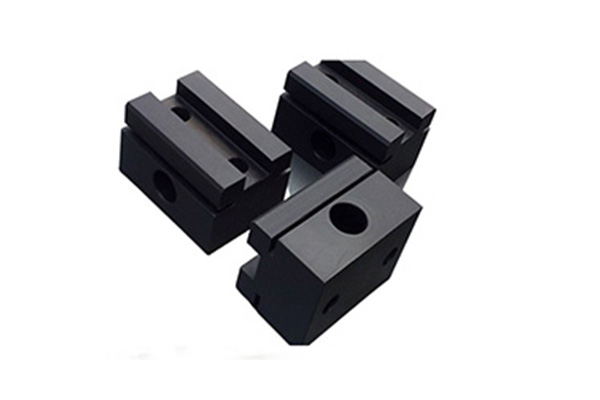
10. How Does Delrin Perform in Harsh Environments?
Let’s take a closer look at Delrin’s performance in extreme conditions.
- Resistance to Chemicals and Moisture: Delrin is highly resistant to a wide range of chemicals and moisture, making it suitable for use in environments where other materials might degrade. It excels in applications where exposure to oils, fuels, and solvents is common.
- Performance Under High Stress: Even under high-stress conditions, Delrin maintains its strength and dimensional stability, making it a reliable choice for mechanical parts that are subject to constant wear.
- Performance in Extreme Temperatures: Delrin performs well in low-temperature environments, maintaining its rigidity and toughness. However, its performance at high temperatures is more limited, making it less ideal for some applications where heat resistance is crucial.
Delrin’s resistance to chemicals, moisture, and stress makes it ideal for challenging environments.
11. What Are the Different Grades of Delrin Used in CNC Machining?
Not all Delrin grades are created equal. Let’s explore the different grades available for CNC machining.
- Standard Grade (POM-H): This is the most commonly used grade of Delrin. It is ideal for general-purpose applications, offering a good balance of strength, durability, and machinability.
- Delrin for High-Performance Applications: For applications that require higher mechanical properties, Delrin comes in higher-grade versions, such as Delrin 150, which offers enhanced wear resistance and chemical stability.
- Differences in Grades and Their Applications: The different grades of Delrin vary in properties such as strength, impact resistance, and chemical resistance. Choosing the right grade depends on the specific requirements of your application.
Understanding these grades will help you select the right type of Delrin for your CNC machining needs.
12. How Can CNC Machinists Choose the Right Delrin Grade for Their Projects?
Choosing the right Delrin grade is crucial for ensuring the success of your CNC machining project. Let’s look at what factors should influence your decision.
- Factors to Consider (Load, Temperature, Wear): When choosing a Delrin grade, consider the mechanical load the part will undergo, the operating temperature, and the wear conditions. High-performance grades are recommended for parts that will face extreme conditions.
- Comparing Costs and Performance: Higher grades of Delrin tend to cost more but offer better performance. It’s important to strike a balance between cost and required performance to ensure you choose the right grade for your needs.
- Common Industry Applications: Different industries require different grades. Automotive parts, for example, may require higher grades, while general-purpose applications may suffice with standard POM-H grade.
By considering these factors, machinists can make informed decisions about the best Delrin grade for their projects.
13. How Does Delrin Contribute to Sustainable CNC Machining Practices?
Ready for the good part? Let’s talk about sustainability. Delrin plays an important role in green manufacturing practices.
- Recyclability of Delrin: Delrin is a recyclable material, which helps reduce waste and promotes sustainability in manufacturing. Recycling Delrin parts can significantly lower the environmental impact of CNC machining processes.
- Environmental Impact Compared to Other Plastics: When compared to other plastics, Delrin has a lower environmental impact due to its durability and ability to be recycled. This makes it a more sustainable option for manufacturers looking to reduce their ecological footprint.
- The Role of Delrin in Green Manufacturing: Delrin’s ability to withstand long-term use without degradation makes it a material of choice for green manufacturing initiatives. It reduces the need for frequent replacements, thus minimizing waste.
Delrin’s recyclability and overall reduced environmental impact make it a great choice for sustainable manufacturing practices.
14. What Are Some Case Studies of Delrin Used in CNC Machining?
Let’s take a closer look at some real-world applications of Delrin in CNC machining.
- Real-World Examples from Automotive, Aerospace, and Manufacturing Sectors: Delrin is used in automotive components like fuel systems and bearings, in aerospace for actuators and gears, and in manufacturing for robotics and conveyor systems.
- Success Stories of Delrin’s Application: In the automotive industry, Delrin’s use in components like window regulators has resulted in increased longevity and reduced maintenance costs.
- Lessons Learned from These Case Studies: The versatility of Delrin has been proven across multiple sectors, with lessons learned about its performance under high stress and in harsh conditions.
15. How Do You Maintain CNC Machining Equipment When Using Delrin?
Delrin’s unique properties can have an impact on your machining equipment. Let’s talk about how to maintain your CNC tools when working with this material.
- Cleaning and Maintaining Tools After Machining Delrin: Delrin’s low-friction properties can lead to a build-up of residue on tools, so it’s essential to clean them after each use.
- Preventing Build-up and Wear: Regular maintenance of CNC tools ensures that the material doesn’t cause excessive wear, which could affect the accuracy of future machining projects.
- Ensuring Smooth Operations: By following best practices for tool maintenance, you can ensure smooth and efficient machining operations when working with Delrin.
Proper equipment maintenance is key to getting the best results when using Delrin in CNC machining.
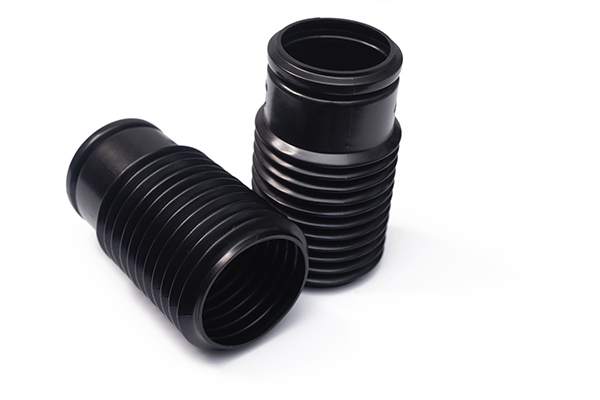
Phần Câu hỏi thường gặp
Câu hỏi 1: What is Delrin (POM-H)?
Delrin (POM-H) is a high-performance thermoplastic polymer commonly used in precision parts. It’s known for its high strength, wear resistance, and low friction properties, making it ideal for CNC machining.
Câu hỏi 2: How does Delrin compare to other plastics in CNC machining?
Delrin offers superior machinability and durability compared to many other plastics like acrylic and polyethylene, especially in high-stress applications.
Câu hỏi 3: What are the main applications of Delrin in CNC machining?
Delrin is widely used in industries such as automotive, aerospace, and manufacturing, particularly for creating parts that require high precision, strength, and wear resistance.
Câu hỏi 4: How can I prevent Delrin from degrading during CNC machining?
To prevent Delrin from degrading, ensure proper storage, avoid excessive heat exposure, and handle it carefully to avoid UV damage.
Câu hỏi 5: What are the best practices for machining Delrin?
Best practices for machining Delrin include selecting the right tool material, using appropriate feed rates, and ensuring proper cooling during the machining process.