Introduction
CNC milling is a crucial aspect of modern manufacturing, enabling the creation of complex parts with high precision and minimal human intervention. In this guide, we will delve into the ins and outs of CNC milling, providing a comprehensive understanding of how it works, its applications, and why it’s essential in various industries. Whether you’re new to machining or looking to refine your knowledge, this article will answer all your pressing questions.
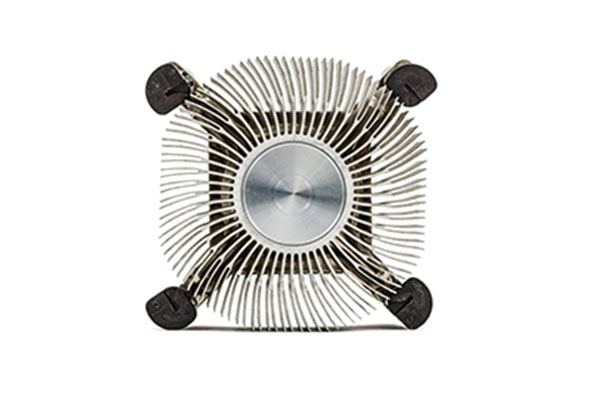
1. What is CNC Milling?
CNC milling is a computer-controlled machining process that involves using rotating cutting tools to remove material from a workpiece. It’s a subtractive manufacturing method that enables precise shaping and cutting of metal, plastic, wood, and other materials. But here’s the kicker – CNC milling can create incredibly complex and detailed parts that would be nearly impossible to achieve with traditional machining methods.
In CNC milling, the machine’s movements are controlled by a computer program that follows specific instructions, which are typically written in G-code. These instructions direct the machine on where to move, how fast to cut, and when to stop. This precise control allows manufacturers to create highly intricate designs that maintain tight tolerances. CNC milling machines can perform a range of operations, such as drilling, tapping, facing, and contouring.
Why is this important? CNC milling allows businesses to produce high volumes of custom parts with uniform quality, making it a go-to choice for industries like aerospace, automotive, and medical device manufacturing.
Here’s a breakdown of key CNC milling operations:
Operation Type | Description | Common Use |
---|---|---|
Facing | Cutting the surface of the workpiece flat. | Smoothing surfaces for further work. |
Drilling | Creating holes in the workpiece. | Used in automotive, aerospace, etc. |
Tapping | Cutting internal threads into a hole. | Making threaded holes for screws. |
Contouring | Creating curved or complex shapes. | Used in prototyping and product design. |
2. How Does CNC Milling Work?
Now, let’s dig into how CNC milling actually works. To the untrained eye, a CNC milling machine might look like a complicated assembly of motors, tools, and software. But once you understand the process, it’s clear that CNC milling follows a logical, step-by-step approach to create parts.
It all begins with the design. Engineers and designers create a 3D model of the part using CAD (Computer-Aided Design) software. This model is then converted into a set of instructions (G-code) that tells the CNC machine exactly how to move its tools and cut the material. Ready for the good part? Once the machine receives these instructions, it begins the process by securing the workpiece on the table.
The tool rotates at high speed and removes material from the workpiece in precise increments. The cutting tool moves along different axes – typically X, Y, and Z – to perform specific operations. For example, in a vertical CNC milling machine, the cutting tool moves up and down while the workpiece is moved horizontally.
To visualize this, consider a case study where a complex aerospace part is being produced. The design team creates a CAD model of a turbine blade, which is then transferred to the CNC milling machine. The machine performs operations such as drilling and contouring to shape the turbine blade with high precision, ensuring that the end product meets stringent quality standards.
Machine Type | Description | Key Features |
---|---|---|
Vertical CNC | A milling machine with a vertically positioned spindle. | Great for precision cutting. |
Horizontal CNC | A milling machine with a horizontally positioned spindle. | Ideal for heavier workpieces. |
5-Axis CNC | A CNC machine that can move the tool or workpiece on five axes. | Best for highly complex parts. |
3. What Are the Types of CNC Milling Machines?
The world of CNC milling is vast, and the machines themselves come in several configurations, each tailored for different applications. So, what’s the real story behind these machines?
The most common types of CNC milling machines are vertical, horizontal, and 5-axis mills. Vertical CNC mills are the most widely used, with the cutting tool positioned vertically to cut along the X and Y axes. These machines are ideal for applications where the workpiece is smaller, and precision is paramount.
Horizontal CNC mills, on the other hand, feature a horizontally oriented spindle. These are used primarily for larger workpieces and are excellent for jobs that require heavy material removal. For instance, they are ideal for parts like engine blocks that need precise machining but are too large for vertical mills.
Ready for the good part? 5-axis CNC mills are the most advanced machines on the market. They can move the cutting tool or workpiece along five different axes, making them suitable for the most complex and intricate designs. These machines are commonly used in industries like aerospace, where components have multiple angles and require high precision.
Machine Type | Features | Best Use |
---|---|---|
Vertical CNC | Spindle orientation is vertical. | Ideal for small parts and detailed work. |
Horizontal CNC | Spindle orientation is horizontal. | Perfect for larger, heavier workpieces. |
5-Axis CNC | Can move in five directions (X, Y, Z, plus rotation). | Best for complex, multi-angle machining. |
4. What Materials Can Be Processed with CNC Milling?
CNC milling is incredibly versatile when it comes to the materials it can handle. You might be wondering, what can CNC milling machines really work with? The answer is: almost anything! From metals and plastics to composites and even wood, CNC mills can process a wide range of materials, making them indispensable in various industries.
The most common materials for CNC milling include metals like aluminum, steel, and titanium. Aluminum is widely used because it’s lightweight, easy to machine, and has excellent corrosion resistance. Steel is more challenging to machine, but it’s incredibly strong and durable, making it ideal for structural applications.
But wait, there’s more! Plastics and polymers are also frequently processed with CNC milling, particularly in the automotive and medical industries. For example, plastic parts used in automotive interiors are often milled using CNC machines. Composite materials, such as carbon fiber, are also gaining popularity, especially in aerospace applications, due to their strength-to-weight ratio.
Material Type | Advantages | Common Uses |
---|---|---|
Aluminum | Lightweight, corrosion-resistant, easy to machine. | Aerospace, automotive, and consumer products. |
Steel | Strong and durable but harder to machine. | Structural parts, automotive, manufacturing. |
Plastic | Easy to machine and cost-effective. | Automotive, medical devices, electronics. |
Carbon Fiber | High strength-to-weight ratio. | Aerospace, sports equipment, and automotive. |
5. What Industries Use CNC Milling?
CNC milling is a cornerstone of modern manufacturing, and its applications span multiple industries. But what industries use CNC milling the most? The short answer: nearly every industry that requires high-precision parts.
One of the largest sectors for CNC milling is aerospace. Parts such as turbine blades, engine components, and structural elements are all produced using CNC milling machines. The automotive industry is another major player, where CNC milling is used to manufacture engine blocks, gears, and transmission parts.
What’s the real story? Medical device manufacturers also rely heavily on CNC milling, especially for creating surgical instruments, implants, and prosthetics. These parts require exceptional precision to ensure patient safety and device reliability. The electronics industry also uses CNC milling to create components like circuit boards and connectors.
Industry | Applications | Key Benefits |
---|---|---|
Aerospace | Turbine blades, engine parts, structural elements. | High precision, reliability, and strength. |
Automotive | Engine blocks, gears, transmission parts. | Efficient production, high precision. |
Medical | Surgical instruments, implants, prosthetics. | Precision, safety, and customization. |
Electronics | Circuit boards, connectors, and casings. | Complex designs, miniaturization, accuracy. |
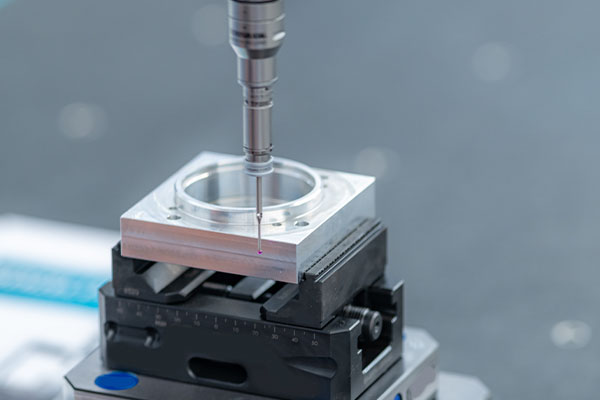
6. What Are the Advantages of CNC Milling?
CNC milling offers numerous advantages that have made it the go-to solution for manufacturers around the world. First and foremost, CNC milling machines provide exceptional precision and repeatability. Each part produced is nearly identical to the next, ensuring consistent quality across large production runs.
The ability to automate processes also makes CNC milling highly cost-effective. Labor costs are reduced, and the machines can run continuously without requiring frequent breaks or supervision. This leads to higher throughput and shorter production times.
But here’s the kicker – CNC milling can create parts with complex geometries that would be difficult or impossible to make with traditional methods. This is especially useful in industries like aerospace and automotive, where parts often require multiple intricate features.
Advantage | Description | Impact on Manufacturing |
---|---|---|
Precision | CNC milling machines produce highly accurate parts. | Ensures consistent quality and tight tolerances. |
Automation | CNC mills are automated and require minimal supervision. | Reduces labor costs and increases efficiency. |
Complex Parts | CNC milling can create intricate shapes and features. | Expands design possibilities in multiple industries. |
7. What Are the Limitations of CNC Milling?
While CNC milling has numerous benefits, it’s not without its limitations. First and foremost, the initial cost of purchasing a CNC machine can be substantial. The machines themselves are expensive, and the software and setup also require a significant investment.
Another limitation is the size of the parts that can be machined. While CNC milling machines can handle relatively large workpieces, there are still size constraints. If a part exceeds the machine’s capacity, it may require multiple setups or different machines altogether, which can increase production time.
What’s the real story? CNC milling machines also require regular maintenance to ensure optimal performance. Over time, the tools can wear down, and the machine may require recalibration. This downtime can lead to increased costs for businesses, especially if they need to outsource repairs.
Limitation | Description | Potential Solutions |
---|---|---|
High Initial Cost | CNC machines and setup require a large upfront investment. | Consider leasing options or smaller-scale machines for initial projects. |
Size Constraints | Larger workpieces may exceed the machine’s capacity. | Use larger machines or multiple setups. |
Maintenance | CNC milling machines require regular maintenance and tool replacement. | Implement preventive maintenance programs. |
8. What is the Difference Between CNC Milling and CNC Turning?
CNC milling and CNC turning are both essential machining processes, but they’re used for different purposes. So, what’s the real difference? In CNC milling, the tool rotates while the workpiece stays stationary, cutting away material from all sides. In CNC turning, however, the workpiece rotates, and the tool moves along the length of the workpiece, removing material to shape the object.
CNC turning is typically used for cylindrical parts, like shafts or pulleys, whereas CNC milling is better for parts that require complex shapes or flat surfaces. Ready for the good part? CNC turning machines tend to be simpler and more cost-effective for producing round parts, but CNC milling is preferred when the design is more complex.
Process Type | Description | Best Use Case |
---|---|---|
CNC Milling | Tool rotates, cutting material from all sides. | Ideal for complex, intricate parts. |
CNC Turning | Workpiece rotates, tool moves along it. | Best for cylindrical parts, like shafts. |
9. How is CNC Milling Controlled?
CNC milling is controlled by a computer system that uses specialized software to translate design files into machine instructions. But here’s the kicker – these instructions are written in G-code, a programming language used by CNC machines. The G-code defines the movements, speeds, and tool changes needed to create the part.
CNC operators must ensure that the G-code is properly written and that the machine is correctly set up before starting the machining process. In some cases, operators may need to fine-tune the settings during production to ensure optimal results. For example, if the part isn’t being cut as accurately as expected, the operator can adjust the feed rate or tool speed to improve performance.
Control Type | Description | Key Features |
---|---|---|
G-code | The programming language used for CNC machines. | Directs machine movements and tool changes. |
CAM Software | Converts CAD designs into machine instructions. | Facilitates the CNC machining process. |
Operator Input | Manual adjustments to optimize machining. | Ensures precision and machine efficiency. |
Conclusion
In this article, we’ve covered the essentials of CNC milling, from its definition and various types of machines to the materials it can process and the industries it serves. We’ve also discussed the advantages, limitations, and the key differences between CNC milling and other machining processes like CNC turning. Ultimately, CNC milling is a powerful tool that allows manufacturers to create precise, complex parts, but it does come with its challenges, such as high initial costs and the need for regular maintenance.
By understanding the intricacies of CNC milling, manufacturers can better leverage this technology to improve their production processes and produce high-quality parts consistently.
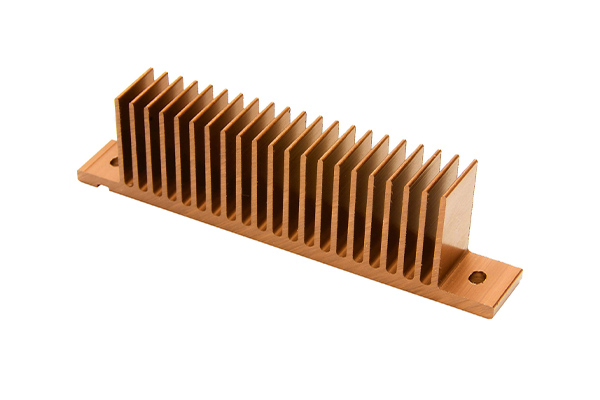
10. What Types of Tools Are Used in CNC Milling?
CNC milling requires various types of tools, each designed for specific cutting operations. You might be wondering, what tools are essential for CNC milling? The answer lies in understanding the various tool types and their functions. The most commonly used tools in CNC milling include end mills, drills, reamers, and face mills.
End mills are probably the most versatile tool in CNC milling. They have cutting edges on the sides and ends, making them suitable for a variety of milling operations like face milling, slot milling, and profiling. These tools come in different shapes and sizes depending on the application, and they are typically used for cutting in different directions.
Drills, on the other hand, are used to create holes in the workpiece. They are designed to remove material from the center of the workpiece to create a cylindrical hole. Reamers are used to finish the holes drilled by creating a smoother, more precise surface. They work best when exact hole dimensions are required, such as in the production of components like bearings.
What’s the real story? Face mills are larger tools used for cutting broad flat surfaces. They work by removing material across the entire surface of the workpiece, ensuring uniformity and precision.
Tool selection is critical for CNC milling success. The wrong tool can lead to defects, inefficiencies, or even machine damage. In fact, selecting the proper tool for the job can help minimize tool wear and prolong the lifespan of the CNC machine itself.
Tool Type | Description | Common Use |
---|---|---|
End Mill | A tool with cutting edges on both the sides and ends. | Versatile cutting tool for a wide variety of operations. |
Drill | A tool used to create cylindrical holes. | Primarily used to drill holes for various parts. |
Reamer | A tool for finishing holes with precision. | Ideal for creating smooth, precise holes. |
Face Mill | A tool used for cutting broad flat surfaces. | Used for surface finishing and material removal. |
11. How Do You Set Up a CNC Milling Machine?
Setting up a CNC milling machine can be a daunting task for beginners, but understanding the process step by step can help simplify it. So, how do you set up a CNC milling machine correctly? It starts with ensuring that the machine is properly calibrated and positioned.
The first step in setup is securing the workpiece onto the machine table. This is usually done using clamps, vises, or fixtures to ensure the workpiece doesn’t move during the cutting process. Once the workpiece is in place, it’s essential to zero the machine’s axes. This means calibrating the machine’s movements so that the tool is positioned accurately relative to the workpiece.
Now, here’s where it gets interesting. After setting up the workpiece and zeroing the axes, the next step is selecting the proper cutting tool and ensuring it’s properly installed. The operator needs to ensure that the correct tool is selected based on the task at hand, whether it’s drilling, milling, or tapping.
To complete the setup, the CNC machine must be programmed with the necessary G-code instructions. This step involves inputting the exact cutting paths, speeds, and feeds for the machine to follow during the operation. Once everything is ready, the machine can begin its milling process. However, operators must continually monitor the process for any signs of error or malfunction.
Setup Step | Description | Key Considerations |
---|---|---|
Secure Workpiece | Clamping or fixturing the workpiece to prevent movement. | Proper securing prevents movement and ensures precision. |
Zero Axes | Calibrating the CNC machine to ensure precise tool positioning. | Ensures accuracy in part manufacturing. |
Select Tools | Choosing the correct tools based on material and machining needs. | Tool selection affects part quality and efficiency. |
Input G-code | Programming the CNC machine with the necessary instructions. | Proper G-code is crucial for correct operations. |
12. What Are the Safety Precautions for CNC Milling?
CNC milling machines are powerful and precise, but they also come with inherent risks. That’s why safety is paramount. So, what safety precautions should you take when using CNC milling machines? The answer lies in both proper training and the use of safety equipment.
One of the most critical safety precautions is wearing appropriate protective gear. Operators should always wear safety goggles to protect their eyes from flying debris and dust. Ear protection is also necessary due to the loud noise levels produced by the machine. Additionally, wearing gloves is crucial to avoid injury when handling sharp tools or parts, but it’s also important not to wear loose clothing that could get caught in the machine.
Ready for the good part? Another essential safety measure is to always ensure that the machine is properly maintained. Regular maintenance checks can prevent machinery failures, which might lead to accidents. Operators should also avoid bypassing safety features like emergency stops or guards.
Lastly, it’s vital to have proper training before operating a CNC milling machine. Operators must understand how the machine works, what safety features it has, and how to stop the machine in case of an emergency. Having an emergency plan and knowing where the emergency shutoff button is located can save lives.
Safety Measure | Description | Importance |
---|---|---|
Protective Gear | Wearing goggles, ear protection, and gloves. | Prevents injuries from flying debris and machinery. |
Machine Maintenance | Regularly servicing the machine to ensure it’s running properly. | Reduces the risk of accidents caused by machine failure. |
Operator Training | Ensuring the operator knows the machine’s function and emergency procedures. | Increases safety and reduces human error. |
13. What Are the Costs Associated with CNC Milling?
The costs associated with CNC milling can vary depending on several factors. So, what are the key costs you need to consider? The most significant upfront cost is the CNC milling machine itself. Machines can range from a few thousand dollars for smaller, entry-level models to hundreds of thousands for larger, industrial-grade machines.
The next big cost comes from tooling. While the machine is the primary investment, tools such as cutters, drills, and end mills wear down over time and need to be replaced regularly. Tooling costs are ongoing and should be factored into the cost of each production run. The type of material being processed also influences tool wear, as harder materials require tougher, more expensive tools.
But here’s the kicker – CNC milling requires skilled operators, and their salaries should be taken into account. The complexity of the project may necessitate the hiring of highly experienced personnel, which adds to labor costs. In addition to operator salaries, there’s also the cost of machine maintenance and software updates.
What about operational costs? CNC mills typically have low operating costs per part, especially when running high volumes. However, energy consumption can be significant, and the more advanced the machine, the higher its energy consumption tends to be.
Cost Type | Description | Average Cost Range |
---|---|---|
Machine Purchase | Initial cost of purchasing the CNC machine. | $5,000 to $500,000, depending on size and complexity. |
Tooling | Costs for the cutting tools used in CNC milling. | Varies from $10 to several hundred dollars per tool. |
Labor | Salaries for CNC operators and technicians. | $20 to $50 per hour, depending on experience. |
Maintenance | Costs for servicing and repairing the CNC machine. | $500 to $2,000 annually, depending on machine type. |
14. How Can You Improve CNC Milling Efficiency?
Improving efficiency is key to staying competitive in the manufacturing world, and CNC milling is no exception. So, how can you boost the efficiency of your CNC milling operations? The answer lies in a combination of optimizing machine settings, utilizing better tools, and leveraging modern technologies.
One of the most effective ways to improve efficiency is by optimizing the feed rate and cutting speed. By adjusting these parameters, you can reduce the time it takes to complete each part without compromising the quality of the product. Operators must understand the materials being used and the machine’s capabilities to find the optimal settings for each job.
Ready for the good part? Investing in high-quality tools can make a significant difference in milling efficiency. High-speed steel and carbide tools, for example, last longer and cut faster than standard tools. This not only reduces tool replacement costs but also speeds up production.
Another way to improve efficiency is by using automation. With advancements in robotics and CNC machine integration, it’s possible to automate loading, unloading, and part inspection, which reduces downtime and increases throughput.
Efficiency Improvement | Strategy | Impact |
---|---|---|
Optimizing Settings | Adjusting feed rate and cutting speed for efficiency. | Reduces machining time without sacrificing quality. |
High-Quality Tools | Using durable tools that maintain sharpness longer. | Increases cutting speed and tool lifespan. |
Automation | Implementing automated loading and unloading. | Reduces labor costs and increases throughput. |
15. What Is the Future of CNC Milling?
The future of CNC milling is bright, with constant advancements in technology driving more capabilities and efficiencies. So, what does the future hold for CNC milling? The answer is in automation, artificial intelligence (AI), and machine learning.
Automation is already a key player in CNC milling, and it will only become more prevalent. Robotic arms are now commonly used in conjunction with CNC machines for tasks like part loading and unloading, further reducing manual labor and increasing operational speed.
What’s the real story? AI and machine learning are making their way into CNC milling machines. These technologies enable machines to learn from past operations and make adjustments in real time, improving precision and reducing errors. This means that the future will bring even greater reliability and higher-quality production at lower costs.
Additionally, sustainability is becoming an increasingly important consideration. As manufacturers look to reduce waste and energy consumption, CNC milling machines are being developed to be more eco-friendly. Energy-efficient motors, recyclable materials, and better coolant systems are just a few innovations that will help the industry become more sustainable.
Future Trend | Description | Impact |
---|---|---|
Automation | Increased use of robotic systems in milling operations. | Reduces labor costs and speeds up production. |
AI & Machine Learning | Machines learning and adapting to optimize performance. | Increases precision and reduces errors. |
Sustainability | Development of eco-friendly milling technologies. | Reduces environmental impact and operational costs. |
Conclusion
In conclusion, CNC milling is a vital manufacturing process used to produce high-precision, intricate parts. From the types of CNC milling machines and tools to understanding the setup, safety measures, and costs involved, this article has provided a comprehensive overview of CNC milling. The future of this technology looks promising with advancements in automation, AI, and sustainability, which will continue to enhance the capabilities and efficiency of CNC milling machines.
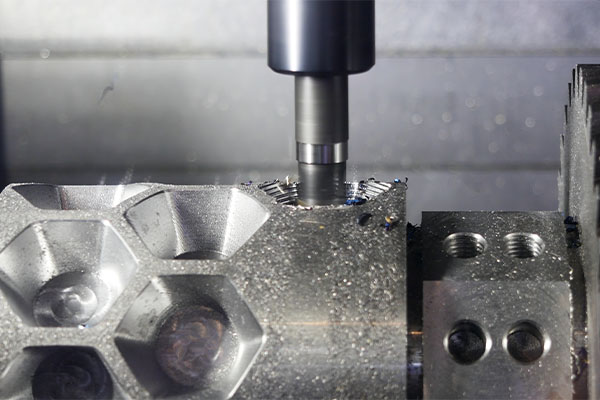
FAQ Section
Q1: What is CNC milling?
CNC milling is a machining process that uses rotating cutting tools to remove material from a workpiece, shaping it into precise parts.
Q2: How does CNC milling work?
CNC milling works by using computer-generated instructions (G-code) to control the movement of cutting tools, which remove material from the workpiece to create the desired shape.
Q3: What types of CNC milling machines are there?
CNC milling machines come in vertical, horizontal, and 5-axis varieties, each designed for different applications and workpiece sizes.
Q4: What materials can be processed with CNC milling?
CNC milling can process metals like aluminum and steel, plastics, wood, and composite materials, making it suitable for a wide range of industries.
Q5: What industries use CNC milling?
Industries such as aerospace, automotive, medical device manufacturing, and electronics use CNC milling for producing high-precision parts.