Introduction
CNC milling machining is one of the most precise and efficient manufacturing methods used in industries today. Whether you’re producing parts for aerospace, automotive, or medical devices, CNC milling plays a crucial role in achieving high-quality products with exact specifications. But what exactly is CNC milling, and why is it so widely used? In this article, we’ll walk you through everything you need to know about CNC milling, from the basics of how it works to the various types of machines and operations it involves. We’ll also dive into the advantages, common applications, and materials used in CNC milling, as well as how to optimize your milling processes for improved results. Let’s explore!
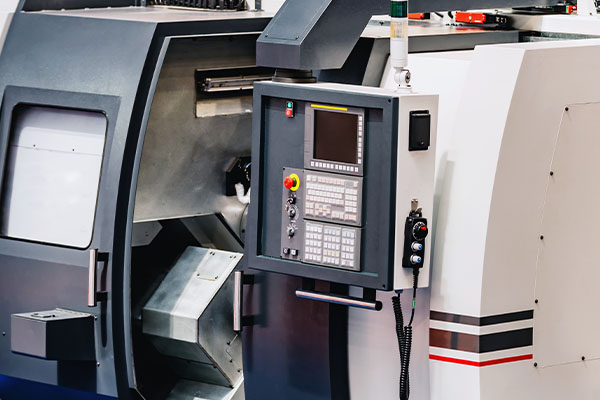
The Basics of CNC Milling
What Does CNC Stand For?
CNC, or Computer Numerical Control, refers to the automated control of machining tools, such as drills, lathes, and mills, through computers executing pre-programmed sequences of commands. The process involves the use of computers to manage the actions of these machines, allowing them to produce highly accurate and complex parts. Without CNC, manufacturers would rely on manual processes that could be prone to human error and inconsistency.
How Does CNC Milling Work?
CNC milling is a process where a computer-controlled machine removes material from a workpiece to create a desired shape. A rotating cutter, guided by the machine’s instructions, moves across the material to cut it into the precise dimensions specified in the design. Unlike traditional manual milling, CNC milling can operate on multiple axes (X, Y, Z) simultaneously, allowing for the creation of complex shapes and parts with high precision.
CNC milling machines use specialized software that converts the design into a set of machine-readable instructions known as G-code. This G-code controls the movements of the milling machine, including how fast the cutter moves, how deep it cuts, and the direction it follows. The process is incredibly versatile and can be used for both small-scale and large-scale production, offering high repeatability.
Manual Milling vs. CNC Milling
While manual milling relies on human operators to control the machine and make decisions based on their expertise, CNC milling relies on programmed instructions, making it far more precise and efficient. The major benefit of CNC milling is its ability to produce parts with exact specifications without the risk of human error.
How CNC Milling Machines Operate
Machine Components
CNC milling machines consist of several key components that work together to perform the milling process. These components include the spindle, which holds the cutting tool; tool holders, which secure the tools in place; workpieces, which are the materials being cut; and the CNC controller, which processes the instructions from the software and directs the machine’s movements. Together, these components create a smooth and controlled milling process.
Types of CNC Milling Machines
There are different types of CNC milling machines, each designed for specific tasks:
- Vertical Milling Machines: The spindle is mounted vertically, allowing the tool to cut from above. These machines are ideal for operations that require precision, such as drilling and surface cutting.
- Horizontal Milling Machines: The spindle is horizontal, and the workpiece is moved along the X and Y axes. These machines are better suited for heavy-duty tasks like cutting larger parts or complex geometries.
- 3-Axis, 4-Axis, and 5-Axis Milling Machines: The number of axes indicates the number of directions the tool can move in. A 3-axis machine moves along the X, Y, and Z axes, while a 4-axis machine adds a rotational axis, and a 5-axis machine can rotate in multiple directions simultaneously, offering maximum flexibility.
Each type of milling machine has its advantages, depending on the complexity and size of the workpiece.
Advantages of CNC Milling
Precision and Accuracy
One of the biggest advantages of CNC milling is its precision. CNC machines can produce parts with tolerances as tight as a few microns, making them perfect for industries that require high levels of accuracy, such as aerospace and medical device manufacturing. The ability to replicate exact dimensions repeatedly is a major benefit over manual methods.
Consistency and Repeatability
CNC milling offers consistency across multiple production runs. Once the machine is programmed, it can produce identical parts with the same level of precision every time. This repeatability ensures that large batches of parts meet the same quality standards, reducing the likelihood of defects.
Complex Geometries
CNC milling machines can handle more complex geometries than traditional milling machines. With the ability to operate on multiple axes simultaneously, CNC milling can create intricate shapes and fine details that would be difficult, if not impossible, to achieve manually.
Efficiency and Speed
Thanks to automation, CNC milling is faster and more efficient than manual methods. CNC machines can run 24/7, with minimal downtime, allowing manufacturers to meet tight deadlines. The efficiency of CNC milling also reduces the overall cost of production, making it an attractive option for both small and large-scale manufacturers.
Common Applications of CNC Milling
Industries That Use CNC Milling
CNC milling is widely used across a range of industries due to its precision, versatility, and efficiency. Aerospace, automotive, and medical industries rely on CNC milling for manufacturing complex and high-performance parts. For example, CNC milling is used to create turbine blades for jet engines, automotive engine components, and surgical tools.
Types of Parts Produced
CNC milling is ideal for producing a variety of parts, including gears, brackets, casings, and electronic housings. The ability to create parts with exact dimensions and intricate features makes CNC milling indispensable in many production processes.
Prototyping and Mass Production
CNC milling is used not only for mass production but also for prototyping. Engineers can quickly turn a design into a physical part, testing and refining it before moving on to mass production. This flexibility makes CNC milling a valuable tool in the product development process.
Materials Used in CNC Milling
Metals
CNC milling machines can handle a variety of metal materials, including steel, aluminum, titanium, and more. These materials are chosen based on the part’s required strength, durability, and resistance to wear.
Plastics
Various plastics, such as acrylic, Nylon, and PVC, are commonly used in CNC milling. These materials are often used for prototyping, lightweight components, and parts that do not require high-strength characteristics.
Composites
Some advanced CNC milling machines are designed to work with composite materials, such as carbon fiber or fiberglass, which are commonly used in industries like aerospace. These materials are often chosen for their lightweight and high-strength properties.
Material Choice and Its Impact
The choice of material plays a crucial role in the milling process, influencing factors like tool wear, machining speed, and the final product’s strength. Manufacturers must carefully consider the material properties when planning a CNC milling operation to ensure optimal results.
The CNC Milling Process: Step by Step
Preparation of the Workpiece
Before the milling process can begin, the workpiece must be properly prepared. This includes securing it in the machine and ensuring it is positioned correctly. In some cases, the workpiece may need to be pre-machined to a rough shape before being placed in the CNC milling machine.
Tool Selection and Setup
The next step is selecting the right tools for the job. The choice of tools depends on the material, the desired cut, and the part’s geometry. Once the tools are chosen, they are installed in the machine’s tool holder.
Programming the CNC Machine
The CNC machine needs to be programmed with the correct instructions. This is typically done using CAD/CAM software, which generates the necessary G-code. The G-code tells the machine how to move, how fast to move, and what actions to take at each step.
Milling Process
Once the machine is set up and the program is loaded, the milling process begins. The machine moves the tool along the pre-programmed paths, cutting away material from the workpiece to achieve the desired shape.
Post-Production Finishing
After the milling process is complete, additional finishing operations may be required to smooth surfaces, remove burrs, or add coatings. These post-production steps ensure that the part meets the required specifications and quality standards.
Types of CNC Milling Operations
Face Milling vs. Peripheral Milling
Face milling involves cutting with the face of the tool, while peripheral milling uses the edge of the tool. Each operation is suited for different types of cuts. Face milling is used for larger surface cuts, while peripheral milling is often employed for more precise cuts along edges or contours.
Slot Milling, Contour Milling, and Others
Other milling operations include slot milling, which creates grooves or slots in the material, and contour milling, which is used to cut along the shape of a part. Each type of operation has specific uses depending on the geometry of the part.
Drilling, Tapping, and Boring
CNC milling machines are also capable of performing operations like drilling, tapping, and boring. These processes are often required for creating holes, threads, or finishing holes to precise dimensions.
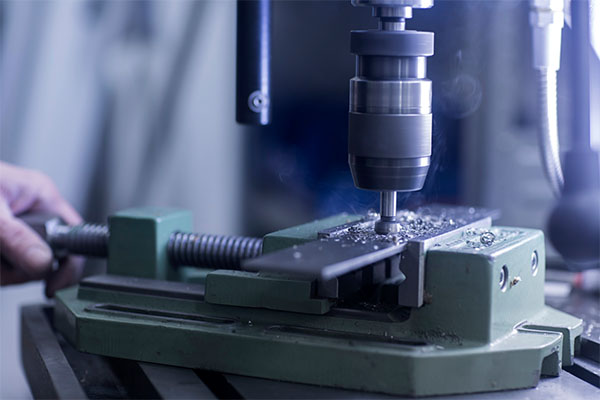
What Are CNC Milling Tools?
Tool Types
CNC milling requires a variety of tools to perform different cutting operations. Common tools include end mills, face mills, drills, and reamers, each designed for specific tasks such as cutting, drilling, or finishing surfaces.
Tool Materials
The materials used for cutting tools play a significant role in performance. Common materials include high-speed steel (HSS) and carbide. These materials are chosen based on the material being cut, as well as the required tool life and cutting speeds.
Tool Wear and Maintenance
Tools used in CNC milling can wear down over time, affecting the quality of the parts produced. Regular maintenance, including tool inspection and replacement, ensures consistent production quality.
CNC Milling vs. CNC Turning: What’s the Difference?
CNC Turning Explained
CNC turning is a process where a rotating workpiece is cut by a stationary tool. Unlike milling, which involves a stationary workpiece and a moving tool, turning is ideal for parts with a cylindrical shape.
Advantages and Disadvantages
Both CNC milling and turning have their advantages. Milling is better for creating flat surfaces, complex shapes, and precise contours, while turning is more efficient for parts requiring round features or symmetrical shapes.
Factors Affecting CNC Milling Performance
Machine Speed and Feed Rates
The speed at which a CNC milling machine operates, as well as the feed rate, plays a significant role in the performance and quality of the final part. The optimal speed and feed rate depend on the material being milled and the type of operation being performed.
Cutting Force and Tool Pressure
High cutting forces and excessive tool pressure can lead to tool wear, deformation, and poor surface finishes. Proper tool selection and machine calibration are essential to managing these factors.
Coolants and Lubricants
Using the right coolants and lubricants helps reduce heat and friction during the milling process, improving tool life and the quality of the part.
Common Challenges in CNC Milling
Material Issues
Milling certain materials can be challenging due to their hardness, abrasiveness, or tendency to heat up during cutting. Manufacturers must choose the right tools and cutting parameters to overcome these challenges.
Machining Errors
Machining errors such as misalignment, tool deflection, and backlash can lead to inaccuracies. These issues can be minimized through proper machine setup, tool maintenance, and calibration.
Maintaining Quality
Ensuring that parts meet tight tolerances and are free from defects requires careful attention to detail during every step of the process. Regular inspection and quality control help maintain consistent results.
CNC Milling Software: Programming and Control
CAD/CAM Software
CAD (Computer-Aided Design) and CAM (Computer-Aided Manufacturing) software are essential tools in the CNC milling process. CAD software is used to design parts, while CAM software converts these designs into machine-readable instructions.
G-code and M-code
G-code and M-code are programming languages used to control CNC machines. G-code defines the movement of the machine, while M-code controls auxiliary functions such as spindle speed and tool changes.
How Software Affects Production
The quality of the software used to program CNC milling machines significantly impacts the production process. Advanced software features can optimize tool paths, reduce cutting times, and improve part accuracy.
Future Trends in CNC Milling
Automation and AI Integration
The integration of artificial intelligence (AI) and automation in CNC milling machines is revolutionizing manufacturing processes. AI can optimize machining parameters in real-time, leading to increased efficiency and reduced waste.
Additive Manufacturing Hybrid Models
Some companies are experimenting with hybrid models that combine CNC milling with additive manufacturing (3D printing). This approach allows for the production of highly complex parts with both subtractive and additive techniques.
Advances in Materials and Tools
The development of new materials and cutting tools is improving the capabilities of CNC milling machines. New composite materials and advanced cutting tools are enabling the production of even more complex and high-performance parts.
Conclusion: Why CNC Milling Is Essential for Modern Manufacturing
CNC milling has become an indispensable part of modern manufacturing. Its ability to produce precise, complex parts with repeatable accuracy makes it ideal for industries that require high-quality, reliable components. As technology continues to evolve, CNC milling will remain at the forefront of manufacturing, enabling businesses to meet the ever-increasing demands of the market.
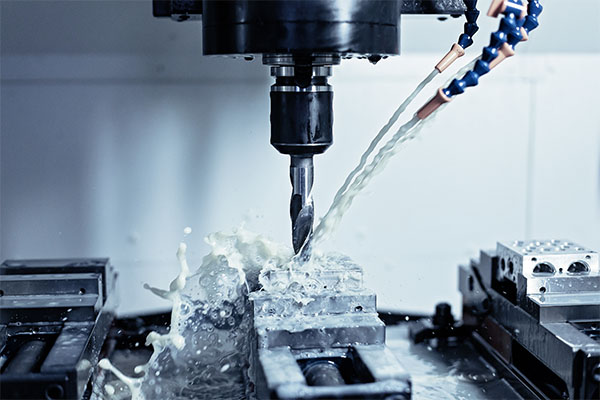
FAQ Section
- What is the difference between CNC milling and CNC machining? CNC machining is an umbrella term that encompasses all machine tools controlled by a computer. CNC milling is a specific type of machining where a rotating cutter is used to remove material from a stationary workpiece. CNC milling is just one form of CNC machining, which also includes turning, drilling, and grinding.
- How precise is CNC milling? CNC milling is extremely precise, often able to produce parts with tolerances as tight as 0.001 inches or smaller. This level of precision is essential for industries such as aerospace, medical device manufacturing, and electronics, where accuracy is critical.
- Can CNC milling handle all types of materials? CNC milling can handle a wide range of materials, including metals like aluminum, steel, and titanium, plastics like PVC and nylon, and composites such as carbon fiber and fiberglass. Each material has specific properties that affect the milling process, but CNC machines can be adjusted to accommodate most materials.
- What industries use CNC milling the most? Several industries rely heavily on CNC milling due to its precision and versatility. The aerospace industry uses CNC milling to produce complex parts for aircraft, engines, and other components. Automotive manufacturers use it for engine parts, chassis, and other precision components. Medical device manufacturers use CNC milling to create implants, surgical tools, and prosthetics. Electronics companies rely on it for creating intricate enclosures and parts for devices like smartphones and computers.
- Is CNC milling cost-effective for small batch production? Yes, CNC milling can be cost-effective for small batch production due to its high repeatability and low labor costs. While initial setup costs can be higher than traditional methods, the automation of the process allows for consistent production at lower costs per unit. This is especially true for complex parts that require precise machining.
- What are the safety concerns with CNC milling? CNC milling machines can present several safety concerns, including sharp tools, flying debris, and heavy machinery. Operators need to follow strict safety protocols, such as wearing protective gear like safety glasses and gloves, and ensuring that the work area is clear of unnecessary objects. Regular maintenance and operator training are essential to prevent accidents.
- How often should CNC milling machines be serviced? CNC milling machines should be serviced regularly to ensure they operate at peak efficiency. Depending on usage, servicing can range from every six months to annually. Routine checks include cleaning, lubrication, calibration, and inspection of the tools and components. Ensuring the machine is well-maintained helps avoid costly breakdowns and maintains consistent performance.
- What’s the cost of a CNC milling machine? The cost of a CNC milling machine varies significantly depending on its size, complexity, and features. Entry-level models can cost around $10,000 to $50,000, while more advanced, larger machines can range from $100,000 to $500,000 or more. Additional costs may include software, tools, and ongoing maintenance.
- How can I improve the efficiency of CNC milling operations? Improving CNC milling efficiency involves optimizing several aspects of the process, including the selection of cutting tools, machine settings, and programming. Using high-performance tools, setting optimal speeds and feeds, minimizing machine downtime, and implementing automation can help maximize efficiency. Regular maintenance and using the latest software for programming can also streamline operations.
- What skills are needed to operate a CNC milling machine? Operating a CNC milling machine requires a combination of technical skills, including an understanding of CNC programming, machine setup, tool selection, and troubleshooting. Operators must be able to read technical drawings and blueprints, adjust machine settings for different materials, and ensure that the machine is operating safely and efficiently. Continuous learning is also important as technology in CNC machining evolves.