Introduction
Rapid prototyping is a process that allows designers and engineers to quickly create a physical version of a product’s design, often using 3D printing or other advanced manufacturing techniques. This process helps in testing concepts, verifying designs, and improving the development cycle of products before full-scale production. Whether you are designing a new gadget, a mechanical part, or even an architectural model, rapid prototyping can drastically reduce both the time and cost involved in product development. But how exactly does rapid prototyping work, and what are its advantages? Let’s dive into the details.
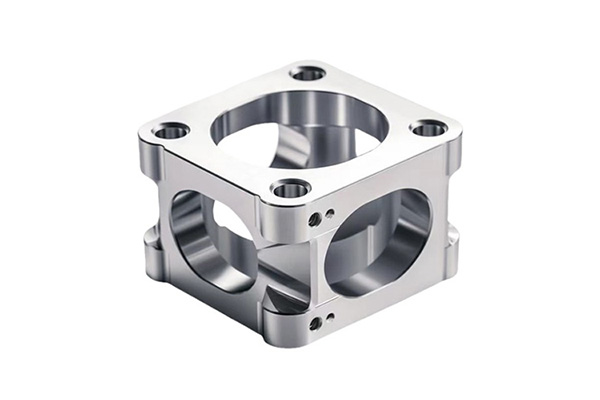
1. What is Rapid Prototyping?
Rapid prototyping is a technique used to quickly fabricate a physical model of a part or assembly using 3D computer-aided design (CAD) data. The process involves turning digital models into tangible objects within a short time frame, often measured in days or hours rather than weeks or months. This method is crucial for validating designs before committing to expensive production runs.
But here’s the kicker – rapid prototyping isn’t just about speed. It’s also about testing ideas early in the design process. Engineers and designers can create a prototype, test its functionality, and make improvements, all before committing to the final production method. This early-stage testing helps ensure that the final product will meet design specifications and performance requirements.
The importance of rapid prototyping in industries like automotive, healthcare, and consumer electronics cannot be overstated. With rapid prototyping, product development cycles can be shortened, risks can be reduced, and innovation can be accelerated.
Table 1: Key Benefits of Rapid Prototyping
Benefit | Description |
---|---|
Time Efficiency | Rapid prototyping speeds up the design process, allowing for quick iteration. |
Cost Reduction | Minimizes costs by identifying design flaws early. |
Enhanced Testing | Prototypes allow for real-world testing before full production. |
Design Flexibility | Changes can be made quickly without significant additional costs. |
Improved Communication | Prototypes improve communication between designers, engineers, and clients. |
2. How Does Rapid Prototyping Work?
In essence, rapid prototyping involves converting a digital 3D design into a physical model using a variety of methods. The first step typically involves using CAD software to create a 3D model of the product. From there, different technologies, such as 3D printing, CNC machining, or injection molding, are used to bring the design to life.
What’s the real story behind the actual process? The most commonly used method for rapid prototyping is 3D printing, or additive manufacturing. In this method, material is deposited layer by layer to form the physical object. The material can vary, ranging from plastics and metals to more specialized substances like ceramics and composites.
Another popular method is CNC machining, which uses subtractive techniques to carve out a prototype from a solid block of material. Both methods offer unique advantages depending on the complexity of the design and the materials needed.
Table 2: Common Methods of Rapid Prototyping
Method | Description | Best Use Case |
---|---|---|
3D Printing | Additive manufacturing method that builds layers of material. | Complex geometries and quick turnaround prototypes. |
CNC Machining | Subtractive process where material is removed to form parts. | High precision and strength in final prototypes. |
Injection Molding | Creates prototypes by injecting material into molds. | Mass production prototypes for plastics. |
SLA (Stereolithography) | Uses UV light to cure layers of resin into a solid object. | High detail prototypes, often in resin or plastic. |
3. What Are the Types of Rapid Prototyping Methods?
When it comes to rapid prototyping, there isn’t just one technique. There are several methods, each suited to different needs, materials, and applications. So, what’s the real difference between all these options?
3D printing, CNC machining, and injection molding are some of the most commonly used rapid prototyping methods, but each has its own strengths and weaknesses. For example, 3D printing is incredibly versatile and great for complex shapes, but it may not always offer the strength or finish quality needed for some applications. CNC machining, on the other hand, can provide highly durable prototypes with a smooth surface finish, though it tends to be slower and more expensive.
One of the newer methods, selective laser sintering (SLS), is gaining popularity. This technique uses a laser to fuse particles of material together. It’s often used for creating functional parts with good mechanical properties.
Ready for the good part? Let’s break down the details of each method, including when and why you’d use them.
Table 3: Comparison of Rapid Prototyping Methods
Prototyping Method | Material Options | Speed | Cost | Best for |
---|---|---|---|---|
3D Printing | Plastics, metals, ceramics | Fast (1-2 days) | Low to medium | Complex shapes, quick iterations |
CNC Machining | Metals, plastics | Medium (1-3 days) | Medium to high | High precision, durability |
Injection Molding | Plastics | Medium to slow (3+ days) | Medium to high | Mass production, high volume |
Selective Laser Sintering (SLS) | Plastics, metals | Medium (2-3 days) | Medium to high | Strong parts, detailed parts |
4. What Are the Benefits of Rapid Prototyping?
The benefits of rapid prototyping extend far beyond just creating a quick mock-up of a design. What’s the real story here? Rapid prototyping allows for a range of advantages that can fundamentally change how products are developed.
For one, rapid prototyping accelerates the design process. Designers and engineers can quickly create prototypes, test them, and make adjustments before production. This reduces the chances of costly mistakes or product recalls once manufacturing begins.
Another significant advantage is cost savings. Rapid prototyping allows for early identification of design flaws, meaning expensive errors can be avoided later on. This is particularly important for industries with high development costs, such as automotive or aerospace.
And that’s not all. Rapid prototyping also fosters innovation. By enabling quick testing of multiple design ideas, it opens the door to more creative solutions that might not have been considered otherwise.
Table 4: Major Benefits of Rapid Prototyping
Benefit | Impact |
---|---|
Faster Time to Market | Speeds up the development process and reduces delays. |
Lower Development Costs | Early testing and revisions reduce the risk of costly mistakes. |
More Design Flexibility | Allows for quick changes and updates to designs before mass production. |
Improved Product Quality | Better testing ensures higher-quality products with fewer defects. |
Increased Innovation | Encourages the exploration of new design concepts through rapid iteration. |
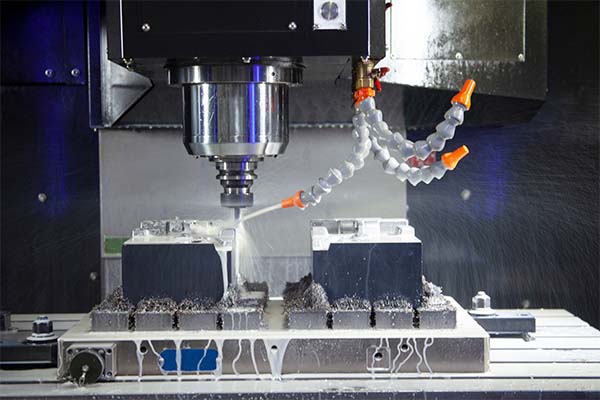
5. How Is Rapid Prototyping Used in Product Development?
So, how does rapid prototyping fit into the larger process of product development? It’s not just about making a prototype – it’s about integrating it into the design workflow. This is where rapid prototyping truly shines.
First, rapid prototyping allows for testing designs before committing to full-scale manufacturing. Let’s say you’ve created a new product idea. Instead of guessing how it will perform, you can build a prototype to simulate its functionality in the real world. This helps you identify potential issues early on, so you don’t waste resources on flawed designs.
In industries like medical devices or aerospace, this process is especially critical. Prototypes must meet strict regulatory standards. With rapid prototyping, adjustments can be made quickly and efficiently, ensuring that the product will be safe and compliant before hitting the market.
But here’s where it gets interesting. Rapid prototyping is not just for the development phase – it also plays a key role in the manufacturing process. Once the prototype is perfected, it can serve as a model for mass production, ensuring that the final product meets the required specifications.
Table 5: How Rapid Prototyping Fits into Product Development
Stage | How Rapid Prototyping Helps |
---|---|
Conceptualization | Provides a tangible version of design ideas for initial evaluation. |
Design Refinement | Allows for quick testing and iteration to improve product design. |
Testing and Validation | Ensures that products meet functionality, safety, and regulatory standards. |
Production Readiness | Translates the final prototype into a model for mass production. |
6. What Are the Applications of Rapid Prototyping?
Rapid prototyping isn’t limited to just one industry; its applications are vast and varied across multiple sectors. So, why does it matter? In industries where time and accuracy are crucial, rapid prototyping is invaluable.
Take the automotive industry, for example. Engineers can quickly produce prototypes of parts and test them in real-world conditions. This reduces the risk of design flaws in final production vehicles and saves manufacturers significant time and money. A great example is how major car companies use rapid prototyping to create and test prototypes for dashboards, engine parts, and other critical components.
In the medical field, rapid prototyping is a game-changer. Medical devices, especially custom implants or prosthetics, require precision. Rapid prototyping allows doctors and engineers to quickly test fit, function, and usability before manufacturing the final product. For instance, prosthetic limbs can be tailored to an individual’s unique measurements using 3D scanning and prototyping, leading to better results and improved patient satisfaction.
And then, there’s aerospace. Rapid prototyping can be used to develop parts that need to meet stringent safety and performance standards, all while ensuring that they are lightweight and durable. From creating models of aircraft interiors to testing components for aircraft engines, rapid prototyping plays a crucial role in this industry.
What’s the takeaway? Rapid prototyping is transforming industries that require precision, fast iterations, and high-quality products, whether it’s creating prototypes of products, parts, or medical devices.
Table 6: Applications of Rapid Prototyping Across Industries
Industry | Applications |
---|---|
Automotive | Prototype parts, dashboards, engine components, and custom fittings. |
Medical Devices | Custom implants, prosthetics, surgical tools, and medical equipment. |
Aerospace | Lightweight and durable components, aircraft interiors, engine testing. |
Consumer Electronics | Prototype consumer gadgets, wearables, and electronic accessories. |
Architecture | Rapid models for building designs, structural elements, and layouts. |
7. What Materials Are Used in Rapid Prototyping?
Materials play a huge role in the rapid prototyping process. What’s the real story behind the materials used in these techniques? The choice of material can affect the prototype’s functionality, durability, and finish.
Plastics are by far the most common materials used in rapid prototyping. Polylactic acid (PLA) and acrylonitrile butadiene styrene (ABS) are common 3D printing materials that offer great strength, flexibility, and ease of use. These materials are affordable, easy to mold, and provide good results for basic prototype testing.
Metals are another crucial material, especially when the prototypes require durability and heat resistance. Stainless steel, aluminum, and titanium are often used in 3D printing or CNC machining for parts that need to withstand high stress or extreme conditions. For example, aerospace companies use metal prototypes to test engine components, ensuring they can handle the rigors of flight.
But here’s where it gets interesting: composites and hybrid materials are becoming increasingly popular in rapid prototyping. These materials combine the strengths of multiple substances, such as carbon fiber-reinforced plastics, to provide additional strength without increasing weight. This is particularly beneficial in industries like automotive and aerospace, where minimizing weight while maintaining strength is key.
Table 7: Common Materials Used in Rapid Prototyping
Material Type | Common Materials | Best Use Case |
---|---|---|
Plastics | PLA, ABS, Nylon, PETG | Low-cost, quick prototypes, simple models |
Metals | Stainless steel, Aluminum, Titanium | Functional prototypes, aerospace, automotive |
Composites | Carbon fiber, Fiberglass, Kevlar | Strong and lightweight parts |
Resins | Standard resins, Tough resins | High-detail prototypes, smooth finishes |
Ceramics | Ceramic powder, Clay-based materials | Heat-resistant prototypes in various industries |
8. How Does 3D Printing Fit into Rapid Prototyping?
Let’s get down to it: 3D printing is arguably the most significant technological advancement in the field of rapid prototyping. But why is it so important? The ability to create complex, intricate shapes in a matter of hours has revolutionized product development across industries.
In rapid prototyping, 3D printing is often used because it can produce prototypes faster and cheaper than traditional methods. For example, a designer might create a prototype of a new consumer product, print it, and test it within a day. This speeds up the iteration process and allows for quick feedback from stakeholders.
Another reason 3D printing stands out is its versatility. Unlike traditional manufacturing methods, which might require expensive molds or tooling, 3D printing allows for virtually any shape to be produced. This means that designers can experiment with unconventional designs that might be too complex or expensive to make using other methods.
What’s more, 3D printing can be done with a variety of materials, from plastics to metals, allowing manufacturers to test functional parts in real-world conditions before committing to production.
Table 8: Benefits of 3D Printing in Rapid Prototyping
Benefit | Description |
---|---|
Speed | Rapid creation of prototypes in a matter of hours. |
Complexity | Ability to produce intricate and complex shapes easily. |
Cost-Effective | Eliminates the need for costly molds or tooling. |
Material Flexibility | Can print using various materials, from plastics to metals. |
Low-Volume Production | Ideal for low-volume, custom prototypes. |
9. How Does CNC Machining Contribute to Rapid Prototyping?
CNC machining is another critical method in the rapid prototyping process. This technique uses computer-controlled machines to cut, mill, and carve prototypes out of solid materials, including metals, plastics, and composites. What makes CNC machining so valuable? The precision it offers.
For example, aerospace manufacturers use CNC machining to create highly detailed, accurate components that can withstand extreme conditions. This is crucial when developing parts like engine components, where strength and precision are paramount.
CNC machining also plays a significant role in creating parts with a smooth surface finish, which is essential for products that need to be both functional and aesthetically pleasing. For instance, consumer electronics prototypes, such as smartphone casings, benefit greatly from CNC machining because of the high-quality finish it provides.
Here’s the interesting part: CNC machining allows for the creation of prototypes that are nearly identical to the final product in terms of material properties and strength. This makes it a vital part of rapid prototyping, especially when testing for functionality.
Table 9: CNC Machining vs. 3D Printing for Prototyping
Aspect | CNC Machining | 3D Printing |
---|---|---|
Material Options | Metals, plastics, composites | Plastics, metals, ceramics |
Speed | Medium (depends on part complexity) | Fast (1-2 days for basic models) |
Surface Finish | High-quality, smooth finish | Can vary, rougher surface unless post-processed |
Cost | Higher for low-volume runs | Generally lower, especially for smaller parts |
Best Use Case | Precision parts, durable components | Complex shapes, rapid iterations |
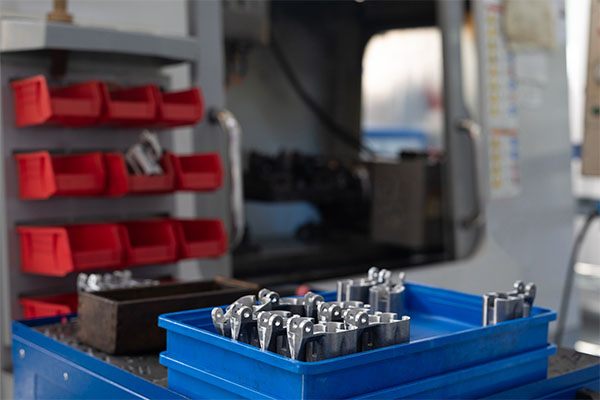
10. What Are the Challenges in Rapid Prototyping?
Like any technology, rapid prototyping is not without its challenges. While it offers numerous benefits, it also comes with some hurdles that need to be considered. For starters, there’s the issue of material limitations.
Not all materials are suited for prototyping. For example, while plastics are great for initial testing, they may not replicate the strength or durability required for final products, particularly in industries like aerospace or automotive. This can result in prototypes that don’t accurately represent the final product’s performance.
Another challenge is the trade-off between speed and quality. While rapid prototyping can produce models quickly, the time constraints may sometimes lead to less-than-perfect prototypes. In some cases, especially with 3D printing, the surface finish might not meet the required standards for final production.
And then there’s the issue of cost. While rapid prototyping is generally more cost-effective than traditional methods, the cost can still be high for complex parts or low-volume production. For example, creating metal parts using additive manufacturing or CNC machining can be expensive.
Table 10: Challenges of Rapid Prototyping
Challenge | Description |
---|---|
Material Limitations | Limited availability of strong, durable materials for some applications. |
Quality vs. Speed | Balancing the need for fast prototypes with the need for high-quality parts. |
Cost | High costs for certain materials and complex prototypes. |
Post-Processing | Many rapid prototypes require additional finishing. |
Complexity | More intricate designs may lead to longer production times and higher costs. |
11. How Much Does Rapid Prototyping Cost?
When it comes to rapid prototyping, cost is one of the first questions that comes to mind. The good news is that the cost has significantly decreased over the years, making it more accessible for smaller businesses and startups. However, the cost still varies depending on a variety of factors.
The complexity of the design plays a significant role. Simple prototypes made of plastic materials, for example, are often much cheaper to produce than metal prototypes that require more specialized equipment. Additionally, some rapid prototyping methods, such as 3D printing, are generally less expensive than others like CNC machining, especially for small runs.
Another factor to consider is material choice. While plastics tend to be the most affordable option, metal prototypes can be significantly more expensive. For instance, a basic plastic prototype might cost just a few hundred dollars, while a metal prototype could run into the thousands, depending on the size and complexity.
Table 11: Cost Breakdown of Rapid Prototyping
Method | Material | Average Cost Range |
---|---|---|
3D Printing | Plastic, Resin | $100 – $2,000 |
CNC Machining | Metals, Plastics | $500 – $5,000 |
Injection Molding | Plastic | $1,000 – $10,000 |
Selective Laser Sintering | Metals, Plastics | $500 – $3,000 |
12. What Are the Key Considerations When Choosing a Rapid Prototyping Service?
Choosing the right rapid prototyping service can be a challenge, but it’s also crucial for ensuring that your prototypes meet your needs. So, what do you need to look for? First, consider the specific requirements of your project. Does your prototype require precision? Are you working with a specific material that needs to be matched?
Another consideration is the turnaround time. Depending on the complexity of your design, you may need to work with a service provider that can deliver your prototype quickly.
Quality control is another important factor. You want to ensure that the service provider has quality assurance procedures in place to meet your specifications.
Table 12: Factors to Consider When Choosing a Service Provider
Factor | Consideration |
---|---|
Material Options | Ensure the service can provide the necessary materials for your prototype. |
Turnaround Time | Choose a provider that can deliver within your required timeframe. |
Quality Control | Ensure the service maintains high standards of quality assurance. |
Experience and Expertise | Look for providers with experience in your specific industry. |
Cost | Compare prices for similar services to find the best value. |
13. How Can Rapid Prototyping Be Integrated into the Manufacturing Process?
Integrating rapid prototyping into the manufacturing process isn’t just about testing new designs. It’s also about ensuring that the prototype can be smoothly transitioned into full-scale production. Once a prototype has been validated, manufacturers need to ensure that the design can be scaled up without compromising quality or efficiency.
One way rapid prototyping aids this process is by helping identify potential production issues early. For example, you may discover that a certain component is too complex to manufacture efficiently at scale. By identifying this early, you can make the necessary design changes before full production begins.
Moreover, rapid prototyping also supports design for manufacturability (DFM). This concept involves designing products in a way that makes them easy and cost-effective to manufacture. Prototypes can be used to simulate the manufacturing process, ensuring the final design is optimized for mass production.
Table 13: Benefits of Integrating Rapid Prototyping into Manufacturing
Benefit | Description |
---|---|
Early Issue Detection | Identify potential manufacturing problems before full production. |
Design for Manufacturability (DFM) | Ensure prototypes are designed with production efficiency in mind. |
Improved Communication | Enhances collaboration between designers, engineers, and manufacturers. |
Faster Time to Market | Streamlines the process from prototype to mass production. |
Cost Savings | Reduce costs by preventing issues that arise during production. |
14. What Are Some Case Studies of Successful Rapid Prototyping?
Case studies provide concrete examples of how rapid prototyping can be used effectively across various industries. For instance, a well-known automotive manufacturer used rapid prototyping to develop a new car part. By using 3D printing to test the part’s fit and functionality, the company was able to identify design flaws early, saving them both time and money in the production phase.
In another example, a medical device company used rapid prototyping to create custom implants for patients. By 3D printing the implants and testing them on real patients, the company was able to ensure the implants would fit perfectly, leading to better outcomes and reduced risk.
What’s the takeaway? These case studies highlight how rapid prototyping can save both time and money while enhancing innovation and quality across industries.
Table 14: Case Studies in Rapid Prototyping
Industry | Example | Result |
---|---|---|
Automotive | Car part testing using 3D printing | Identified design flaws, saved time and money. |
Medical Devices | Custom implants for patients created through 3D printing | Improved patient outcomes, reduced risk. |
Consumer Electronics | Prototype smartphone casings using CNC machining | Achieved high precision and smooth finish. |
15. What is the Future of Rapid Prototyping?
The future of rapid prototyping looks bright, with advancements in technology making the process faster, cheaper, and more accessible. The integration of artificial intelligence (AI) and automation into rapid prototyping will allow designers to generate and refine prototypes with even greater speed and efficiency.
Moreover, new materials are being developed all the time, opening up new possibilities for what can be prototyped. For example, the use of bio-materials and nanotechnology could revolutionize industries like healthcare and electronics, enabling the development of new types of products that were previously unimaginable.
So, what’s next? The future of rapid prototyping is poised to bring even more advancements, and industries that adopt these technologies early will have a significant edge in product development.
Table 15: Future Trends in Rapid Prototyping
Trend | Description |
---|---|
AI Integration | AI will help automate design iterations and optimize prototypes. |
New Materials | Advancements in bio-materials and nanotechnology will enable new applications. |
Faster Prototyping | Continuous improvements in 3D printing and CNC machining will shorten production times. |
Customization | More industries will use rapid prototyping for highly customized products. |
Sustainability | Prototyping methods will become more environmentally friendly. |
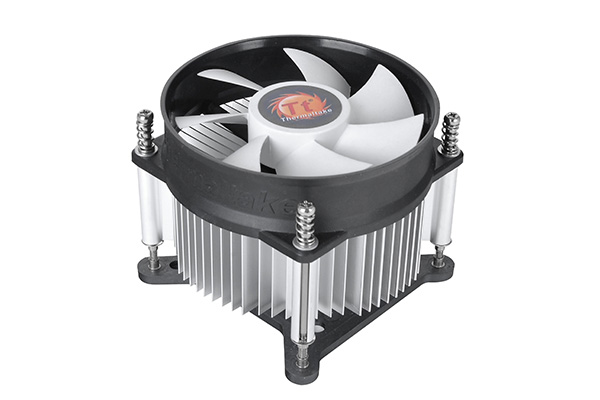
FAQ Section
Q1: What is rapid prototyping?
Rapid prototyping is the process of creating a physical prototype of a design quickly using technologies such as 3D printing, CNC machining, and others. This allows for fast iterations and testing.
Q2: How does 3D printing work in rapid prototyping?
3D printing works by adding layers of material on top of one another to build a physical object based on a 3D digital model. This allows for complex shapes and designs to be created quickly and efficiently.
Q3: What are the benefits of using rapid prototyping?
The main benefits of rapid prototyping include faster product development, cost savings by identifying design flaws early, the ability to test and iterate on designs, and improved product quality.
Q4: How much does rapid prototyping cost?
The cost of rapid prototyping varies based on the method used, the materials involved, and the complexity of the design. Prices can range from a few hundred to several thousand dollars, depending on the prototype’s size and specifications.
Q5: What industries use rapid prototyping?
Industries such as automotive, aerospace, medical devices, consumer electronics, and architecture use rapid prototyping to accelerate product development and improve design quality